Дипломная работа: Вплив легування цинком на властивості МОН-структур
Дипломная работа: Вплив легування цинком на властивості МОН-структур
МІНІСТЕРСТВО ОСВІТИ І НАУКИ УКРАЇНИ
НАЦІОНАЛЬНИЙ УНІВЕРСИТЕТ
“ ЛЬВІВСЬКА ПОЛІТЕХНІКА”
Інститут
телекомунікацій, радіоелектроніки та електронної техніки
Кафедра
напівпровідникової електроніки
ДИПЛОМНА РОБОТА
Вплив легування цинком на властивості
МОН-структур.
Виконав:
Студент групи ФБЕ-61
Ревула Р.Л.
Науковий керівник:
ст.викл., Логуш О.І.
Консультант з економічної частини:
доц., Мороз Л.Г.
Консультант
з охорони праці:
доц., Яцюк Р.А.
ЛЬВІВ-2002
Зміст
Вступ
1.
ЛІТЕРАТУРНИЙ ОГЛЯД
1.1.
Методи вирощування плівок термічного SiO2.
1.2.
Основні властивості диоксиду кремнію та меж розділу з напівпровідником та
металом.
1.3
. Гетерування
дефектів в технології напівпровідникових приладів.
2.
МЕТОДИКА ЕКСПЕРИМЕНТУ
2.1.
Методика вирощування плівок термічного SiO2 з одночасним легуванням
в процесі росту.
2.2.
Визначення параметрів технологічного процесу.
2.3.
Методика дослідження
дефектності діелектричних плівок.
2.4.
Методика вимірювання характеристик систем Si-SiO2.
3.
РЕЗУЛЬТАТИ ДОСЛІДЖЕНЬ.
3.1.
Дослідження пористості плівок термічного SiO2.
3.2
Взаємозв’язок структурної досконалості монокристалічної кремнієвої підкладки і
плівокSiO2..
3.3.
Гетеруюча дія цинку. Оптимізація технологічного процесу за концентрацією
домішки..
3.4.
Електрофізичні характеристики структур.
Висновки.
4.
Охорона праці.
5.
Економічна частина.
Література.
ВСТУП
Використання напівпровідників в
електроніці пройшло довгий шлях – від першого детектора на кристалі сульфіду
свинцю і до сучасної мікро ЕОМ, яка виконана на кремнієвій пластині, площею
меншою 1 см2. Такий результат досягнутий завдяки успіхам технології,
яка, в свою чергу, спирається на фізичну електроніку. В наші дні розвиток
електроніки безперервно стимулюється успіхами в області фізики напівпровідників
і в області технології виробництва нових напівпровіднкових структур та
об’єднання їх у великі інтегральні схеми (ВІС).
Підвищення ступеня інтеграції ВІС та
пов’язана з цим реалізація граничних розмірів елементів та, відповідно,
граничних значень параметрів вимагає якісного вдосконалення практично всіх
технологічних процесів створення схем. Зокрема, процес окислення повинен
вдосконалюватися в напрямку зменшення товщини та дефектності шару оксиду.
Перехід від топологічної норми 2 мкм до 0.5мкм вимагає зменшення товщини оксиду
від 0.4-0.8 до 0.1 -0.4 мкм, а його пористості від 10 до 1 см-2 .
Зі сказаного очевидно, що виробництво
великих і надвеликих ІМ представить підвищені вимоги до якості вихідних
матеріалів. Водночас, зберегти властивості навіть ідеального злитку в реальному
технологічному процесі неможливо, так як в кремній вносяться домішки і
виникають дефекти. Щоб зменшити вплив цих домішок і дефектів на параметри і
надійність мікросхем, в технологічні маршрути вводять спеціальні операції
гетерування, завдяки чому вдається зберегти якість робочих областей приладу на
заданому рівні.
Вирощування легованих плівок SіO2, як відомо
з літератури [1], є одним з методів модифікації електричних параметрів як окремих елементів, так і схеми в
цілому. Причому, в залежності від
необхідності досягнення заданих параметрів приладу використовують для легування
як стандартні, так і нетипові домішки кремнію. Рівні легування використовують
також різні: від найменших до суттєвих, аж до утворення елемент силікатного
скла. На даний час процес впливу домішок на характеристики МДН-структур
досліджений недостатньо.
Домішки можуть створювати під дією
зовнішніх факторів,
зокрема радіації, різні типи радіаційно активних дефектів, які будуть приводити
до деградації параметрів приладів. Без всебічного дослідження впливу легування
на електрофізичні параметри структур, а також їх модифікації під дією зовнішніх
факторів неможливе забезпечення стабільності та довговічності роботи приладів.
Впровадження методів домішкового
гетерування також неможливе без дослідження впливу легування на електрофізичні
властивості структур.
Метою цієї дипломної роботи є
всебічне дослідження зарядових характеристик та параметрів розподілу
МОН-структур з легованим в процесі гетерування дефектів шарів SіO2
та структур в цілому.
Для дослідження вказаних параметрів
вибрані стандартні методи С(V) і C(t)–характеристик.
1. ЛІТЕРАТУРНИЙ ОГЛЯД
Термічне окислення кремнію здійснюється в системах
проточного типу в атмосфері, що містить кисень, вуглекислий газ, пари води з використанням
в якості транспортуючих газів аргону, водню, кисню, або в замкнутих системах
при високому тиску окислювача.
Головна відмінність між окисленням в
парах води і в сухому кисні полягає в тому, що
дифундуючою крізь плівку окислу речовиною є не
вода, а молекули або іони кисню і гідроканальних
груп. Дослідження з допомогою звичайної методики
мічених атомів продемонструвало, що ріст окислу здійснюється не на межі газ -
оксид, а на межі окисел - кремній. [2].
Кінетика окислення в області низьких температур обумовлюється найчастіше не
дифузією кисневих іонів, а швидкістю реакції на
межі розділу. Відхилення від параболічного закону в
бік лінійності спостерігається при температурах нижче 1300 К.
Установка для окислення в сухому кисні зображена на
рис.1.1. Як осушувач можна використовувати
виморожуючу пастку, хімічний поглинач або інший пристрій, що дозволяє знизити вміст вологи в
кисні до точки роси - 200 К. Фільтр служить для видалення частинок розміром 0.5
мкм і вище.
Криві окислення при таких умовах
виглядатимуть, як на рис.1.2. [3]. У високотемпературній області експериментальні
дані добре узгоджуються одне з одним, в низькотемпературній - спостерігається
великий розкид. Отримані в області високих температур результати добре описуються
параболічним рівнянням:
x2 = 21. 2 t ехр(-1. 33/Т)= t×10(1. 326-6100/T)
(1),
де: х
- товщина плівки, нм, t - час
окислення, хв, Т - температура
процесу, К.
О2
4
Рис. 1.1. Окислення в сухому кисні:
1-осушувач;2 – фільтр;
2
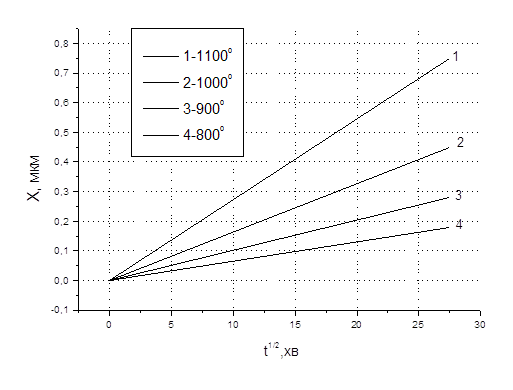
– піч для окислення; 4
– термопара.
Рис. 1.2. Окислення в сухому кисні при тиску 1 ат.
Рис. 1.3. Ріст оксиду
кремнію у вологих газах.
Висока енергія активації, характерна для окислення в сухому кисні, відображає міцність зв’язків кисневих
іонів в окислі. Про це свідчить також енергія
активації дифузії кисню
в кварці.
Установка для окислення кремнію в вологому кисні - це
система, в якій сухий кисень із балону спочатку пропускається
через барботер, а потім
надходить до печі для окислення. Вміст вологи в потоці газу визначається температурою барботера та швидкістю потоку.
Оскільки окислення в водяних парах відбувається
набагато швидше, ніж в сухому кисні, вміст вологи в потоці газу-носія є найважливішим фактором, що зумовлює швидкість
окислення при заданих значеннях часу та
температури. Майже по всьому діапазону типових значень температури
водяної бані заміна кисню інертним газом-носієм не впливає суттєво на ріст окислу, хоча, як видно з рис. 3, при
температурі водяної бані 300
К склад газу-носія може відчутно впливати на швидкість росту [3].
Тут, як і
при окисленні в парах води, необхідний підігрів магістралей, що з’єднують водяну баню з реактором. Бажана також
фільтрація газу-носія, хоча пробулькування газу через воду саме по собі
здійснює на нього фільтруючу дію, відкидаючи
більшість частинок, що захоплюються, як правило, субмікронними фільтрами.
Головна відмінність окислення в вологому кисні від
процесу, який протікає в сухому кисні, або в парах
води, полягає в легкій зміні концентрації окислювача. При окисленні
в потоці водяної пари окислювачем є вода при парціальному тиску 1 атм,
при окисленні в
сухому кисні -
кисень при тиску 1 атм. В установці для окислення у вологому кисні, як окислювач
використовується суміш води і кисню, причому співвідношення цих компонентів припускає зміни. В принципі можна змінювати швидкість
окислення від величини, що відповідає 100% вмісту кисню, до величини, що відповідає 100% вмісту води. Застосувавши аргон або азот як
газ-носій та знизивши температуру барботера до 290 К, досягнемо меншої швидкості окислення, ніж в сухому
кисні. Практично температура барботера буває не нижчою від кімнатної, а потік газу-носія
складає не менше 200 см /хв
для реактора діаметром 150 мм.
При окисленні у вологому кисні при температурі 1300 К величина константи параболічного
рівняння швидкості знаходиться між відповідними значеннями для окислення в сухому кисні (3.6 х 10-4
мкм2/хв) та для окислення в парах води (99 х 10-4 мкм2/хв). Величина константи
швидкості залежить від парціального тиску водяних парів. Значення констант не
змінюються при зміні потоку газу від 30 до 200 см3/хв, що свідчить про насичення
газу-носію протягом всього процесу окислення. Різниця між константами швидкості
в атмосфері інертного газу або кисню приблизно дорівнює константі швидкості
окислення в сухому кисні (3.6х10-4 мкм2/хв
при 1400 К).
Енергія активації окислення в
вологому кисні зменшується зі збільшенням концентрації парів води, що пов’язано з різницею між швидкостями
потоку кисню, а також з різними температурними діапазонами процесів окислення.
Енергія активації знаходиться
в діапазоні від 0.8 еВ для водяної пари до 133
еВ, що відповідає сухому кисню.
Експериментально знайдені значення складали 1.6
еВ при окисленні в вологому аргоні при температурі
барботера 290 К [4].
Легування плівок диоксиду кремнію найкраще здійснювати в процесі росту.
При цьому легуючу домішку необхідно вводити в реактор в вигляді пари. Легування
плівок має свої відмінності при їх вирощуванні в “вологих” та “сухих”
процесах[5].
При вирощуванні плівок в атмосфері вологого кисню
домішку цинку найкраще розчиняти в приготовленому для барботування розчині. Як
вихідна речовина при цьому використовується хлорид цинку.
Незважаючи на те, що згадана сіль
надзвичайно гігроскопічна, при розчиненні у воді спостерігається помутніння
розчину при гідролізі пов’язане з наявністю в ньому завислих комплексів, в
склад яких входять не розкладені на іони молекули ZnCl2. Хлорид
цинку повністю розчиняється у воді при надлишку іонів хлору. Тому, для повного
розчинення солі у воді, розчин ZnCl2 необхідно титрувати соляною
кислотою до повної прозорості, або відфільтровувати завислі комплекси через
мікропористий фільтр.
Як згадано в [6,7] для барботування
використовується вихідний розчин хлориду цинку концентрації 1 - 3%, або, при
миттєвому випаровуванні розчину в реакторі, 0,001 - 0,025% розчин. В цьому
випадку готується вихідний 1% розчин ZnCl2, який потім розводиться
деіонізованою водою до необхідної концентрації. Миттєве випаровування
попередньо приготованого розчину здійснюється шляхом введення його в реактор через
капіляр з витратою 10 мл/хв.
1.2.
Основні властивості диоксиду кремнію та меж розділу з
напівпровідником та металом.
У
літературі щодо властивостей кремнію наводяться різні конкретні значення
величин параметрів, що характеризують властивостей оксидів кремнію. Очевидно,
що ці залежать від експериментальних умов вирощування оксиду. Наприклад.
Коефіцієнт заломлення плівок оксиду, вирощеного в сухому кисні, зменшується із
збільшенням температури, досягаючи постійного значення 1.4620 при температурі
вище 1190 °С. Швидкість травлення термічних оксидів при
кімнатній температурі в HF (4.9%) складає 100 нм/хв і змінюється залежно від
температури та концентрації травника. Крім того, швидкість травлення залежить
від густини оксиду та від температури окислення.
В тонких оксидних плівках значно впливає на
властивості окислу межа розділу фаз.
Здатність шару SiO2
служити локальним маскуючим покриттям при дифузії атомів легуючої домішки при
підвищених температурах – дуже корисна властивість для технології формування
ІС. В процесі маскування поверхні кремнію від дифузії домішки, оксид
перетворюється в склоподібну фазу – так зване домішковосилікатне скло.
Значення дифузійних констант для
різних легуючих домішок в SiO2 від концентрації домішок,
властивостей та структури SiO2.
Найчастіше для створення в кремнію
областей з провідністю n-типу застосовують Р, Sb та As, а для формування
області з провідністю р-типу – В. ці домішки мають малі коефіцієнти дифузії в
оксиді, тому оксид може застосовуватись для маскуванні при дифузії домішки в
кремнію. Що стосується галію та алюмінію, то при їх використанні застосовувати
окисел кремнію для маскування не можна. Найчастіше плівки оксиду, що
використовують для маскування традиційних домішок в стандартних технологічних
процесах формування напівпровідникових приладів, мають товщину 0.5-0.7 мкм.
1.2.1.
Заряд в
окислі.
Межа розділу Si-SiO2 є
перехідною областю між кристалічним кремнієм і аморфним кварцевим склом, як
щодо положення атомів, так і щодо стехіометрії. Різні за природою заряди та
пастки носіїв супроводжують термічно окислений кремній, частина з них зв’язана
з перехідною областю. Заряд на межі розділу може індукувати заряд протилежної
полярності в розташованій під нею області кремнію, впливаючи на і деальність
характеристик МОН-приладу та цим самим на вихід якісних виробів і їх
надійність.
На рис. 1.4. показані основні види
зарядів, зв’язаних з оксидом. Вони записуються:
N=Q/q,
де Q(Кл/см2) –
результуючий ефективний заряд на одиницю площі на межі розділу – Si-SiO2;
N (см-2) – результуюче число зарядів на одиницю площі на межі
розділу Si-SiO2; q – заряд електрона.
Заряд поверхневих станів - це заряд
електронних станів, що локалізовані на границі розділу SI-SiO2 і
енергія яких лежить в глибині забороненої зони напівпровідника. Ці поверхневі
стани (їх називають також швидкими) можуть досить швидко перезаряджатися,
обмінюючись електронами (дірками) з кремнієм. Поверхневі стани зумовлені
надлишковими атомами кремнію, надлишковим киснем або домішковими атомами.
