Курсовая работа: Расчет механизации доставки и откатки рудной массы, стационарной установки для рудника цветной металлургии
Курсовая работа: Расчет механизации доставки и откатки рудной массы, стационарной установки для рудника цветной металлургии
Министерство образования и науки РФ
Магнитогорский государственный технический университет им. Г.И.
Носова
Кафедра Механизации и электрификации горного производства
ПОЯСНИТЕЛЬНАЯ ЗАПИСКА
к курсовому проекту
Магнитогорск 2007
Исходные данные
|
Значение |
Вид
полезного ископаемого
Годовая
производственная мощность шахты (Агш), млн.т./год
Плотность
полезного ископаемого ( ), т/м3
Длина
доставки (Lдост), км
Длина
откатки (Lотк), км
Глубина
шахты (Нш), м
Коэффициент
водообильности пород (Кво)
Коэффициент
кратности водопротока (Ккр)
Водородный
показатель воды (рН)
Количество
дней в году с минимальным водопротоком (Nдн.min)
Количество
дней в году с максимальным водопротоком (Nдн.max)
Количество
подаваемого в шахту для проветривания (Qвозд), м3/с
Минимальная
депрессия (hmin), мм. вод. ст.
Максимальная
депрессия (hmax), мм. вод. ст.
Количество
потребителей сжатого воздуха на каждой стрелке (см.схему):
Длина
конвейерной ленты (lконв), м
-
перфораторы (nn), шт
-
вентиляторы местного проветривания (nвмп), шт
-
погрузочные машины (nпм), шт
-
количество углубочных комплексов (nук), шт
|
Cu
1,3
2,7
0,35
3,55
480
1,95
1,14
6
330
33
430
235
455
27
7
3
3
1
|
Реферат
В данном курсовом проекте было предложено рассчитать механизацию
доставки и откатки рудной массы, стационарные установки для рудника цветной металлургии.
Доставку горной массы в пределах блока осуществляется автосамосвалами
МоАЗ-7405-9586 в количестве 2 автосамосвалов на каждом участке.
Откатку
горной массы – электровозами КТ14 в количестве 4 шт. и вагонеток ВГ4,5А.
Водоотлив
осуществляется центробежными насосами ЦНС 300-120…600. В количестве 1 рабочий,
1 резервный, 1 на ремонте.
Проветривание
горных выработок центробежными вентиляторами ВЦД-47,5У/495. В количестве 1
рабочего, для резерва воспользуемся только двигателем.
Снабжение
сжатым воздухом производится центробежными компрессорами К-500-61-2 и
4М10-100/8.
Подъем полезного ископаемого многоканатным скиповым подъемом,
подъемной машиной ЦШ-2,25х6. Отклоняющий шкив поставляется вместе с подъемной
машиной.
Содержание
Реферат
Содержание
Введение
1.
Технология ведения и комплексной механизации горных работ
1.1 Общие
сведения
1.2 Способ и
схема вскрытия месторождения
1.3 Система
разработки
2. Рудничный
транспорт
2.1 Описание
технологического процесса транспортирования горной массы
2.2
Самоходный транспорт
2.2.1
Тяговый расчет
2.2.2
Эксплуатационный расчет
2.2.3 График
организации движения
2.3
Электровозный транспорт
2.3.1
Тяговый расчет
2.3.2
Эксплуатационный расчет
2.3.3 График
организации движения
2.4
Ленточный конвейер
3.
Эксплуатационный расчет водоотливной установки
3.1 Технологическая
схема водоотлива
3.2
Определение водопритока в шахте
3.3
Производительность насоса
3.4
Определение напора насоса
3.5 Выбор
типа и количества насосов
3.6
Обоснование количества нагнетательных ставов и составление гидравлической схемы
3.7 Расчет
характеристики внешней сети
3.8 Проверка
действительного режима работы насосной водоотливной установки
3.9 Расчет
мощности на валу насоса электропривода
3.10 Обоснование
объема водосборника
4.
Эксплуатационный расчет вентиляторов главного проветривания
4.1 Описание
схемы проветривания и выбор типа вентилятора
4.2
Определение действительного режима работы вентилятора главного проветривания
4.3 Расчет
электропривода вентилятора главного проветривания
5.
Эксплуатационный расчет пневмоснабжения рудника
5.1 Схема
пневмосети и потребителей сжатого воздуха
5.2 Расчет
производительности и выбор типа компрессора
6.
Эксплуатационный расчет подъемной установки
6.1
Обоснование и выбор схемы подъема полезного ископаемого
6.2
Производительность и грузоподъемность подъемной установки
6.3 Выбор
подъемных сосудов
6.4 Расчет и
выбор подъемных канатов
6.5 Расчет и
выбор подъемной установки
6.6
Расположение подъемной машины относительно оси шахты
7.
Организация технического обслуживания и ремонта оборудования
8. Генеральный
план промышленной площадки рудника
Список
литературы
Введение
В нашей стране подземным способом добывают около 30% металлических
руд и горно-химического сырья, однако на подземных работах занято значительно
большее количество трудящихся, чем на открытых работах.
Одним из наиболее важных звеньев в комплексной механизации
подземной добычи руд является процесс перемещения руды от забоя до поверхности,
включая операции выпуска, погрузки, доставки ее в пределах очистного блока и
транспорта по магистральным выработкам до ствола шахты. На доставку и
транспортирование руды приходится около 50% всех затрат по добыче.
Среди горно-механического оборудования, от которого зависит
эффективность и надежность работы горных предприятий, значительную и
ответственную часть составляет стационарные машины и установки. Они
представляют собой комплексы энергомеханического оборудования, предназначенные
для подъема полезного ископаемого и пустых пород на поверхность, подъема спуска
людей, материалов и оборудования. Осушение месторождения полезного ископаемого
и откачки воды из горных выработок на поверхность, искусственного проветривания
горных выработок, выработки сжатого воздуха, который используется в качестве
энергоносителя некоторых горных машин и механизмов.
Стационарные установки обеспечивают на горных предприятиях
благоприятные условия и эффективность выполнения основных производственных
процессов. От надежной и безаварийной работы стационарного оборудования зависят
не только производительность труда, но часто и сама возможность ведения горных
работ. Выход из строя приводит к нарушению ритма, а иногда и к остановке работы
всего горного предприятия. Поэтому к устройству и эксплуатации стационарных
установок предъявляются повышенные требования.
1. Технология ведения и
комплексной механизации горных работ
1.1 Общие сведения
Рудничный транспорт рудных шахт представляет собой многозвенную
систему, состоящую из различных транспортных машин и установок, выполняющих
следующие функции:
- транспортирование полезного ископаемого
от очистных забоев, полезного ископаемого и породы из подготовительных забоев
до околоствольного двора или до поверхности шахты, а также транспортирование
полезного ископаемого по поверхности до склада или до мест погрузки в вагоны
железнодорожного транспорта и породы в отвал;
- транспортирование с поверхности шахты к
очистным и подготовительным забоям и обратно вспомогательных грузов различного
назначениям и оборудования;
- перевозка людей к местам их работы и
обратно.
Канатная подъемная установка представляет
комплекс энергомеханического оборудования, предназначенного для обеспечения
транспортной связи подземных горных выработок шахты или глубоких горизонтов
карьера с земной поверхностью. При помощи канатных подъемных установок на
горных предприятиях осуществляют подъем полезных ископаемых и попутных горных
пород, а также спуск подъем и подъем людей, материалов и оборудования.
Водоотливная установка служит для откачки
подземных вод из дренажных горных выработок шахт.
Вентиляторные установки на горных
предприятиях служат для проветривания горных выработок и поддержания в них
комфортных условий труда путем создания атмосферных условий, при которых состав
воздуха соответствует требованиям отраслевым ПБ.
1.2 Способ и схема вскрытия месторождения
Способ вскрытия.
Вскрытие месторождения осуществляется тремя вертикальными стволами.
Главный ствол (рудовыдачной) оснащен скипо-клетевым подъемом, вспомогательные стволы -
клетевым с противовесом.
Схема вскрытия.
Схема вскрытия принимается в зависимости от схемы проветривания.
Принимаем фланговую схему проветривания, по вспомогательному стволу, пройденный
возле главного ствола, воздух подается, а по второму вспомогательному стволу -
выдается.
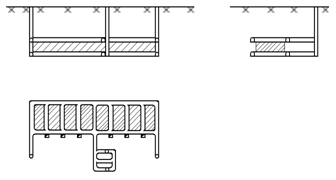
Рис.1.1. Схема вскрытия месторождения
1.3 Система разработки
Для данного месторождения с учетом его горно-геологических
характеристик применим сплошную систему разработку с двухслойной выемкой и
применением самоходного оборудования.
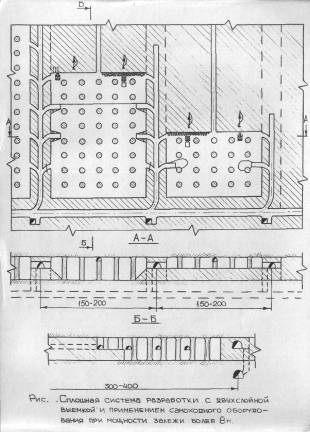
2. Рудничный транспорт
2.1 Описание технологического процесса транспортирования горной
массы
Схему транспортирования предопределяет принятая схема вскрытия и
система разработки.
Доставка при сплошной системе разработки с двухслойной выемкой с
применением самоходного оборудования подразумевается погрузка горной массы
погрузчиком в автосамосвалы. При длине доставке, Lдост =350, этот
комплекс является наиболее эффективным, т.к. средняя длина доставки
автосамосвалов при их максимальном использовании является 300-600м.
Автосамосвал разгружается в рудоспуск.
Откатка горной массы до околоствольного двора осуществляется
электровозным транспортом. Вагонетки загружаются под рудоспуском с помощью
вибролюков. В околоствольном дворе вагонетки разгружаются с помощью опрокида в
бункер, а затем грузят в скипы. Скип поднимается по стволу, разгружается, по
конвейеру горная масса поступает на обогатительную фабрику.
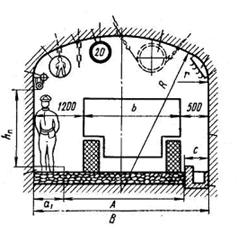
рис 2.1. Технологическая схема доставки, транспортирования и
подъема
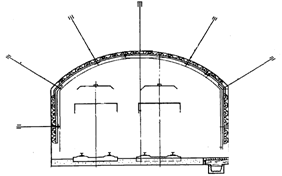
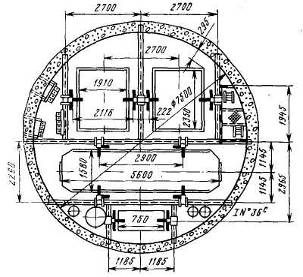
Рис.2.2. Типовые сечения горных выработок,
штрека, квершлага, ствола
2.2 Самоходный транспорт
Выберем отечественный автосамосвал с дизельным приводом,
грузоподъемностью 22 т, МоАЗ-7405-9586.(1.стр83 табл.5.4)
Техническая характеристика автосамосвала МоАЗ-7405-9586
Параметры |
Значение |
Грузоподъемность,
т
Мощность
привода, кВт
Скорость
максимальная, км/ч
Габариты,
мм:
- длина
- ширина
- высота
Масса, т
|
22
140
40
8610
2850
2630
19,5
|
2.2.1 Тяговый расчет
Сила тяги автосамосвала, развиваемая на уклоне
(2.1)
где G0, G - масса соответственно машины и груза, т;
ω0 - основное удельное сопротивление движению машины, Н/кН (ω0=80-100
для дорог без покрытия, с зачисткой)(1.стр.93); ωкр
=(0,05÷0,08)ω0 - дополнительное сопротивление движению
на криволинейных участках, Н/кН (ωкр=0,05·100=5 Н/кН); Wв
- дополнительное сопротивление воздуха, Н/кН (Wв = 0 - при скорости
движения менее 20 км/ч); i - удельное сопротивление на уклоне, Н/кН (i=3Н/кН);
а - ускорение трогания, м/с2 (а=0,4-0,5).
Сила тяги в грузовом направлении движения автосамосвала вверх

