Реферат: Типы соединения деталей машин
Реферат: Типы соединения деталей машин
МИНИСТЕРСТВО
ОБРАЗОВАНИЯ И НАУКИ РЕСПУБЛИКИ КАЗАХСТАН
Северо-Казахстанский
государственный университет
им.М. Козыбаева
Факультет:
энергетики машиностроения
Кафедра:
технологии машиностроения
РЕФЕРАТ:
Тема: Типы
соединений деталей машин
Мирошников Константин
Специальность: 5В071200
Машиностроение
Курс 1, группа МС-10
Форма обучения: очная
Руководитель: Сорокин Виталий Владимирович
Петропавловск,
2010
Содержание
Введение
1. Резьбовые соединения
1.1 Резьба
1.2 Основные типы крепежных деталей
1.3 Способы стопорения резьбовых соединений
2. Заклепочные соединения
3. Сварные соединения
3.1 Стыковое соединение
3.2 Нахлесточное соединение
4. Соединения пайкой и склеиванием
4.1 Соединение пайкой
4.2 Соединение склеиванием
5. Клеммовые соединения
6. Шпоночные и зубчатые (шлицевые) соединения
6.1 Шпоночные соединения
6.2 Оценка соединений призматическими шпонками и их
применение
6.3 Зубчатые (шлицевые соединения)
7. Соединение деталей посадкой с натягом
7.1 Оценка и область применения
Заключение
Список литературы
Введение
Деталь – такая часть
машины, которую изготавливают без сборочных операций. Детали могут быть
простыми (гайка, шпонка) или сложными (корпус редуктора).
Среди большого
разнообразия деталей машин выделяют такие, которые применяют почти во всех
машинах (болты, валы, механические передачи и т.д.). Эти детали называют
деталями общего назначения. Все другие детали (поршни, лопатки турбин,
гребневые винты и т.п.) относятся к деталям специального назначения.
Детали общего назначения
применяют в машиностроении в очень больших количествах.
Поэтому любое
совершенствование методов расчета и конструкции этих деталей, позволяющее
уменьшить затраты материала, понизить стоимость производства, повысить
долговечность, приносит большой экономический эффект.
1. Резьбовые соединения
Соединение деталей с
помощью резьбы является одним из старейших и наиболее распространенных видов
разъемного соединения. К ним относятся соединения с помощью болтов, винтов,
шпилек, винтовых стяжек и т.д.
1.1 Резьба
Резьба – выступы,
образованные на основной поверхности винтов или гаек и расположенные по
винтовой линии.
Классификация резьб:
1.
По форме профиля:
Ø упорные;
Ø треугольные;
Ø прямоугольные;
Ø круглые;
Ø трапецеидальные;
2.
По форме основной
поверхности:
Ø цилиндрические;
Ø конические;
3.
По назначению:
Ø крепежные;
Ø ходовые;
Ø специальные;
4.
По направлению
винтовой линии:
Ø правые;
Ø левые.
Методы изготовления
резьбы:
1)
Нарезкой вручную
метчиками или плашками. Способ малопроизводительный. Его применяют в
индивидуальном производстве и при ремонтных работах.
2)
Фрезерованием на
специальных резьбофрезерных станках. Применяют для нарезки винтов больших
диаметров с повышенными требованиями к точности резьбы.
3)
Накаткой на
специальных резьбонакатных станках-автоматах. Этим высокопроизводительным и
дешевым способом изготовляют большинство резьб стандартных крепежных изделий.
Накатка существенно упрочняет резьбовые детали.
4)
Литьем на деталях
стекла, пластмассы, металлокерамики и др.
Основными элементами
резьбы являются диаметр наружный d,
средний d2 и внутренний d1; шаг S,
угол профиля а, высота профиля h
(рис. 31)
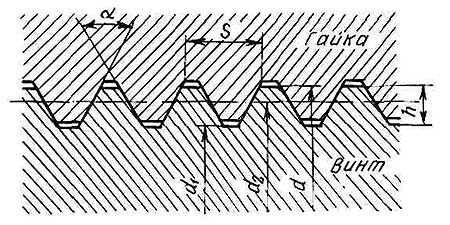
Рис. 1 Элементы резьбы
1.2 Основные типы крепежных деталей
Для соединения деталей
применяют болты, винты, шпильки с гайками (рис.1).
