Лабораторная работа: Загальні властивостi будiвельних матеріалів
Лабораторная работа: Загальні властивостi будiвельних матеріалів
1. Загальні властивостi будiвельних матерiалiв
Розрахунки по
визначенню загальних властивостей будiвельних матерiалiв дозволяють оцiнити їх
вiдповiднiсть технiчним вимогам, можливiсть застосування в конкретних умовах
експлуатації. Знання загальних властивостей матерiалiв необхiдно для
рiзноманiтних iнженерних розрахункiв. Наприклад, для розрахунку навантажень,
визначення маси споруд, транспортних розрахункiв, вибору місткості складських
примiщень необхiдно знати щiльнiсть матерiалiв. Для оцiнки мiцностi i стiйкостi
споруд, прогнозу їх довговiчностi важливo врахування мiцностi матерiалiв, вiдношення
їх до вологи, температури i т.п.
При розрахунках,
що враховують властивості матеріалів, необхідно добре орієнтуватись в їх
розмірностях, що відображають зв’язок з основними величинами системи одиниць
виміру.
В табл. 1.1 і 1.2
наведені розрахункові формули основних фізичних та механічних властивостей
різних матеріалів.
В Міжнародній
системі одиниць (СІ) в якості основних прийняті наступні одиниці: метр (м) –
одиниця довжини; кілограм (кг) – одиниця маси; секунда (с) – одиниця часу;
ампер (А) – одиниця сили струму; градус Кельвіна (°К) – одиниця термодинамічної
температури; кандела (кд) – сила світла і моль – кількість речовини. Іноді
зручніше застосовувати одиниці більші (кратні) або дрібні (часткові). Їх
утворюють множенням початкових одиниць на число 10, взяте у відповідному ступені.
Назва одиниць при цьому набуває відповідної приставки (табл. 1.3).
Температуру
прийнято виражати як в градусах Кельвіна (°К), так і в градусах Цельсія
(°С).
Вибрати приставки
рекомендується таким чином, щоб числові значення величини знаходились в
діапазоні 0,1…1000.
Таблиця 1.1
Властивість
|
Розмірність
|
Розрахункова
формула
|
Пояснення
до формули
|
Дійсна густина |
кг/м3
|

|
m – маса сухого матеріалу; V – об’єм в ущільненому
стані |
Середня густина |
кг/м3
|

|
V1 – об’єм матеріалу з урахуванням пор та
порожнин
|
Властивість
|
Розмірність
|
Розрахункова
формула
|
Пояснення
до формули
|
Насипна густина |
кг/м3
|

|
Vн – об’єм матеріалу в пухкому стані
|
Пористість |
% |
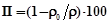
|
|
Вологість |
% |
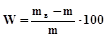
|
mв – маса вологого матеріалу
|
Гігроскопічність |
% |
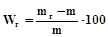
|
mг – маса матеріалу після досягнення
рівноважної вологості при перебуванні у повітряному середовищі із 100 %–ю
вологістю
|
Водопоглинання за масою |
% |
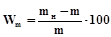
|
mн – маса насиченого водою матеріалу
|
по об’єму |
% |
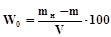
|
|
Сорбційна вологість |
% |
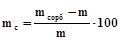
|
mсорб – маса матеріалу після досягнення
рівноважної вологості
|
Коефіцієнт фільтрації |
м/год |

|
Vв – об’єм води, яка просочилась; d – товщина стінки; S –
площа стінки; Dр – різниця гідростатичного тиску на границях стінки, мм вод. ст.; t – час
|
Коефіцієнт паропроникності |
г/(м.год. Па)
|

|
Vп – об’єм пари (густиною r), яка пройшла через стінку;
Dрп
– різниця тисків пари на границях стінки, Па
|
Коефіцієнт розм’якшення |
— |

|
Rнас – міцність насиченого в воді матеріалу;
Rс – міцність сухого матеріалу
|
Теплопровідність |
Вт/(м.°С)
|
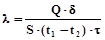
|
Q – кількість теплоти, Дж; t1 – температура
поверхні гарячої сторони зразка, °С; t2 – температура поверхні
холодної сторони зразка, °С
|
Властивість
|
Розмірність
|
Розрахункова
формула
|
Пояснення
до формули
|
Термічний опір |
м2.°С/Вт
|

|
|
Питома теплоємність |
кДж/(кг.°С)
|

|
|
Температуропровідність |
м2/год
|

|
|
Коефіцієнт лінійного теплового розширення |
— |

|
l0 – початкова довжина зразка; l1
– довжина зразка після нагріву
|
Таблиця 1.2
Властивість
|
Розмірність
|
Розрахункова
формула
|
Пояснення до формули
|
Межа міцності |
МПа |

|
F – руйнівне навантаження; S – розрахункова площа
перерізу зразка |
Твердість за Брінеллем |
МПа |
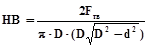
|
D – діаметр кульки; d – діаметр відбитку |
Стираність |
г/см2
|

|
m – маса зразка до стирання; m1 – маса
зразка після стирання; S – площа стирання
|
Ударна міцність |
МПа |
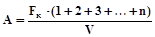
|
Fк – вага баби копра; n – порядковий
номер удару, який руйнує зразок
|
Усадка |
мм/м |

|
l0 – початкова довжина зразка; l1
– кінцева довжина зразка
|
Повзучість |
мм/м |
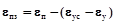
|
eп – повна деформація; eу – пружна деформація
|
Модуль пружності |
МПа |

|
sн – номінальна напруга
|
Межа текучості |
МПа |

|
Fт – навантаження, яке відповідає межі
текучості
|
Таблиця 1.3
Приставка
|
Позначення
|
Множник на який множать основну
одиницю
|
Приставка
|
Позначення
|
Множник на який множать основну
одиницю
|
Тера |
Т |
1012
|
Санти |
с |
10–2
|
Гіга |
Г |
109
|
Мілі |
м |
10–3
|
Мега |
М |
106
|
Мікро |
мк |
10–6
|
Кіло |
к |
103
|
Нано |
н |
10–9
|
Гекто |
г |
102
|
Піко |
п |
10–12
|
Дека |
да |
101
|
Фемто |
ф |
10–15
|
Деци |
д |
10–1
|
Ато |
а |
10–18
|
1.1. Густина і
пористість
1. Визначити
мінімально необхідну корисну площу штабелів для розміщення m=10 т сипучого
матеріалу з насипною густиною rн=1300 кг/м , якщо висота шару
матеріалу в штабелях не повинна перевищувати h=1,5 м.
Знаходимо об’єм
матеріалу в штабелях:
v=m/rн =10000:1300=7,69 м3.
Площа штабелів
повинна складати:
S=v/h=7,69:1,5=5,13
м2.
2. Визначити
ємність, довжину штабельного складу щебеню, необхідного для 10 – добової роботи
бетонного заводу із добовою витратою mдоб.=600 т. Висота
штабеля h=4 м. Кут насипу щебеню b=35°. Насипна густина щебеню rн=1450 кг/м3.
При розрахунку
ємності складу заповнювачів використовують формулу:
vз=vдоб.×tзбер.×1,2×1,02
де vдоб
– добова витрата матеріалів, м3 ; .tзбер. – нормативний запас
збереження матеріалів;
1,2 – коефіцієнт
розрихлення; 1,02 – коефіцієнт, що враховує втрати при транспортуванні.
vдоб.=mдоб./rн=600:1,45=413,7 м3;
v=413,7×10×1,2×1,02=5063,7 м3.
Довжину
штабельного складу знаходять за формулою:

де b – кут природного ухилу
матеріалу а штабелі:
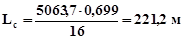
Площа складу
визначають за формулою:
;
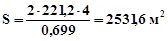
3. Розрахувати
об’єм бункерів закритого складу заповнювачів, що забезпечують загальний
нормативний запас на t=10 діб роботи бетонного заводу із добовим випуском
бетонної суміші vдоб.=500 м3. Витрата піску і гравію
на 1 м3 бетонної суміші (з врахуванням виробничих витрат)
складає відповідно П=712 кг/м3 і Г=1320 кг/м3.
Коефіцієнт заповнення бункерів 0,9. Насипна густина піску rн.г=1500 кг/м3 і
гравію rн.г.=1400 кг/м3.
Нормативний запас
заповнювачів:
Піску по масі – Пн=vдоб.×t×П=500×10×0,712=3560 т;
Гравію по масі –
Гн=vдоб.×t×Г=500×10×1,32=6600 т;
Піску за об’ємом
– vп.н.=Пн/rн.п.=3560:1,5=2380 м3;
Гравію за об’ємом
– vг.н.=Гн/rн.г.=6600:1,4=4360 м3.
З поправкою на коефіцієнт
заповнення 0,9 необхідні об’єми бункерів складів піску (vб.п.) і
гравію (vб.г.) буде відповідно vб.п=2650 м3
і vб.г=4840 м3.
4. Насипна
густина сухого піску rн=1500 кг/м3. При 5% – й вологості (wп.=5%)
вона зменшилась до rнw=1150 кг/м3. Визначити приріст об’єму піску
за рахунок зволоження.
Перший спосіб
рішення:
1 т сухого піску займає об’єм vc=1:1,5=0,66 м3,
вологого піску vв=1:1,15=0,87 м3.
Приріст об’єму
піску складає:
.
Другий спосіб
рішення:
Маса піску після зволоження :
.
Об’єм вологого
піску: vw=m/rнw=1575:1150=1,37м3.
Dv=vw–vc=1,37–1=0,37
або 37%.
5. Визначити
середню густину кам’яного зразка неправильної форми, якщо при його зважуванні
на повітрі маса була mс=100 г, а у воді mw=55 г.
До зважування у воді зразок парафінували. Маса парафінованого зразка mп.з.=101,1 г.
Густина парафіну rп.=0,93 г/см3.
Об’єм
парафінованого зразка по закону Архімеда дорівнює втраті його маси при
зважуванні у воді, тобто при густині води rв.=1 г/см3.
.
Маса парафіну mп=mп.з.–mс=101,1–100=1,1 г,
а об’єм його vп=mп/rп=1,1:0,93=1,18 см3.
Об’єм
непарафінованого зразку v0=vп.з.–vп.=46–1,18=44,82 см3.
Середня густина
матеріалу rо=mс/vо=100:44,82=2,23 г/см3.
6. При визначенні
дійсної густини будівельного гіпсу була взята наважка mо=85 г.
В колбу Ле–Шательє була внесена частина цієї наважки, залишок склав m1=15,5 г.
При цьому рівень керосину у колбі підвищився від нульової відмітки до 25 см3.
Розрахувати дійсну густину будівельного гіпсу.
Маса гіпсу, що
поміщена у колбу Ле–Шател’є,
mг=mо–m1=85–15,5=69,5 г
Об’єм гіпсу в
абсолютно щільному стані дорівнює об’єму витисненого керосину, тобто vг=25 см3.
Таким чином,
дійсна густина гіпсу r=mг/vг=69,5:25=2,7 г/см3.
7. Яке
навантаження на кожну з двох опор здійснює залізобетонна балка прямокутного
перерізу розміром 60´14 см і довжиною l=6,5 м при середній густині
залізобетону r=2500 кг/м3?
Об’єм балки vб=0,60×0,14×6,5=0,55 м3;
Маса балки mб=vб×rо=0,55×2500=1380 кг.
Чисельне значення
маси тіла в кілограмах (кг) рівне чисельному значенню його ваги, тобто сили
тяжіння в кілограмах (кгс). В СІ сила вимірюється в ньютонах. 1 Н – сила,
що повідомляє тілу масою 1 кг прискорення 1 м/с2 в напрямку
дії сили. 1 кгс»10 Н.
Таким чином, сила
або навантаження, що здійснює залізобетонна балка на дві опори, складе Fб=1380
.10=13,8 кН;
Навантаження, що
діє на кожну опору, Fo=13,8:2=6,9 кН.
8. Зовнішня
стінова панель із газобетону має розміри 3,1´2,9´0,3 м і масу mп=2160 кг.
Визначити пористість газобетону, приймаючи значення дійсної густини r=2,81 г/см.
Об’єм панелі vп=3,1×2,9×0,3=2,7 м3;
Середня густина
газобетону rо=mп/vп=2160:2,7=800 кг/м3.
Пористість
газобетону