Основною причиною виникнення цих станів є те, що сама межа розділу є порушенням
просторової періодичності кристалічної решітки. В сучасних МОН-структурах, які
отримують шляхом термічного окислення кремнію, більша частина поверхневого
заряду нейтралізується в процесі низькотемпературного відпалу (450 °С) в
атмосфері водню. В кращих зразках величина Nit не перевищує 1010
см-2, що відповідає одному захопленому заряду на кожні 105
атомів межі розділу.
Поверхневі стани вважаються
донорними, якщо, віддаючи електрон, вони стають нейтральними або позитивно
зарядженими. Акцепторними називають поверхневі стани, які стають нейтральними
або негативно зарядженими, захоплюючи електрон.
Еквівалентна електрична схема
МОН-структури, що враховує вплив поверхнева станів, показана на рис.2.2.
На цьому малюнку Сi і Сd
ємності ізолятора та збідненого шару напівпровідника. Еквівалентна ємність Сs,
і еквівалентний опір Rs, залежать від поверхневого потенціалу і
описують перезарядку поверхневих станів. Добуток СsRs,
визначає час релаксації заповнення поверхневих пасток та залежність процесу
перезарядки поверхневих станів. Паралельні гілки електричної схеми на рис. 2.2
можна показати в вигляді залежної від частоти еквівалентної ємності:
Cp=Cd+Cs/(1+wt2),t
включеної паралельно з провідністю:
Cp/w= Cswt/(1+w2t2),
де t=СsRs.
Активна та реактивна складові повної
комплексної провідності еквівалентах схем, показаних на рис. 2.2 :
Yig=Gin+jw×Cin,
визначаються виразами:
Gin=w2CstCi2/[Ci+Cd+Cs)2+w2t2(Ci+w2t2(Ci+Cd)2],
Cin=Ci{Cd+Cs[(Ci+Cd+Cs)2+w2t2Cd(Ci+Cd)]/[( Ci+Cd+Cs)2+
w2t2Cd(Ci+Cd)]}/
[(Ci+Cd+Cs)…
Для визначення величини заряду,
захопленого на поверхневі пастки, можна використовувати вимірювання вхідної
ємності МДН-структури та вимірювання ЇЇ вхідної провідності. Метод провідності
дозволяє точніше визначати густину поверхневих станів. Це особливо важливо при
дослідженні МОН-структур з відносно малою (~1010 см-2еВ-1)
густиною поверхневих станів. Перевага ємнісних методів полягає в тому, що з їх
допо-
могою можна порівняно легко визначити
зсув напруги плоских зон та величину повного захопленого заряду Оit.
На рис. 2.2 проілюстроване витягування
С-V-характеристики МОН-структури за рахунок поверхневого захопленого заряду.
При високих частотах (wt>>1) заряд на поверхневих станах не встигає за
змінами тестуючої напруги. В цьому випадку вираз для значення С набуде вигляду:
С=Сi×Cd/( Сi+Cd) (Ф/см2).
Високочастотна вольт-фарадна залежність МОН-структури,
в яку не входить
ємність поверхневих станів Сs
зображена на рис.2.2 штриховою лінією. Але і в цьому випадку поверхневі стани
впливають на форму вольт-фарадної характеристики, зсовуючи ї вздовж осі напруг.
При наявності зв'язаного поверхневого заряду вимагається відповідне збільшення
заряду на металі.
По формі високочастотної
вольт-фарадної залежності густина поверхневих станів визначаеться за допомогою
виразу:
Dit=Ci[(dBs/dV)-1-1]/q-Cd/q
(см/еВ)
Фіксований заряд в окислі Qf
(звичайно додатній) розміщений на відстані ~3 нм від межі розділу Si-SiO2.
Він не може збільшуватись або зменшуватись. Густина його знаходитьcя в
діапазоні від 1010 до 1012 см-2 та залежить
від режиму окислення і умов відпалу, а також від орієнтації підкладки.
Виникнення Qf пов'язане безпосередньо з самим процесом окислення.
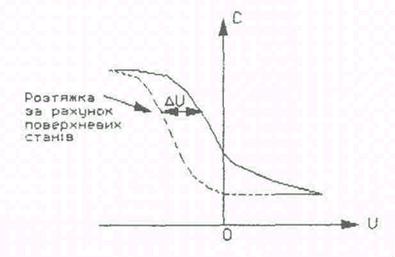
Рис. 1.2.3. Зміна С-V-кривих під
впливом заряджених поверхневих станів.
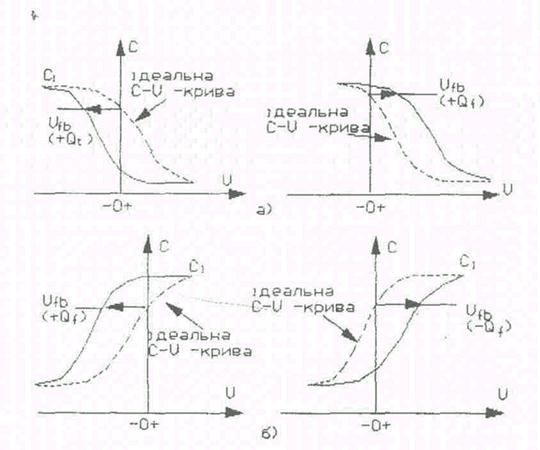
Рис. 1.2.4. Зсув С-V-кривих вздовж
осі напруг, зумовлений
додатнім або від'ємним фіксованим
зарядом оксиду:
а) для напівпровідника р-типу;
б) для напівпровідника n-типу.
Припускається, що фіксований заряд Qf
зумовлений або надлишковим (тривалентним) кремнієм, або надлишковим (не
зв'язаним із загубленим одним електроном) киснем в приповерхневому шарі SiO2
. При аналізі електричних характеристик МОН-структур фіксований заряд Qf
можна розглядати як заряджений шар, локалізований на межі розділу Si-SiO2.
На рис.1.2.4 приведені високочастотні
вольт-фарадні залежності, зсунуті вздовж осі напруг в результаті наявності
додатнього або від'ємного фіксованого заряду Qf на межі розділу.
Положення цих кривих характеризує так званий зсув напруги плоских зон,
визначеннй по відношенню до С-V -характеристики ідеальної МДН-структури з Qf
=0.
Незалежно від типу провідності
підкладки позитивний заряд Qf зсуває С-V-характеристику в бік
від'ємних напруг зміщення, а від'ємний заряд Qf - в бік додатніх.
Характер впливу фіксованого заряду
Qf на С - V -характеристики можна легко пояснити за допомогою рис.
1.2.5., де умовно показаний "поперечний переріз" МОН-структури з
позитивним Qf при негативній напрузі зміщення.
Для повної електронейтральності
структури необхідно, щоб кожний від'ємний заряд на ії металічному електроді
компенсувався рівним за величиною та протилежним за знаком зарядом в
діелектрику або в напівпровіднику. В ідеальній МДН-структурі Qf = О,
та ця компенсація здійснюється тільки за рахунок заряду іонізованих донорів в
збідненому шарі напівпровідника. В реальній МОН-структурі з позитивним Qf
частина зарядів на металічному електроді компенсується фіксованим зарядом
окисла, що приводить до відповідного зменшення глибини області збіднення в
порівнянні з ідеальною.
МДН-структурою при цій же напрузі
зміщення. Оскільки глибина області збіднення зменшується, вся С - V -крива
зсувається по відношенню до ідеальної в бік від'ємних напруг при від'ємних Qf
С -V - в протилежному напрямку. Абсолютна величина цього зсуву:
D Vf=Qf/Ci.
Заряд, захоплений в шарі окислу, Q0t,
приводить до зсуву С-V-характсристик МОН-структур. Цей заряд зумовлений
структурними дефектами в шарі окислу. Пастки в окислі, як правило, нейтральні,
але можуть заряджатися, захоплюючи електрони та дірки. На рис. 1.2.6 зображена
зонна діаграма розподілу заряду, електричного поля та потенціалу в
МОН-структурі, що містить як фісований заряд, так і заряд, захоплений в окислі.
Зсув напруги, зумовлений зарядом, захопленим в окислі, записується у вигляді:
DV0t=Q0t/Ci=1/
Ci[1/d xr0t(x)dx],
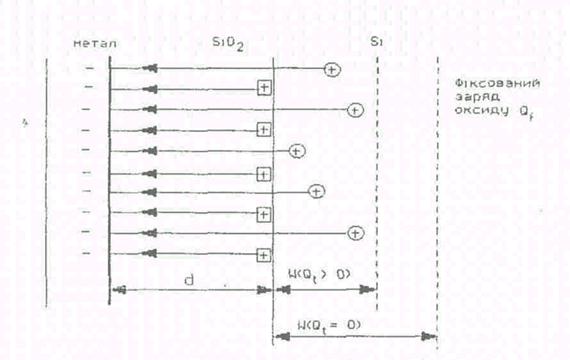
Рис. 1.2.5. Вплив фіксованого заряду
окислу на властавості МДН-структур.
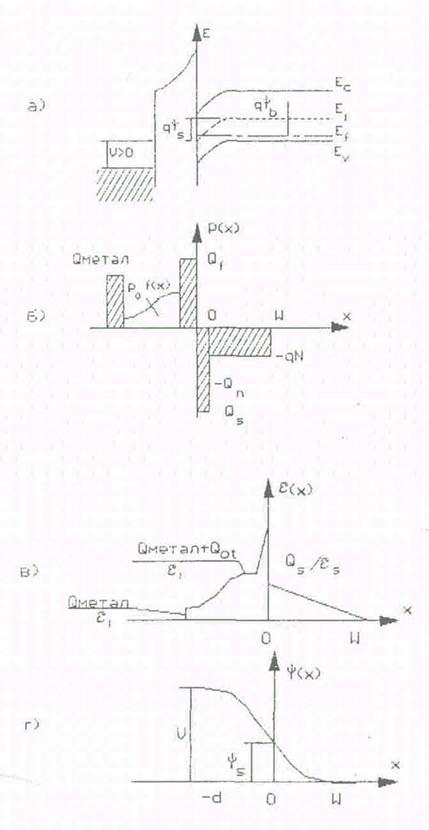
Рис. 1.2.6. МДН-структура з
фіксованимта захопленим в оксиді зарядами:
а) зонна діаграма;
б) розподіл заряду;
в) електричне поле;
г) потенціал.
Де Q0t - ефективна
поверхнева густина цього заряду, приведена до одиниці площі межі розподілу
Si-SiO2; r0t - істинна об'ємна густина заряду, захопленого в окислі.
Результуючий зсув напруги плоских зон DVfb, зумовлений
всіма компонентами зарфду в окислі:
DVfb=DVf+DVm+DV0t=Q0/Ci,
де Q0= Qf+ Qm+ Q0t
- сума відповідних ефективних зарядів на одиницю площі розподілу Si-SiO2.
В ідеальній МДН-структурі різниця
роботи виходу електрона з металу і напівпровідника дорівнює 0:
jms=jm-(x+Eg/2q-yb).
Якщо ця різниця відмінна від 0, а крім того, в
діелектрику МДН-структури присутній заряд Q0, С-V-характеристики
реальної МДН-структури будуть зсунуті вздовж осі напруг відносно ідеальної С -V
-кривої на величину:
Vfb=jms- Q0/Сi=jms-( Qf+ Qm+ Q0t)/Ci,
що називається зсувом напруги плоских зон.
Встановлено, що ширина забороненої
зони SiO2 приблизно дорівнює 9 еВ, а спорідненість до електрону qXi=0.9
еВ. Робота виходу з металу в МОН-структурах |звичайно визначається за
результатами фотовідклику або вольт-фарадних характерик.
Висота енергетичного бар'єру на межі
Si-SiO2 практично не залежить від кристалічної орієнтації підкладки
(в межах похибки 0.1еВ)
Різниця робіт виходу ms може складати
відчутну міру спостережуваного зсуву напруг плоских зон МОН-структури, і тому
її необхідно враховувати при оцінках величини фіксованого заряду окисла за
зсувом С-V -характеристик.
1.3. ГЕТЕРУВАННЯ ДЕФЕКТІВ В ТЕХНОЛОГІЇ НАПІВПРОВІДНИКОМ ВИХПРИЛАДІВ.
Однією з найважливіших задач
напівпровідникової електроніки є забезпечення високої міри чистоти та
досконалості кристалічної структури напівпровідникових матеріалів, що
використовують для виробництва дискретних приладів та інтегральних мікросхем.
Сучасна технология забезпечує
отримання практично бездислокаційних монокристалів напівпровідників. Але при
цьому різко зростає роль точкових дефектів-вакансій, домішкових атомів та їх
кластерів. При відсутності дислокацій, що є стоком для точкових дефектів, в
ході технологічного процесу виготовлення приладів відбувається постійне
збільшення концентрації вакансій та небажаних домішок натрію, калію, міді,
золота та ін., в напівпровідниковому матеріалі. Наявність точкових дефектів і
їх кластерів приводить до погіршення характеристик напівпровідникового
матеріалу, деградації параметрів приладів, сприяє утворенню структурних
дефектів при термічній обробці.
Для уникнення небажаного впливу
точкових дефектів розроблені методи, що дозволяють нагромаджувати їх в
неробочих ділянках пластин або взагалі виводити їх з пластин напівпровідника.
Процес виводу та дезактивації дефектів прийнято називати гетеруванням. Цей
термін вперше введений Готцбергом і Шоклі по аналогії з геттером в вакуумних
лампах, що використовується для зняття слідів залишкових газів при отриманні
високого вакууму. В застосуванні до напівпровідникової технології під
гетеруванням розуміють:
• очистку об'єму напівпровідника від
швидкодифундуючих домішок;
• попередження утворення центрів
зародження структурних дефектів;
• скорочення раніше утворених
структурних дефектів шляхом спрямованого руху точкових дефектів.
Для гетерування дефектів необхідно
забезпечити рухливість точкових дефектів, звідси будь-який метод гетерування
включає термообробку, температура та тривалість якої достатні для дифузії
точкових дефектів із областей пластини, де формуються прилади, в область
гетера. Існуючі методи можуть бути умовно розділені на три основні групи, в
яких гетерування здійснюється за допомогою:
• шару напівпровідникового матеріалу
з порушеною кристалічною структурою;
• нанесеного гетеруючого шару;
• термообробки в спеціальному
середовищі.
Одним з методів термообробки в
спеціальному середовищі є термічне окислення кремнію в хлормісткому середовищі,
Відомо, що додавання незначної
кількості (0.1%...6%) хлору або його сполук в окислюючу атмосферу приводить до
зменшення заряду і дефектів в окислі, зниженню густини поверхневих станів на
межі поділу кремній-діоксид кремнію, підвищенню пробивної напруги та
стабільності МОН-струкгур і т.ін.
Крім покращення властивості окислу
при “хлорному" окисленні відбувається значне покращення властивостей
кремнію, на декілька порядків зростає час життя неосновних носіїв, зменшується
кількість дефектів пакування, покращуються параметри напівровідникових
приладів.