Сила тяги в порожняковом направлении движения автосамосвала вниз

Скорость машины, зависимая от условия движения машины
(2.2)
где N - мощность двигателя машины, кВт; ηт
=0,72÷0,75 - коэффициент полезного действия гидромеханической передачи,
(ηт=0,75); ηк - коэффициент полезного действия
колеса, (ηк=0,95).(1.стр92)
Скорость машины в грузовом направлении движения вверх

Скорость машины в грузовом направлении движения вниз

Предельный угол преодолеваемый машиной при трогании на подьем.
(2.3)

Сцепной вес машины при двух ведущих колесах
(2.4)
Сцепной вес машины в грузовом направлении движения

Сцепной вес машины в порожняковом направлении движения

Максимальная сила тяги по условию сцепления ведущих колес машины с
дорогой, которую способна развить машина
(2.5)
где ψ - коэффициент сцепления пневмошин с дорогой,
(ψ=0,5-дороги забойные, в крепких породах, дорожное покрытие мокрое,
слегка загрязненное).
Максимальная сила тяги в грузовом направлении движения

Максимальная сила тяги в порожняковом направлении движения

Т.к. Fmax(гр)>Fгр, Fmax(пор)>Fпор,то
машина может перемещаться на данном уклоне.
Тормозной путь до полной остановки при груженом направлении
движения по уклону вниз
(2.6)
где kин - коэффициент инерции вращающихся масс для
машин с гидромеханической передачей, (kин = 1,03 - в режиме движения
с грузом); Vн - начальная скорость, м/с (Vн = Vгр).

Тормозной путь, пройденный за время реакции водителя
(2.7)
где tp = 0,5÷0,6 с - время реакции водителя, с
(tp = 0,6).
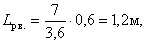
Полный тормозной путь с учетом времени реакции водителя и действия
тормозов
(2.8)
2.2.2 Эксплуатационный расчет
Время погрузки одного автосамосвала в комплексе с ковшовым
погрузчиком
(2.9)
где Vкуз - вместимость кузова, м3; kз.к.-
коэффициент загрузки кузова, (kз.к.=0,9);
tц - время цикла черпания грузонесущим органом, с (tц=50
с); kман - коэффициент, учитывающий время, затрачиваемое на маневры
машины в забое, (kман=1,2); ξ - коэффициент, учитывающий время,
затрачиваемое на разборку негабарита, (ξ=1,15); Vк -
вместимость ковша погрузчика, м3; kз - коэффициент заполнения
ковша, (kз=0,8).

Продолжительность движения машины в грузовом и порожняковом
направлениях
(2.10)
где Lдост - длина доставки, км; kс.х.-
коэффициент, учитывающий среднеходовую скорость движения, (kс.х.=0,75
при Lдост=0,35 км).[1,стр90]
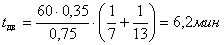
Время разгрузки зависит от конструктивного исполнения кузова
транспортной машины, для автосамосвалов с опрокидным кузовом tраз=0,7мин.
Продолжительность маневров в забое tм.з. и у мест
разгрузки tм.р. зависит от конкретных условий эксплуатации
транспортных машин и определяется хронометражными наблюдениями, т.е. по графику
организации работ. tм.з.=1мин, tм.р.=1 мин.
Продолжительность ожидания машины на разминовках tразм=2мин.
Продолжительность одного рейса транспортной машины
=4+6,2+0,7+1+1+2=14,9 мин (2.11)
Эксплуатационная сменная производительность одной транспортной
машины, автосамосвала
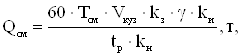
где kи - коэффициент использования машины, (kи=0,8)[1,стр89];
kн - коэффициент неравномерности грузопотока, (kн=1,5 при
отсутствии аккумулирующей емкости).
(2.12)
Сменная производительность рудника
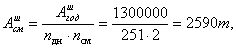
где nдн - количество рабочих дней в году, (nдн=251
дней, режим работы рудника); nсм - число рабочих смен в сутки по
выдаче полезного ископаемого, (nсм=2 смены).
Сменная производительность первого участка
(2.13)
где nуч - число участков на руднике, (nуч=3).
Расчетное число рабочих транспортных автосамосвалов на
эксплуатируемом участке
принимаем 2 автосамосвала (2.14)
Инвентарное число машин с учетом машин, находящихся в резерве и
ремонте
автосамосвалов (2.15)
Сменный пробег рабочих автосамосвалов
(2.16)
где kх - коэффициент, учитывающий холостой пробег
машины на заправку, к пунктам обслуживания и т.д., (kх=1,2).[1,cтр92]