9. Зразок із
газобетону з розміром ребер а=20 см занурений у воду і плаває. Висота над
рівнем води в перший момент складала h=6,5 см. Визначити густину
газобетону, приймаючи його дійсну густину r=2,79 г/см3.
Поглинанням води при цьому можна знехтувати.
Маса (об’єм)
води, що був витиснений зразком газобетону, рівна масі зразка. Оскільки висота
зразка над рівнем води 6,5 см, значить, він занурився на h1=20–6,5=13,5 см
і витиснув при цьому vв=20´20´13,5=5400 см3
води. Таким чином, маса зразка mо=5400 г або 5,4 кг.
Об’єм зразка –
куба з а=20 см, vо=20´20´20=8000 см3.
Середня густина
газобетону rо=mо/vо=5400:8000=0,68 г/см2
або 680 кг/м3.
10. Кузов
автомашини розміром 2,8´1,8´0,6 м заповнений на 2/3 своєї висоти щебенем, маса
автомашини без щебеню mа=3 т, із щебенем m'а=5,86 т.
Розрахувати насипну густину щебеню і його порожнистість. Дійсна густина щебеню rщ=2,700 г/см3.
Об’єм щебеню vщ=2,8×1,8(0,6×2/3)=2 м3.
Маса щебеню mщ=m'а–mа=5,86–3=2,86 т.
Насипна густина
щебеню rн.щ.=mщ/vщ=2860:2=1430 кг/м3.
Порожнистість
щебеню П=(1–rн.щ/rщ).100=(1–1430/2700).100=47 %
1.2.
Гідрофізичні властивості
11. Маса сухого
матеріалу m=90,9 кг. При зволоженні матеріалу до деякої початкової
вологості маса його зросла до mв=100 кг. Якою повинна бути маса
матеріалу при зволоженні його до w=20%?
Знаходимо
початкову вологість матеріалу:
.
Масу матеріалу mw
при w=20% знайдемо з виразу вологості:
.
12. Сорбційна
вологість ніздрюватого бетону змінюється зі зміною відносної вологи повітря.
При середній густині ніздрюватого бетону в сухому стані rо.с.=500 кг/м3
сорбційна волога бетону по об’єму при відносній вологості повітря 40% складає wo=1,4%;
80% – 2,9 і 100% – 9,4%. Знайти середню густину ніздрюватого бетону при різній
відносній вологості повітря.
Для переводу
вологості матеріалів по об’єму (wo) до вологості по масі (wm)
використовують формулу:
.
При відносній
вологості повітря 40 % –
; 80% – ; 100% – .
Середня густина
ніздрюватого бетону при відносній вологості повітря:
40% – ;
80% – ;
100% – .
13.
Повітряно–суха деревина при вологості w = 20% має середню густину rо.w.=670 кг/м3.
При насиченні її під тиском середня густина збільшилась до rо.w.=1300 кг/м3.
Визначити відкриту пористість деревини.
Маса 1 м3
абсолютно сухої деревини:
.
Кількість
поглинутої води mв=rо.w.–rо=1300–536=764 кг, або vв=0,764 м3.
Об’єм води,
поглинутої під тиском, відповідає об’єму відкритих пор в деревині.
Відкрита
пористість деревини П=vв×100=0,764×100=76%.
14.
Водопоглинання бетону по масі і об’єму дорівнює відповідно wm=4,2%;
wo=9,5%. Знайти загальну пористість бетону при його дійсній густині r=2,7 г/см3.
Середня густина
бетону rо=wo/wm=9,5/4,2=2,26 г/см3,
або rо=2260 кг/м3.
Загальна
пористість бетону:
.
15. Маса зразка
каменю з дійною густиною r=2,5 г/см3 в сухому стані
m=100 г. Після водонасичення маса склала mн=110 г і
об’ємне водопоглинання – wo=20%. Визначити пористість каменя.
Водопоглинання по
масі:
.
Середня густина
каменя rо=wo/wm=20/10=2, що відповідає rо=2 г/см3, або rо=2000 кг/м3.
Пористість каменя
П=(1–ro/r).100=(1–2/2.5).100=20%.
16. Визначити
коефіцієнт насичення пор цегли розмірами 250´120´65 мм з дійсною густиною r=2,6 г/см3 і
масою в сухому стані m=3,5 кг, якщо після витримування у воді маса цегли
стала рівною mв=4 кг.
Коефіцієнт
насичення kн рівний відношенню водопоглинання по об’єму до
пористості матеріалу.
Водопоглинання
цегли по масі:
.
Об’єм цегли vц=25´12´0,65=1950 см3.
Середня густина
цегли rо=m/vк=3500/1950=1,8 г/см3,
або 1800 кг/м3.
Водопоглинання
цегли по об’єму wo= wm×rо=14,3×1,8=25,7%/
Загальна
пористість цегли П=(1–ro/r).100=(1–1,8/2,6).100=30,8%.
Коефіцієнт
насичення kн=wo/П=25,7/30,8=0,83.
17. Керамічна
каналізаційна труба зовнішнім діаметром Dз=460 мм, внутрішнім
діаметром Dв=400 мм і довжиною l=800 мм знаходиться на
випробуванні під гідравлічним тиском Р=0,3 МПа. За добу крізь стінки труби
просочилось vв=37 см3 води. Розрахувати коефіцієнт
фільтрації керамічної труби.
Площа внутрішньої
поверхні труби S=p×Dв×l =3,14×40×80= =10000 см3.
Товщина труби:
або d=3 см.
Коефіцієнт
фільтрації
,
або 1,54×10–5 м/год.
Примітка: При
розрахунках коефіцієнта фільтрації гідравлічний тиск Р виражається в метрах
водяного стовпчика (Р=0,3 МПа=30 м вод. ст.).
18. У
повітряно–сухому стані межа міцності вапняку Rс=9,5 МПа, а
коефіцієнт його розм'якшення kp=0,65. Визначити міцність вапняку в
насиченому водою стані.
Міцність вапняку
в насиченому водою стані Rн=k×Rc=0,65×9,5= =6,18 МПа.
19. Різниця
тисків водяних парів в середині і ззовні приміщення DPп=50 Па. Визначити
коефіцієнт паропроникності стіни загальною площею S=30 м2 і
товщиною d=51 см, через яку за t=24 год. проходить mп=54 г пари.
Коефіцієнт
паропроникності знаходимо за формулою:
.
1.3.
Теплофізичні властивості
20. Кубічний
зразок кам’яного матеріалу з розміром а=10 см має у повітряно–сухому стані
масу m=2,2 кг. Визначити орієнтовно теплопровідність і можливу назву
матеріалу.
Для орієнтовного
визначення теплопровідності по величині середньої густини можна використати
формулу В.П.Некрасова:
,
де rо – середня густина, г/см3.
Середня густина
кубічного зразка матеріалу:
rо=m/а3=2200/1000=2,2 г/см3.
Орієнтовано
теплопровідність матеріалу
Вт/(м×°С).
По довідковим
даним встановлюємо, що можливий вид матеріалу – важкий бетон.
21. Через
зовнішню стіну із цегли площиною S=25,5 м2 проходить за t=24 год.
Q=76000 кДж теплоти. Товщина стінки d=51 см, температура теплої
поверхні стіни t1=15°С, холодної – t2=–12°С. Розрахувати теплопровідність
цегляної кладки.
Теплопровідність
цегляної стіни
кДж/(м×год×°С),
або
0,65 Вт/(м×°С).
22. Теплопровідність
фіброліту із середньою густиною rо=500 кг/м3 в сухому
стані при t=25°С становить lt=0,1 Вт/(м×°С). Знайти розрахункове
значення теплопровідності: а) при t=0°С; б) при t=25°С і вологості w=20%.
Для перерахунку
теплопровідності до нульової температури використовуємо формулу:
lt=lo.(1+0,0025.t),
де lo – теплопровідність при 0°С.
Теплопровідність
фіброліту при 0°С
Вт/(м×°С).
Для врахування
впливу вологості на теплопровідність можна використати спрощену формулу:
lw=l+Dl.wо,
де lw – теплопровідність вологого
матеріалу; Dl – приріст теплопровідності на 1% об’ємної вологості, яке
складає для неорганічних матеріалів при додатній температурі 0,0023, при
від’ємній – 0,0046; для органічних відповідно 0,0035 і 0,0046; wo –
об’ємна вологість.
Об’ємна вологість
фіброліту wo=w×rо=20×0,5=10%
Теплопровідність
фіброліту lw=0,1+0,0035×10=0,13 Вт/(м×°С).
23. Необхідно
замінити теплоізоляцію із пінобетонних виробів із середньою густиною rо=500 кг/м3 і товщиною
d=100 мм на теплоізоляцію
із мінеральної вати (в набивку під сітку) марки 100. Температура поверхні, що
ізолюється t1=300°С, а поверхні ізоляції t2=25°С. Визначити товщину
теплоізоляційного шару із мінеральної вати.
Середня
температура теплоізоляційного шару
tсер.=(t1+t2)/2=(300+25)/2=167,5°С
Теплопровідність
виробів із пінобетону при rо=500 кг/м3 по
довідковим даним
lп.б.=0,13+0,0003×tсер.=0,13+0,0003×167,5=0,18 Вт/(м×°С).
Теплопровідність
мінеральної вати марки 100 по довідковим даним
lм.в.=0,047+0,00023×tсер=0,047+0,00023×167,5=0,0855 Вт/(м×°С).
Термічний опір
ізоляції із пінобетону
Rt=dп.б./lп.б.=0,1/0,18=0,56 м2×°С/Вт.
Товщина шару із
мінеральної вати за необхідним проектним термічним опором
dм.в.=Rt.×lм.в.=0,56×0,0855=0,048 м або
48 мм.
24. Яку кількість
теплоти потрібно, щоб нагріти з t2=10°С до t1=30°С стіну площею S=20 м2
і товщиною d=25 см із ніздрюватого бетону густиною rо=600 кг/м3 і деревини
такої ж густини?
Питома
теплоємність ніздрюватого бетону Сб=0,838 кДж/ /(кг×°С), деревини Сд=1,9 кДж/(кг
×°С).
Кількість
теплоти:
Q=c×m×(t1–t2),
де m – маса
матеріалу, що нагрівається.
Маса ніздрюватого
бетону, що нагрівається і деревини однакова: m=S×d×ro=20×0,25×600=3000 кг.
Кількість
теплоти, що необхідна для нагріву ніздрюватого бетону, Qб=0,838×3000×20=50280 кДж; деревини Qд=1,9×3000×20= =114000 кДж.
25. Яку кількість
теплоти, кДж, потрібно для нагріву від t2=15°С до t1=95°С газобетонної панелі
розміром 3,1´2,7´0,3 м із середньою густиною rо=850 кг/м3 і об’ємною
вологістю wo=20%?
Питома
теплоємність газобетону в сухому стані Сс=0,92 кДж/ /(кг×°С).
Вологість
газобетону по масі w=wo/ro=20/0,85=23,5%.
Питома
теплоємність газобетону у вологому стані
Сw=Cc+0,042w=0,92+0,042×23,5=1,9 кДж/(кг×°С).
Об’єм
газобетонної панелі і її маса: vп=3,1×2,7×0,3=2,5 м3; mп=vпrо=2,5×850=2125 кг.
Кількість
теплоти, що необхідна для нагріву панелі,
Q=Cw×mn×(t1–t2)=1,9×2125×(95–15)=323000 кДж.
26. Яка швидкість
розповсюдження температури в ніздрюватому бетоні і деревині з середньою
густиною rо=600 кг/м3? Теплопровідність ніздрюватого
бетону, lб=0,5 Вт/(м×°С), деревини lд=0,15 Вт/ /(м×°С), питома теплоємність
бетону Сб=0,838 кДж/(кг×°С), деревини Сд=1,9 кДж/(кг×°С).
Швидкість
розповсюдження температури (температуропровідність) ніздрюватого бетону aб=lб/(Сб×rб)=0,5×3,6/(0,838×600)=0,0036 м2/
/год., деревини aд=lд/(Сд×rо)=0,25×3,6/(1,9×600)=0,000789 м2/год.
27. Початкова
довжина зразків із сталі з різним вмістом нікелю при t1=20°С була однакова – lo=500 мм.
Якщо врахувати, що коефіцієнти лінійного теплового розширення сталі at з 20% Ni – 11,5×10–6, 30,4% Ni –
5,04×10–6
; 36,1% Ni – 0,9×10–6 град–1, якою стала довжина зразків
при t2=300°С?
Довжину стальних
зразків після нагріву l1 можна знайти із формули коефіцієнта
лінійного теплового розширення:
; l1=at×lo×(t2–t1)+lo
Для зразків із
сталі з 20% Ni l1=(11,5×5×28)×10–3+500=501,61 мм;
30,4% Ni l1=(5,04×5×28)×10–3+500=500,7 мм;
36,1% Ni l1=(0,9×5×28)×10–3+
+500=500,13 мм.
1.4. Міцнісні
властивості
28. Визначити межу
міцності на стиск: а) зразків–кубів бетону, кладочного розчину, природного
каменя; б)половини призми із цементно–піщаного розчину. Руйнуючі навантаження
F, кН: для природного каменя – 600, для бетону – 500, для деревини – 8, для
цегли – 145, для цементно–піщаного розчину – 120, для кладочного розчину – 25.
Розміри стандартних зразків і розрахункові формули при стисненні вказані в
табл. 1.4. Для природного каменя розміри зразків–кубів прийняти 15´15´15 см. Межа міцності при
стиску зразків–кубів:
бетону ;
кладочного
розчину ;
природного каменя
;
цегли ;
цементу .
29. Визначити
межу міцності на згин керамічної цегли, стандартних зразків цементно–піщаного
розчину, бетону і деревини. Руйнівне навантаження F для зразків, Н: цегли –
3460, цементно–піщаного розчину – 270, бетону – 338, деревини – 1417. Розміри
стандартних зразків і розрахункові формули наведені в табл. 1.5.
Межа міцності на
згин:
керамічної цегли ;
цементно–піщаного
розчину
;
бетону ;
деревини .
Таблиця 1.4
Зразок
|
Ескіз
|
Розрахункова формула
|
Матеріал
|
Розмір
стандартного зразка, см
|
Куб
|
|

|
Бетон |
15´15´15 |
Розчин |
7,07´7,07´7,07 |
Природний камінь |
5´5´5, 15´15´15 |
Циліндр |
|