Болтом называется
крепежная деталь, представляющая собой цилиндрический стержень, как правило, с
шестигранной головкой на одном конце и винтовой резьбой на другом. Головки
болтов могут иметь и другую форму: квадратную, прямоугольную, полукруглую с
квадратными головками или усом.
Винт отличается от болта
наличием прорези (шлица) под отвертку. Винты подразделяются на два типа:
крепежные и установочные. Основные типы крепежных винтов различаются по форме
головки (цилиндрическая, полукруглая, потайная, полупотайная).
Шпилька – цилиндрический
стержень, на обоих концах которого нарезана резьба.
Гайка представляет собой
деталь призматической формы, снабженную сквозным, а иногда глухим осевым
резьбовым отверстием.
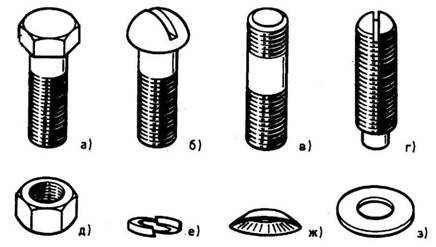
Рис. 1. а — болт; б
винт; в - шпилька; г — установочный винт; д — гайка; e — пружинная шайба; ж
деформируемая шайба; з — плоская шайба
Основным преимуществом
болтового соединения (рис.2) является то, что при нем не требуется нарезать
резьбу в соединяемых деталях. К недостаткам можно отнести следующее: обе
соединяемые детали должны иметь место для расположения гайки или головки винта;
при завинчивании и отвинчивании гайки необходимо удерживать головку винта от
проворачивания; по сравнению с винтовым болтовое соединение несколько
увеличивает массу изделия и искажает его внешние очертания.
Рис.2 Болтовое
соединение, Винтовое соединение.
Винты и шпильки применяют
в тех случаях, когда постановка болта невозможна или нерациональна. Например,
нет места для размещения гайки, нет доступа к гайке, при большой толщине детали
необходимо глубокое сверление и длинный болт и т.п.
Если при эксплуатации деталь
часто снимают и затем снова ставят на место, то ее следует закреплять болтами
или шпильками, так как винты в многократном завинчивании может повредить резьбу
в детали. Повреждение резьбы в этом случае более вероятно, если деталь
изготовлена из малопрочных хрупких материалов, например из чугуна, дюралюминия
и т.п.
Подкладную шайбу ставят
под гайку или головку винта для уменьшения смятия детали (гайкой, если деталь
сделана из менее прочного материала(пластмассы, дерева и т.д.), предохранения
чистых поверхностей деталей от царапин при завинчивании гайки(винта);
перекрытия большого зазора отверстия. В других случаях подкладную шайбу
использовать нецелесообразно. Кроме подкладных шайб применяют стопорные или
предохранительные шайбы, которые предохранят соединение от самоотвинчивания.
Шпонки – это
конструктивный элемент, служащий для соединения с валом деталей передающих
вращательное и колебательное движение. По конструкции шпонки делятся на
призматические, сегментные, клиновые (рис.3).
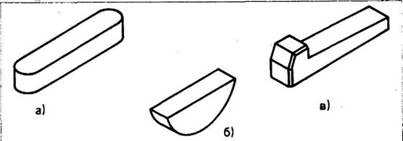
Рис. 3. Шпонки: а
призматическая; б – сегментная, в – клиновая.
1.3 Способы стопорения резьбовых
соединений
Самоотвинчивание
разрушает соединение и может привести к аварии. Предохранение от
самоотвинчивания весьма важно для повышения надежности резьбовых соединений и
совершенно необходимо при вибрациях, переменных и ударных нагрузках. Вибрации
понижают трения и нарушают условие самоторможения в резьбе.
Существует много
способов стопорения или предохранения от самоотвинчивания:
1. Повышают и
стабилизируют трение в резьбе путем постановки контргайки, пружинной шайбы, применения
резьбовых пар в резьбе и т.п. контргайка создает дополнительное натяжение и
трение в резьбе. Пружинная шайба поддерживает натяг и трение в резьбе на
большом участке самоотвинчивания. Кроме того, упругость шайбы значительно
уменьшает влияние вибрации на трение в резьбе, а остальные кромки ее прорези
затрудняют поворот гайки (головки винта) относительно детали при отвинчивании.
2. гайку жестко соединяют
со стержнем винта, например, с помощью шплинта или прошивают группу винтов
проволокой. Способы стопорения этой группы позволяют производить только
ступенчатую регулировку затяжки соединения.