2.2.3 График организации движения
График организации движения автосамосвалов
на первом участке представлена на рис. 2.3.
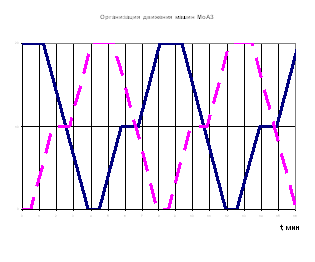
Рис.2.3. График организации движения автосамосвалов
2.3
Электровозный транспорт
Электровоз принимается по сцепному весу в зависимости от
производственной мощности рудника, при мощности Aгодш=1,3
млн.т./год, сцепной вес электровоза равен Рсц= 140 кН.
Принимаем электровоз КТ14
Техническая характеристика электровоза КТ14 [1,стр154]
Параметры |
Значение |
Масса, т
(сцепной вес, кН)
Габариты,
мм
- длина
- ширина
- высота
Жесткая
база, мм
Часовая/длительный
режим
Сила тяги,
кН
Сила тока,
А
Скорость,
км/ч
Двигатель
- тип
-
мощность, кВт
|
14 (140)
5800
1350
1650
1700
27/14
204/122
11,5/14
ДТН45
2х46
|
Выбор вагонетки производим учитывая длину откатки и
производительность рудника, при Lотк=3,55 км и Aгодш=1,3
млн.т./год, принимаем ВГ4,5А. [1,стр151]
Техническая характеристика ВГ4,5А [1,стр140]
Параметры |
Значение |
Вместимость
кузова, м3
Грузоподъемность,
т
Колея, мм
Длина по
буферам, мм
Ширина
кузова, мм
Высота от
головки рельса, мм
Жесткая
база, мм
Диаметр
колеса, мм
Масса, кг
|
4,5
13,5
750; 900
4100
1350
1550
1250
400
4500
|
2.3.1 Тяговый расчет
Масса поезда при трогании на подъем на засоренных путях у
погрузочных пунктов
(2.17)
где Р - масса электровоза, т; ψ - коэффициент сцепления колес
электровоза с рельсами, (ψ=0,17 - поверхность рельсов влажные, практически
чистые. Условие движения без подсыпки песка)[1,177с,табл 10.2]; ωг
- удельное сопротивление движению, Н/кН (ωг=5 Н/кН); ωкр
- удельное сопротивление на криволинейных участках, Н/кН (ωкр=6
Н/кН); ip - руководящий уклон пути, Н/кН (ip=3 Н/кН); а -
ускорение при трогании, м/с2 (а=0,03 м/с2)[1,стр178].

Число вагонеток в составе
(2.18)
где Vв - вместимость кузова вагонетки, м3;
γ - насыпная плотность транспортируемой горной массы, т/м3; G0
- масса вагонетки, т.
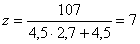
Параметры состава
- масса груза в одном вагоне
(2.19)
- масса порожнего поезда
(2.20)
- масса груженого поезда без локомотива
(2.21)
- длина поезда
(2.22)
где lэ,lв - длина соответственно электровоза
и вагонетки, м.
Проверка массы поезда по условию торможения
Удельная тормозная сила
(2.23)
Согласно ПБ на преобладающем уклоне при перевозки грузов тормозной
путь lт=40 м.
Допустимая скорость груженого поезда (км/ч) на расчетном
преобладающем уклоне пути
(2.24)
Проверка массы поезда по условию нагрева тяговых двигателей
электровоза
Сила тяги, отнесенная к одному тяговому двигателю в грузовом F’г
и порожняковом F’п направлениях
(2.25)
(2.26)
где nдв- число тяговых двигателей; ωп -
удельное сопротивление движению порожних вагонеток, Н/кН (ωп=8
Н/кН).
Согласно электромеханической характеристике электродвигателя
ДТН45, полученным значениям силы тяги соответствуют токи Iг=40 А, Iп=70А.[1,стр168.рис10.7]
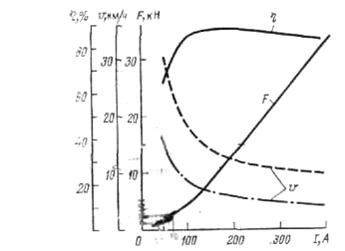
Рис.2.4. Электромеханическая характеристика ДТН45
Время движения груженого состава определим исходя из скорости
движения допустимой по торможению
(2.27)
где Lг - длина пути в грузовом направлении, км; kг
- коэффициент, учитывающие снижение скорости в периоды разгона и торможения, (kг=0,75);
Vг - скорость движения в грузовом направлении, км/ч (Vг=Vдоп.г.=14км/ч).

При силе тока Iп=70 А, скорость движения поезда в
порожняковом направлении по электротехнической характеристике Vп=28
км/ч.
Время движения порожнякового состава
(2.28)
где Lп - длина пути в порожняковом направлении, км; kп
- коэффициент, учитывающие снижение скорости в периоды разгона и торможения, (kп=0,8)[1,стр179].
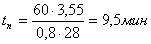
Продолжительность пауз θц включает
продолжительность разгрузки в опрокидыватели tразгр=0,67 мин,
загрузке под люком tзагр =2 мин и резерв времени на различные
задержки (10 мин)[1,стр185]
(2.29)
Продолжительность одного рейса
(2.30)
Эффективный ток тягового двигателя
(2.31)
где α - коэффициент, учитывающий дополнительный нагрев
двигателей при выполнении маневров (α=1,3 - для контактных электровозов).
(2.32)
Длительный ток электровоза определяем по его технической
характеристике Iдл=122А, т.к. Iэф < Iдл,
следовательно, оставляем в составе 7 вагонеток.
Длина разминовки
(2.33)
Вывод: в результате расчетов принимаем наименьшее значение массы
груженого поезда исходя из условии четырех проверок
2.3.2 Эксплуатационный расчет
Число рейсов одного электровоза в смену
(2.34)
где kэ - коэффициент, учитывающий время подготовки
электровоза к эксплуатации (kэ=0,8 - для контактных электровозов)[1,стр181].

Число рейсов в смену необходимое для вывоза горной массы при
суммарной сменной производительности
, (2.35)
где kн - коэффициент неравномерности работы поступления
груза (kн=1,25 - при наличии аккумулирующей емкости)[1,стр181]; nл,
nм - число рейсов на одно крыло соответственно с людьми и
вспомогательными материалами, (nл=2, nм=2).
рейсов
Число электровозов необходимых для работы
электровозов (2.36)
Инвентарное число электровозов
Nи=Nр+Nрез,
где Nрез - число резервных электровозов, (Nрез=2
при Nр=5).
Nи=7+2=9 электровозов (2.37)
Сменная производительность одного электровоза
1313,5 (т·км) (2.38)
Необходимое число вагонеток
zв.п.=1,25·z·Np+zв.м., (2.39)
где zв.м - число вагонеток, транспортирующих
вспомогательные материалы, (zв.м=4).
zв.п.=1,25·7·7+4 = 66 вагонеток
Расход энергии на электровозный транспорт
Расход энергии за один рейс, отнесенный к колесам электровоза
, МДж (2.40)

Расход электровозом энергии за 1 рейс, отнесенный к шинам
подстанции
(2.41)
где ηэ - КПД электровоза (ηэ=0,6);
ηс - КПД тяговой сети (ηс=0,95); ηп
- КПД подстанции (ηп=0,93)[1,стр181].
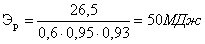
Удельный расход энергии на шинах подстанции за смену, отнесенный к
1 т·км транспортируемого груза
(2.42)
Общий расход энергии за смену
(2.43)
Коэффициент одновременности
(2.44)
Средний ток
(2.45)
Потребная мощность подстанции
(2.46)
где U - напряжение сети, В.

Максимально допустимую длину участка по одну сторону от тяговой
подстанции определяют по условиям падения напряжения
(2.47)
где ΔU - допустимое падение напряжения в контактной сети,
которое при наибольшей нагрузке не должно превышать 15-20%, В (ΔU =
0,2·220=44В);
- среднее сопротивление
контактного провода и рельсовых путей , Ом/м (Rср = 0,105+0,028=0,133
Ом/м).
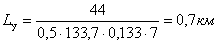
Т.к. Lу < Lг, следовательно, необходимо
проложить усиливающий кабель от тяговой подстанции на 1/2 длины(1,8 км)
откаточного участка. Усиливающий кабель присоединяется к контактной сети через
каждые 200-300 м.[1,стр182]
2.3.3 График организации движения
Приведем организацию движения электровозов на первом участке
рудника. Где число рабочих электровозов примем, Np = 2. Применим
организацию движения с закреплением электровоза за определенным составом,
электровоз протягивает состав в процессе погрузки и разгрузки. При такой
организации движения упрощается диспетчерское управление.
График организации движения электровозов приведена на рис. 2.5
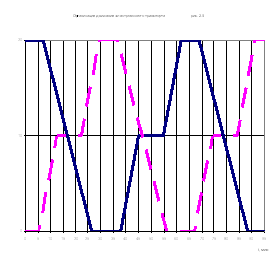
Рис.2.6. График организации движения
электровозной откатки
2.4 Ленточный конвейер
Часовая производительность конвейера
(2.48)
где tсм - продолжительность смены, ч; kи -
коэффициент использования конвейера, (kи=0,9).
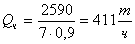
Необходимая ширина ленты конвейера[1,стр 272 ]
(2.49)
где kп - коэффициент
производительности, (kп =550 при δ = 200, φд=200);[1,таб.15.4]kв
- коэффициент снижения площади поперечного сечения горной массы на ленте в
зависимости от угла наклона конвейера, (kв=1 - при 0 угле наклона
конвейера)[1,стр271]; k1 - коэффициент, учитывающий условия
эксплуатации, (k1=1 - для стационарных установок); V - скорость
движения ленты, м/с (V=2,5м/с)[1,стр271]; γ - насыпная плотность, т/м3.