Вивчення механізму гетерування при
"хлорному" окисленні засвідчило, що покращення параметрів кремнію та
виготовлених з нього приладів пов'язане з нейтралізацією небажаного впливу
домішок лужних, перехідних та важких металів, які, взаємодіючи з хлором, або
вилучаються з поверхні кремнію у вигляді летючих сполук, або перетворюються в
нейтральні комплекси, що вже не впливають на характеристики приладів. Домішки
золота та металів платинової групи важко гетеруються хлормісткою атмосферою,
що, напевно, пов'язано з термодинамічною нестабільністю хлоридів при високих
температурах.
Застосування хлору та хлористого
водню при термічному окисленні ускладнюється через високу реакційну здатність
цих реагентів. Тому досліджувалась можливість їх заміни іншими, менш хімічно
активними газами, наприклад трихлоретаном, чотирихлористим вуглецем,
трихлоретиленом, що за своєю дією на окисел подібні до хлору або хлористого
вуглецю. Найефективнішими та безпечними в експлуатації є трихлоретан та
трихлоретилен. На рис.1.3.1. показана схема установки для окислення пластин з
використанням трихлоретилену. При високій температурі трихлоретилен
розпадається з утворенням цілого ряду продуктів:
4С2HCl3+9O2× 2Н2О+6Сl2+8CO2
2H2O+2Cl2×4HCl+O2
Наявність води в продуктах піролізу
трихлоретилену приводить до збільшенняшвидкості росту окислу, а присутність
хлору і хлористого водню забезпечує гетерування домішок металів.
Експериментально встановлено, що
окислення з добавками трихлоретилену покращує параметри МОН-структури, знижує
струми втрат діодів, зменшує густину та розмір окислювальних дефектів
пакування, причому збільшення концентрації трихлоретилену приводить до
зменшення розмірів дефектів пакування, особливо помітному при високій
температурі окислення
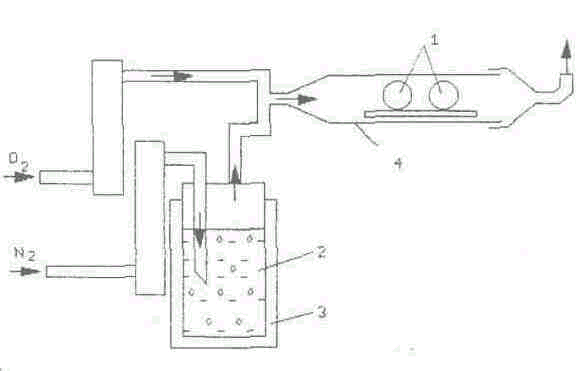
Рис. 1.3.1. Схема установки
термічного окислення кремнієвих пластин:
1 -пластини; 2-барботер; 3 -
термостат; 4 - реакційна камера.
(рис. 1.3.2). При певному
співвідношенні температури окислення та концентрації трихлорстилену можна
повністю уникнути появи утворення окислювальних дефектів пакування (рис.
1.3.3.).
Додавання невеликої кількості
трихлоретилену дозволяє погасити утворення окислювальних дефектів пакування не
лише в процесі "хлорного" окислення, а й при наступному звичайному
окисленні в сухому кисні після зняття "хлорного" окислу. Це
безпосередньо вказує на те, що в процесі обробки в хлормісткому середовищі
відбувається гетерування центрів зародження дефектів пакування.
Одним із методів гетерування дефектів
в плівках SiO2 на поверхні кремнієвої пластини є введення в ядра
дислокацій домішкових атомів, що гальмують рух дислокацій під дією
термомеханічних навантажень в процесі росту оксидної плівки. В цьому випадку
незавершені зв'язки дислокацій та підкладки заповнюються валентними електронами
домішкових атомів, в результаті чого зменшується рухливість дислокацій та гальмується
один із механізмів утворення пор в плівках SiO2.
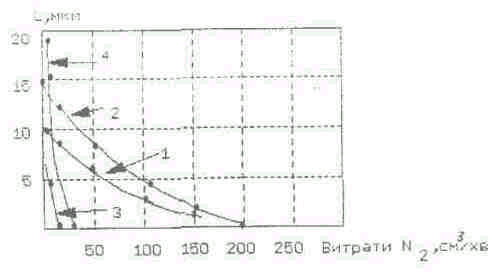
Рис. 1.3.2. Залежність розмірів
окислюваних дефектів упаковки від витрат азоту, який пропускають через барботер
з трихлоретиленом:
1 - температура окислення 1373 К,
тривалість окислення 1 год.;
2 - температура окислення 1373 К,
тривалість окислення 2 год.;
3 - температура окислення 1473 К,
тривалість окислення 15 хв.;
4 - температура окислення 1473 К»
тривалість окислення 1 год.
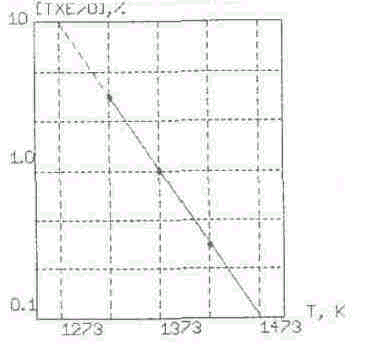
Рис. 1.3.3, Залежність температури окислення, при якій
відсутні окислювані дефекти упаковки, від співвідношення концентрацій
трихлоретилену та кисню в окислюваній атмосфері.
Висновки та постановка
завдань досліджень.
Сучасний рівень щільності пакування
елементів ІС вимагає високої суцільності плівок у взаємозв'язку з необхідними
електрофізичними параметрами елементів та їх стабільнісію. Це вимагає розробки
нових і вдосконалення відомих технологічних процесів виготовлення ІС, які
дозволили б забезпечити; необхідний рівень Їх якості. Зокрема, як видно з
літературного огляду, один з напрямків вказаних робіт - це розробка і
всестороннє дослідження методів гетерування дефектів матеріалів електронної
техніки, які є складовими частинами ВІС.
Методи домішкового гетерування на
сьогодні є на стадії досліджень і апробацій, хоча перші відомі з літератури
результати вказують на їх перспективу при використанні в області технології
мікроелектроніки. Однак, впровадження їх у виробництво неможливе без
оптимізаціі параметрів технологічного процесу за багатьма факторами, до складу
яких входять: суцільність плівок, параметри ОПЗ, межі розділу
діелсктрик-напівпровідник, зарядових характеристик діелектрика і вивчення
впливу на них зовнішніх умов які можуть проявлятися при роботі приладів. До них
відносяться термопольові і радіаційні навантаження структур.
Метою даної роботи е оптимізація
процесу домішкового гетерування дефектів плівок термічного діоксиду кремнію та
встановлення області концентрації домішки, яка забезпечила б його
найефективніше використання.
Для досліджень найкраще вибрати
традиційні методи руйнуючого та неруйнуючого контролю параметрів МДН-структур,
які пройшли широку апробацію не тільки в наукових установах, але й на
підприємствах електронної техніки. Це, зокрема, відомі методи дослідження
суцільності плівок і дислокаційної структури підкладки, вольт-фарадний та
ємнісно-часовий методи дослідження електрофізичних характеристик, як
діелектрика, так і межі розділу. Безумовно, достовірність результатів
досліджень підтвердили б дослідження параметрів структур після
радіаційно-термічної обробки, які дозволили б суттєво скоротити час оптимізащї
технологічного процесу.
Завданням даного дипломного проекту є вивчення вище
згаданими методами впливу легування діелектрика і межі розділу на
характеристики МОН-структур для з’ясування можливостей їх покращення.
Завдання
досліджень дипломного проекту :
1. Вивчити та засвоїти технологію одержання
МОН-структур з легуванням в процесі росту;
2.
Опанувати
методи вимірювання вольт-фарадних і фарадно-часових характеритик та розрахунку
за ними основних параметрів МОН-структур;
3.
Вивчити
вплив легування на характеристики структур;
4.
Зробити
висновки за отриманими результатами і оцінити можливість практичного
використання структур з легованим діелектриком.
2. Методика експерименту
2.1. Методика вирощування плівок
термічного SiO2 з одночасним легуванням в процесі росту.
Плівки диоксиду кремнію вирощували в стандартній
проточній системі схема якої приведена на рис.2.
У цій установці передбачено окислення кремнієвих
пластин, як за стандартною технологією в атмосфері сухого кисню та водяної
пари, так і окислення в середовищах, що містять домішки хлору та хлоридів, що,
в свою чергу, дозволяє легувати плівки диоксиду кремнію в процесі росту. Для
легування плівок під час процесу “вологого” окислення попередньо готувався
розчин хлориду цинку в деіонізованій воді і заливався у барботер. Барботування
проводили киснем з витратою 200 л/хв, за рахунок чого в парогазове окислювальне
середовище потрапляв як окислювач, так і домішка. Однак, як показали
дослідження, в процесі барботування концентрація вихідного розчину змінюється
за рахунок різної швидкості випаровування розчинника та складових (іонів)
розчиненої солі [10].
Навіть приготування вихідного розчину
ZnCl2 в деіонізованій воді має свої особливості. Незважаючи на
високу гігроскопічність солі, в процесі гідролізу хлориду цинку спостерігається
помутніння розчину, виділення нерозчинного осаду, який знаходиться у зваженому
стані. Після фільтрування розчину ми провели цикл досліджень його складу
використовуючи для визначення концентрації іонів цинку комплексометричний метод
[11], а для визначення концентрації
іонів хлору аргентометричний метод [12]. З’ясовано, що для повного розчинення солі і отримання гомогенного
прозорого розчину необхідно, щоб молярне співвідношення іонів хлору до іонів
цинку складало 1,012. Вказане співвідношення зберігалося для діапазону
концентрацій ZnCl2 до 5% маси.
Тому доцільніше використовувати метод миттєвого
випаровування, що полягає в подачі в реактор попередньо підготованого розчину
та випаровування його в буферному циліндрі. Температуру буферного циліндра
вибирали значно вищою від температури кипіння як води, так і хлориду цинку, а
теплоємність його суттєво перевищувала теплоємність розчину, що подається через
капіляр. Тому випаровування проходить миттєво і його склад відповідає складу
газової фази у реакторі.
При отриманні легованих плівок диоксиду
кремнію в середовищі сухого кисню, у буферний циліндр поміщали наважку
попередньо розрахованої маси оксиду цинку. В реактор подавалась суміш кисню та
хлориду водню. Хлорид водню взаємодіяв з оксидом цинку за реакцією:
2HCl+ZnO=ZnCl2+H2O
Температура зони, в яку поміщалась наважка, обиралась
вищою від температури кипіння хлориду цинку, тому продукти реакції були газами
при температурах технологічного процесу. Таким чином, процес окислення
відбувався з одночасним легуванням плівки диоксиду кремнію введеною в реактор
домішкою.
Температуру процесу окислення обирали та підтримували
за допомогою блоку регулювання та підтримування температур, яке здійснювалося
пропорційним інтегрально-диференціальним регулятором. Процес
завантаження-вивантаження пластин в реактор тривав не менше 5 хвилин для
уникнення термоударів пластин та генерації при цьому дислокацій за рахунок
термомеханічних навантажень.
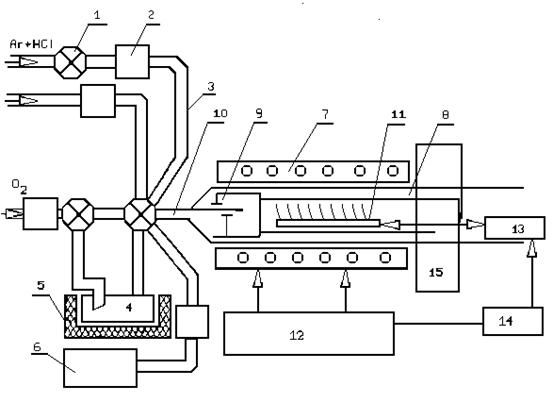
Рис.2. Система СДО-125/3
1-крани;
9-буферний циліндр;
2-витратоміри;
10-вхідний патрубок з капіляром;
3-трубопроводи; 11-човник
з Si-пластинами;
4-барботер; 12-блок живлення
та регулювання
5-термостат; температури;
6-парогенератор; 13-пристрій
вводу-виводу пластин;
7-нагрівач; 14-пристрій
керування;
8-реактор;
15-завантажувальна камера.
2.2. Визначення параметрів технологічного процесу.
Для проведення досліджень параметрів структур Si-SiO2
необхідно отримати плівки заданої товщини, яка співрозмірна з товщиною діелектрика
напівпровідникових приладів. Оптимізацію ефективності процесу гетерування
необхідно проводити шляхом вивчення впливу концентрації легуючої домішки на
параметри структур.
Для зменшення об’єму емпіричних досліджень вирощування
плівок проведено розрахунок температурно-часових характеристик технологічного
процесу отримання плівок SiO2 заданої товщини при різному складі
парогазового середовища в реакторі. В якості вихідних використали відомі з
літератури [10] залежності швидкості росту оксидних плівок на монокристалічному
кремнії в атмосфері або зволоженого кисню, або парах води з вмістом хлориду
водню, які найближчі до досліджуваного в даній роботі процесу гетерування
дефектів плівок SiO2. Це визначається тим, що в ньому в склад
окислювального середовища вводять хлорид цинку, тобто, він є, в якійсь мірі,
аналогом відомого з літератури процесу хлорного окислення. Тому тут використані
такі стандартні рівняння:
1.
d2=4.16*103p1.6t
exp(-1.7/kT) – в парах води (16);
2.
d=1.4*103p0.8t
exp(-1.7/kT) – в сухому кисні (17),
де d – товщина плівки [нм];
t – час [с];
T – температура [К];
k – постійна Больцмана.
При розрахунках товщину плівки підзатворного
діелектрика задавали в межах від 50 до 150 нм. З умов проведення експерименту
загальний тиск в системі приймали рівним атмосферному. Температуру процесу
окислення задавали в межах від 950 до 1100°С з кроком 50°С. Для
розрахунків використовували програмний пакет “Maple 6”.
Результати розрахунків приведені в табл. 1
2.3
Методика досліджень
дефектності діелектричних плівок.
Методи дослідження дефектності плівок розробляли
виходячи з особливостей структури, кількості, розмірів та розміщення дефектів
у матеріалі. При чому, в залежності від характеристик об’єкту досліджень,
методи досліджень суттєво відрізняються між собою [10].
В діелектричних плівках виробів електронної техніки
пори проявляються як поодинокі небажані дефекти. Пори в плівках мають, як
правило, субмікронні розміри і безпосередньо не виявляються оптичними
приладами.
Методи дослідження дефектності, зокрема пористості
діелектричних плівок виробів електронної техніки описані в [10]. Проведемо їх
аналіз. За дією на об’єкт досліджень їх можна поділити на дві групи: руйнуючі і
неруйнуючі. Суцільною рисою всіх методів є фіксація місця розміщення пори на
поверхні і наступні металографічні дослідження.
Неруйнуючі методи:
а) одним з методів виявлення дефектних місць у
діелектричній плівці на монокристалічній напівпровідниковій підкладці є
“бульбашковий” метод: підкладку занурюють в електролітичний розчин і освітлюють
її поверхню. До підкладки прикладають від’ємну напругу зміщення так, що в
провідних місцях (електрично активних) утворюються бульбашки газоподібного
водню. Електроліт не повинен окислювати поверхню напівпровідникової підкладки.
Як електроліти використовують 1-2% розчини лимонної або оцтової кислоти в
деіонізованій воді. Роль анода у електролітичній комірці виконує платиновий
дріт. Контроль якості діелектричних плівок з допомогою методів, основаних на
виділенні газоподібних продуктів електролізу з дефектних місць, проводиться
також при електролізі розчинів метилового і етилового спиртів, які містять 1%
оцтової або сірчаної кислоти у деіонізованої води [15,16].