3. гайку жестко соединяют
с деталью, например, с помощью специальной шайбы или планки.
2. Заклепочные соединения
Клепаное соединение -
неразъемное. В большинстве случаев его применяют для соединения листов и
фасонных профилей. Соединение образуют расклепыванием стрежня заклепки,
вставленное в отверстие деталей.
При расклепывании
вследствие пластических деформаций образуется замыкающая головка, а стержень
заклепки заполняет зазор в отверстии. Силы, вызванные упругими деформациями
деталей и стержня заклепки, стягивают детали. Относительному сдвигу деталей
оказывают сопротивление стержни заклепок и частично силы трения в стыке.
Отверстия в деталях
продавливают или сверлят. Сверление менее производительно, но обеспечивает
повышенную прочность. При продавливании листы деформируются, по краям отверстия
появляются мелкие трещины, а на выходной стороне отверстия образуется острая
кромка, которая может вызвать подрез стержня заклепки. Поэтому продавливание
иногда сочетают с последующим рассверливанием.
Клепку (осаживание
стержня) можно производить вручную или машинным способом. Машинная клепка дает
соединения повышенного качества, так как она обеспечивает однородность посади
заклепок и увеличивает силы сжатия деталей. Стальные заклепки малого диаметра
(до 10 мм) и заклепки из цветных металлов ставят без нагрева – холодная
заклепка. Стальные заклепки диаметром больше 10 мм перед установкой в детали нагревают – горячая клепка. Предварительный нагрев заклепок,
облегчает процесс клепки и повышает качество соединения (достигаются лучшее
заполнение отверстия и повышенный натяг в стыке деталей, связанный с тепловыми
деформациями при остывании).
Клепаные соединения
применяются для деталей, материал которых плохо сваривается, и в тех
конструкциях, где важно растянуть во времени развития процесс разрушения.
Например: разрушение одной или нескольких из тысяч заклепок крыла самолета еще
не приводит к его разрушению, но уже может быть обнаружено и устранено при
контроле и ремонте.
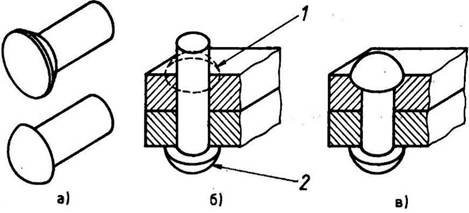
Рис. 3. Клепаное
соединение
3. Сварные соединения
Сварное соединение
неразъемное. Оно образуется путем сваривания материалов деталей в зоне
стыка и не требует никаких вспомогательных элементов. Прочность соединения
зависит от однородности и непрерывности материала сварного шва и окружающей его
зоны. Сварное соединение является наиболее совершенным из неразъемных
соединений, так как лучше других приближает составные детали к цельным. При
сварном соединении проще обеспечить условия равнопрочности, снижения массы и
стоимости изделия.
Применяемые в современном
машиностроении виды сварки весьма разнообразны. Каждый из них имеет свои
конкретные области применения. Из всех видов сварки наиболее широко
распространена электрическая.
Различают два вида электрической
сварки:
1. Электродуговая
сварка: основана на использовании теплоты электрической дуги для
расплавления металла. Для защиты расплавленного металла от вредного действия
окружающего воздуха на поверхность электрода наносят толстую защитную обмазку,
которая выделяет большое количество шлака и газа, образуя изолированную среду.
Этим обеспечивают повышение качества металла сварного шва, механические
свойства которого могут резко ухудшиться под влиянием кислорода и азота
воздуха.
С той же целью производят
сварку под флюсом. Этот вид сварки в настоящее время считается основным видом
автоматической сварки. Производительность автоматической сварки в 10 – 20 раз и
более выше ручной. Повышение производительности достигают путем применения тока
1000 – 3000 А вместо 200 – 500 А при ручной сварке. Это обеспечивает более
рациональное формирование шва и повышает скорость сварки.
В то время как при ручной
сварке образование шва достигается в основном за счет металла электрода, при
автоматической сварке шов формируется в значительной степени за счет
расплавленного основного металла, что не только сокращает время сварки, но и
значительно снижает расход электродного материала. Автоматическая сварка под
слоем флюса обеспечивает высокие и, что особенно важно, однородные, на
зависящие от индивидуальных качеств сварщика механические свойства соединений.