Проверяем ширину ленты по кусковатости руды
(2.50)
где аmax - наибольший размер куска, мм (аmax=300
мм).

Принимаем ленту шириной 800 мм, которая удовлетворяет требования
по кусковатости транспортируемой руды. В=800 мм.[1,стр249,табл15.2]
Масса груза на 1 м конвейера
(2.51)
На конвейере на верхней ветви установлены трехроликовые опоры, при
расстоянии между опорами lв=1м, масса вращающихся частей верней
роликоопор Gв=22 кг. На нижней ветви установлены однороликовые
опоры, lн=2 м, Gн=7,7 кг.
Масса вращающихся частей роликоопор
соответственно в верхней и нижней ветви.
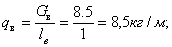 (2.52)
Линейная масса резинотросовой ленты 2РТЛО-500 шириной 800 мм, прочность 500H/мм. и
массой 20,5 кг/м
qл = В · mл
=800·20,5=16,4 кг/м (2.53)
Для определения натяжения и запаса
прочности ленты выполним тяговый расчет ленточного конвейера методом обхода
контура по точкам с учетом конфигурации трассы и схемы обводки лентой барабана.
 
  Рис.2.7.
Схема ленточного конвейера и его привода.
Сопротивление перемещению груженой ленты на верхней ветви
(2.54)
где Lконв - длина конвейерной ленты, м; g - ускорение
свободного падения, м/с2; β - угол наклона конвейерной ленты,
(β=0); ω - коэффициент сопротивления движению ленты по роликовому
ставу, (ω=0,04).

Сопротивление перемещению порожней ленты на нижней ветви
(2.55)

Составим систему уравнения
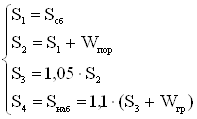 (2.56)
Минимальное натяжение ленты у привода на сбегающей ветви по
условию её пробуксовки
(2.56)
где kт - коэффициент запаса тяговой способности
привода, (kт=1,5); kд - коэффициент, учитывающий
перегрузку ленты при пуске и торможении конвейера, (kд = 1); eμα
- тяговый фактор привода конвейера (eμα =3,52 - при
α=1800 - угол обхвата, футерованный резиной при сухих условиях
работы конвейера).
Обычно для горизонтальных конвейеров
натяжение у привода S’min=S1=Sсб, а S’max=Sнаб=S4,
следовательно,
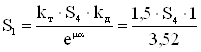
Решая уравнения получим
S1=1881 Н; S4=4415
Н.
Запас прочности ленты
(2.57)
Мощность привода конвейера
(2.58)
где kзап - коэффициент запаса, (kзап=1,2);
η - коэффициент использования электропривода во времени, (η=0,85).

3. Эксплуатационный расчет водоотливной установки
3.1 Технологическая схема водоотлива
Опытом эксплуатации и технико-экономическим сравнением
установлено, что одноступенчатая схема является наиболее экономичной. Откачка
воды из водосборника на поверхность обеспечивается одним насосным агрегатом.
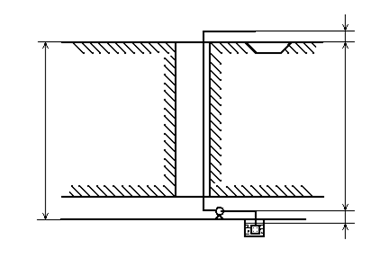
Рис. 3.1. Схема одноступенчатого водоотлива
3.2 Определение водопритока в шахте
Нормальный суточный водоприток
(3.1)
где kв - коэффициент водообильности; Dк -
количество календарных дней в году.
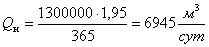
Максимальный суточный приток
(3.2)
где kкр - коэффициент кратности водопритока.
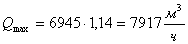
3.3 Производительность насоса
При откачке нормального водопритока
, (3.3)
где Т - нормативное время откачки суточного притока воды в
соответствии с правилами безопасности, ч (Т=20 ч - для рудных шахт).
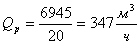
При откачке максимального притока воды
(3.4)
3.4 Определение напора насоса
Расчетный напор насоса
(3.5)
где Нг - геодезическая высота насосной установки, м; Нвс
- высота всасывания насоса, м (Нвс = 8м); Нн - высота
нагнетания, м (Нн=Нш=480- м); Нсл - высота
слива на поверхности, м (Нсл=2м).
Нр=3+480+2=485 м
3.5 Выбор типа и количества насосов
Выбираем центробежный насос по графику зон промышленного
использования насосов (Рис.3.2). Насос принимаем по расчетным значениям подачи
Qp и напора Нр. Необходимо учитывать, что главные
водоотливные установки оборудуются обычно однотипными насосными агрегатами. Это
связано с заменами запасных частей насоса. При этом стремятся выбрать насосы
таким образом, чтобы расчетные значения обеспечивались одним насосным
агрегатом.
При Qp = 347 м3/ч и Нр =485 м,
выбираем насос ЦНС- 300-600
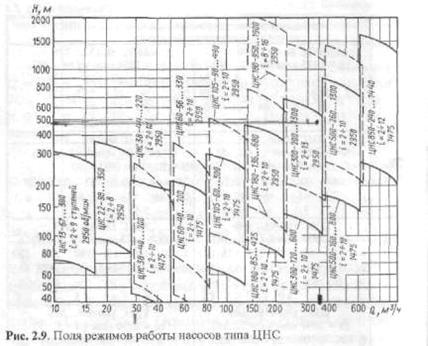
Рис. 3.2. Зоны промышленного использования насосов типа ЦНС
Расчетные параметры для дальнейшего расчета выбираются по
индивидуальной характеристике насоса при максимальном КПД. Индивидуальная
характеристика представлена на рис.3.5. При ηmax=71
%, Qн=380 м3/с; Нр.к.=110 м; Нвс=18м.
Количество колес для обеспечения подачи напора на глубине шахты
определяем по выражению
колес (3.6)
Количество насосов для откачки суточного водопритока по
нормальному водопритоку
(3.7)
где Qн - производительность насоса, м3/с.
3.6 Обоснование количества нагнетательных ставов и составление гидравлической
схемы
Главная водоотливная установка должна быть оборудована не менее
чем двумя нагнетательными трубопроводами, один из которых является резервным.
Принимаем кольцевую схему соединения с параллельным включением
коммутационных задвижек. В этом случае нагнетательные трубопроводы 8 и 9
соединяются между собой перемычками 5. На каждой перемычке устанавливаются две
коммутационные задвижки 10, между которыми через тройники подключаются насосы
4.
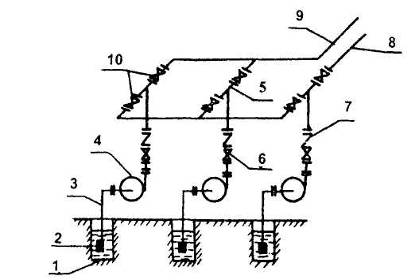
Рис. 3.3. Гидравлическая кольцевая схема
3.7 Расчет характеристики внешней сети
Расчетным путем определим характеристику внешней сети водоотливной
установки для наиболее удаленного участка сети.
Внутренний диаметр нагнетательного трубопровода
(3.8)
где Vн - скорость движения воды в нагнетательном
трубопроводе, м/с (Vн=2 м/с).
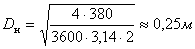
Внутренний диаметр всасывающего трубопровода
(3.9)
где Vн - скорость движения воды во всасывающем
трубопроводе, м/с (Vн=1,5 м/с).
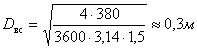
Коэффициенты местных гидравлических сопротивлений в нагнетательном
и всасывающем трубопроводе
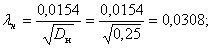 (3.10)
Постоянная трубопровода
(3.11)
где lвс - длина всасывающего трубопровода, м (по рис
3.3);
lвс=l1+l2=3+3=6 м (3.12)
lн - длина нагнетательного трубопровода, м (по рис 3.3);
lн=lпов+Hш+lходка+b2+lкамеры+hкамеры=30+480+20+3+30+2=565
м (3.13)
, - эквивалентная длина арматуры
всасывающего и нагнетательного трубопровода.
(3.14)
(3.15)
где ξс, ξк.п., ξо.к.,
ξу.к., ξз.к., ξз, ξт
- гидравлические коэффициенты потерь соответственно в приемной сетке, приемном
клапане, обратном клапане, угловом колене, закругленном колене, задвижке,
тройнике (ξс=2,51, ξк.п.=0,5, ξо.к.=1,7,
ξу.к.=0,32 - при угле поворота 1350, ξз.к.,=1,265
- при повороте 900, ξз=0,07, ξт=1,5);
nо.к., nу.к., nз.к., nз.,
nт. - число обратных клапанов, угловых колен, закругленных колен, задвижек,
тройников (nо.к.=1, nу.к.=2, nз.к.=3, nз.=2,
nт.=2).