|
Бетон |
d=15; h=30 |
Природний камінь |
d=h=5; 7; 10; 15 |
Призма |
|

|
Бетон |
a=10; 15; 20;
h=40 |
Деревина |
a=2; h=3 |
Складений |
|

|
Цегла |
a=12; b=12; h=14 |
Половина призми |
|

|
Цемент |
a=4; S=25 см2
|
30. Визначити
межу міцності при трьохосьовому розтягу стального стержня і зразка–призми із
бетону. Руйнуюче навантаження F для зразків сталі і бетону 30 кН. Розміри
стандартних зразків і розрахункові формули наведені у табл. 5. Розміри бетонної
призми 10´10´80 см.
Межа міцності на
розтяг:
сталі ;
бетону .
Таблиця 1.5
Зразок
|
Ескіз
|
Розрахункова формула
|
Матеріал
|
Розмір
стандартного зразка, см
|
Призма,
цегла
(в натурі)
|
|
При згині

|
Цемент |
4´4´16, l=10 |
Цегла |
12´6,5´25, l=20 |
Призма |
|

|
Бетон |
15´15´60, l=45 |
Деревина |
2´2´30, l=24 |
Стержень,
"вісімка",
призма
|
|
При осьовому розтязі

|
Бетон |
5´5´50, 10´10´80 |
Сталь |
d=1; l=5; l≥10d |
Циліндр |
|
При розтязі розколюванням

|
Бетон |
d=l=15 |
31. Зразок цегли
при випробовуванні зруйнувався при показі манометра Р=40 МПа. Коефіцієнт
розм'якшення цегли kц=0,9. Площа зразка So в два рази
більша площі поршня гідравлічного преса Sп. Визначити межу міцності
цегли на стиск в насиченому водою стані.
Допустиме
навантаження F=P×Sп=40×Sп
Міцність цегли в
сухому стані Rс=F/So=40×Sn/So=20 МПа.
Міцність цегли в
насиченому водою стані Rн=kр×Rс=0,9×20= =18 МПа.
32. Залізобетонна
квадратна плита розміром 4´4´0,4 м опирається по
краям на чотири цегляних стовпа перерізом 0,51´0,51 м кожний. Висота
стовпів h=6,5 м. На залізобетонну плиту по її центру поставили баддю з
бетоном. Маса бадді без бетону mб=87 кг, а об’єм бетону в бадді
vб.с.=0,85 м3. Визначити, який тиск на цегельні
стовпи на рівні їх фундаменту.
Середня густина
цегляної кладки rо.к= 750 кг/м3 ; залізобетону rо.з=2500 кг/м3;
бетонної суміші rо.б=2400 кг/м3.
Маса
залізобетонної плити mп=2500×4×4×0,4=16000 кг.
Маса бетонної
суміші mб.с.=vб.с×rо.б=0,85×2400=2040 кг.
Маса плити з
вантажем
М=mп+mб.с.+mб=16000+2040+87=18127 кг.
Навантаження на
кожний цегельний стовп
F=M/4=18127/4==4600 кг=46 кН.
Навантаження, що
створюється власною вагою цегельного стовпа,
Fц.с.=S×h×r=0,51×0,51×6,5×1750=3000 кг=30 кН,
де S – площа
перерізу цегляного стовпа.
Загальне
навантаження на фундамент кожного стовпа
F0=F+Fк.с.=46+30=76 кН.
Тиск , що
здійснюється на цегельні стовпи на рівні фундаменту,
P=Fo/S=76×103/(0,51×0,51)=304×103 Н/м2=0,3 МПа
33. Протягом
7 діб два рази за зміну при 2–змінній роботі відбирали проби бетонної
суміші на марку 200. Результати досліджень наведені нижче:
№п/п
|
Ri, МПа
|
№п/п
|
Rі, МПа
|
1 |
22,5 |
8 |
22,2 |
2 |
22,7 |
9 |
21,3 |
3 |
21,5 |
10 |
20,8 |
4 |
20,8 |
11 |
21,7 |
5 |
22,1 |
12 |
21,9 |
6 |
20,9 |
13 |
20,4 |
7 |
21,8 |
14 |
28,3 |
Визначити середнє
квадратичне відхилення і коефіцієнт варіації міцності.
Коефіцієнт
варіації (мінливості) міцності бетону є критерієм його однорідності. Його вираховують
за формулою:
,
де s – середнє
квадратичне відхилення окремих результатів досліджень від середньої міцності:
,
– середня міцність бетону,
що дорівнює середньому арифметичному межі міцності окремих зразків Ri:
.
Середнє
квадратичне відхилення
.
Коефіцієнт
варіації міцності бетону cv=1,92/22,06×100»9%.
34. Знайти
коефіцієнт конструктивної якості ряду матеріалів, значення меж міцності яких на
стиск R і середньої густини rо наведені нижче:
Матеріал
|
R, МПа
|
rо, кг/м3
|
Граніт |
150 |
2700 |
Вапняк |
60 |
1800 |
Важкий бетон |
60 |
2300 |
Легкий бетон |
20 |
1200 |
Цегла керамічна |
15 |
1800 |
Сосна (вздовж волокон) |
95 |
500 |
Скло віконне |
600 |
2550 |
Сталь |
400 |
7850 |
Коефіцієнт
конструктивної якості матеріалів знаходиться як відношення межі міцності до
середньої густини. Для граніту він дорівнює 150/2700=0,056, вапняку –
60/1800=0,033, важкого бетону 60/2300= =0,026, легкого бетону 20/1200=0,017,
керамічної цегли 15/1800= =0,008, сосни 90/500=0,18, віконного скла
600/2550=0,24, сталі 400/7850=0,051.
35. Випробуванню
на стиранність підлягали зразки–куби розміром 7,07´7,07´7,07 см із граніту,
вапняку, шлакоситалу. Якою стала маса зразків після випробувань, якщо
стираність (Ст) граніту 0,04; вапняку – 0,8; шлакоситалу – 0,02 г/см3?
Середня густина граніту 2700 кг/м3, вапняку 1800 кг/м3,
шлакоситалу 2650 кг/м3?
Масу зразків
після випробувань m1=m–Ст×S,
де m – маса
зразка до стирання, г; S – площа стирання.
Маса зразків до
стирання, г: граніту – m=2,7×353,5=954,5; вапняку – m=1,8×353,5=636,3; шлакоситалу –
m=2,65×353,5=936,8.
Площа стирання
S=7,07×7,07=50 см2.
Маса зразків
після випробувань, г: граніту – m1=954,5–2=952,5; вапняку – m1=636,3–40=596,3;
шлакоситалу – m1=936,8–1=935,8.
36. Визначити
твердість по Бринеллю підшипникового сплаву, якщо при стандартному випробуванні
глибина відбитку стальної кульки діаметром d=5 мм становила h=0,1 мм.
Число твердості
по Бринеллю НВ визначається як тиск, який припадає на одиницю площі сферичної
поверхні відбитку.
Площу сферичної
поверхні відбитку знаходимо за формулою
S=p×d×h=3,14×5×0,1×10–6=1,57×10–6 м2.
Між навантаженням
F, H і діаметром шарика, мм, існує певна залежність. Так, як для чорних металів
F=300×d2,
для міді, бронзи і латуні F=100×d2 , алюмінію і
підшипникових сплавів F=25×d2 .
Навантаження на
шарик F=25×25=625 Н;
Число твердості
НВ=F/S=625×106/1,57=398 МПа.
37. Зразок
природного каменя у вигляді циліндра діаметром D=40 мм і висотою h=65 мм
випробовується на удар під лабораторним копром. Вага падаючої баби
F=20 Н.Руйнування каменя відбулося при 12–м ударі баби. Розрахувати
міцність каменя при ударі.
Міцність
матеріалу при ударі розцінюється роботою руйнування, віднесеною до одиниці
об’єму зразка.
Об’єм циліндра:

Робота руйнування
дорівнює добутку ваги баби на шлях при падінні. При цьому останній удар до
уваги не береться:
А=20(1+2+3+…+11)=13,2 Н×м.
Міцність
природного каменя при ударі:
Ry
=А/v=13,2×106/81=0,163 МПа.
1.5.
Деформативні властивості
38. Зразки–призми
перерізом 40´40 мм і довжиною lo=160 мм із цементного
тіста, містить 45 і 75% заповнювача, по мірі тверднення відбулася усадка. Вона
склала при видаленні 10, 20 і 30% води для зразків із цементного тіста
відповідно 1×10–3, 2×10–3 і 2,8×10–3; зразків із
вмістом 45% заповнювача: 0,3×10–3, 0,55×10–3 і 1×10–3; зразків з
вмістом 75% заповнювача: 0,05×10–3, 0,07×10–3 і 0,15×10–3. Знайти зміну
довжини зразків, мкм, по мірі висихання.
Для розрахунку
зміни довжини зразків Dl по мірі висихання використовуємо розрахункову формулу для
визначення лінійної деформації eус. При усадці:
Dl=l1–lo=eус×lo.
При видаленні 10,
20 і 30% води Dl зразків із цементного тіста повинно відповідно скласти: Dl1=160×103×1×10–3=160 мкм;
Dl2=160×103×2× ×10–3=320 мкм;
Dl3=160×103×2,8×10–3 =
448 мкм.
Аналогічно
отримаємо для зразків із вмістом 45% заповнювача: Dl1=480 мкм, Dl2=93,5 мкм, Dl3=160 мкм;
для зразків із вмістом 75% заповнювача: Dl1=8 мкм, Dl2=11,2 мкм, Dl3=24 мкм.
39. Який діаметр
повинен мати стальний стержень довжиною lo.=2,5 м, якщо
потрібно утримувати вантаж m=6 т (F=60 кН). Розрахувати абсолютне
граничне видовження стержня Dl. Допустима напруга на розтяг для сталі s =160 МПа, модуль
пружності Е=2×105 МПа.
Із виразу для
напруги знайдемо площу перерізу S, а потім і діаметр стержня d:
;
.
Подовження
стального стержня можна знайти із закону Гука
Е=s/e, де s =F/S, а e =Dl/l.
Абсолютне
видовження стального стержня
.
40. Порівняти
значення початкового модуля пружності важкого і легкого бетонів з межею
міцності при стиску Rст.=25 МПа. Середня густина легкого бетону
rо=1200 кг/м3 .
Початковий
(миттєвий) модуль пружності бетону Еб відповідає навантаженню бетону
до таких напруг, при яких виникають тільки пружні деформації.
Його можна
вирахувати з достатньою точністю по емпіричним формулам:
для важкого
бетону ;
для бетону на
пористому заповнювачі .
Можна застосувати
до умов задачі:
для важкого
бетону МПа;
для легкого
бетону МПа.
41. Розрахувати
модуль пружності листового скла наступного хімічного складу,
%: SiO2
– 71,8, Na2O – 14,9, CaO – 7, MgO – 4,1, Al2O3
–2,2.
При розрахунку
застосувати правило адитивності. Коефіцієнти для розрахунку модуля пружності:
SiO2 –
700, Na2O – 610, CaO – 700, MgO – 400, Al2 O3
–1800.
У відповідності з
правилом адитивності модуль пружності скла може бути розрахований по емпіричним
формулам
Е=700×71,8+1800´ ´2,2+700×7+400×4,1+61×14,9=61669 МПа.
42. Зразки–призми
із литого бетону розміром 7´7´21 см ізолювали парафіном і
при напрузі s = 2,5 МПа визначали повні деформації eп. Паралельно встановлювали на
ненавантажених зразках до заданого строку тверднення усадочні деформації eус.. Визначити деформації
повзучості бетону у віці 2, 6, 12 і 18 місяців, якщо повні деформації бетону у
вказаному віці складали відповідно 0,1;0,5;0,7 і 0,8 мм/м, а усадочні
деформації 0,1;0,28;0,35 і 0,36 мм/м. Результати вишукувань показати графічно.
Деформації
повзучості визначають за виразами eпз = eп – eус.
Графіки за
результатами дослідів і вишукувань приведені на рис.1.4.
43. Розрахувати міру повзучості бетонів з межею
міцності на стиск Rст у 28 добовий вік 40,23 і 25 МПа і витратою
води В відповідно 245,225 і 160 кг/м3 (бетони№1,2 і 3).
Для орієнтованого
розрахунку міри повзучості бетону Сm, МПа–1,
застосовують різні емпіричні формули. У даному випадку зручніше було б використати
формулу:
Сm×106=16В/Rст.
Міра повзучості
бетону №1 Сm×106 =16·245/40=98 МПа–1;
бетону №2 Сm×106=16·225/23=150
МПа–1;
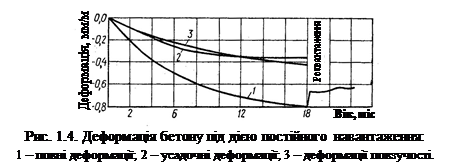
бетону №3 Сm×106=16·160/25=80
МПа–1;
44. Визначити
кінцевий показ на манометрі преса, якщо після
розвантаженні
зразка деформація залишалась незмінною, початкова напруга складала s =30 МПа і пройшов час,
що відповідав часу релаксації (часу, протягом якого напруга знижується в е
разів, тобто в 2,72 рази). Кінцевий показ манометра після розвантаження
зразка склав s1=s/е=30/2,72=11,02 МПа.
45. Для
збільшення довжини зразка полімерної плівки з 100 до 250 мм було
прикладена напруга sо=5,5 МПа. Після витримки плівки в цьому положенні
протягом t =30 діб напруга знизилась до s =3,1 МПа.
Визначити постійну часу релаксації і діючу напругу після витримки протягом t1 =80 діб.
Релаксація напруг
слідує експоненціальному закону:

де s – напруга через час t; sо – початкова напруга; lр – постійна часу релаксації.
Постійну lр можна знайти із виразу:
lns/sо=–t/lр.
ln(3,1/5,5)=–30/lр, звідки lр=52,6 діб.
Напруга після
витримування протягом 80 діб повинна бути:
s80=5,5·е–80/52,6=5,5·е–1,52=1,20 МПа.
2. Природні
кам’яні і керамічні матеріали
46. Для визначення
придатності вапняку при отриманні стінового каменя були визначені середня
густина, водопоглинання, морозостійкість і коефіцієнт розм'якшення зразків.
Отримані наступні усереднені дані.
Шматок каменя
масою m = 207 г виштовхнув із об’ємоміру vв=111 г води. Після
витримки каменя у воді об’ємне водопоглинання склало wо=50%. Межа
міцності на стиск в сухому стані Rс=27 МПа, після насиченні у
воді Rн=21 МПа, після заморожування і відтавання Rмрз=18 МПа.
Чи відповідає фізично – механічним умовам випробувана гірська порода ГОСТ
4001–84 “Камни стеновые из горных пород”?
Можна вважати, що
об’єм вапняку дорівнює об’єму витісненої ним води. Тоді середня густина
вапняку:
rо=m/vв=207/111=1,86 г/см3=1860 кг/м3.
(У тому випадку,
якщо припустити, що вапняк поглинув деяку кількість води, середня густина його
повинна бути трохи менше).
Знаючи величину
об’ємного водопоглинання, можна знайти водопоглинання вапняку по масі : w=wо/rо=50/1,86=26,88%
Коефіцієнт
розм'якшення каменя kр=Rн/Rс=21/27=0,78.
Втрата міцності
на стиск після випробування на морозостійкість
DRмрз=Rн–Rмрз/Rн=21–18/21·100=14,2%.
Порівнюючи
отримані дані з вимогами ГОСТ 4001–84 “Камни стеновые из горных пород”, можна
заключити, що по всім фізико–механічним показникам досліджувана порода
задовільняє необхідним вимогам.
47. Осадові
гірські породи мають наступний хімічний склад, %:
|
SiO2
|
Al2O3
|
MgO
|
CaO
|
№1 |
88,5 |
4,9 |
2,5 |
4,1 |
№2 |
62,5 |
17,4 |
12,5 |
7,6 |
№3 |
5,19 |
0,95 |
24,5 |
69,36 |
Яка хімічна
стійкість порід до кислот і лугів?
Для приближеного
висновку про хімічну стійкість гірських порід в кислих і лужних середовищах
використаємо оцінку модуля основності Мо:
.
Гірські породи
мають наступні значення Мо: №1 – 0,07; №2 – 0,25; №3 – 15,3. Можна
припустити, що породи №1 і №2 стійкі до кислот, але взаємодіють із основними
оксидами. Гірська порода №3 повинна легко руйнуватися кислотами, але бути
стійкою до лугів.
48. При
випробуванні на копрі Педжа шляхом послідовних ударів гирею масою mг=2 кг
з інтервалами по висоті Dh=1 см при початковій висоті hн=1 см
був доведений до руйнування через n=15 ударів зразок граніту у вигляді паралелепіпеда
розміром 2´2´5 см.
Яка питома робота
при ударному розколюванні зразка граніту?
Питому робота при
ударному розколюванні гірських порід знаходимо за формулою:
,
де Fг
– зусилля створене гирею (Fг=20 Н); S – площа розколу
(S=4 см3).
.
49. Хімічний
аналіз карбонатної гірської породи показав, що в ній присутні 40% СаО, 12% MgO.
Визначити вміст в породі доломіту, кальциту.
Встановити її
назву, використавши класифікацію наведену в табл. 2.1.
Таблиця 2.1
Порода
|
Склад, %
|
СаСО3– кальцит
|
СаMg(СаО3)2–доломіт
|
Вапняк |
95–100 |
5–0 |
Доломітистий вапняк |
75–95 |
5–25 |
Доломітовий вапняк |
50–75 |
25–50 |
Вапняковий доломіт |
25–50 |
25–50 |
Вапняковистий доломіт |
5–25 |
75–95 |
Доломіт |
0–5 |
95–100 |
Припустимо, що
вся кількість MgO в карбонатній породі зв’язано в доломіт – СаMg(СаО3)2.
Із молекулярної маси доломіту
М СаMg(СО3)2=184
можна підрахувати, що на долю MgO приходиться 21,7%. В породі міститься 12%
MgO, тобто доломіту повинно бути 55,3%. Не важко підрахувати, що в 100%
доломіту зв’язується 30,4% СаО, відповідно, в 55,3% повинно зв’язуватись 16,8%
СаО. Залишкова кількість СаО, тобто 23,2%, зв’язано в кальциті СаСО3.
Із формули кальциту слідує, що в 100% СаСО3 знаходиться 56% СаО.
23,2% СаО повинно йти на утворення 41,4 % СаСО3. Таким чином, в
дослідженій гірській породі знаходиться 41,4% СаСО3 і 55,3% СаMg(СО3)2.
По табл. 2.1 її можна віднести до вапнякового доломіту.
50. Визначити по
масі і об’єму витрату глини, що необхідна для виготовлення 10000 шт. потовщеної
цегли із середньою густиною rок=1400 кг/м3, об’ємом
порожнин vп=30%, якщо середня густина сирої глини rог=1600 кг/м3,
вологість w=15%. При випалі сирцю в печі втрати при прокалюванні (в.п.п.)складають
10% від маси сухої глини.
Об’єм одної
цегли:
без врахування
порожнин (брутто) v`к=0,25×0,12×0,088=0,00264 м3;
з урахуванням
порожнин (нетто) vк=v`к–vп/100=0,00264–0,00264× ·0,3=0,0018 м3.
Об’єм
10000 шт. цеглин vп=vк×n=0,0018×10000=18 м3.
Маса
10000 шт. потовщеної цегли mп=vп×rок=18×1400=25200 кг.
Маса сухої
непрокаленої глини, що необхідна на 10000 шт. цегли,
.
Маса сирої глини,
необхідної на 10000 шт. цегли,