В электрошлаковой сварке
источником нагрева служит теплота, выделяющаяся при прохождении тока от
электрода к изделию через шлаковую ванну. Электрошлаковая сварка предназначена для
соединения деталей большой толщины. Толщина свариваемых деталей практически не
ограничивается. Толщина свариваемых деталей практически не ограничивается. Электрошлаковая
сварка позволяет заменять сложные и тяжелые цельнолитые и цельнокованые конструкции
сварными из отдельных простых отливок, поковок и листов, что значительно
облегчает и снижает стоимость производства. Эта сварка применена и для чугунных
отливок.
2. Контактная сварка
основана на использовании повышенного омического сопротивления в стыке деталей
и осуществляется несколькими способами.
При стыковой контактной
сварке через детали пропускают ток, сила которого достигает нескольких тысяч
ампер. Основное количество теплоты выделяется в месте стыка, где имеется
наибольшее сопротивление; металл в этой зоне разогревается до пластического
состояния или даже до поверхностного оплавления. Затем ток выключают, а
разогретые детали сдавливают с некоторой силой – происходит сварка металла
деталей по всей поверхности стыка. Этот вид сварки рекомендуют применять для
стыковых соединений деталей, площадь поперечного сечения которых сравнительно
невелика.
При точечной контактной
сварке соединение образуется не по всей поверхности стыка а лишь в отдельных
точках, к которым подводят электроды варочной машины.
При шовной контактной
сварке узкий непрерывный или прерывистый шов расположен вдоль стыка деталей.
Эту сварку выполняют с помощью электродов, имеющих форму дисков, которые
катятся в направлении сварки. Точечную и шовную сварку применяют в нахлесточных
соединениях преимущественно для листовых деталей толщиной не более 3 – 4 мм и тонких стенок арматурных стенок. В отличии от точечной шовная сварка образует герметичное
соединение.
Все рассмотренные виды
контактной сварки высокопроизводительны, их широко используют в массовом
производстве для сварки труб, арматуры, кузовов автомобилей, металлической
обшивки железнодорожных вагонов, корпусов самолетов, тонкостенных резервуаров и
т.д.
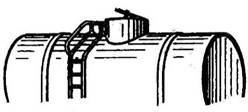
Рис. 4. Сварное
соединение
3.1 Стыковое
соединение
Стыковое соединение во
многих случаях является наиболее простым и надежным. Его следует применять
везде, где допускает конструкция изделия. В зависимости от толщины соединяемых
деталей соединение выполняют с обработкой или без обработки кромок, с подваркой
и без подварки с другой стороны.
При малых толщинах
обработка кромок не обязательна, а при средних и больших толщинах она
необходима по условию образования шва на всей толщине деталей. Автоматическая
сварка под флюсом позволяет увеличить предельные толщины листов, свариваемых
без обработки кромок, примерно к два раза.
Сварить встык можно не
только листы или полосы, но также трубы, уголки, швеллеры и другие фасонные
профили. Во всех случаях составная деталь получается близкой к целой.
Стыковое соединение может
разрушаться по шву, месту сплавления металла шва с металлом детали в зоне термического
влияния. Зоной термического влияния называют прилегающий ко шву участок детали,
в котором в результате нагревания при сварке изменяются механические свойства
металла. Понижение механических свойств в зоне термического влияния особенно
значительно при сварке термически обработанных, а также наклепанных сталей. Для
таких соединений рекомендуют термообработку и наклеп после сварки. Практикой
установлено, что при качественном выполнении сварки разрушение соединения
стальных деталей происходит преимущественно в зоне термического влияния.
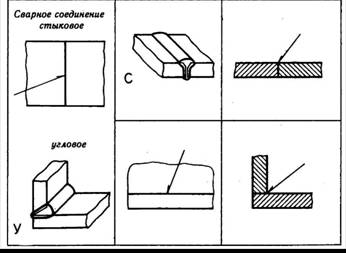
Рис. 5. Виды сварных
соединений
3.2 Нахлесточное
соединение
Выполняется с помощью
угловых швов.
В зависимости от формы
поперечного сечения различают угловые швы:
Ø нормальные – наиболее распространены
на практике;
Ø улучшенные;
Ø вогнутые – снижают концентрацию
напряжений и рекомендуются при действии переменных нагрузок. Вогнутость шва
достигается обычно механической обработкой, которая значительно увеличивает
стоимость соединения. Поэтому такой шов применяют только в особых случаях,
когда оправдываются дополнительные расходы;
Ø выпуклые – образуют резкое изменение
сечения деталей в месте соединения, что является причиной повышенной
концентрации напряжений. В нагруженных силовых конструкциях не рекомендуется.