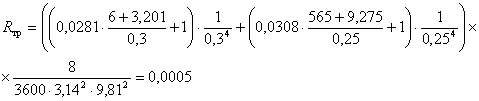
Расчет напорной характеристики внешней сети водоотливной установки
производится по формуле
и ведется в табличной форме
Q,м3/ч
|
0 |
95 |
190 |
285 |
380 |
475 |
570 |
665 |
Rтр·Q2,м
|
0 |
4,5 |
18 |
40,6 |
72,2 |
112,8 |
162,5 |
221,1 |
Нс
|
485 |
489,5 |
503, |
525,6 |
557,2 |
597,8 |
647 |
706,1 |
Графики характеристик напорной внешней сети и насоса представлены
на рис.3.5. Работа насоса с шестью и семью рабочими колёсами не обеспечивает
выдачу на поверхность нормального суточного водопритока, следовательно,
принимаем насос с восемью рабочими колесами.
Пересечение кривых характеристики внешней сети и технической
характеристики напора насоса на 4 рабочих колес (т.С), является действительным
режимом работы насоса.
Ннд = 560 м; ηнд = 71 %; Qнд=
390 м3/ч.
 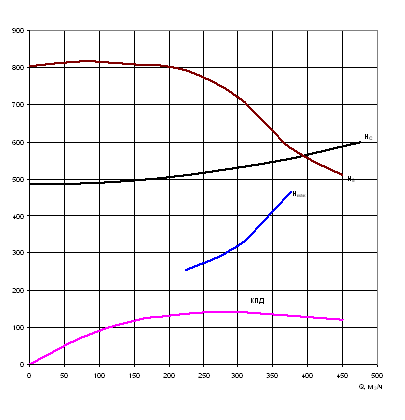
Рис.3.4. Определение действительного режима работы насосной
установки
3.8 Проверка действительного режима работы насосной водоотливной
установки
Проверка режима работы на обеспечение необходимой подачи
Qнд > Qр; 390м3/ч > 347 м3/ч
Проверка режима работы на экономичность
ηнд > 0,9·ηmax; 71 % > 65%
Проверка режима работы на обеспечения напора
Ннд > Нг (Нш); 560
м > 485 м
Водоотливная установка проверяется на время для откачки
нормального водопритока. Которое должно быть не менее 20 ч.

3.9 Расчет мощности на валу насоса электропривода
Мощность на валу насоса электродвигателя
 
Расчетная мощность Np электродвигателя рассчитывается
Nр.эл.дв.=(1,1÷1,15)·Nв=1,15· =103,5 кВт
На водоотливных установках горных предприятий используется
электропривод, работающий в длительном режиме с относительно постоянной
нагрузкой. Применительно к такому режиму работы наиболее экономичны асинхронные
электродвигатели с короткозамкнутым ротором, которые получили наибольшее
распространение на водоотливных установках.
По мощности электродвигателя Nр.эл.дв = 103,5 кВт и
синхронной частоте вращения 1500 мин-1 принимаем ближайший больший
по мощности электродвигатель, 4А280-4, Nэл.дв.=110 кВт, КПД = 92,5
%.
3.10 Обоснование объема водосборника
Объем водосборника определяется по формуле согласно требованиям
ЕПБ.
Qвод > 4·Qнорм, следовательно объем
водосборника равен Qвод=4·300 = 1200м3.
Параметры водосборника (ширину, длину, высоту) подбираем таким
образом, что бы его объем был равен 1200 м3.
Ширина а = 8м. Высота h = 6 м. Длина l = 25 м.
4. Эксплуатационный расчет вентиляторов
главного проветривания
4.1 Описание схемы проветривания и выбор типа вентилятора
Схема проветривания рудника фланговая, по вспомогательному стволу,
пройденный параллельно главному, свежий воздух подается, по второму
вспомогательному - выдается.
Способ проветривания нагнетательный, так как применяется в шахтах
опасных по взрыву газа и пыли. На таких рудниках главные вентиляторные
установки могут состоять из одного агрегата с резервным электроприводом.
Выбор вентилятора главного проветривания производится по графику
промышленного использования центробежных вентиляторов. Выбор центробежных
вентиляторов обоснован тем, что они являются более производительными по
сравнению с осевыми.
По расходу воздуха Qвозд=430 м3/с,
максимальным и минимальным депрессиям, hmin = 235мм.вод.ст.=235/0,102=2304
Па, hmax=465мм.вод.ст.=455/0,102=4461 Па, по рис. 4.1.,
примем
вентилятор
ВЦД-47,5У/495.
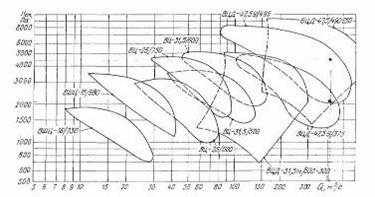
Рис.4.1.График
промышленного использования центробежных вентиляторов.
4.2 Определение
действительного режима работы вентилятора главного проветривания
Характеристика внешней сети для минимальной и максимальной
депрессии определяются по общему уравнению
(4.1)
где Нс - сопротивление внешней сети вентиляторной
установки, Па; Q - расход воздуха, м3/с; Rc - коэффициент
сопротивления внешней сети.
Коэффициент сопротивления сети при минимальной депрессии
(4.2)
Коэффициент сопротивления сети при максимальной депрессии
(4.3)
Расчеты характеристики внешней сети в начале и конце эксплуатации
ведем в табличной форме
 (4.4)
Q,м3/с
|
0 |
107 |
322 |
430 |
645 |
752 |
860 |