Виділення бульбашок водню з дефектних місць при
електролізі спиртових розчинів починається при напрузі 8-10 В. плавне
підвищення прикладеної напруги приводить до виявлення менших за розмірами пор і
збільшення їх густини, але при напрузі більшій 30 В відбувається інтенсивне
віялоподібне виділення водню у електроліті, що робить неможливим реєстрацію і
визначення істинної густини дефектів.
Електроліз супроводжується виділенням водню на
пластині–катоді у місцях дефектів і кисню на аноді. В реальному випадку за
рахунок впливу поляризації електроліту і типу електродів для розкладення
деіонізованої води необхідно прикладати напругу 2,1-2,6 В. Розроблена комірка,
яку застосовували для вивчення електрохімічних процесів виділення бульбашок, в
якій їх реєстрували на поверхні діелектричної плівки в дефектних місцях після
2-3 хв. електролізу при напрузі 4-6 В. Продовження електролізу веде до
збільшення бульбашок за розміром і у випадку їх утворення над дефектами великих
розмірів – до віддалення від поверхні, тому підрахунок густини бульбашок
проводиться після вимикання або зниження напруги. Роздільна здатність цього
методу складає 40-60 мкм.
б) зручнішим для аналізу дефектності діелектричних
плівок є метод, який полягає у використанні спеціального електроліту, до складу
якого входять: сірчанокисла мідь – 5 г/л; желатин – 5 г/л; деіонізована вода –
1л [13,14].
Суть методу полягає в наступному. При подачі напруги з
області пори на пластині-катоді відбувається електрофоретичне виділення водню в
результаті електролізу. Процес проводять при напрузі 10-50 В. Бульбашки водню
покриті плівкою желатину, армованою міддю, що забезпечує високу міцність плівки
і добре зчеплення з поверхнею діелектрика. Висока чутливість (біля 0.1 мкм)
методу забезпечується тим, що електроліз води йде не на кремнії, а на міді, яка
осідає у порі і виходить на поверхню плівки. Вказаний метод ми використовували
для дослідження наших об’єктів.
Рис 2.3.1. Схема установки.
Руйнуючі методи:
а) Анодне травлення використовується для виявлення
дефектів в підкладці з полікристалічного кремнію [15] і має переваги хімічного
травлення і методу наведення струму. Електролітична комірка складається з
пластмасової склянки з електролітом, в який занурюють катод з платинового дроту
і зразок – анод, закріплений на металевому стержні. Електролітом служить розчин
плавикової кислоти концентрації 1-10%. Напруга живлення від джерела постійного
струму регулюється в межах від 0.5 до 20 В. Оптимальне розтравлення дефектів
спостерігали в області потенціалів між 0.7 і 2 В. Встановлено, що характер травлення
дефектів в кремнії р-типу залежить від прикладеної напруги; при дуже низькій
напрузі травляться дефекти, які класифікують за методом наведеного струму як
“електрично активні”, при збільшенні напруги травлення стає подібним до
хімічного, але зростає чутливість до дефектів (видно дефекти, які не завжди
проявляються при хімічному травленні); анодне травлення – метод виявлення
дефектів в будь-яких напівпровідниках р- і n-типу провідності, здатний повністю
замінити методи хімічне травлення і наведеного струму.
б)Хімічне травлення в травниках, що містять плавикову
кислоту (НNO3:HF: CH3COOH) приводить як до зменшення товщини
нарощеної плівки, так і до розтравлення її в місці пори до розмірів, достатніх
для спостереження під мікроскопом.
Характерно, що при обробці поверхні у вказаному
травнику розтравлюється також поверхня кремнієвої пластини під порою, що
дозволяє встановити точне положення пор на пластині.
Апробація вказаного методу для наших об’єктів
досліджень показала, оптимальний час травлення у вказаному травнику при
кімнатній температурі складає 5-7 хвилин. При цьому пори можна спостерігати під
мікроскопом при збільшенні х100 (рис. 2.3.2.)
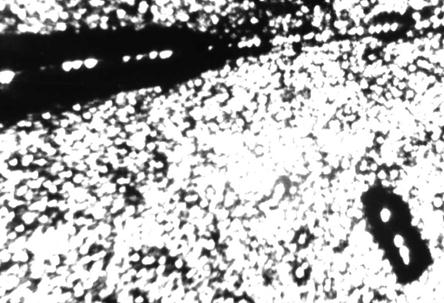
Рис. 2.3.2 Вид поверхні кремнієвої пластини після
селективного травлення. (Ділянки темного фону розміщені строго під порами у
плівці.)
2.4. Методика вимірювання вольт-фарадних характеристик
систем Si-SiO2
МДН-структура є сформованим конденсатором. Для
дослідження їх електрофізичних характеристик широко використовується метод
вольт-фарадних характеристик (ВФХ), в основі якого лежить вивчення залежності
поперечної диференціальної ємності МДН-структури (Сс) від зовнішньої
напруги, прикладеної між підкладкою і верхнім електродом (U). Зміна Сс
викликана модуляцією зовнішньої напруги ємності приповерхневої області
просторового заряду напівпровідника [16].
Еквівалентом вимірювання низькочастотної ВФХ є так
званий квазістатичний метод. Якщо до елементарного кола, що складається з
резистора і конденсатора, прикладати напругу, лінійно зростаючу з часом Uc=at
(де а звичайно складає 0.05 – 0.2 В/с), то струм в цьому колі буде
пропорційний ємності. Схема установки для знімання квазістатичних ВФХ
приведена на рис.2.4.1. [17]
Знімати ВФХ краще в напрямку від інверсії до
збагачення. Для вибору початкової робочої точки генератор пилоподібної напруги
з’єднують послідовно з джерелом постійної регулюючої напруги. Тоді Uc=В+аt.
Вибір полярності напруг залежить від типу провідності підкладки і знаку
поверхневого заряду.
Високочастотною (ВЧ) вважається така область частот,
при якій можна знехтувати вкладом у ємність МДН-структури, ємності інверсного
шару (С1) і ємності поверхневих станів (Сss). Умови
високочастотності записуються:
Rpb>>1/wCd, Rhs>>1/wCd.
Апаратура для вимірювання високочастотних ВФХ
розрізняється за методом вимірювання ємності, методом вимірювання зміщення на
МДН – структурі (Uc), методиці фіксації і методом обробки
результатів.
11
Рис. 2.4.1. Схема установки для вимірювання
квазістатичних ВФХ.
1 – джерело пилоподібної напруги; 2 – електрометричний
підсилювач.
Рис. 2.4.2. Схема установки для вимірювання
високочастотних ВФХ:
1 – джерело зміщення МДН-структури; 2 – ВЧ-генератор;
3 –резонансний підсилювач; 4 – двокоординатний самописець.
На рис.2.4.2. показана схема установки для
вимірювання високочастотних ВФХ.
Від генератора змінної напруги через розділюючий
конденсатор С1 сигнал поступає на ланку, що складається із Сс,
який має МДН-структури, і еталонного резистора R1 (C1>>Cсвч).
Спад ВЧ напруги на резисторі R1 (R1<<1/wCcвч)
пропорційний Свч.[18]
Підсилена і випрямлена напруга, пропорційна Свч
реєструється по координаті “Y” двокоординатного самописця. Зміщення Uc,
яке повільно змінюється, через роздільний резистор (R2>>1/wCcвч)
подається на МДН-структуру і координату “Х” самописця. В результаті
двокоординатний самописець фіксує ВФХ досліджуваної структури.
Високочастотна напруга на МДН-структурі Свч
повинна забезпечувати малосигнальний режим і відповідно задовольняти
співвідношенню Uc<<kT/q у всьому діапазоні Uc. При
записі ВФХ МДН-структура повинна перебувати в темноті для уникнення фотоефекту.
При зніманні ВФХ доцільно застосовувати таку
послідовність операцій: до МДН-структури прикладається напруга зміщення, яка
відповідає глибокій інверсії; освітлюється МДН-структура для збільшення
генерації неосновних носіїв і утворення рівноважного шару (часто буває
достатньо використання звичайного лабораторного освітлення); потім
МДН-структура повністю затемнюється, і напруга зміщення починає змінюватись від
інверсії до збагачення, при цьому на самописці фіксується рівноважна
високочастотна ВФХ.
Іншим варіантом ФВХ є диференціальний високочастотний
вольт-фарадний метод. При аналізі високочастотного вольт-фарадного методу
зазначалося, що для визначення густини поверхневих станів необхідно порівнювати
нахили експериментальної і теоретичної високочастотних ВФХ. Це означає графічне
диференціювання експериментальної кривої. Зручніше проводити диференціювання
експериментальної ВФХ апаратурним методом. Для цього в установку зйомки ВФХ
додатково вводять диференціюючу ланку [11]. При використанні зміщення Uc=at,
яке лінійно змінюється, диференціююча ланка на виході забезпечує сигнал,
пропорційний dC/dU, який записується на самописці одночасно з записом ВФХ.
Розшифровка залежностей С(V) відбувається аналогічно до розшифровки
високочастотних ВФХ. Перевага цього методу полягає в більшій швидкодії і
підвищенні точності в порівнянні з вольт-фарадним методом. [17]
Блок-схема установки для дослідження МДН-структур
приведена на рис. 5.3. при вимірюванні С(V) і G(V) залежностей (П1 – в
положенні “1”, П2 – в положенні “2”) на структуру подаються два сигнали: малий
синусоїдальний від генератора (2) і напругу зміщення з генератора пилоподібної
напруги (КГТН) (4). Сигнал з виходу інтегруючого (ІП)( 8) або диференціюючого
(ДП) (9) підсилювача подається на вхід широкополосного (10) або вибіркового
(11) підсилювача і далі на фазовий (ФД) (12) або амплітудний (АД) (13)
детектор. На вхід “2” ФД подається опорний сигнал з генератора (2).
Встановлення фази сигналу на вході “1” ФД створюється незначним розладнанням
підсилювача (11). Напруга з виходу ФД (VG) і АД (VC) подається на входи “Y”
двокоординатних самописців (6) і (7). На входи “Х” самописців поступає напруга
з виходу КГТН.
При вимірюванні С(t) залежностей (П1, П2 і П3 в
положенні “2”) на структуру подається стрибок напруги або послідовність
імпульсів з формувача (3). Вихідний сигнал КГТН при дослідженні повільних
процесів використовується для часової розгортки самописців. Для реєстрації
процесів з часами релаксації 0.3 с використовується осцилограф (14).
Градуювання С(V), G(V), i C(t) – залежностей проводиться
магазином ємностей і провідностей (П2 в положенні “1”). Установка дозволяє
проводити експрес вимірювання параметрів, та досліджувати їх неоднорідності.
Рис.2.4.3. Блок-схема установкт для вимірювання C(V), G(V) та С(t)-характеристик:
1 – магазин ємностей та провідностей;
9 – диференціюючий підсилювач;
3
–
генератор;
4
10 –
широкосмуговий підсилювач;
3 – формувач;
11 – вибірковий підсилювач;
5
–
керуючий генератор трикутної напруги;
6
12 –
фазовий детектор;
5 – МОН-структура;
13 – амплітудний детектор;
7
–
двокоординатний самописець;
8
14 –
осцилограф;
7 – двокоординатний самописець
15 – вимірювач температури.
8 – інтегральний підсилювач;
3. Результати досліджень.
3.1. Дослідження пористості плівок
термічного диоксиду кремнію.
Дефектами плівок диоксиду кремнію
вважають порушення однорідності аморфного шару [23]. До їх числа відносяться
включення іншої фази: пори і кристалічні ділянки. Густина структурних дефектів
визначає вихід виробів електронної техніки, особливо ВІС високого ступеня
інтеграції, тому розробка способів виявлення дефектів і вивчення механізмів
дефектоутворення привертала увагу ряду дослідників. Для їх дослідження
розроблено ряд методів, описаних в огляді, та роботах [19,20].
Літературні дані про природу
пороутворення часто носять дискусійний характер. Переважно їх появу пов’язують
з неконтрольованим забрудненням поверхні кремнієвої пластини до і в процесі
росту плівки оксиду. Це викликало необхідність проведення циклу
експериментальних досліджень пористості плівок для встановлення механізмів їх
утворення.
Плівки SiO2 товщиною від
0.1 до 0.6 мкм вирощували в стандартних процесах термічного окислення
кремнієвих пластин в середовищі сухого і вологого кисню. Дефектність плівок
визначали шляхом металографічних досліджень під мікроскопом NU-2E після
візуалізації пор бульбашками желатину при електролізі водного розчину CuSO4
і желатину (250 : 5 : 5) і шляхом селективного травлення поверхні плівок в
травнику складу HF : HNO3 : CH3COOH (1 : 10 : 1) протягом
3...7 хвилин. Селективне тралення плівки оксиду проводили аж до підтравлювання
підкладки, після чого знімали плівку в розчині HF і виявляли дислокації
поверхні кремнієвих пластин в травнику Сіртля.
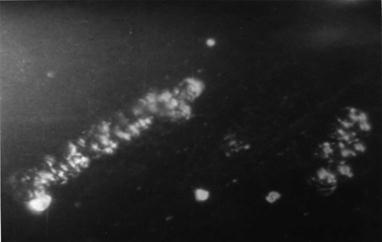
Рис.
3.2.1. Неоднорідності візуалізації пор, обумовлені їх різними розмірами
(металографія, x 200)
При дослідженні пористості плівок
мідножелатиновим методом, як видно з рис.3.2.1., в місцях провідних ділянок
плівок виростали або желатинові грона, або бульбашки желатину значно меншого
розміру. Це обумовлено суттєвою різницею швидкості процесу електролізу в різних
провідних ділянках плівки викликану різними розмірами пор, що вказує на
наявність щонайменше двох механізмів процесу пороутворення. Як правило,
желатинові грона хаотично розміщалися по поверхні пластини і спостерігалися по
подряпинах плівки. Встановлено взаємозв’язок густини “великих” пор від
запиленості технологічного приміщення в якому перебували пластини після
передокислювальної хімічної обробки. При запиленості в межах 4...30 л-1 їх
густина в плівках SiO2 товщиною 0,1 мкм складала 0,5...2 см-2
і зменшувалась з ростом товщини плівки. В той же час, порушення норм запиленості,
або спеціальна, навіть короткочасна, витримка пластин в середовищі з
запиленістю до 300 л-1 приводила до різкого росту дефектності
плівок до 102...103 см-2. В той же час, при
ретельному контролі та дотриманні чистоти технологічного приміщення “великі”
пори практично не проявлялися.
При дослідженні плівок SiO2, препарованих
за методикою [24], шляхом просвічуючої електронної мікроскопії на МВ-100
встановлено, що розміри “великих” пор співрозмірні з товщиною плівки [24].
Виходячи з приведених результатів,
механізм утворення наскрізної пори можна подати таким чином: при згоранні або
випаровуванні речовини пилинки чи інших неконтрольованих забруднень кремнієвої
підкладки при температурі окислення тиск пари в хмаринці домішок може досягнути
критичної величини, достатньої для локального руйнування плівки оксиду.
Аналогічний механізм пороутворення може проявлятися при випаровування
преципітатів як легуючих, так і неконтрольованих домішок, сконцентрованих на
структурних порушеннях кремнієвої підкладки.