4. Соединение пайкой и склеиванием
В отличии от сварки пайка
и склеивание позволяют соединять детали не только из однородных, но и из
неоднородных материалов, например: сталь с аллюминием6 металлы со стеклом,
графитом, фарфором, керамика с полупроводниками: пластмассы, дерево, резина и
пр.
При пайке и склеивании
кромки детали не расплавляются, что позволяет более точно выдерживать их
размеры и форму, а также производить повторные ремонтные соединения. По
прочности паяные и клееные соединения уступают сварным в тех случаях, когда
материал деталей обладает достаточно хорошей свариваемостью. Исключение
составляют соединения тонкостенных элементов типа оболочек, когда имеется
опасность прожога деталей при сварке.
Применение пайки и
склеивания в машиностроении возрастает в связи с широким внедрением новых
конструкционным металлов (например: пластмасс) и высокопрочных легированных
сталей, многие из которых плохо свариваются. Примерами применения пайки и
склеивания в машиностроении могут служить радиаторы автомобилей и тракторов,
камеры сгорания жидкостных реактивных двигателей, лопатки турбин, топливные и
масляные трубопроводы и др.
Пайка и склеивание
является одним из основных видов соединения в приборостроении, в том числе и
радиотехнике, где они являются преимущественно связующими, а не силовыми
соединениями.
Процессы пайки и
склеивания сравнительно легко поддаются механизации и автоматизации. Во многих
случаях применение пайки и склеивания приводит к значительному повышению
производительности труда, снижению массы и стоимости конструкций.
Эффективность применения
паяных и клееных соединений, их прочность и другие качественные характеристики
в значительной степени определяются качеством технологического процесса:
правильным подбором типа припоя и клей, температурным режимом, очисткой
поверхностей стыка, их защитой от окисления и др.
4.1 Соединения пайкой
Соединение образуется в
результате химических связей материала деталей и присадочного материала,
называемого припоем. Температура плавления припоя (например, олово) ниже
температуры плавления материала деталей, поэтому в процессе пайки детали
остаются твердыми. При пайке расплавленный припой растекается по нагретым
поверхностям стыка деталей. Поверхности детали обезжиривают, очищают от окислов
и прочих посторонних частиц. Без этого нельзя обеспечить хорошую смачиваемость
поверхности припоем и заполнение зазора в стыке.
Размер зазора в стыке
деталей в значительной мере определяет прочность соединения. Уменьшение зазора
до некоторого предела увеличивает прочность. Это связано, во – первых, с тем,
что при малых зазорах появляется эффект капиллярного течения, способствующий
заполнению зазора расплавленным припоем; во – вторых, диффузионный процесс и
процесс растворения материалов деталей и припоя может распространяться на всю
толщину паяного шва (диффузионный слой и слой раствора прочнее самого припоя). Чрезмерно
малые зазоры препятствуют течению припоя. Размер оптимального зазора зависит от
типа припоя и материала деталей. Для пайки стальных деталей тугоплавкими припоями
(серебряными и медными) приближенно рекомендуется зазор 0,003 – 0,15 мм, при легкоплавких припоях (оловянных) - 0,05 – 0,2 мм.
Необходимость малых и
равномерно распределенных зазоров является одним из недостатков пайки,
ограничивающим ее применение, в особенности для крупногабаритных конструкций.
По сравнению со сваркой пайка требует более точной механической обработки и
сборки деталей перед пайкой.
Нагрев припоя и деталей
при пайке осуществляется паяльником, газовой горелкой, ТВЧ, в термических
печах, погружением в ванну с расплавленным припоем и др.
Для уменьшения вредного
влияния окисления поверхностей деталей применяют специальные флюсы (на основе
буры, хлористого цинка, канифоли); паяют в среде нейтральных газов (аргона) или
в вакууме.
В качестве припоев
применяют как чистые металлы, так и сплавы. Чаще других применяют сплавы на
основе олова, меди, серебра.
При соединении стальных
деталей прочность материала деталей обычно больше прочности материала шва. В
побочных случаях условие равнопрочности можно обеспечить только для
нахлесточных соединений.
4.2 Соединение склеиванием
Конструкция клеевых
соединений подобна конструкции паяных, только припой здесь заменен клеем, а
образование соединения выполняют без нагрева деталей. Соединение осуществляется
за счет сил адгезии (сил сцепления) в процессе затвердевания твердого клея.