|
0 |
141,9 |
1285,6 |
2292,7 |
5158,7 |
7012,2 |
9171 |

|
0 |
274,7 |
2488,4 |
4437,6 |
9984,6 |
13572,1 |
17750,4 |
По
полученным табличным значениям на индивидуальной характеристике вентилятора
строим кривые h1, h2 (Рис.4.2.).
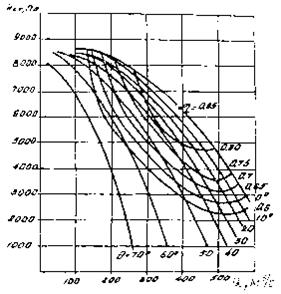
Рис.4.2.Характеристика
вентилятора ВЦД-47,5У и характеристика сети
Регулирование режимов работы вентилятора производится изменением
угла установки лопастей направляющих аппаратов.
Угол установки лопастей направляющих аппаратов определяется по
пересечению перпендикуляра, исходящий из расхода воздуха необходимый для
проветривания шахты, и кривых характеристик углов установки лопаток
направляющего аппарата на вентиляторе. Определяются статические давления при
соответствующих углов.
Время,
через которое необходимо заменить установку угла лопаток
года (4.5)
лет (4.6)
лет (4.7)
лет (4.8)
Резерв производительности вентилятора
- в начале эксплуатации
(4.9)
- в конце эксплуатации
, (4.10)
где , -необходимый расход воздуха,
принимаемый по заданию
4.3 Расчет электропривода вентилятора главного проветривания
Мощность электропривода
- в начале эксплуатации
(4.11)
- в конце эксплуатации
(4.12)
Необходимую мощность привода определяем по большей из полученных
расчетов.
Принимаем электропривод сдсз-2-17-76-12. N=4000кВт, частота
вращения. 500 мин-1, КПД 95,5%.
5. Эксплуатационный расчет
пневмоснабжения рудника
5.1 Схема пневмосети и потребителей сжатого воздуха
 ЦЦ
Рис.5.1. Расчетная схема централизованного снабжения
подземных горных работ сжатым воздухом
Таблица
5.1.
Технические
характеристики потребителей сжатого воздуха на каждой стрелке (см. схему)
Потребители
сжатого воздуха |
Обоз-наче-ние |
Кол-во |
qi,
м3/мин
|
pi,
бар
|
kиз
|
kодн
|
Перфораторы |
БП |
5 |
3,5 |
5,0 |
1,15 |
0,65 |
Вентиляторы
ВМП |
ВМ |
3 |
5,0 |
4,0 |
1,0 |
1,0 |
Погрузочные
машины |
ПМ |
3 |
22 |
5,0 |
1,1 |
0,4 |
Углубочный
комплекс |
УК |
1 |
- |
- |
- |
- |
-
Перфораторы |
БП |
4 |
3,5 |
5,0 |
1,15 |
0,65 |
-
вентиляторы ВМП |
ВМ |
2 |
5,0 |
4,0 |
1,0 |
1,0 |
-
грейферный погрузчик |
ГП |
2 |
20 |
5,6 |
1,15 |
0,45 |
5.2 Расчет
производительности выбор
типа и количества компрессоров
Участок |
Наименование
потребителей |
Длина
участка |
Число
потребителей |
Путевой
расход воздуха |
9-8 |
5БП+3ВМ+3ПМ |
100 |
11 |
57,12 |
11-8 |
5БП+3ВМ+3ПМ |
100 |
11 |
57,12 |
10-8 |
5БП+3ВМ+3ПМ |
100 |
11 |
57,12 |
12-7 |
5БП+3ВМ+3ПМ |
100 |
11 |
57,12 |
13-7 |
5БП+3ВМ+3ПМ |
100 |
11 |
57,12 |
15-6 |
5БП+3ВМ+3ПМ |
100 |
11 |
57,12 |
14-6 |
5БП+3ВМ+3ПМ |
100 |
11 |
57,12 |
3-2 |
5БП+3ВМ+3ПМ |
100 |
8 |
41,17 |
20-5 |
5БП+3ВМ+3ПМ |
100 |
11 |
57,12 |
19-5 |
5БП+3ВМ+3ПМ |
100 |
11 |
57,12 |
18-5 |
5БП+3ВМ+3ПМ |
100 |
11 |
57,12 |
16-4 |
5БП+3ВМ+3ПМ |
100 |
11 |
57,12 |
17-4 |
5БП+3ВМ+3ПМ |
100 |
11 |
57,12 |
8-7 |
Q9-8+Q11-8+Q10-8 |
200 |
11 |
171,36 |
7-6 |
Q8-7+Q13-7+Q12-7 |
250 |
11 |
285,61 |
6-2 |
Q14-6+Q15-6+Q7-6 |
250 |
11 |
399,85 |
5-4 |
Q20-5+Q19-5+Q18-5 |
300 |
11 |
514,09 |
4-2 |
Q5-4+Q17-4+Q16-4 |
350 |
11 |
628,33 |
2-1 |
Q6-2+Q3-2+Q4-2 |
440 |
11 |
1069,35 |
, м3/мин 5.1
- потери
сжатого воздуха из-за утечек воздуха во внешней пневмо сети, м3/мин;
, м3/мин 5.2
где
а
величина удельных потерь сжатого воздуха отнесенная к единице длины
воздухопровода, м3/мин, а=0,005 м3/мин; - эквивалентная
длина внешней сети , м; - величина удельных
утечек сж. воздуха в узлах подключения ответвлений пневмо сети, =0,4; m
количество узлов подключения пневмопотребителей, по схеме.
, м
м3/мин
, м3/мин
Для
выбора компрессора принимают расчетную производительность компрессора.
Выбор
типа компрессора для стационарных компрессорных станций обычно производится на
основе технико-экономического сравнения вариантов. Специальными исследованиями
установлено, что при производительности станции 1000 и более м3/мин
целесообразны центробежные компрессоры К-500-61-2.
Принимаем
2 компрессора К-250-61-2. и 2 поршневых компрессора 4М10-100/8, для работы в
период минимального потребления сжатого воздуха, т.е. ступенчатого
регулирования.
Техническая
характеристика компрессоров приведена в таблице 5.2
Таблица
5.2
Техническая
характеристика компрессоров 4М10-100/8 и К-500-61-2
Параметры |
Значение |
4М10-100/8 |
К-500-61-2 |
Производительность, м3/мин
|
100 |
525 |
Абсолютное давление, бар:
- на всасывание
- на нагнетание
|
1
9
|
Частота вращения вала, мин-1
|
500 |
7636 |
Мощность компрессора, кВт |
540 |
2030 |
Расход масла, г/ч |
250 |
- |
Электродвигатель
- марка
- мощность, кВт
- напряжение, В
|
СДК2-17-26-12К
630
6000
|
СТМ-3500-2
3500
6000
|
Давление
определяется из условия нормальной работы наиболее удаленного потребителя
, МПа
5.3
- относительные
потери давления сжатого воздуха при движении к самому удаленному источнику;
- давление сжатого
воздуха у самого удаленного потребителя, =0,5МПа.
5.4
-
относительные удельные потери;
- длина
труб до наиболее удаленного участка
Расчет
ведем в табличной форме
№ уч |
Q, м3/мин
|
Lтр
|
L |

|

|

|

|
dтр
|
dтр
по ГОСТ
|
1 |
2 |
3 |
4 |
5 |
6 |
7 |
8 |
9 |
10 |
9-8 |
57,12 |
100 |
1608 |
0,00009328 |
0,009328358 |
0,50007861 |
0,509407 |
151,1572 |
160 |
11-8 |
57,12 |
100 |
1608 |
0,00009328 |
0,009328358 |
0,50007861 |
0,509407 |
151,1572 |
160 |
10-8 |
57,12 |
100 |
1608 |
0,00009328 |
0,009328358 |
0,50007861 |
0,509407 |
151,1572 |
160 |
12-7 |
57,12 |
100 |
1608 |
0,00009328 |
0,009328358 |
0,50007861 |
0,509407 |
151,1572 |
160 |
13-7 |
57,12 |
100 |
1608 |
0,00009328 |
0,009328358 |
0,50007861 |
0,509407 |
151,1572 |
160 |
15-6 |
57,12 |
100 |
1608 |
0,00009328 |
0,009328358 |
0,50007861 |
0,509407 |
151,1572 |
160 |
14-6 |
57,12 |
100 |
1608 |
0,00009328 |
0,009328358 |
0,50007861 |
0,509407 |
151,1572 |
160 |
3-2 |
41,17 |
100 |
1608 |
0,00009328 |
0,009328358 |
0,50007861 |
0,509407 |
128,3199 |
130 |
20-5 |
57,12 |
100 |
1608 |
0,00009328 |
0,009328358 |
0,50007861 |
0,509407 |
151,1572 |
160 |
19-5 |
57,12 |
100 |
1608 |
0,00009328 |
0,009328358 |
0,50007861 |
0,509407 |
151,1572 |
160 |
18-5 |
57,12 |
100 |
1608 |
0,00009328 |
0,009328358 |
0,50007861 |
0,509407 |
151,1572 |
160 |
16-4 |
57,12 |
100 |
1608 |
0,00009328 |
0,009328358 |
0,50007861 |
0,509407 |
151,1572 |
160 |
17-4 |
57,12 |
100 |
1608 |
0,00009328 |
0,009328358 |
0,50007861 |
0,509407 |
151,1572 |
160 |
8-7 |
171,36 |
200 |
1608 |
0,00009328 |
0,018656716 |
0,50007861 |
0,518735 |
261,812 |
270 |
7-6 |
285,61 |
250 |
1608 |
0,00009328 |
0,023320896 |
0,50007861 |
0,5234 |
337,9978 |
350 |
6-2 |
399,85 |
250 |
1608 |
0,00009328 |
0,023320896 |
0,50007861 |
0,5234 |
399,9244 |
400 |
5-4 |
514,09 |
300 |
1608 |
0,00009328 |
0,027985075 |
0,50007861 |
0,528064 |
453,4716 |
460 |
4-2 |
628,33 |
350 |
1608 |
0,00009328 |
0,032649254 |
0,50007861 |
0,532728 |
501,3317 |
520 |
2-1 |
1069,35 |
440 |
1608 |
0,00009328 |
0,041044776 |
0,50007861 |
0,541123 |
654,0176 |
660 |
6. Эксплуатационный расчет подъемной установки
6.1 Обоснование и выбор схемы подъема полезного ископаемого
Для подъема полезного ископаемого по главному стволу наиболее
эффективным является двухсосудный подъем, т.к. цикл подъема полезного
ископаемого в 2 раза короче, чем при однососудном подъеме, т.е. увеличивается
производительность подъема.
Подъем полезного ископаемого отдают предпочтение в скипах, т.к. они
является более производительным, чем подъем в клетях. Подъем полезного
ископаемого в клетях подразумевает выдачу руды в вагонетках, т.к. максимальный
объем вагонетки, который помещается в клетях, для подъема равен 3 м3.
Следовательно, такой подъем не может обеспечить необходимую производительность.
Бадьевой подъем не применяется, т.к. он является проходческим оборудованием, а
не эксплуатационным.
Принимаем многоканатную подъемную установку, т.к. они применяются
на большегрузных подъемных установках.
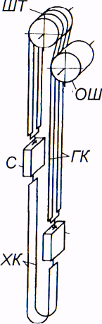
1 - шкив трения
2 - огибающий канат
3 - головной канат
4 - скип
5 - хвостовой канат
Рис.6.1. Схема многоканатной подъемной установки
6.2 Производительность и грузоподъемность
подъемной установки
Полная высота подъема грузов для скиповых установок
Н=Нш+hо+hп, м, (6.1)
где hо - глубина опускания подъемного сосуда ниже
основного откаточного горизонта шахты для его погрузки, м (hо=25 м);
hп - высота переподъема сосуда над поверхностью шахты для его
разгрузки, м (hп=25 м).
Н=480+25+25=530 м
Расчетная часовая производительность скиповой подъемной установки
(6.2)
где kр - коэффициент резерва, учитывающий
неравномерность поступления грузов к канатному подъемнику, (kр=1,15);
zг - число рабочих дней в году, (zг=251 - режим работы
рудника); tч - нормативное число часов работы подъемной установки, ч
(при двух рабочих сменах по 6 ч, tч=12ч).
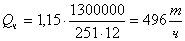
Наивыгоднейшая грузоподъемность грузовой подъемной установки
(6.3)
где ас - коэффициент, учитывающий тип подъемной
установки в отношении количества подъемных сосудов. (ас=1 - при
двухсосудном подъеме); bт - коэффициент оптимальной
продолжительности подъема (bт=4,5 - для многоканатного подъема);
θ - длительность пауз между очередными подъемами, с (θ=20 с).