Що стосується “дрібних” пор, то їх густина, усереднена
на пластину, складала 1,5...3, 3,4...5,5 і 6,5...15 cм-2 для плівок
термічного диоксиду кремнію товщиною 1, 0,5 і 0,15 мкм відповідно. Виявлена
тенденція зменшення густини пор від краю до центру пластини. Причому, біля 80%
пор розміщалися по її периметру в області до 7...12 мм від краю. Характерно, що
густина пор в цій області майже на порядок вища, ніж в центрі. Скупчення пор
(рис.3.2.2) проявлялися також в місцях контакту пластини з кварцовим човником і
в значній мірі визначалися щільністю входження пластини в його пази.
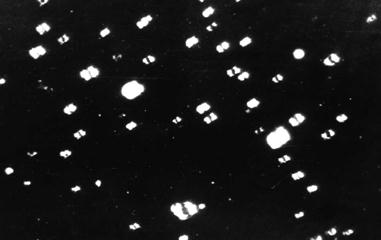
Рис.3.2.2.
Вид поверхні пластини після візуалізації пор (x200, металографія)
Як правило, по декілька пор розміщалися в ряд, причому
лінії їх утворення відповідали кристалографічним лініям ковзання дислокацій.
Різко неоднорідний розподіл пор в плівках SiO2, який відображає
дефектоутворення в кремнієвих підкладках і свідчить про тісний взаємозв’язок
умов росту плівки з дефектоутворенням в кремнію, яке проявляється в конкретному
циклі дифузійно-окислювальних процесів спостерігали також в [9].
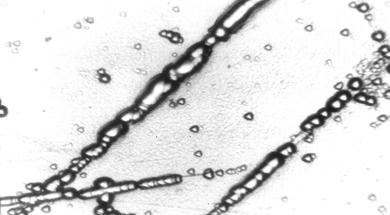
Рис. 3.2.3. Розміщення пор в плівках вздовж ліній
ковзання
Ідентичність якісного радіального
розподілу дефектів в плівках SiO2 і кремнієвих підкладках
підтверджена послідовними дослідженнями розподілу пор та дислокацій вздовж
фіксованих смуг шириною 5 мм вздовж діаметра пластини. Однак, в кількісному
відношенні, густина пор в плівках значно нижча від густини дислокацій, які
виходять на поверхню підкладки. Це вказує на те, що далеко не кожна дислокація
є ініціатором пороутворення в вирощуваній плівці термічного SiO2.
3.2. Взаємозв’язок структурної
досконалості монокристалічної кремнієвої підкладки і плівок SiO2.
Розглянемо можливі причини
неоднорідного розподілу дефектів. Розрахунок характеру нагріву однієї пластини
[19] і партії пластин [20] показав, що як при прогріві, так і при охолодженні
росте нерівномірність розподілу температур вздовж радіуса пластини. В
результаті розв’язання крайової задачі теплопровідності і аналізу кінетики
нагріву та теплообміну в партії пластин в [20] показано, що максимальний
перепад температури складає 46К при швидкості завантаження 0,002 м/c і 340К при
0,01 м/c. При цьому радіальні і тангенціальні термічні напруження пластини
ростуть пропорційно різниці температур:
(19)
(20)
де: a - коефіцієнт термічного
розширення; E - модуль Юнга; DT - різниця температур; r - координата; R - радіус
пластини.
Під їх дією утворюються дислокації і
проходить знімання термічного напруження в межах даної ділянки. При повторній
циклічній обробці знов виникають термічні напруження, причому умови утворення
дислокацій значно полегшуються (проходить розмноження дислокацій і починає
діяти механізм їх передачі). Оскільки градієнт температури максимальний на краю
пластини, дислокації виникають практично завжди на периферії в вигляді ліній
зсувів і, в подальшому, переміщаються до центру вздовж площин ковзання [21].
Внаслідок того, що плівка SiO2 жорстко зв’язана з підкладкою, в
місцях переміщення сусідніх атомних площин в напрямку ковзання дислокацій
виникатимуть максимальні напруження плівки, релаксація яких буде проходити
шляхом локального руйнування плівки і утворення пор. Таким чином, на нашу
думку, пори повинні наслідувати не дислокації як такі, а утворюватися при їх
русі вздовж площин ковзання [21].
Вказане припущення підтверджене
експериментально при металографічному дослідженні протравленої в дислокаційному
травнику підкладки після візуалізації пор методом [19]. На рис. 3.1.1. ділянки
темного фону відповідають розтравленій поверхні кремнієвої пластини під порою.
Ямки травлення виходів дислокацій на цих ділянках проявляються вздовж ліній їх
утворення. Наслідування порами плівки смуги ковзання дислокацій підтверджує
також рис. 2.3.2. Як видно з рисунків, в кількісному відношенні густина
розтравлених ямок травлення значно менша їх сумарної густини.
Використовуючи в якості відліку
орієнтацію пластин кремнію і базового зрізу встановлено напрями ліній
пороутворення в плівках диоксиду кремнію. Вони відповідають кристалографічним
напрямам <110> в підкладці, які, згідно [22], є найвірогіднішими
напрямками ковзання в гратці типу алмаз.
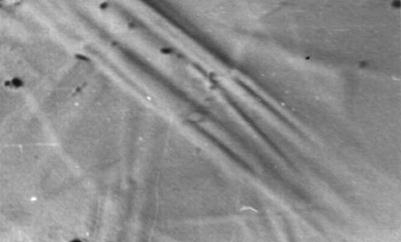
Рис. 3.1.1. Закристалізована ділянка
протравленої плівки SiO2
Як винятки, при металографічному дослідженні поверхні
частково протравлених плівок SiO2 спостерігали також
закристалізовані ділянки (Рис.3.1.1).
Пори на цих ділянках проявлялися між границями
кристалітів і аморфної матриці. Їх утворення зв’язують з механічними
напруженнями, що перевищують критичні, обумовленими різними значеннями к.т.р.
кремнієвої підкладки, кристалічного і аморфного диоксиду кремнію. Ініціатором
локальної кристалізації плівок через рідку фазу диоксид кремнію - домішка
можуть служити навіть незначні кількості домішок лужних металів, найімовірнішим
джерелом яких може бути поверхня кварцового реактора та неконтрольовані
забруднення використовуваних реагентів.
Виходячи з викладеного можна виділити такі механізми
пороутворення в плівках термічного диоксиду кремнію:
· руйнування плівки внаслідок
випаровування або згорання матеріалу локальних забруднень поверхні кремнієвих
пластин в процесі росту плівки;
· утворення пор при русі
дислокацій підкладки під дією термомеханічних напружень;
· утворення пор при локальній
кристалізації плівок, стимульованій домішками.
Характерно, що переважаюча кількість пор утворюється
внаслідок дії механізму пороутворення, пов’язаного з рухом дислокацій
кремнієвої підкладки в процесі росту плівки.
3.3. Гетеруюча
дія цинку. Оптимізація технологічного процесу за концентрацією домішки.
Для зменшення густини дефектів можна використовувати методи
гетерування (див. §1.3). Переважна більшість з них передбачає спеціальну
обробку поверхні пластин перед першою термічною операцією. До них відносяться
гетерування з допомогою порушеного шару, який створюється різними методами,
гетерування з допомогою нанесених шарів, термічна обробка в спеціальному
хімічному середовищі.
Але, на нашу думку оптимальними були
б такі методи, які можна сумістити з першою термічною операцією – термічним
окисленням пластин. Зокрема, знизити активність процесу утворення пор, пов’язаного
з рухом дислокацій підкладки вздовж ліній ковзання можна шляхом впровадження в
їх ядра домішкових атомів з газової фази в процесі росту плівки. Згідно
літературних даних [25] в якості гетеруючої домішки ми вибрали цинк, який буде
декорувати дислокації, заповнювати і зв’язувати їх незавершені зв’язки.
Дослідження гетеруючого впливу цинку,
який вводили в реактор з розчину хлориду цинку, проводили при таких
концентраціях у вихідному розчині, що заливався у барботер: 0; 0.1; 0.5; 1; 2;
3; 5% для визначення оптимального вмісту.
Отримані плівки диоксиду кремнію
товщиною 120¸140 нм досліджували мідножелатиновим методом і селективним
травленням для визначення густини пор (див. § 2.3).
Встановлено, що густина пор в
плівках SiO2 при окисленні за стандартною технологією складає від
6.5 до 15 см-2. Отримані дані узгоджуються з результатами роботи
[23].
При введенні хлориду цинку в процесі
окислення густина пор складала від 0.3 до 1.5 см-2, що на порядок
нижче, ніж при окисленні за стандартною технологією. Дослідження показали, що
навіть при незначних концентраціях (менше 1%) пористість плівок різко
понижується. Зниження пористості йде до певного рівня, який близький до 1 см-2.
Мінімальне значення пористості спостерігали на зразках, які окислювали при
концентрації хлориду цинку в діапазоні 1…3%. Суттєво, що в цьому діапазоні
концентрації пористість плівок диоксиду кремнію слабо залежить від концентрації
розчину хлористого цинку. При подальшому збільшенні концентрації пористість отриманих
плівок збільшується. Отже, збільшення концентрації водного розчину хлористого
цинку вище 3% недоцільно.
Отримані результати ілюструє рис.
3.3.1. .
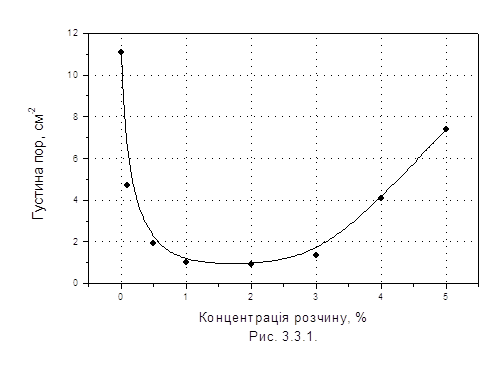
Таким чином, експериментально
підтверджена можливість пониження дефектності плівок диоксиду кремнію
гетеруванням домішкового цинку дислокацій підкладки. Ефективність
запропонованого методу, як показали експериментальні дослідження, у два-три
рази вища, ніж при гетеруванні дефектів порушеним шаром неробочої сторони
пластини Si. Це пов’язане з тим, що в нашому випадку знижується рухливість
існуючих дислокацій, а не тільки їх густина на робочій стороні пластини.
Недоліком методу барботування для
створення парогазового окислювального середовища у реакторі є зміна
концентрації розчину, пов’язана з різною швидкістю випаровування компонентів.
Для усунення цього недоліку ми
відпрацювали процес монокристалічного кремнію з домішкою хлориду цинку в
газовый фазі при миттєвому випаровуванні компонентів розчину. (див.2.1)
Результати досліджень пористості
вирощених плівок приведені на рис 3.3.2.
Рис. 3.3.2. залежність густини пор у
плівок SiO2 від концентрації водного розчину хлориду цинку при
миттєвому випаровуванні для різної товщини вирощеної плівки: трикутник -
товщина плівки 1200А; кружок - товщина плівки 5000А.
Як видно з рис. На кривій
концентраційної залежності густини дефектів у плівках також чітко проявляється
область мінімальної концентрації пор. Процес вирощування плівок найкраще
проводити у цій області, яка лежить біля 0.001%
Для подальшого використання необхідні
дослідження електрофізичних параметрів структур, результати яких приведені у
наступному параграфі.
3.4.
Електрофізичні
характеристики структур.
Як видно з результатів, описаних
вище, у легованих цинком структурах Si-SiO2 спостерігається
покращення суцільності плівок SiO2. Це пов’язане з заповненням
легуючою домішкою незавершених зв’язків дислокацій приповерхневої області
кремнієвої пластини і зниження, за рахунок цього, рухливості дислокацій.
Оскільки одним з механізмів утворення пор є деформаційне локальне руйнування
плівки, щільно з’єднаної з підкладкою, за рахунок напружень, які перевищують
критичні, під час зміщення сусідніх атомних площин при русі дислокацій. Вказане
легування при оптимальних концентраціях повинне приводити до покращення
структурної досконалості межі розділу, зменшення рухливості дислокацій і,
відповідно, пористості плівок SiO2 [19].
Можна сподіватися, що легування
приповерхневої області кремнію приводитиме і до покращення електрофізичних
характеристик межі розділу, що буде проявитися перш за все на таких параметрах,
як густина поверхневих станів та генераційно-рекомбінаційний час життя.
Розрахунок приводили за результатами
вимірювання вольт-фарадних характеристик за методикою, описаною в § 2.4
Результати дослідження параметрів ОПЗ
легованих цинком структур приведені в таблиці.
Таблиця. 3
Концентрація домішки, % |
0 |
0.0005 |
0.001 |
0.0025 |
Густина поверхневих станів, Dit,
еB/кв.см.
|
5.7´1011
|
5.7´1011
|
5.0´1011
|
5.2´1011
|
Час життя, tg, 10-6 c
|
45 |
40 |
86 |
55 |
Як видно з таблиці, введення домішки
цинку приводить до підвищення структурної досконалості приповерхневої області
кремнію, що виявляється в зменшенні з ростом рівня легування густини
поверхневих станів та підвищенні часу життя нерівноважних носіїв заряду,
причому вказане покращення спостерігається лише при повному рівні легування,
який має свій оптимальний діапазон. Високолеговані структури порівняно з
контрольними характеризувалися гіршими показниками якості. Це пояснюється тим,
що при концентрації домішки 3´10-3% і вище, атоми цинку
будуть входити не лише в ядро дислокацій, а й легувати поверхню кремнію і
цілому, тобто створювати точкові дефекти в кристалічній гратці, а при високому
рівні – і дислокації невідповідності [10]. Наявність дефектів структури
приводить до появи додаткових рекомбінаційних центрів і енергетичних станів,
пов’язаних з ними, що знижує рухливість носіїв заряду, їх час життя і підвищує
концентрацію енергетичних поверхневих станів, тобто в цілому призводить до
погіршення параметрів структур.
Симптоматично, що структури з
оптимальним рівнем легування після опромінення і наступного відпалу
характеризувалися кращими значеннями параметрів межі розділу порівняно з
контрольними, тобто мали нижчу радіаційну чутливість. Це пояснюється зниженням
рівня механічних напружень приповерхневої області за рахунок легування та
зменшення її дефектності. Як відомо [17], підвищення структурної досконалості
кристалічної гратки в області межі розділу повинно приводити до покращення
електрофізичних характеристик системи Si-SiO2.
На рис.3.4.1 приведені концентраційні
залежності часу життя неосновних носіїв заряду 1/tg = f(С). У діапазоні концентрацій,
близьких до 0.002% спостерігається чітко виражений мінімум, характерний як для
опромінених, так і для неопромінених структур. Причому величина часу життя
неосновних носіїв заряду при оптимальному рівні легування в області мінімуму
кращі, ніж у контрольних зразках, що піддавались і не піддавались
радіаційно-термічній обробці.
Зниження часу життя при рівнях
легування, що перевищують оптимальні, найвірогідніше зумовлене структурним
розпорядкуванням приповерхневої області під впливом високої концентрації
легуючої домішки, утворенням складних комплексів, що містять цинк та самочинно
не розпадаються під час відпалу.
Залежність величини, оберненої до
часу життя, від концентрації домішки, а не часу життя, приводиться тому, що 1/tg пропорційна густині
генераційно-рекомбінаційних центрів і виражає зміну рівня дефектності
приповерхневої області кремнію.