Об’єм необхідної
глини vг=mг/rог=31878:1600=19,92 м3.
51. Скільки штук
керамічних каменів розміром 250´120´138 мм з порожнинністю
П=33% можна виготовити із 15 т глини з вологістю w=12%, втратами при
прокалюванні в.п.п.=8,5%. Середня густина звичайної цегли з цієї глини rо=1750 кг/м3.
З 15 т глини
з вологістю 12% можна отримати прокалену спечену керамічну масу:
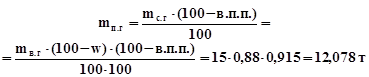
Об’єм прокаленої
спеченої керамічної маси
vп.г=mп.г/rо=12078:1750=6,9 м3.
Об’єм одного
керамічного каменя без врахування пустот
v`к=0,25×0,12×0,138=0,0041 м3.
Об’єм одного
керамічного каменя з врахуванням пустот:
vк=v`к–`
(v`к П)/100=0,0041–0,0013=0,0028 м3.
Можлива кількість
керамічних каменів із 15 т глини
n=vп.г./vк=6,9:0,0028=2464 шт.
52. Визначити
витрату деревних стружок для отримання n=1000 шт. пористої цегли із
середньою густиною rо=1210 кг/м3 , якщо середня густина звичайної
цегли rо=1740 кг/м3 .
середня густина стружки rо=610 кг/м3.
Маса
1000 шт. звичайної цегли
mз.ц=1000×0,25×0,12×0,065×1740=3393 кг.
Маса
1000 шт. пористої цегли
mп.ц.=1000×0,25×0,12×0,065×1210=2359 кг.
Об’єм пустот, що
створені стружкою в керамічній масі:
vп=(mз.ц–mп.ц.)/rо=(3393–2359)/1740=0,59 м3.
Необхідна витрата
стружки по масі
mо.п=vп×rоп=0,59×610=360 кг.
53. При
випробуванні п’яти зразків повнотілої цегли пластичного формування були отримані
наступні результати:
Межа міцності на стиск, МПа
|
Межа міцності на згин, МПа
|
16,5 |
3,3 |
15,6 |
3,0 |
14,3 |
2,8 |
16,2 |
3,2 |
12,6 |
1,7 |
До якої марки
можна віднести випробувану цеглу?
Знаходимо середнє
і найменше значення межі міцності на стиск
( , min) і згин ( , min,)
випробуваної
цегли:
=15,04 МПа; мін=12,6 МПа;
=2,8 МПа; мін=1,7 МПа.
У відповідності з
ДСТУ БВ.2.7–61–97 цегла має марку 150. По ГОСТу для цегли марки 150 середня для
5 зразків значення межі міцності на стиск і згин повнотілої цегли пластичного
формування повинна бути не менше відповідно 15 і 2,8 МПа.
Найменше для
окремого зразка значення Rст. мін і Rзг. мін повинно бути
не менше відповідно 12,5 МПа і 1,4 МПа.
54. При
виробництві керамзиту використана глина, що має середню густину rог=2550 кг/м3 при
вологості w=13,5%.
Керамзитовий
гравій має середню насипну густину rн.к.=450 кг/м3,
міжзернову пустотність П=44%. Розрахувати, в скільки раз збільшиться об’єм
глини при спученні, якщо маса глини і керамзиту однакова.
Середня густина
сухої глини:
r’о.г.=rо.г/(1+w/100)=2550/(1+0,135)=2246 кг/
м3.
Середня густина
керамзиту в грудці:
rо.к.=rн.к./(1–П/100)=450/(1–0,44)=804 кг/ м3.
Збільшення об'єму
глини при вспученні еквівалентно зменшенню її середньої густини:
.
3. Мінеральні
в’яжучі речовини
55. Визначити
вихід будівельного гіпсу і ангідритового в’яжучого із 1 т гіпсового каменя
3–го сорту, вологістю 7%, що містить 80% СаSO4×2H2O. В склад
домішок входять 7% глини, 9% піску, 4% органічних включень.
Маса сухого
гіпсового каменя mг.к.=1000×0,93=930 кг.
В хімічному
процесі отримання в’яжучих буде приймати участь маса двоводного гіпсу: mг.=930–0,2×930=744 кг.
Реакції отримання
будівельного гіпсу і ангідритового в’яжучого:
СаSO4×2H2O=СаSO4×0,5H2O+1,5H2O;
СаSO4×2H2O=СаSO4+2H2O.
Кількість напівгідрату
і ангідриту в будівельному в’яжучому, отриманому із 744 кг гіпсу, знайдемо
із пропорцій:
172 кг СаSO4×2H2O – 145 кг СаSO4
× 0,5H2O
744 кг СаSO4×2H2O – Х кг СаSO4
× 0,5H2O
ХСаSO4×0,5H2O=(744×145)/172=627 кг;
172 кг СаSO4×2H2O – 136 кг СаSO4
744 кг СаSO4×2H2O – Х кг СаSO4
ХСаSO4=(744×136)/172=588 кг
У в’яжуче
перейдуть домішки у кількості 16% від маси сухого гіпсового каменя (органічні
домішки повинні вигоріти), тобто 158 кг.
Таким чином, із
1 т гіпсового каменя повинно вийти: будівельного гіпсу – mб.г.=627+158=785 кг
або ангідритового в’яжучого mа.в.=88+158=746 кг.
56. Для отримання
1 моля напівводного гіпсу із двогідрату теоретично потрібно затратити
q=84 кДж теплоти, а 1 моля вапна із карбонату кальцію q1=190 кДж.
Яка витрата умовного палива необхідна для отримання 1 т СаSO4×0,5H2O і СаО?
Мольна маса СаSO4×0,5H2O рівна
145 г/моль. Значить, для отримання 1 т напівводного гіпсу потрібно:
Q=(q×1000)/0,145=(84×1000)/0,145=579310 кДж.
1 т умовного
палива еквівалентна 29330 кДж теплоти. Значить, для отримання 1 т
напівводного гіпсу необхідна витрата палива
Т=579310/29330=19,75 кг.
Для отримання
1 т СаО необхідно
Т1=(190×1000)/(0,056×29330)=115,7 кг.
57. Визначити
пористість затверділого будівельного гіпсу, якщо водогіпсового
відношення В/Г=0,7. Дійсна густина rг=2,7 г/см3.
Перший спосіб
рішення. Для
визначення пористості затверділого будівельного гіпсу визначимо його дійсну і
середню густину.
Дійсна густина
затверділого гіпсу r=mг.з /va, де mг.з – сумарна
маса гіпсу і хімічно зв’язаної води в одиниці абсолютного об'єму va.
Склад хімічно
зв’язаної води Вх.зв. легко знайти із рівняння гідратації основного
компонента будівельного гіпсу
H2O:СаSO4×0,5H2O+1,5H2O=СаSO4×2H2O.
Вх.зв.=(27×100)/145=18,6%.
Припустимо, що
густина хімічно зв’язаної води rв=1, тоді
.
Середня густина
затверділого гіпсу rо=mг.з/v, де v – об’єм з урахуванням пор, утворених
надлишковою породою.
.
Пористість
затверділого гіпсу:
Пз.г.=(1–rо/r)·100=(1–1,1/2,13)·100=48%
Другий спосіб
рішення
більш простіший:
.
58. Скільки
вапнякового тіста ( по масі і об’єму), із вологістю wт=50% можна
отримати із mв=15 т негашеного вапна із активністю А=85%.
Середня густина вапняного тіста rт=1400 кг/м3.
Склад активного
СаО в 15 т негашеного вапна
СаОакт.=(А×mв)/100=(85×15)/100=12,75 т.
Гашення вапна
проходить за рівнянням СаО+Н2О=Са(ОН)2.
Із 56 масових
частинок СаО можна отримати 74 частини сухого гідратного вапна, а із
12,75 т СаО
mСа(ОН)2=(12,75×74)/56=16,84 т.
Можлива кількість
вапнякового тіста:
по масі 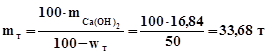
по об’єму .
59. Яку кількість
гідратного вапна і води міститься у вапняному тісті масою mт=10 т
із середньою густиною rт=1400 кг/м3? Дійсна густина порошкоподібного
гідратного вапна rп=2,05 г/см3.
1 м3
вапняного тіста можна уявити через суму об’ємів гідратного вапняку і води,
тобто mп/rп+mв/rв=1, де mп і mв
– маса відповідно сухого гідратного вапна (пушонки) і води; rв – густина води.
.
Звідси вміст в
1 м3 вапняного тіста гідратного вапна mп==0,781 т
(55%); води mв=1,4–0,781=0,619 т (45%).
В 10 т
вапняного тіста міститься гідратного вапна
m`п=(0,781×10/1,4=5,58 т, води m`в=4,42 т.
Вміст гідратного
вапна у вапняному тісті, як і інших речовин в тістоподібних масах, можна також
визначити за формулою:
,
де Т – вміст
твердої речовини в тісті, кг/м3; rп – дійсна густина твердої речовини, що
утворює з водою тістоподібну масу, г/см3; rо – середня густина тіста, кг/м3.
60. Розрахувати
активність вапна, отриманого із крейди, що містить 42,5% СаО; 3,5% MgO;17,5%
SiO2+Al2O3, при втратах при прокалюванні
в.п.п.=36,5%. Ступінь декарбонізації крейди при випалі х=0,9.
Для розрахунку
активності вапна А можна використати формулу А.В. Волженського, виведену в
припущенні, що залишок у випаленому матеріалі СО2 зв’язаний тільки з
оксидом калію:
,
де R2O3
– сумарний вміст у сировині Al2O3 + Fe2O3,
%.