6.3 Выбор подъемных сосудов
По расчетной наивыгоднейшей грузоподъемности установки, принимаем
скип по технической грузоподъемности [2, табл.1.1.]. Выбираем скип 2СН15-1,
грузоподъемностью Qгр=20т, масса скипа Qс=10,8т.
6.4 Расчет и выбор подъемных канатов
Масса концевого груза скиповой подъемной установки
Q0=Qгр+Qс=20+10,8=30,8 т (6.4)
Высота расположения подшкивной площадки проходческих копров
hк=hп+hап+hд, м, (6.5)
где hк - высота технологического переподъема сосуда над
поверхностью для его разгрузки, м (hп=25м); hап - запас
высоты на случай аварийного переподъема сосуда, м (hап=5м); hд
- дополнительный запас высоты до подшкивной площадки, м (hд=2м).
hк=25+5+5=35 м (6.6)
Максимальная длина отвеса
Но=Нщ+hо+hк=480+25+35
=540м
При высоте подъема Н <600 м канат рассчитывают на статическое
растяжение под действием концевого груза и силы собственного веса каната.
Расчетная линейная масса каната
(6.7)
где m’ - запас прочности по концевой статической нагрузке, (m’=8,5
- для грузовых подъемных установок); ρ0 - условная плотность
каната, кг/м3 (ρ0=9500 кг/м3); σв
- временное сопротивление разрыву проволок каната, Па (σв=1470·106Па);
nк - количество канатов, (nк=4).
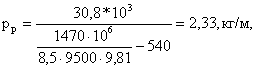
Примем закрытые проволочные канаты, обладающие преимуществами по
сравнению с канатами других типов. Диаметр каната, dк=25 мм, σв=1470·106Па,
линейная масса р=3,65 кг/м, Fсп=628 кН, Fк=532 кН.[2,стр50
табл.1.7]
Проверочный расчет фактического запаса прочности каната
(6.8)
где Fсп - суммарное разрывное усилие проволок каната,
Н; р - линейная масса каната, кг/м.

Канат считается пригодным для последующей эксплуатации при Н <
600м mф>m, 7,81>7,5.
Оценка степени статической неуравновешенности подъемной системы без
хвостового каната
(6.9)
δст<0,5, применение хвостового каната, как и
других способов статического уравновешения подъемных систем, считается
экономически не целесообразным.
6.5 Расчет и выбор подъемной установки
Расчетный диаметр барабана
Dно=kD·dk, мм, (6.10)
где kD - коэффициент соотношения между диаметрами
навивочного органа и каната, (kD=79 - для многоканатных подъемных машин
с отклоняющими шкивами).
Dно=79·25= 1975 мм
Максимальное статическое натяжение головных канатов
Smax=g·(Q0+nк·p·H0)=9,81·(30800+4·3,65·540)=379кН (6.11)
Максимальная разность статических натяжений ветвей канатов для
двухсосудных подъемных установок
Fmax=g·(Qгр-Δ·H),кН, (6.12)
где Δ - разность суммарных линейных масс комплектов хвостовых
и головных канатов (Δ=-р - для установок без хвостовых канатов,
Δ=-3,65кг/м).
Fmax=9,81·(20-(-3,65)·540)=19,5 кН
Предварительно выберем подъемную установку со шкивом трения ЦШ- 2,25х6.
Проведем его проверочный расчет по:
- прочности футеровки канатоведущего шкива;
-отсутствию скольжения каната относительно поверхности шкива.
Статическое натяжение поднимающихся и опускающихся ветвей канатов
Sп=Smax=379 кН; Sоп=Smax
- Fmax=379-19,5=359,5 кН.
Среднее удельное давление на футеровку шкива трения
(6.13)
где DШТ - диаметр шкива трения, м (DШТ=4м).
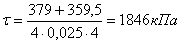
Необходимое условие выполнено. τдоп=2500 кПа>
τ,
где τдоп - допустимое удельное давление на
футеровку шкива трения, кПа.
Условие не скольжения канатов относительно поверхности
канатоведущего шкива
, (6.14)
где f - коэффициент трения между канатом и поверхностью
канатоведущего шкива, (f=0,2); α - угол охвата шкива канатом, рад.

Условие выполняется, окончательно принимаем шкив трения ЦШ-2,25х6.
Табл.6.1. Техническая характеристика подъемных машин с
многоканатным шкивом трения
Параметры |
Значение |
Допустимое
статическое натяжение каната Sд, кН
Допустимая
разность статических натяжений каната Fд, кН
Передаточные
отношения редукторов
Масса
шкива трения mмi,т
Момент
инерции отклоняющих шкивов Jшк, т·м2
|
500
150
7,35;10,5;11,5
8,0
4,0
|
Dно< Dд; Smax<Sд;
Fmax<Fд.
Отклоняющие шкивы многоканатных подъемных машин поставляется
комплектом с выбранной машиной и имеют тот же диаметр, что и канатоведущие
шкивы трения.
6.6 Расположение подъемной машины относительно оси шахты
Подъемные машины с многоканатными шкивами трения располагаются над
устьем шахтных стволов в верхней части башенных копров. При таком расположении
подъемных машин основным расчетным параметром является высота башенного копра,
измеряемая от устья шахтного ствола до оси вращения канатоведущего шкива.
Для многоканатной подъемной системы, имеющей отклоняющий шкив
высота копра расчетная равна
hк=hрб+ hс+ hсп+ hтб+
hпк+ Rош+hош+ hап, м,
где hрб - высота верхней кромки разгрузочного буккера
от уровня устья шахтного ствола, м (hрб=25 м); hс -
высота сосуда в положении разгрузки от низа до верхнего зажима каната, м (hс=11,3м);
hсп -высота свободного переподъема сосуда до входа в верхнее
предохранительное устройство, м (hсп=3 м - согласно ЕПБ); hтб
- длина тормозных брусьев для предохранения головки копра при аварийном
переподъеме сосуда, м (hтб=4 м); hпк - высота
противометанного канала, м (hпк=0,8м); Rош - радиус
отклоняющего шкива, м (Rош=2 м); hош - расстояние по
вертикали между осями отклоняющего и канатоведущего шкивов, м; hап -
дополнительная высота на случай аварийного переподъема, когда тормозной башмак
сосуда достигает верхнего окончания тормозных брусьев, м (hап=3,3м).