Порівняно з нелегованими структурами,
оптимальне легування приводить до швидшого відновлення густини поверхневих
станів після радіаційно-термічної обробки, що відображено на рис.3.4.1. Причому, як видно з малюнка,
термічна обробка після опромінення приводить до менших значень густини
поверхневих станів приповерхневої області кремнію, порівняльно з вихідними
структурами.
Характерно, що оптимальні значення
параметрів структур спостерігаються при тих же значеннях концентрацій домішки,
при яких плівки SiO2 характеризуються найкращою
суцільністю.
Таким чином, встановлений нами
діапазон оптимальних концентрацій гетеруючої домішки буде приводити не тільки
до зниження густини структурних дефектів плівок SiO2, але й до покращення електрофізичних
характеристик м6ежі розділу діелектрика з монокристалічною підкладкою, що
важливо для подальшого практичного використання.
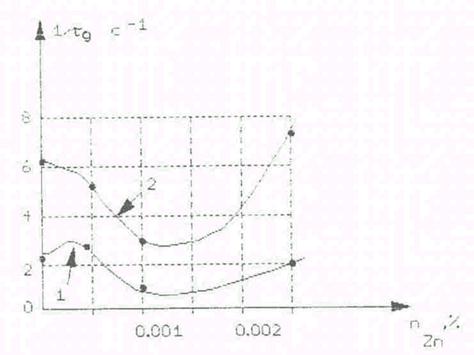
Рис. 3.4,1. Залежності впливу
опромінення та наступного вщпалу на 1/Тд: 1 - вихідні; 2 - після
опромінення.
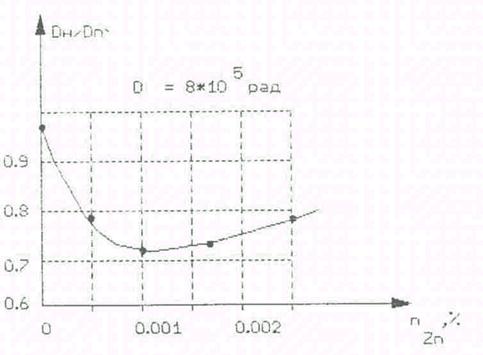
Рис. 3.4.2. Концентраційна залежність
відносної зміни густини поверхневих станів після радіаційно-термічної
обробки.
Висновки
1.
Вивчені
механізми попроутвореня і плівках термічного диоксиду кремнію;
2.
Показано,
що переважаюча кількість пор утворюється вздовж ліній ковзання внаслідок
напружень плівок, викликаних рухом дислокацій монокристалічнолї підкладки.
3.
Запропоновано
механізм гетерування дуфектів шляхом гальмквання руху дислокацій атомами цинку;
4.
Визначений
діапазон оптимальних концентрацій домішки у газовій фазі при якій плівки
характеризуються мінімальними значеннями пористості і оптимальними
електрофізичними параметрами.
5.
ЕКОНОМІЧНА ЧАСТИНА
У зв’язку
з особливостями
науково-дослідних розробок для їх ефективного
здійснення, координацій робіт, оперативного управління ходом робіт, передбачене
сіткове планування та керування.
5.1. Планування науково-дослідної
роботи (НДР).
В розрахунково
- пояснювальній записці до дипломної роботи планування
НДР здійснюється в
наступній послідовності :
1.
Розбиття
комплексу робіт на окремі етапи.
2.
Виявлення
та опис всіх подій та робіт.
3.
Визначення
часу виконання робіт.
4.
Побудова
сіткового графіка.
5.
Розрахунок
параметрів сіткового графіка.
5.1.1 Розбиття комплексу робіт на
окремі етапи.
Весь комплекс робіт ділиться на такі
етапи :
*
підготовчий;
*
теоретична
розробка теми;
*
проведення
експерименту;
*
обробка
даних, отриманих при експериментах;
*
технічний
звіт;
Таблиця 1.Тривалість розробки етапів
проекту
№ |
Назва етапу |
Виконавець
|
Кількість виконавців |
Тривалість етапу, днів |
1
2
3
4
|
Розробка графіка робіт
Написання теоретичної
частини дипломної
роботи
Проведення досліджень і
зняття характеристик
МДН-структур
Обробка експериментальних даних
|
студент-дипломник;
керівник
студент-дипломник;
керівник
студент-дипломник;
керівник
студент-дипломник
|
2
2
2
1
|
35
15
10
20
|
5.1.2 Виявлення та опис всіх подій та
робіт.
Графічна модель всього процесу виконання НДР ( сітковий графік ) складається з подій та
робіт. Кількість робіт в сітковому графіку залежить
від ступеня його деталізації, що визначається об’ємом і складністю
розробки. Границі деталізації подій та робіт
визначаються технологією робіт і границею відповідальності
виконавців. Чим більш деталізована сіть, тим простіше її оцінити і проконтролювати по коду виконання розробки. Всі подіі та роботи, що входять в комплекс робіт, зводимо
в таблицю в порядку їх послідовності, тобто необхідно
скласти бібліотечний список. Цей список включає
перелік подій та їх індексацію, а також перелік робіт та їх коди.
Таблиця 2.
Перелік робіт та подій
№
|
Назва подіі
|
Код роботи
|
Зміст роботи
|
0 |
Завдання отримано. |
0-1.
|
Складання плану роботи. |
1 |
План роботи складено. |
1-2 |
Вивчення літератури. |
2 |
Література вивчена. |
2-3 |
Підготовка монокристалу для нанесення плівки.
|
|
|
2-4 |
Підготовка обладнання для вирощування плівки SiO2.
|
|
|
2-8 |
Підготовка обладнання для дослідження.
|
|
|
2-20 |
Аналіз. |
3 |
Пластини монокристалу підготовлені |
3-5 |
Складання установки для вирощування
плівок. |
|
|
3-6 |
Розрахунок умов вирощування |
4 |
Обладнання для вирощу- вання
підготовлене. |
4-5 |
Підготовка матеріалу для вирощування. |
5 |
Установка складена. Матеріал
підготовлений. |
5-6 |
Наладка установки для вирощування. |
6 |
Умови вирощування плівок
розраховані. |
6-7 |
Вирощування плівок діоксиду
кремнію. |
7 |
Плівки нарощені |
7-8 |
Підготовка пластин з нарощеною
плівкою. |
|
|
7-10 |
Зняття діелектричної плівки. |
8 |
Обладнання та пластини готові для
дослідження. |
8-9 |
Визначення дефектності
діелектричних плівок |
9 |
Визначено дефектність діелектричних
плівок. |
9-12 |
Знаходження напружень пластин. |
10 |
Діелектрична плівка знята |
10-11 |
Визначення дефектності пластин. |
|
|
10-12 |
Знаходження напружень пластин. |
11 |
Дефектність пластин досліджена. |
11-14 |
Фотографування дефектності пластин. |
12 |
Напруженість всіх пластин Si
визначена. |
12-13 |
Порівняння результатів двох
досліджень. |
13 |
Порівняння проведені. |
13-14 |
Знаходження залежності густини пор
від напруження. |
14 |
Дефектність сфотографована. Залеж- |
14-15 |
Опис результатів. |
|
ність густини пор від напруження
встановлена. |
|
|
15 |
Опис результатів проведений. |
15-16 |
Побудова сіткового графіка. |
16 |
Сітковий графік побудовано. |
16-17 |
Розрахунок параметрів сіткового
графіка. |
17 |
Розрахунок параметрів проведено. |
17-18 |
Визначення затрат на проведення
НДР. |
|
|
17-20 |
Аналіз отриманих результатів |
18 |
Затрати визначені. |
18-19 |
Оцінка науково-технічної
ефективності НДР. |
19 |
Ефективність оцінена. |
19-20 |
Аналіз ефективності. |
20 |
Аналіз проведено. |
20-21 |
Висновки. |
21 |
Висновки зроблено. |
21-22 |
Оформлення. |
22 |
Робота оформлена |
|
|
5.1.3. Визначення
часу виконання робіт.
Для планування тривалості виконання
робіт необхідно користуватись відповідними нормативами або узагальненими даними минулих аналогічних розробок ( з врахуванням процента їх
виконання ).
В більшості випадків при плануванні комплекса робіт творчого характеру, а також при плануванні нових досліджень, що не мають аналогів в минулому, не існує ні нормативів, ні досвіду роботи. В таких випадках
використовують три або дві ймовірні оцінки часу. Ці оцінки визначаються в днях.
tоч =
(tmin+ 4tнй +tmax ) / 6
s2 tоч = [(tmax-tmin)/6]
Приклад розрахунку для роботи 0-1:
tоч = (4+4´5+7)/6=5
s2 tоч = (7-4)/6=0.25
Всі результати розрахунків зведені в
таблицю 3.
5.1.4. Побудова сіткового графіка.
Таблиця 3. Трудоємність виконання
робіт та кількість виконавців.
Код роботи
|
Трудомісткість роботи в днях
|
Дисперсія s2 tоч, дні
|
К-сть викон.
|
tmin
|
tнй
|
tmax
|
tоч
|
0-1 |
4 |
5 |
7 |
5 |
0.25 |
2 |
1-2 |
4
|
5 |
6 |
5 |
0.11 |
1 |
2-3 1
|
1 |
1 |
2 |
1 |
0.03 |
1 |
2-4
|
2 |
3 |
4 |
3 |
0.11 |
2 |
2-8 |
1 |
1 |
2 |
1 |
0.03 |
2 |
2-20 |
5 |
7 |
8 |
7 |
0.25 |
1 |
3-5 |
3 |
4 |
5 |
4 |
0.11 |
2 |
3-6 |
6
|
7 |
7 |
7 |
0.03 |
2 |
4-5 |
1 |
2 |
2 |
2 |
0.03 |
1 |
5-6 |
1 |
1 |
2 |
1 |
0.03 |
1 |
6-7 |
1 |
1 |
2 |
1 |
0.03 |
2 |
7-8 |
1 |
1 |
2 |
1 |
0.03 |
1 |
7-10 |
1 |
1 |
2 |
1 |
0.03 |
1 |
8-9 |
1 |
2 |
4 |
1 |
0.25 |
2 |
9-12 |
1 |
1 |
2 |
1 |
0.03 |
2 |
9-14 |
1 |
1 |
3 |
1 |
0.11 |
1 |
10-11 |
1 |
1 |
2 |
1 |
0.03 |
2 |
10-12 |
1 |
2 |
2 |
2 |
0.03 |
2 |
11-14 |
1 |
1 |
2 |
1 |
0.03 |
1 |
12-13 |
1 |
1 |
2 |
1 |
0.03 |
2 |
13-14 |
1 |
1 |
3 |
1 |
0.11 |
1 |
14-15 |
2 |
3 |
5 |
3 |
0.25 |
1 |
15-16 |
1 |
1 |
2 |
1 |
0.03 |
1 |
16-17 |
1 |
1 |
2 |
1 |
0.03 |
1 |
17-18 |
1 |
1 |
3 |
1 |
0.11 |
1 |
17-20 |
2 |
4 |
4 |
4 |
0.11 |
1 |
18-19 |
1 |
1 |
2 |
1 |
0.03 |
1 |
19-20 |
1 |
1 |
2 |
1 |
0.03 |
2 |
20-21 |
2 |
3 |
3 |
3 |
0.03 |
2 |
21-22 |
4 |
6 |
7 |
6 |
0.25 |
1 |
5.1.5 Розрахунок параметрів
сіткового графіка.
До основних параметрів сіткового
графіка відносяться:
Тривалість шляху t(L) |
t(L) = tijk |
Тривалість критичного шляху Ткр |
Ткр = t[L(I-C)max ]
|
Резерв часу шляху R(L) |
R(L) = Ткр -t(L)
|
Ранній термін здійснення події Трі |
Трі = t[L(I-і)mах ]
|
Пізній термін здійснення подіі Тпі |
Тпі = Ткр - t[L(і-С)mах ]
|
Резерв часу події Rі |
Rі = Тпі - Трі |
Ранній термін початку роботи Трпіj |
Трпij =
t[L(1-і)mах ] або
Трпіj = Трі
|
Ранній термін закінчення роботи
Трзіj |
Трзіj = Tpпij+tij
|
Пізній термін початку роботи Тппіj |
Тппіj = Тпзіj -tij |
Пізній термін закінчення роботи
Тпзіj |
Тпзіj =
Тпj
|
Повний резерв часу роботи Rпіj |
Rпіj =
Тппіj - Трпіj або
Rпіj = Тпзіj - Трзіj
|
Вільний резерв часу роботи Rсіj |
Rсіj=Rпіj -Rj
|
Коефіцієнт напруженості роботи Кніj |
Кніj=[t(Lmax)-t’(Lкр)]/[Ткр - t’(Lкр)]
|
де t (Lmах)-тривалість
максимального шляху, який проходить через дану роботу ; t’(Lкр)- відрізок шляху, що співпадає
з критичним шляхом.
Приклад розрахунку: t(L)=t01 =5
Tкр =
5+5+1+7+1+1+2+1+1+1+3+1+1+4+3+6=43
R = 43-5=38 Tрз01 =5 Rc01
=0
Tp1 = 5 Tпп01 =0
Кн01=1
R1 =0 Tпз01 =5
Трп01=0 Rп01 =0
Всі результати розрахунку наведені в
таблиці 4.