61. Для
визначення складу напівводного гіпсу у будівельному гіпсі наважку подрібненого
гіпсу mг=2,5 г, попередньо висушену до постійної маси, залили
водою. Затверділий матеріал висушили при 50 – 55оС до постійної
маси, яка стала яка стала mг.з.=2,84 г. Який вміст в
будівельному гіпсі СаSO4×0,5H2O?
Із реакції СаSO4×0,5H2O+1,5H2O=СаSO4×2H2O можна
заключити, що для гідратації 145 г СаSO4×0,5H2O потрібно
27 г води. У нашому випадку, для гідратації х г напівводного гіпсу
потрібно mг.з.–mг. г води.

62. При
визначенні вмісту у негашеному кальцієвому вапні активних СаО+MgO на титрування
m=1,2 г вапна використано v=37,5 мл 1 н розчину НСl. До якого
сорту по вмісту активних СаО і MgO належить вапно?
З реакції
нейтралізації, що відбувається при титруванні (СаО+2НС1=СаС12+Н2О),
витікає, що 1 мл 1 н розчину соляної кислоти відповідає 0,028 г
СаО.
Можна скласти
відношення:
0,028 г СаО – 1
мл НС1
m г СаО – v
мл НС1
Звідки,
СаО=(0,028·v/m)·100=87,5%.
Для кальцієвого
вапна вміст MgO – не більше 5%. Можна вважати, що у дослідженому вапні вміст
активних СаО+MgO=87%. Це відповідає по ДСТУ В.2.7–90–99 нормам для негашеного
вапна 2–го сорту.
63. Хімічний
склад цементного клінкера, %: СаО–65,5; SiO2 – 22,2; Al2O3
– 6,4; Fe2O3 – 3,1; MgO – 1,5; SO3 – 0,4; Na2O
– 0,9. Визначити вміст у клінкері трьохкальцієвого силікату С3S,
двокальцієвого силікату С2S, трьохкальцієвого алюмінату С3А,
чотирьохкальцієвого алюмофериту С4АF, а також сульфату кальцію СаSO4.
Встановити по табл. 3.1, до якого виду відноситься клінкер.
Таблиця 3.1
Клінкер
|
Приблизний вміст, %
|
С3S
|
С2S
|
С3А
|
С4АF
|
Алітовий |
Більше 60 |
Менше 15 |
— |
— |
Нормальний(по вмісту аліту) |
60 – 37,5 |
15 – 37,5 |
— |
— |
Белітовий |
Менше 37,5 |
Більше 37,5 |
— |
— |
Алюмінатний |
— |
— |
Більше 15 |
Менше 10 |
Нормальний(за вмістом алюмінату) |
— |
— |
15 – 7 |
10 – 18 |
целітовий |
— |
— |
Менше 7 |
Більше 18 |
Мінералогічний
склад цементних клінкерів, %, можна визначити за формулами, запропонованими
В.А.Кіндом:
С3S=3,8·SiO2(3КН–2)
С2S=8,6·SiO2(1–КН)
де КН – коефіцієнт
насичення, що показує відношення кількості оксиду кальцію в клінкері, фактично
зв’язаного з кремнеземом. До кількості його, теоретично необхідному для повного
зв’язування кремнезему в трьохкальцієвий силікат. Коефіцієнт насичення
вираховують по спрощеній формулі:
.
Формули для
розрахунку С3А і С4АF вибираються в залежності від
значення глиноземистого модуля ГМ, рівного відношенню процентного вмісту Al2O3 і Fe2O3.
При ГМ>0,64: С3А=2,65·(Al2O3–0,64·Fe2O3);
С4АF=3,04·Fe2O3.
При ГМ<0,64: С3А=1,7·(Al2O3–1,57·Fe2O3);
С4АF=4,77·Al2O3.
Вміст сульфату
кальцію визначають за формулою
СаSO4=4,77·SO3.
За допомогою
наведених вище формул розрахуємо мінералогічний склад клінкера по даним
хімічного аналізу.
,
ГМ=6,4:3,1=2,06;
С3S=3,8×22,2·(3×0,87–2)=51,4%;
С2S=8,6×22,2·(1 – 0,87)=24,8%;
С3А=2,65·(6,4–0,64×3,1)=11,7%;
С4АF=3,04×3,1=9,42%;
СаSO4=1,7×0,4=0,68%.
По класифікації,
наведеній в табл. 3.1, клінкер можна віднести до нормальних.
64. В якій
пропорції потрібно взяти вапняк і глину, щоб отримати цементний клінкер з
коефіцієнтом насичення КН=0,88? Хімічний склад вапняку і глини, %, наведений нижче:
|
SiO2
|
Al2O3
|
Fe2O3
|
СаО
|
MgO
|
SO3
|
В.п.п.
|
вапняк |
7,80 |
1,65 |
1,04 |
48,8 |
0,91 |
– |
39,80 |
глина |
64,55 |
16,51 |
8,17 |
1,90 |
0,89 |
0,79 |
7,09 |
Визначимо
співвідношення глини до вапняку 1:х. Тоді вираз для КН прийме наступний вираз:
.
Звідки х»7 частин по масі вапняку.
Сировинна суміш буде складатися на 87,6% із вапна і на 12,4% із глини.
65. Яку кількість
Са(ОН)2 виділиться при повній гідратації 1 кг портландцементу,
що містить 95% клінкера і 5% гіпсу? Вміст основних мінералів в клінкері, %: С3S
– 57, С2S – 22, С3А – 7, С4АF – 11. Яку
кількість добавки трепелу із вмістом SiO2=72% необхідно для повного
зв’язування виділеного Са(ОН)2?
Виділення
гідроксиду кальцію йде в основному в результаті гідролізу при гідратації С3S.
Найбільш ймовірна при звичайних умовах схема гідратації С3S:
2·(3СаО×SiO2)+6Н2О=3СаО×2SiO2×2Н2О+3Са(ОН)2.
Кількість Са(ОН)2,
який виділяється при гідратації можна знайти із пропорції:
456 г 3СаО×SiO2 – 222 г Са(ОН)2.
0,95×0,57×100 г – х г
хСа(ОН)2=264 г.
При взаємодії
Са(ОН)2 з кремнеземом трепелу можна допустити утворення
однокальцієвого гідросилікату СаО×SiO2×Н2О.
Тоді для
зв’язування 1 моля, тобто 74 г Са(ОН)2, потрібно
1 моль, тобто 60 г SiO2, а для 264 г Са(ОН)2
– х г SiO2.
хSiO2=(264×60)/74=214,05 г.
Для повного
зв’язування Са(ОН)2, який виділяється при гідратації 1 кг цементу
необхідно 214,05:0,72=297 г трепелу. 66. Потрібно, щоб теплота гідратації
цементу для зведення бетонної греблі в трьохдобовий вік була не більше
210 кДж/кг, в семидобовий період 251 кДж/кг. Розрахувати орієнтовно
теплоту гідратації цементу в 3 і 7 добовий вік при наступному вмісті мінералів,
%: С3S – 47,5; С2S – 21,4; С3А – 7,8; С4АF
– 14,5. Чи може бути застосований цей цемент для зведення бетонної греблі? Теплота
гідратації цементу qп, Дж/кг, при орієнтованому підрахунку може бути
визначена за формулою:
qn=anC3S+bnC2S+cnC3A+dnC4AF,
де an,
bn, cn, dn – коефіцієнти тепловиділення
мінералів, визначенні по табл. 3.2.
Таблиця 3.2
Тривалість тверднення, діб.
|
an
|
bn
|
cn
|
dn
|
3 |
3,89 |
0,666 |
6,36 |
– 0,499 |
7 |
4,57 |
0,967 |
8,67 |
– 1,73 |
28 |
4,78 |
0,641 |
9,63 |
0,59 |
q3=3,89×47,5+0,666×21,4+6,36×7,8–0,499×14,5=178,9 кДж/кг;
q7=4,57×47,5+0,967×21,4+8,67×7,8–1,78×14,5=280,28 кДж/кг.
Результати
розрахунку підказують, що тепловиділення цементу у семидобовий вік виходить за
установлені межі. Кінцеве значення про надійність цементу може бути дано після
експериментального вивчення його теплоти гідратації.
4. Бетони і розчини
67. На завод залізобетонних виробів поступили два види піску –