где В0 - расстояние между отвесами канатов в шахтном
стволе, м (В0=2,25 м).
hк=30,5+11,3+3+4+0,8+2+10,1+3,3=70 м
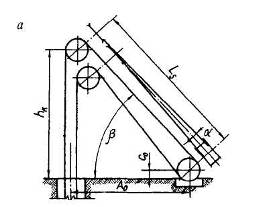
Рис.
6.2. Схема расположения одноканатной подъемной машины
7. Организация
технического обслуживания и ремонта оборудования
Ремонт электромеханического оборудования проектируем выполнять по
смешанной форме организации ремонта, при которой часть ремонтных сил и средств,
(которыми выполняются капитальные ремонты), сконцентрированы в ведении главного
механика комбината (РМЗ). Остальная часть ремонтных сил и средств, (которыми
выполняются все текущие ремонты и технические обслуживания) – в ведении
главного механика рудника (РММ).
Таблица 7.1. Смешанная форма организации ремонтов
Наименование
формы организации ремонтов |
Виды ППР |
К |
Т |
Т2
|
Т1
|
ТО |
Смешанная
форма ремонта |
СП |
СС |
СС |
СС |
СС |
СП–ППР выполняются силами специализированных организаций (РМЗ);
СС - ППР выполняются силами РММ подземного рудника.
Ремонт электромеханического оборудования подземного рудника
проектируем выполнять по системе планово - предупредительных ремонтов по
агрегатно-узловому методу.
Системой планово - предупредительных ремонтов (ППР), называется
совокупность взаимосвязанных инженерно-технических и организационных
мероприятий, запланированных во времени и направленных на поддержание
оборудования в постоянной работоспособности.
Сущность системы ППР заключается в проведении ежесменных осмотров
машин, в результате которых выполняются работы по чистке, мойке, креплению,
регулировке и смазке деталей и узлов, а также установления фактического
состояния деталей и узлов и замене быстроизнашивающихся деталей.
На основе работ профилактического характера к плановым, текущим и
капитальным ремонтам составляется ведомость дефектов, где указывается, какие детали,
и узлы должны быть заменены при ремонте. По данным составляются нормативы
сроков службы (ресурсов), деталей, узлов и машин в целом.
Ремонт электромеханического оборудования рудника проектируем
выполнять по агрегатно-узловому методу.
Сущность агрегатно-узлового метода ремонта в том, что машина
разбирается на узлы, а собирается из ранее отремонтированных и готовых узлов,
находящихся в оборотном фонде, то есть выполняются только сборочно-разборочные
работы. Поэтому длительность простоя машины на ремонте - минимальная, а
выполнение ремонта и изготовление новых узлов в межремонтный период
обеспечивает получение высокого качества ремонтных работ.
Достоинства агрегатно-узлового метода ремонта:
1) сокращение времени технического обслуживания техники и
ремонтов;
2) высокое качество ремонтных узлов и деталей машин, а также
монтажа и ремонта.
Согласно принятой системы ремонтов и «Временного Положения о ППР»
для заданного количества электромеханического оборудования рудника принимаем
следующие виды:
1. Технического обслуживания:
а) ЕО – ежесменное обслуживание;
б) ЕПП – ежесуточная проверка правильности эксплуатации;
в) ТО – техническое обслуживание;
2. Плановых ремонтов:
Т (Т1, Т2) – текущие ремонты;
К–капитальный ремонт;
Ремонтные нормативы приняты по данным «Положения о ППР», и сведены
в табл. 7.2.
Таблица 7.2.
Ремонтные нормативы
Наименование
одноименного оборудования |
Тип, марка |
Межремонтные
периоды, маш·час.
|
Продолжительность
ремонта, ч
|
Трудоемкость
ремонта, чел·ч |
К |
Т2
|
Т1
|
ТО |
1 |
2 |
3 |
4 |
5 |
7 |
Транспортная
машина |
МоАЗ-7405-9586 |
8460
|
2820
|
1410
|
470
|
160
|
32
|
16
|
8
|
1000 |
192 |
72 |
16 |
Подъемная
машина |
ЦШ 2,25х6 |
37800
|
-
|
3780
|
630
|
48
|
-
|
12
|
6
|
380 |
- |
48 |
6 |
Компрессорная
установка. |
К-500-61-2 |
17520
|
-
|
4380
|
730
|
24
|
-
|
6
|
2
|
72 |
- |
12 |
2 |
4М10-100/8 |
27000
|
2000
|
3000
|
1000
|
720
|
330
|
14
|
20
|
1300 |
400 |
180 |
45 |
Вентилятор
главного проветривания |
ВЦД-47,5/490 |
43800
|
-
|
4380
|
730
|
96
|
-
|
48
|
2
|
120 |
- |
48 |
2 |
Насос центробежный
секционный |
ЦНС
300-120…600 |
17520
|
-
|
4380
|
730
|
24
|
-
|
6
|
2
|
72 |
- |
12 |
2 |
Годовое количество ремонтов определяем расчетно-аналитическим
методом без учета времени, отработанного машиной с начала эксплуатации
; (7.1)
; (7.2)
; (7.3)
; (7.4)
; (7.5)
где - количество однотипных машин; - годовое
плановое время работы машин; - календарное время в году, ч; , и - межремонтные периоды
соответственно капитальных, текущих (вторых, первых) ремонтов и технического
обслуживания.
Для погрузочной и транспортной машины,компрессорной установки:
=5124 ч\год (7.6)
Для насосов и вентиляторов главного проветривания.
ч\год (7.7)
Результаты расчета приведены в табл. 7.3.
Годовой объем ремонтных работ определяем по методу трудоемкости по
выражению
(7.8)
где - годовое количество -тых ремонтов и
технических обслуживаний; -трудоемкость -тых ремонтов и
технических обслуживаний.
Годовое
количество ремонтных и технических обслуживаний и объем ремонтных работ
выполняемых своими силами и силами организации ремонтного оборудования
рассчитываем по выражению
, (7.9)
где - годовой объем ремонтных работ,
маш.·ч; -
годовой фонд времени работы ремонтного оборудования,·ч; - коэффициент
использования ремонтного оборудования во времени, = 0,65 – 0,75 для РММ.
 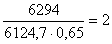
Годовой фонд рабочего времени ремонтного оборудования
рассчитывается по выражению
, ч, (7.10)
где - количество календарных,
праздничных и выходных дней в году; - продолжительность рабочей
смены, ч; -
количество смен; - коэффициент, учитывающий
простои ремонтного оборудования на ремонтах, (КР= 0,95 – 0,97).

Явочный штат ремонтных работ рассчитываем по выражению:
человек (7.11)
где - годовой объем ремонтных работ,
чел·ч; -
годовой фонд рабочего времени одного рабочего, ч; - коэффициент, учитывающий
перевыполнение норм выработки рабочими, занятыми на ремонтах, ( =1,05).
 
Годовой фонд рабочего времени для одного рабочего:
,ч, (7.12)
где - время, на которое сокращается
продолжительность рабочей смены в предпраздничные и предвыходные дни, ( ).

8. Генеральный план промышленной площадки рудника
Поверхность современной шахты это комплекс различных зданий,
сооружений выполняющих определенные технические функции. Территория, на которой
расположен этот комплекс, называется промышленной площадкой рудника. Она как
правила располагается в близи стволов главного, вспомогательного,
вентиляционного. Из поверхностного комплекса зданий и сооружений выделяют так
называемые технологические, вспомогательные цехи и объекты бытового и
хозяйственного обслуживания. В технологический комплекс главного ствола входит
сооружения и оборудования для приема руды и ее технологической обработке. В
этот комплекс также входит здания, копры скипо-клетьевого подъема с приемными
бункерами, машинными зданиями и тд.
1.
Капер
главного ствола
2.
Капер
вспомогательного ствола
3.
АБК
4.
Конвейерная
галерея
5.
Обогатительная
фабрика
6.
Конвейерная
галерея
7.
Бункер
8.
Конвейерная
галерея
9.
Склад
10.
Ремонтная
мастерская
11.
Вентиляторная
и калориферная установки
12.
Котельная
13.
Компрессорная
станция
14.
Установка,
для обеззараживания шахтных вод
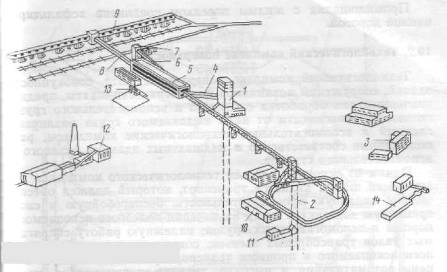
Список литературы
1.
Пухов
Ю.С. рудничный транспорт. М., Недра,1991.
2.
Гришко
А.П., Шелоганов В.И. Стационарные машины и установки. М., МГГУ,-2004.
3.
Попов
В.М. Рудничные водоотливные установки.
4.
Картавый
Н.Г. Стационарные машины. М., Недра,-1981.
5.
Зеленский
О.В. Справочник по проектированию ленточных конвейеров. М., Недра,-1986.
|