Таблиця
4. Параметри сіткового графіку
код
|
|
|
|
|
|
|
|
|
|
|
|
роботи
|
tочij
|
Трj
|
Тпj
|
Rj
|
Tрпij
|
Tрзij
|
Tппij
|
Тпзij
|
Rпij
|
Rcij
|
Kнij
|
i-j
|
|
|
|
|
|
|
|
|
|
|
|
0-1 |
5 |
5 |
5 |
0 |
0 |
5 |
0 |
5 |
0 |
0 |
1 |
1-2 |
5 |
10 |
10 |
0 |
5
|
10 |
5 |
10
|
0 |
0 |
1 |
2-3 |
1 |
11 |
11 |
0 |
10 |
11 |
10 |
11 |
0 |
0 |
1 |
2-4 |
3 |
13 |
13 |
2 |
10 |
13 |
12 |
15 |
2 |
0 |
0.75 |
2-8
|
1 |
20
|
20 |
0 |
10 |
11 |
19 |
20 |
9 |
9 |
0.1 |
2-20 |
7 |
34 |
34 |
0 |
10 |
17 |
27 |
34 |
17 |
17 |
0.29 |
3-5 |
4 |
15 |
17 |
2 |
11 |
15
|
13 |
17 |
2 |
0 |
0.72 |
код
|
|
|
|
|
|
|
|
|
|
|
|
роботи
|
tочij
|
Трj
|
Тпj
|
Rj
|
Tрпij
|
Tрзij
|
Tппij
|
Тпзij
|
Rпij
|
Rcij
|
Kнij
|
i-j
|
|
|
|
|
|
|
|
|
|
|
|
3-6
|
7 |
18 |
18 |
0 |
11 |
18 |
11 |
18 |
0 |
0 |
1 |
4-5 |
2 |
15 |
17 |
2 |
13 |
15 |
15 |
17 |
2 |
0 |
0.75 |
5-6 |
1 |
18 |
18 |
0 |
15 |
16
|
17 |
18 |
2 |
2 |
0.75 |
6-7 |
1 |
19 |
19 |
0 |
18 |
19 |
18 |
19 |
0 |
0 |
1 |
7-8 |
1 |
20 |
20 |
0 |
19 |
20 |
19 |
20 |
0
|
0 |
1 |
7-10 |
1 |
20
|
21 |
1 |
19 |
20 |
20 |
21 |
1 |
0 |
0.75 |
8-9 |
2 |
22 |
22 |
0 |
20 |
22 |
20 |
22 |
0 |
0 |
1 |
9-12 |
1 |
23 |
23 |
0 |
22 |
23 |
22 |
23 |
0 |
0 |
1 |
9-14 |
1 |
25 |
25 |
0 |
22 |
23 |
24 |
25 |
2 |
2 |
0.33 |
10-11 |
1 |
21 |
24 |
3 |
20 |
21 |
23 |
24 |
3 |
0 |
0.5 |
10-12 |
2 |
23 |
23 |
0 |
20 |
22 |
21 |
23 |
1 |
1 |
0.75 |
11-14 |
1 |
25 |
25 |
0 |
21 |
22 |
24 |
25 |
3 |
3 |
0.5 |
12-13 |
1 |
24 |
24 |
0 |
23 |
24 |
23 |
24 |
0 |
0 |
1 |
13-14 |
1 |
25 |
25 |
0 |
24 |
25 |
24 |
25 |
0 |
0 |
1 |
14-15і |
3 |
28 |
28 |
0 |
25 |
28 |
25 |
28 |
0 |
0 |
1 |
15-16 |
1 |
29 |
29 |
0 |
28 |
29 |
28 |
29 |
0 |
0 |
1 |
16-17 |
1 |
30 |
30 |
0 |
29 |
30 |
29 |
30 |
0 |
0 |
1 |
17-18 |
1 |
31 |
32 |
1 |
30 |
31 |
31 |
32 |
1 |
0 |
0.75 |
17-20 |
4 |
34 |
34 |
0 |
30 |
34 |
30 |
34 |
0 |
0 |
1 |
18-19 |
1 |
32 |
33 |
1 |
31 |
32 |
32 |
33 |
1 |
0 |
0.75 |
19-20 |
1 |
34 |
34 |
0 |
32 |
33 |
33 |
34 |
1 |
1 |
0.75 |
20-21 |
3 |
37 |
37 |
0 |
34 |
37 |
34 |
37 |
0 |
0 |
1 |
21-22 |
6 |
43 |
43 |
0 |
37 |
43 |
37 |
43 |
0 |
0 |
1 |
5.1.6. Аналіз сіткового графіка і його
оптимізація .
Одним з перших кроків аналізу
побудованого графіка є перегляд топології сітки. При цьому перевіряється
нумерація подій, встанов-люється доцільність вибору робіт і структури сітки.
Поряд із встанов-ленням зайвих робіт і перевіркою доцільності встановленого
рівня їх деталізації повинно розглядатись питання про можливість паралель-ного
виконання робіт, виходячи з особливостей запланованого процесу і кількості
робітників.
Наступним кроком аналізу сіткового графіка
проводиться його оптимізація. При цьому розв’язуються задачі щодо виявлення
можливостей кращого розподілу трудових видів ресурсів.
Після досягнення необхідного терміну
розробки проводиться оптимізація розподілу ресурсів. Аналіз календарного
графіка та діаграми завантаження виконавців показав на доцільність подальшої
оптимізації сіткового графіка. Оптимізація проведена за рахунок використання
вільних резервів часу (Rвij) шляхом їх заміни на робочий час або часткової
заміни (поділу резерву). Результати оптимізації діаграми завантаження
виконавців наведені на рис. 2.
5.2. Визначення затрат на виконання НДР.
Затрати на виконання НДР поділяють на
капітальні і поточні.
5.2.1. Капітальні затрати
Таблиця 5.
№
|
Назва основних фондів
|
Вартість в грн.
|
1 |
АМЦ-1515 |
10000 |
2 |
Самописець |
8000 |
3 |
СДО 125-15/3 |
18000 |
|
Разом |
36000 |
Поточні затрати на виконання НДР складаються з
наступних статей калькуляції :
- основні матеріали,
- покупні напівфабрикати,
- паливо і енергія зі сторони,
- амортизаційні відрахування,
-
заробітна плата
основна і додаткова,
- відрахування на соціальні заходи,
- накладні видатки.
5.2.2. Поточні затрати
5.2.2.1. Обчислення амортизаційних витрат
Знаючи норми амортизаціі можна визначити амортизацію обладнання
за формулою:
Аоб =
ЦоНаВ / F
де Цо - ціна обладнання, грн;
На - норма амортизації, %;
В - час використання,
год.;
F - річний фонд часу.
Норма амортизації для одного місяця :
Аі = Ці×На /12
де Ці - вартість,
На - норма амортизації.
Таблиця
6. Норма амортизаційних витрат
№
|
Основні фонди
|
Вартість, грн.
|
Норма аморт., %
|
Аморт. відрах., грн.
|
1 |
АМЦ-1515 |
10000 |
19 |
158.33 |
2 |
Самописець |
8000 |
23 |
153.33 |
3 |
СДО 125 - 15/3 |
18000 |
15 |
225 |
Разом: 536.66
грн.
5.2.2.2. Відрахування на оренду
приміщення
Вартість оренди приміщення в якому
проводяться дослідження можна визначити знаючи: орендну плату за 1 м2 за місяць,
площу приміщення і час роботи .
Впр =
Цар×Sплtрб / 30
Впр =
3´(3. 5´4. 5)60 /30 = 94.5 грн.
5.2.2.3. Визначення
затрат на матеріали
Вартість матеріалів, витрачених на виготовлення дослідних взірців, проведення
дослідів визначається на основі програми дослідів,
норм розходу, цінами або по кількості годин досліджень
і нормативах затрат на годину досліджень.
Затрати на основні матеріали
визначаються за формулою :
Мо = (
1+ Ктз -Кво ) ЦiНi
де Ці - оптова ціна одиниці
виробу;
Ні - необхідна потреба в матеріалі;
Ктз - коеф., що враховує транспортно-заготівельні витрати;
Кво - коеф.,
що враховує відходи, які повертаються .
Приймаємо
Ктз= 0.08, Кво= 0.05 .
Таблиця 7. Затрати на матеріали.
№
|
Назва матеріалу
|
Один.виміру
|
Норма розходу
|
Ціна
од. вим.
|
Сума, грн
|
1 |
Пластини Si |
шт. |
20 |
20 |
412 |
2
|
Кисень |
балон |
1 |
15 |
15.45 |
3 |
Плавикова кислота
|
л |
2.5 |
3 |
7.73 |
4 |
Хлор |
балон |
1 |
15 |
15.45 |
5
|
Азот
|
балон |
1 |
15 |
15.45 |
|
|
|
Разом: |
|
466.08
|
Мо = (1+1.03-0.05)´[400+15+ 2.5´7.5+15+15]= 466.08 грн.
5.2.2.4. Розрахунок
вартості палива та енергії
Затрати на електроенергію розраховуються
за формулою:
Ес =
Мд´Fд´Це´Кн
де:
МДН-встановлена потужність енергетичних струмоприймачів, кВт;
Fд- дійсний фонд часу роботи даного виду обладнання, год.;
Це- ціна 1 кВт/год електроенергіі, грн;
Кн- коєф. використання енергетичних установок по потужності і часу (
Кн = 0. 8 ).
Таблиця 8.
N
|
Прилад
|
Час роботи,
год.
|
Споживана
потужність
|
Ціна за
1 кВт, грн
|
Вартість,
грн.
|
1 |
АМЦ-1515 |
150 |
1.5 |
0.23 |
41.4 |
2 |
Самописець |
150 |
1.5 кВт |
0.23 |
41.4 |
3 |
СДО 125-5/3 |
200 |
60 кВт |
0.23 |
2208 |
Разом: 2290.8
5.2.2.5. Визначення фонду заробітної плати
Таблиця 9.
№
|
Посада
|
Місячний оклад, грн.
|
Денна ставка, грн.
|
Трудоємність, людино-дні
|
Витрати на З/П, грн.
|
1 |
Науковий керівник |
300 |
12.50 |
33 |
412,50 |
2 |
Студент-дипломник |
40 |
1,67 |
66 |
110 |
3 |
Консультант з ЕЧ |
360 |
15 |
3 |
45 |
4 |
Консультант з ОП |
360 |
15 |
3 |
45 |
Разом: 612,50
Відрахування
на соціальні заходи
1 |
Відрахування на соцстрах ( 1,5% )
|
612,50´0,025=15,31 грн |
2 |
Відрахування в фонд зайнятості (4%)
|
612,50´0. 025=15,31 грн. |
3 |
Відрахування в пенсійний фонд (32%) |
612,50´0,32=196 грн. |
Разом : 234,58 грн.
Фонд заробітної
плати : 612,50+234,58 = 847,08 грн.
Накладні
видатки : 612,50´1.5 =
918,75 грн.
5.2.3. Кошторис
витрат на виконання НДР.
Таблиця 10.
N
|
Назва елементів витрат
|
Сума витрат, грн.
|
1 |
Амортизаційні витрати |
536,66 |
2 |
Оренда приміщення
|
94.5
|
3 |
Витрати на матеріали
|
466.08 |
4 |
Витрати на енергоресурси |
2290.8 |
5 |
Заробітна плата
|
847,08 |
6 |
Накладні видатки |
918,75 |
7 |
Відрахування на соціальні заходи |
234,58 |
|
Всього |
5388,45 |
5.3. Оцінка техніко-економічної
ефективності.
В даній роботі для оцінки
науково-технічної і економічної ефективності використовується
метод бальних оцінок.
Щоб мати можливість
оперувати з любою кількістю ознак та показників при визначенні
науково-технічного ефекту НДР, необхідно
використовувати при визначенні цього ефекту певну оцінку. Критерій науково-технічної ефективності НДР (Кнте) визначається за
формулою:

де sjk - середнє
значення балу, присвоєне експертами певній якості n-ї
ознаки;
gj - нормована величина валового
коефіцієнту властивості
n-ї ознаки;
sjkmax - максимально можлива
величина балу.
Для оцінки науково-технічної ефективності окремих НДР найбільш доцільно прийняти
чотири важливіших ознаки :
науково-технічний рівень, перспективність, можливий масштаб впровадження, степінь
ймовірності успіху.
Tаблиця 11. Нормована величина
вагового коефіцієнту важливості ознаки
Ознаки
g
|
gi
|
Науково-технічний рівень g1
Перспективність g2
Можливий масштаб впровадження g3
Степінь ймовірності успіху g4
|
0.3
0.3
0.2
0.1
|
Кожна названа ознака володіє деяким набором якостей. На основі ряду експертних
досліджень, кожне з яких проводиться в кілька турів з ціллю забезпечення
високої узгодженості думки експертів, були отримані округлені величини великих
оцінок кожної якості j-ї ознаки.
Таблиця 12
Ознака
|
Якість ознаки
|
Бали
|
Науково-технічний рівень
передбачених результатів |
Перевищує світові досягнення
На рівні світових досягнень
Наближається до світових досягнень
Тривіальний
|
10
7
5
1
|
Ознака
|
Якість ознаки
|
Бали
|
Перспективність |
Дуже важливі
Важливі
Корисні
|
10
7
3
|
Можливий масштаб
Використання
|
В декількох галузях господарства, науки
Галузевий
В межах підприємства
|
10
1
1
|
Ймовірність успіху |
Велика
Помірна
Низька
|
10
6
3
|
Результати експертних досліджень
приведені в таблиці 13.
Таблиця 13.
Ознака
|
Мах Оцінка
|
Оцінка експертів
|
s jk
|
1
|
2
|
3
|
Науково-технічний рівень
Перспективність
Можливий масштаб використання
Ймовірність успіху
|
10
10
10
10
|
8
8
10
9
|
9
9
9
9
|
9
10
10
7
|
8.7
9
9.7
8
|
Кнте = (0.3´8.7+0.4´9+0.2´9.7+0.1´8)/(3+4+2+1)
Кнте = 0.895
Ефективність даної дипломної роботи полягає
в тому, що з її виконанням
вдалось визначити залежність характеристик
МДН - структур від
легування цинком, а
також домогтися покращення
цих характеристик. Це дало можливість покращити роботу структур і їх електрофізичні параметри.
Величину економічного ефекту визначають методом порівняльної економічної ефективності з використання
результатів проведених
розробок за наведеними витратами.
Абсолютна величина економічного
ефекту.
Еп
= [ (С1+Ен´К1)-(С2+Ен´К2) ]´Ап
де Еп-
середньорічна сума
економічного ефекту, що очікується від реалізації НДР.
С1 і С2 - собівартість
одиниці продукції відповідно по базовому і новому варіантах в тому ж році.
К1 і К2-
питомі капітальні вкладення відповідно по базовому і новому варіантах.
Ен - нормативний коефіцієнт ефективності капітальних вкладень.
Ап -
очікуваний річний об’єм виробництва продукції в натуральному або грошовому виразі.
Співставлення абсолютної величини
економічного ефекту із витратами на проведення
НДР.
Ез = Еп/Зп
де Ез -
коефіцієнт ефективності робіт з розрахунку на 1 грн.
витрат.
Зп - передвиробничі
витрати організації на проведення НДР.
Співставлення абсолютної величини економічного
ефекту з витратами праці
виконавців робіт.
Ен = Еп/R
де Ен -
коефіцієнт ефективності
робіт по перерахунку на одного виконавця.
R - кількість виконавців, що
приймали участь у виконанні НДР.
Еп
= [(20+0.15´1100)-(19.5+0.15´2700)]´25
Еп = 124400грн.
Ез = 124400 / 5388.45=23,09 грн.
Ен = 124400/4=31100 грн.
5.4. Висновки з економічної
оцінки
Економічна оцінка дипломної
роботи, що носить науково - дослідний характер, показала, що робота є досить
ефективною з економічної точки зору, оскільки має вагоме наукове значення ( як
показує коефіцієнт науково – технічної ефективності) при порівняно невисоких
затратах.
В економічній частині дипломного проекту було виконано
планування НДР, для чого було використано систему сіткового планування і
управлівння, що забезпечило чітке узгодження всіх робіт в часі. Провівши
оптимізацію сіткового графіка, досягнено вирівнювання завантаження виконавців.
В будь-який момент часу для виконання роботи необхідно не більше 4-х
виконавців. Здійснено розрахунок витрат на проведення НДР. Планова кошторисна
вартість робіт становить 5388,45 грн., з них на оплату праці – 847,08 грн.,
відрахування на соціальні заходи – 234,58 грн. Визначенний коефіцієнт науково-технічної
ефективності (К = 0.895) є достатній для НДР і оправдовує понесені витрати.
ОХОРОНА
ПРАЦІ
КОРОТКА
ХАРАКТЕРИСТИКА ОБ’ЄКТА ПРОЕКТУВАННЯ.
Для виконання робіт по дослідженню
впливу легування на параметри МОН-структур застосовуються прилади:
·
установка
для вимірювання ВФХ АМЦ-1515 з напругою живлення 220 В;
·
самописець
з напругою живлення 220 В;
·
ВЧ-генератор
з напругою живлення 220 В.
Таким чином, у процесі
виконання зазначених робіт можливі ураження електричним струмом, знаходження у
високочастотному електромагнітному полі. З метою створення сприятливих та
безпечних умов при виконанні робіт пропонується ряд заходів з охорони праці.