Имеются клеевые составы с избирательной адгезией к каким – либо определенным
металлам – это специальные клеи (например, резиновые); с высокой адгезией к
различным металла (например, к металлам, керамике, дереву, пластмассам и др.)
это универсальные клеи.
В процессе склеивания
выполняют ряд последовательных операций: подготовку поверхностей деталей,
нанесение клея, сборку соединения, выдержку при соответствующих давлении и
температуре. Подготовка деталей обычно заключается в их взаимной пригонке,
образовании шероховатости путем зачистки наждачной шкурки или пескойструнным
аппаратом, удалении пыли и обезжиривании с помощью органических растворителей. Шероховатость
увеличивает поверхность склеивания. Клей наносят кистью или пульверизатором.
Сравнительно длительная выдержка, необходимая для полимеризации, является одним
из недостатков клеевых соединений.
Прочность клеевого
соединения в значительной степени зависит от толщины слоя клея, которую
рекомендуется назначать в пределах 0,05-0,15 мм. Толщина слоя клея зависит от его вязкости и давления при склеивании. Клеевые соединения лучше работают на сдвиг,
хуже на отрыв. Поэтому предпочтительны нахлесточные соединения. Для повышения
прочности применяют комбинацию клеевого соединения с резьбовым, сварным или
заклепочным.
Качество клеевого
соединения характеризуется не только его прочностью, но и водостойкостью,
теплостойкостью и другими показателями.
5. Клеммовые
соединения
Применяют для закрепления
деталей на осях и валах, цилиндрических колоннах, кронштейнах и т.д.
По конструктивным
признакам различают два типа клеммовых соединений: а) со ступицей, имеющей
прорезь; б) с разъемной ступицей. Разъемная ступица несколько увеличивает массу
и стоимость соединения, но при этом становится возможным устанавливать клемму в
любой части вала независимо от формы соседних участков и других расположенных
на валу деталей.
При соединении деталей с
помощью клемм используют силы трения, которые возникают от затяжки болтов, но
клеммовые соединения не рекомендуют применять для больших нагрузок.
Достоинство клеммового
соединения: простота монтажа и демонтажа, самопредохранение от перегрузки, а
также возможность перестановки и регулировки взаимного расположения деталей как
в осевом, так и в окружном направлениях. Наличие больших зазоров в соединении
может привести к разрушению клеммы от напряжений изгиба. Практически
конструкция с большим зазором считается дефектной.
6. Шпоночные и
зубчатые (шлицевые) соединения
Служат для закрепления
деталей на осях и валах. Такими деталями являются шкивы, зубчатые колеса,
муфты, маховики, кулачки и т.д. Соединения в основном нагружаются вращающим
моментом.
6.1 Шпоночные
соединения
Все основные виды шпонок
можно разделить на клиновые и призматические. Первая группа шпонок образует
напряженные (в соединении образуется напряжение до приложения внешней
нагрузки), а вторая – ненапряженные соединения.
1. Соединение
клиновыми шпонками (например, врезной клиновой шпонкой) характеризуется
свободной посадкой ступицы на вал (с зазором); расположением шпонки в пазе с
зазорами по боковым граням (рабочими являются широкие грани шпонки); передачей
вращающегося момента от вала к ступице в основном силами трения, которые
образуются в соединении от запрессовки шпонки. Запрессовка шпонки смещает
центры вала и ступицы на величину ∆, равную половине зазора и деформации
деталей. Это смещение вызывает дисбаланс и неблагоприятно сказывается на работе
механизма при больших частотах вращения.
Клиновая форма шпонки
может вызвать перекос детали, при котором ее торцовая плоскость не будет
перпендикулярна оси вала. Обработка паза в ступице с уклоном шпонки, создает
дополнительные технологические трудности и часто требует индивидуальной
пригонки шпонки по пазу. Такая пригонка совершенно недопустима в условиях
массового производства. Эти недостатки послужили причиной того, что применение
клиновых шпонок резко сократилось в условиях современного производства.
Значительное сокращение применения клиновых шпонок позволяет не рассматривать в
настоящем курсе их конструктивные разновидности и расчет на прочность.
2. Соединение
призматическими шпонками ненапряженное. Оно требует изготовление вала и
отверстия с большой точностью. Во многих случаях посадка ступицы на вал
производиться с натягом. Момент передается с вала на ступицу боковыми узкими
гранями шпонки. При этом на них возникает напряжение смятия σ см, а в
продольном сечении шпонки – напряжение среза τ.