2 ВИБІР
ПРИМІЩЕННЯ І ОРГАНІЗАЦІЯ РОБОЧОГО МІСЦЯ.
Для проведення робіт пропонується
приміщення технологічної лабораторії з такими розмірами:
·
довжина 4.
5м;
·
ширина 3.
5 м;
·
висота 3.
5м.
Кількість працюючих: |
2 чоловіка. |
Об’єм приміщення: |
55.125 куб. м. |
Об’єм повітря на одного працюючого: |
55.125 / 2 = 27.5 куб. м. |
Загальна площа приміщення: |
4.5 ´ 3.5 = 15.75 кв. м. |
Загальна площа на одного
працюючого: |
15.75 / 2 = 7.875 кв. м. |
Вільна від обладнання площа на
одного працюючого: |
7.25 кв. м. |
У відповідності до вимог санітарних
норм СН 245-71, на одного працівника необхідно не менше 4. 5 кв. м вільної від
обладнання площі. Об’єм повітря повинен бути не менше 15 куб. м, а мінімальна
висота стелі приміщення - 3. 5м
Обране приміщення відповідає вимогам
санітарних норм для виконання науково-дослідницьких робіт.
Згідно з ГОСТ 12.2.032-78
пропонується робоче місце для виконання робіт в положенні "сидячи".
Для роботи пропонується
використовувати письмові столи:висота робочої поверхні для мужчин - 1020 мм,
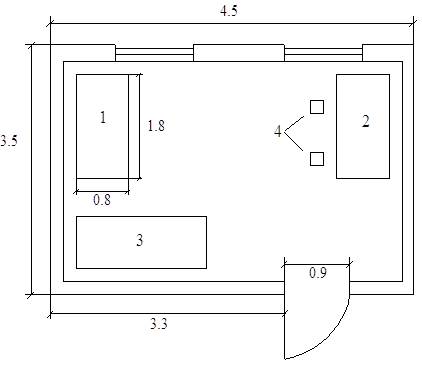
Рис. 1. Приміщення та розташування
обладнання:
1 - стіл з установкою для вимірювань; 2 - робочі місця;
3 - шафа; 4
- крісло.
ширина робочої
поверхні 800 мм,
висота сидіння 430
мм,
висота простору
для ніг 600 мм
4.3 МЕТЕОРОЛОГІЧНІ УМОВИ ВИРОБНИЧОГО
СЕРЕДОВИЩА.
Згідно з ГОСТ 12. 1. 005-88 роботи відносяться до
легких фізичних робіт категорії 1а:
енергозатрати не перевищують 150
ккал/год;
надлишок
виділеного тепла не перевищує 20 ккал/год
Оптимальні та допустимі
норми температури, відносної вологості та швидкості руху повітря в робочій зоні
приміщення представлені в таблиці 1.
Таблиця 1.
Період року |
Категорія робіт |
Температура, град С |
Відносна
вологість,
%
|
Швидкість
руху
не більше,
м/с
|
Оптимальна |
Допустима |
верхня границя |
нижня границя |
на робочих місцях |
постійних |
непостійних |
постійних |
непостійних |
Оптимальна |
Оптимальна |
Оптимальна |
Оптимальна |
холод-ний |
Легка 1а |
22. . . 24 |
25 |
26 |
21 |
18 |
40. . . 60 |
75 |
0. 1 |
0. 1 |
теплий |
Легка 1а |
23. . 25 |
28 |
30 |
22 |
20 |
40. . . 60 |
55 (t=28oC)
|
0. 1 |
0. 2 |
ВЕНТИЛЯЦІЯ І ОПАЛЕННЯ
Необхідний загальний повітрообмін:
L = K´V м3/год,
де: К - кратність повітрообміну;
V - об’єм приміщення.
К = 2,
V = 55. 125 м3
L = 2×55. 125 = 110. 25 м3/год.
У холодний період року передбачається
включення центрального водяного опалення.
Для забезпечення чистоти повітря та
дотримання заданих метеорологічних умов згідно вимоги СНиП 2. 04. 05. 86 передбачається
встановлення кондиціонеру типу КБІ-0. 5-0143з такими характеристиками:
максимальна продуктивність
по повітрю: 500 м3/год;
продуктивність по холоду: 2300
ккал/год;
споживана потужність
електроенергії: 1100 Вт.
ОСВІТЛЕННЯ.
Згідно СНиП ІІ-4-79
[23] роботи відносяться до III розряду точності, оскільки мінімальний розмір
об’єкту розпізнавання - не більше 0.3. . . 0.5 мм.
Природне освітлення.
В лабораторії
використовується бокове природне освітлення. Необхідні розміри вікон:
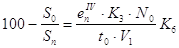
де: S0 - площа
вікон при боковому освітлення, м;
S0 -
площа підлоги, м2;
-
коефіцієнт природнього освітлення, визначений для IV зони за формулою:
,
еn
- нормоване значення коефіцієнта природного освітлення, що дорівнює: 1. 5; c
- коефіцієнт сонячності клімату: 0.
75;
m - коефіцієнт світлового
клімату: 0. 9
K3 -
коефіцієнт запасу;
N0 -
світлова характеристика вікна;
t0 -
загальний показник світлопропускання, що визначається, в свою чергу, за
формулою:
t0 = t1 × t2 × t3 × t4 × t5
t1 - коефіцієнт пропускання
матеріалу вікна:
для подвійного
віконного скла 0. 8;
t2 -
коефіцієнт втрат:
для дерев'яних
роздільних переплетень вікон 0. 6;
t3 -
коефіцієнт втрат несучої конструкції:
при боковому
освітленні 1. 0;
t4 -
коефіцієнт втрат світла в сонцезахисних пристроях:
при використанні
штор 1. 0;
t5 -
коефіцієнт втрат в сонцезахисній сітці:
при відсутності
сітки 1. 0.
t0 = 0. 8×0. 6×1×1×1 = 0. 48;
V1 - коефіцієнт, що враховує
збільшення КПО при боковому освітленні за рахунок світла, відбитого
від поверхні приміщення;
К6 - коефіцієнт, що враховує
затемнення вікон будівлями, що стоять навпроти.
Для нашого
приміщення: = 1.
01;
Sn
= 15. 8 м; t0 = 0. 48;
V1
= 2; K3 = 1. 3;
N0
= 13; K6 = 1.
Звідси:
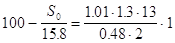
Необхідна площа вікон в приміщенні:
S0 = 2. 81 м2
В приміщенні є два вікна розміром 1.
2´1.
5 метра. Загальна площа вікон складає 2´1. 2´1. 5 = 3. 6 метра, що є
більшим від необхідної розрахункової площі вікон, тобто природне освітлення
задовольняє нормативним нормам.
Штучне освітлення.
Для III розряду високої
точності виконуваних робіт нормована освітленість Е = 300 лк [22], оскільки
мінімальний розмір об’єкта розпізнавання - 0. 3. . . 0. 5 мм.
Для освітлення обрано
світильники з люмінесцентними лампами. Сумарний світловий потік визначається за
формулою [24]:
,
де S - площа приміщення: 15.
8 м2;
К - коефіцієнт
запасу:
для люмінесцентних
ламп 1. 5. . . 2. 0;
Z - коефіцієнт
мінімальної освітленості: 1. 1;
h - коефіцієнт використання світлового
потоку,
що залежить від
показників приміщення,
типу світильника
та коефіцієнту відбиття стін,
стелі та робочої
поверхні 0. 45.
лм.
Для освітлення приміщення
використані люмінесцентні лампи ЛБ-40, що мають світловий потік Фf
= 2000 лм. Необхідна кількість ламп:
n = Фf /Фл
n = 17270 / 2000 = 18 шт.
Лампи розміщені в чотирьох
світильниках типу ЛПОЗІ-2х40-002У4 ( по дві в кожному світильнику) (рис. 2).
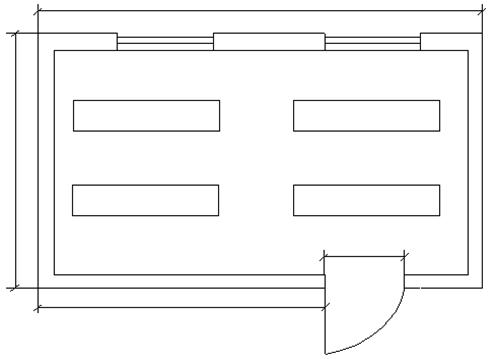
Рис.2. Схема розміщення світильників
ЕЛЕКТРОБЕЗПЕКА.
Приміщення електролабораторії згідно з ПУЕ-86 [27] п .
1. 1. 13 відноситься до 1-го класу, без підвищеної небезпеки (відсутні фактори,
що створюють підвищену небезпеку, а саме:
а) вологість або струмопровідний пил;
б) струмопровідні підлоги;
в) підвищені температур;
г) можливість одночасного дотику
людини до заземлених металоконструкцій приміщення та металевого корпусу
електрообладнання;
д) хімічно активного або органічного
середовища тощо).
Крім того, підлога біля
електроустановок вкрита електроізолюючим покриттям. По електробезпеці персонал
, що обслуговує електроприлади в даній лабораторії згідно з вимогами ПТЕ
відноситься до 1 групи . Для захисту від можливого ураження електричним струмом
передбачається захисне заземлення. До заземлюючого пристрою підлягають
приєднанню: корпуси електричних машин, апаратів, а також металеві корпуси любих
переносних або пересувних електроприймачів. Опір заземлюючого пристрою в усі
пори року згідно ПУЄ не повинен перевищувати 4 0м.
Всі з’єднання елементів заземлюючого
пристрою виконуються зварюванням, приєднання до приладів - за допомогою спеціальних
лабораторних зажимів та гнучких провідників з січенням жил не менше 1. 5 кв.
мм.
Розрахунок заземлюючого пристрою.
1. Вихідні дані:
- питомий опір грунту: r = 40 Oм×м;
тип заземлювача:
вертикальний -
пруток металевий d = 16 мм;
горизонтальний -
сталева полоса 25 ´ 4 мм b = 25 мм2
- довжина вертикальних
заземлювачів l = 2. 5 м;
- віддаль між вертикальними
заземлювачами а = 2. 0 м;
- глибина прокладання
заземлювача в грунті b = 0. 7 м.
2. Розрахунковий опір грунту:

де Y = 1. 32 - коефіцієнт
сезонності.
rp3 = 1. 32 × 40 = 52. 8 Ом×м
3. Опір розтікання струму в землі
одного вертикального заземлювача:
,
Z = h + l/2 = 0. 7+2. 5/2 = 1.
95 м - віддаль від поверхні землі до середини вертикального заземлювача

4. Необхідна кількість вертикальних
електродів:
n = RB /(RH × n)
n - 0. 45 -
коефіцієнт екранування.
n = 16. 32 / (4 × 0. 45) = 9. 0 шт.
5. Довжина горизонтального
заземлювача RГ , що з'єднує вертикальні заземлювачі:
L =а (n - 1)
L = 2 (9 - 1) = 16 метрів.
6. Опір горизонтального заземлювача К
, прокладеного на глибині h = 0. 7 м від поверхні землі:
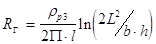
Ом.
7. Загальний опір заземлюючого
пристрою:
,
де nB = 0. 5-
коефіцієнт використання вертикального заземлювача;
nГ = 0.
6- коефіцієнт використання горизонтального заземлювача.
Ом.
Опір захисного заземлення задовольняє
вимогам ПУЕ.
Розрахунок заземлюючого пристрою
Питомий опір грунту |
r
|
Ом×м |
40 |
Діаметр вертикального заземлювача |
d
|
m |
0. 016 |
Ширина полоси горизонтального |
|
|
|
заземлювача |
b
|
м |
0. 025 |
Віддаль між вертикальними |
|
|
|
заземлювачами |
а
|
м |
2 |
|
|
|
|
Довжина вертикальних заземлювачів |
1
|
m |
2. 5 |
|
|
|
|
Глибина прокладання заземлення |
h
|
м |
0. 7
|
Коефіцієнт сезонності |
y
|
|
1. 32 |
Коефіцієнт екранування |
ne
|
|
0. 45 |
Коеф. використання вертик.
заземлювача |
nв
|
|
0. 5 |
Коеф. використання гориз.
заземлювача |
nг
|
|
0. 6 |
|
|
|
|
Віддаль
від поверхні землі
|
|
|
|
до середини вертикального
заземлювача |
Z
|
m |
1. 95 |
|
|
|
|
Опір розтікання струму в землі |
|
|
|
одного вертикального заземлювача |
Rв
|
Ом |
15. 4823 |
|
|
|
|
Необхідна кількість |
|
|
|
вертикальних електродів |
n
|
шт |
9 |
|
|
|
|
Необхідна довжина |
|
|
|
горизонтальних заземлювачів |
L
|
м |
16 |
|
|
|
|
Опір горизонтального |
|
|
|
Заземлювача |
Rг
|
Oм |
2. 99016
|
|
|
|
|
Загальний
опір
|
|
|
|
Заземлюючого пристрою |
R
|
Oм |
2. 03537 |
ЗАХИСТ
ВІД ДІЇ ЕЛЕКТРОМАГНІТНИХ ПОЛІВ.
Оскільки випромінювання ВЧ має високу
проникливість, то, згідно ГОСТ 12. 1. 006-84 пропонується проводити не рідше
одного разу на рік вимірювання напруженості та густини потоку енергії
електромагнітного поля. Додатково такі вимірювання проводяться при введенні
нових приладів, при внесенні змін в конструкцію, розміщення та режим роботи
діючих пристроїв, після проведення ремонтних робіт або при організації нового
робочого місця. Роботи по перевірці рівня електромагнітних полів проводяться
спеціальним персоналом з формою допуску до цих робіт. Результати вимірювань
фіксуються в спеціальному журналі у формі протоколу.
За даними останніх вимірювань,
максимальне енергетичне навантаження з врахуванням часу дії його на організм
працівника за робочу зміну в лабораторії складає 8. 5 Вт/кв. м. Максимальне
значення густини потоку енергії не повинно перевищувати 10 Вт/кв. м, що означає
- додаткових засобів по захисту персоналу від електромагнітного поля передбачати
не потрібно.
4.8
ПОЖЕЖНА ПРОФІЛАКТИКА.
Згідно СНиП 2. 09. 02. 85 приміщення технологічної лабораторії
відноситься до категорії В ( пожежонебезпечна), в зв’язку з чим передбачаються
встановлення пожежної сигналізації, а саме - димового повідомлювача ДИ-1. Як
первинний засіб пожежогасіння передбачається встановити вуглекислотний
вогнегасник ОУ-5. На випадок виникнення пожежі передбачені шляхи евакуації
людей та матеріальних цінностей.
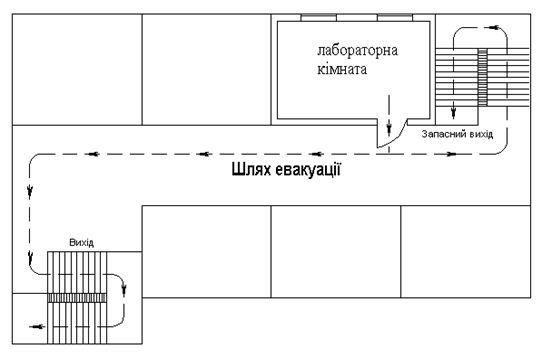
Рис. 3. Схема евакуації.
|