Параллельность граней
призматической шпонки позволяет осуществлять подвижные в осевом направлении
соединения ступицы с валом (коробки скоростей и др.). силы трения, возникающие
при перемещении ступицы в подвижном соединении могут нарушить правильное
положение шпонки, поэтому ее рекомендуют крепить к валу винтами. В некоторых
конструкциях подвижных соединений целесообразно применять короткие шпонки,
прикрепленные к ступице.
6.2 Оценка соединений
призматическими шпонками и их применение
Призматические шпонки
широко применяют во всех отраслях машиностроения. Простота конструкции и
сравнительно низкая стоимость – главные достоинства этого вида соединений.
Отрицательные свойства:
соединение ослабляет вал и ступицу шпоночными пазами; концентрация напряжения в
зоне шпоночной канавки снижает сопротивление усталости вала; прочность
соединения ниже прочности вала и ступицы, в особенности при переходных посадках
или посадках с зазором. Поэтому шпоночные соединения не рекомендуют ля
быстроходных динамически нагруженных валов. Технологическим недостатком
призматических шпонок является трудность обеспечения их взаимозаменяемости,
т.е. необходимость пригонки или подбора шпонки по пазу, что ограничивает их
применение в крупносерийном и массовом производстве. Пригонкой стремятся
обеспечить устойчивое положение шпонки в пазах, так как перекос (выворачивание)
шпонки значительно ослабляет соединение. Сегментная шпонка с глубоким пазом в
этом отношении обладает преимуществом перед простой призматической шпонкой. Ее
предпочитают применять при массовом производстве.
6.3 Зубчатые
(шлицевые) соединения
Зубчатые соединения
образуются при наличии наружных зубьев на валу и внутренних зубьев в отверстии
ступицы. Размеры зубчатых соединений, а также допуски на них стандартизованы.
Зубья на валах получают
фрезерованием, строганием или накатыванием. Протягивание
высокопроизводительный способ и широко применяется в массовом производстве. Для
отделочных операций используют шлифование, дорнирование и др.
Стандартом
предусмотрены три серии соединений:
· Легкая;
· Средняя;
· Тяжелая.
Они отличаются высотой и
числом зубьев, число зубьев изменяется от 6 до 20. У соединений тяжелой серии
зубья выше, а их число больше, что позволяет передавать больше нагрузки.
По форме профиля
различают зубья
· Прямобочные - соединения с
прямобочными зубьями выполняют с центрированием по боковым граням, по наружному
или внутреннему диаметрами.
· Эвольвентные - соединения с
эфольвентными зубьями предпочтмтельны для больих диаметров валов, когда для
нарезания зубьев в отверстии и на валу могут быть использованы весьма
совершенные технологические способы, применяемые для зубчатых колес. Для
сравнительно малых и средних диаметров преимущественно применяют соединения с прямобочными
зубьями, так как эвольвентные протяжки дороже прямобочных. (это связано с
трудностями образования режущих кромок на боковых поверхностях фасонных
профилей эвольвентных зубьев протяжки).
· Треугольные – мало распространены.
7. Соединения деталей
посадкой с натягом
Соединение двух деталей
по круговой цилиндрической поверхности можно осуществить непосредственно без
применения болтов, шпонок и др. Для этого достаточно при изготовлении деталей
обеспечить натяг посадки, а при сборке запрессовать одну деталь в другую.
Натягом N называется положительная разность
диаметров вала и отверстия: N = B – A. После сборки вследствие упругих и пластических деформаций
диаметр d посадочных поверхностей становится
общим. При этом на поверхности возникают удельное давление р и
соответствующие ему силы трения. Силы трения обеспечивают неподвижность
соединения и позволяют воспринимать вращающий момент в осевую силу. Защемление
вала во втулке позволяет, кроме того, нагружать соединение изгибающим моментом.
Нагрузочная способность
соединения, прежде всего, зависит от натяга, величину которого устанавливают в
соответствии с нагрузкой. Практически натяг не очень невелик, он измеряется
микрометрами и не может быть выполнен точно. Неизбежные погрешности приводят к
рассеиванию натяга а следовательно и к рассеиванию нагрузочной способности
соединения.
Сборку соединения
выполняют одним из трех способов: прессованием, нагревом втулки , охлаждением
вала.
Прессование
распространенный и несложный способ сборки. Однако этому способу свойственны
недостатки: смятие и частичное срезание (шабровка) шероховатостей посадочных
поверхностей, возможность неравномерных деформаций деталей и повреждения от
торцов. Шабровка и смятие шероховатостей приводят к ослаблению прочности
соединения до полутора раз по сравнению со сборкой нагревом или охлаждением.
Для облегчения сборки и уменьшения шабровки концу вала и краю отверстия
рекомендуется придавать коническую форму.
Шабровка поверхностей
контакта устраняется полностью при сборке по методу нагревания втулки (200 -
400˚С) или охлаждения вала (твердая углекислота -79 ˚С). Недостатком
метода нагревания является возможность изменения структуры металла, появления
окалины и коробления. Метод охлаждения свободен от этих недостатков.
7.1 Оценка и область
применения
Основное положительное
свойство соединения с натягом – его простота и технологичность. Это
обеспечивает сравнительно низкую стоимость соединения и возможность его
применения в массовом производстве. Хорошее центрирование деталей и распределение
нагрузки по всей посадочной поверхности позволяют использовать соединение в
современных высокоскоростных машинах.
Существенный недостаток
соединения с натягом – зависимость его нагрузочной способности от ряда
факторов, трудно поддающихся учету: широкого рассеивания величин коэффициента
трения и натяга, влияние рабочих температур на прочность соединения и т.д. К
недостаткам соединения также относятся наличие высоких сборочных напряжений в
деталях и уменьшение их сопротивления усталости вследствие концентрации
давления у краев отверстия. Влияние этих недостатков снижается по мере
накопления результатов экспериментальных и теоретических исследований,
позволяющих совершенствовать расчет, технологию и конструкцию соединения.
Развитие технологической культуры и особенно точности производства деталей
обеспечивает этому соединению все более широкое применение. С помощью натяга с
валом соединяют зубчатые колеса, маховики, подшипники качения, роторы
электродвигателей, диски турбин и др. Соединения с натягом могут быть основными
вспомогательными. В первом случае большая доля нагрузки воспринимается
посадкой, а шпонка только гарантирует прочность соединения. Во втором случае
посадку используют для частичной разгрузки шпонки и центрирования деталей.
Заключение
Детали, составляющие
машину связаны между собой тем или иным способом. Эти связи можно разделить на
подвижные (различного рода шарниры, подшипники и т.д.) и неподвижные
(резьбовые, сварные и т.д.). Неподвижные связи в технике называют соединениями.
Соединения являются
важными элементами конструкций. Многие аварии и прочие неполадки в работе машин
и сооружений обусловлены неудовлетворительным качеством соединений.
Основным критерием
работоспособности расчета соединений является прочность. Необходимо стремиться
к тому, чтобы соединение было равнопрочным с соединяемыми элементами.
Желательно, чтобы соединение не искажало форму изделия, не вносило
дополнительных элементов в его конструкции и т.п.
По признаку разъёмности
все виды соединений можно разделить на разъемные и неразъемные:
1) Разъемные соединения
позволяют разъединять детали без всяких повреждений. К ним относятся резьбовые,
штифтовые, клеммовые, шпоночные, шлицевые и профильные соединения.
2) Неразъемные соединения
не позволяют разъединять детали без их повреждений. Применение неразъемных
соединений обусловлено в основном технологическими и экономическими
требованиями. К этой группе соединений относятся заклепочные, сварные и
соединения с натягом.
Список литературы
1.
Артоболевский И.
И. Теория механизмов и машин. – М.: Наука, 1988.
2.
Биргер И. А.,
Иосилевич Г. Б. Резьбовые и фланцевые соединения. – М.:Машиностроение,1990.
3.
Воробьев Н. В.
Цепные передачи. – М.: Машиностроение, 1968.
4.
Детали машин.
Атлас конструкций. Под ред. Решетова Д. Н. Части I и II. =
М.:Машиностроение, 1992.
5.
Иванов М. Н.,
Иванов В.Н. Детали машин. Курсовое проектирование. – М.: Высшая школа, 1975.
6.
Иосилевич Г. Б.
Детали машин. – М.: Машиностроение, 1988
7.
Кудрявцев В. Н.
Детали машин. – Л.: Машиностроение, 1980.
8.
Николаев Г. А.,
Винокуров В. А. Сварные конструкции. Расчет и проектирование. – М.:
Машиностроение,1990.
9.
Решетов Д. Н.
Детали машин. – М.: Машиностроение, 1989.
10.
Хряпин В. И.
Справочник паяльщика. – М.:Машиностроение, 1981.
|