дрібнозернистий річний(№1) і крупнозернистий гірський(№2).Як видно з рис. 4.1.,
обидва піски за зерновим складом не задовільняють вимоги ДСТУ БВ.2.7–32–95.
Дійсна густина піску №1 r1=2,62 г/см3
насипна rн1=1150 кг/м3,
піску №2 – відповідно r2=2,65 г/см3
і rн2=1450 кг/м3.
Визначення водопотреби пісків при нормальній густині цементного тіста
(В/Ц)т=0,245 показало, що при однаковому розпливі конуса, який дорівнює
170 мм, водоцементне відношення розчину(В/Ц)р складу 1:2 на
піску №1 складає 0,48, №2 – 0,36. Визначити
модуль крупності, питому поверхню, водопотребу і пустотність пісків.
Встановити, в якому відношенні потрібно змішати піски №1 і №2, щоб змішаний
пісок (№3) задовольняв вимогам ДСТУ БВ.2.7–32–95 до зернового складу пісків для
бетонів напірних залізобетонних труб. Модуль крупності піску знаходять як
кратне від ділення на 100 суми повних залишків на ситах. За рис. 4.1. можна
підрахувати, додаючи повні залишки на ситах з розмірами отворів 2,5; 1,25;
0,63; 0,315 і 0,14 мм ,що для піску №1:
Мк=0+5+17+28+85/100=1,35; піску N 2:Мк=32+60+85+95+100/100=3,7
Питому поверхню піску, м2/кг, можна підрахувати за формулою
А.С.Ладинського
,
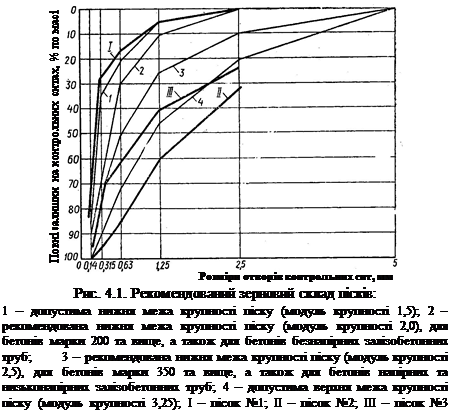
де
k – поправочний коефіцієнт, який залежить від виду піску; для гірського піску
k=2, для річних і морських пісків середньої крупності k=1,65, для дрібних
морських і річних пісків k=1,3; а, б, в, г, д, е – кратні залишки на ситах з
розмірами отворів від 5 до 0,14 мм; ж –прохід через сито 0,14 мм.
Кратні залишки легко знайти за відмінністю повних залишків на ситах.
Для піску №1
,
Для піску №2
,
Водопотребу піску, яку визначають за методом Б.Г.Скрамтаєва і
Ю.М.Баженова, визначають за формулою
.
Для піску №1 
Для піску №2 
Пустотність:
піску №1 ;
піску №2 .
Щоб при змішуванні пісків №1 і №2 з повними залишками на контрольному
ситі А1 і А2 отримати пісок 3 з повним залишком А3,
треба виконати умову
100·А3=А1·x+А2·(100–x),
де x – вміст піску №1 в змішаному піску; (100–x) – вміст піску №2 в
змішаному піску.
Звідси x=(А2–А3)/(А2–А1)·100.
Щоб отримати, наприклад, на ситі з розміром отворів 0,63 мм А3=60%,
треба взяти х=(85–60)/(85–17)·100=36%.
У відповідності з приведеною вище вимогою знайдемо зерновий склад
змішаного піску при x=36%, 100–x=64% (табл. 4.1).
Таким чином, змішуванням двох пісків з незадовільним зерновим складом
вдалося отримати пісок, зерновий склад якого знаходиться в рекомендованій
області (рис. 4.1).
68.На завод залізобетонних виробів надійшов пластифікатор ЛСТ(лігносульфонати
технічні) з густиною rд=1,266 г/см3.
Витрата цементу на 1 м3 бетону Ц=350 кг, води
В=157 л. Питоме дозування добавки, встановлене дослідним шляхом, c=0,25%
маси цементу в перерахунку на суху речовину. Визначити кількість
пластифікатора, яка потрібна для приготування водяного розчину пластифікатора і
заправки ємності vp=1000 л, а також витрата його на 1 м3
бетону в тому випадку, коли розчин має: а) робочу концентрацію; б) 10%–ну
концентрацію.
Таблиця 4.1
Номера сит
|
2,5
|
1,25
|
0,63
|
0,315
|
0,14
|
Мк
|
Повні залишки, %, при х=36% |
20,48 |
40,2 |
60,52 |
70,88 |
94,6 |
2,87 |
Повні залишки піску, які рекомендовані для бетону напірних труб |
10–20 |
25–45 |
50–70 |
70–90 |
95–100 |
2,5–3,25 |
Водний розчин добавок робочої концентрації подають безпосередньо в
бетонозмішувач у вигляді розчину замішування, в якому повністю врахована
необхідна витрата води. Об’єм рідкого пластифікатора vд, необхідний
для приготування заданого об’єму робочої концентрації, знаходять за формулою
,
де Д – вміст сухої речовини добавки в 1 л, тобто концентрація
розчину.
Концентрація розчину добавки знаходиться за довідковими даними за заданою
густиною розчину. Стосовано до добавки ЛСТ(стара назва СДБ) концентрація, %,
може бути знайдена за емпіричною формулою
.
Так як в нашій задачі rд=1,266 г/см3,
Д»50%, або 0,633 кг/л.
.
Необхідна кількість добавки за масою
mд=vд·rд=8,8·1,266=11,15 кг.
Густина
розчину замішування
.
Витрата розчину замішування на 1 м3 бетону
;
mp=157,5·1,002=157,87 кг.
При застосуванні розчину добавки підвищеної концентрації його дозують
паралельно із невистаючою кількістю води або розбавляють до отримання розчину
робочої концентрації.
Густина 10%–го розчину ЛСТ
(Д1=0,104 кг/л).
Витрата 50%–го розчину ЛСТ для отримання 1000 л10%–го розчину

або mд=164,2·1,266=207,9 кг.
Витрата 10%–го розчину ЛСТ на 1 м3 бетону
,
де К – концентрація приготованого розчину, %.
,
Кількість води, якої не вистачає на замішування 1 м3 бетонної
суміші
Вн=В–vр·rд·(1–К/100)=157–8,38·1,044·(1–10/100)=149 л.
69.Визначити номінальний склад гідротехнічного бетону для надводної зони
річкової споруди марки М200 з рухливістю бетонної суміші за осадкою конуса 4–5
см. Матеріали: портландцемент з активністю Rц=45 МПа, пісок
дрібний з водопотребою Вп=9% і дійсною густиною rп=2,65 г/см3, гранітний
щебінь з найбільшою крупністю 70 мм, дійсною густиною rщ=2,6 г/с3 і насипною
густиною rн.щ=1450 кг/м3.
Для визначення складу бетону
використовуємо розрахунково–експериментальний метод Б.Г.Скрамтаєва –
Ю.М.Баженова.
Водоцементне відношення знаходимо за формулою
Rб = А·Rц·(Ц/В–0,5),
де Rб – міцність бетону; А – коефіцієнт якості, який можна
прийняти 0,55; Rц – активність цементу,
.
Найбільш допустиме В/Ц, яке забезпечує комплекс потрібних властивостей
надводного бетону, повинно бути 0,65.Для економії цементу приймаємо рішення
ввести добавку мінерального наповнювача, наприклад золу ТЕЦ (Д), з дійсною
густиною rд=2,1 г/см3.
Орієнтовну витрату води
знаходимо за графіком (рис. 4.2.), вводячи поправку на водопотребу піску і
застосування щебеню:
В=155+5·2+10=175 л/м3.
Витрата цементу із умови міцності
Ц=В:В/Ц=175:0,76=230 кг/м3.
Необхідна витрата добавки мінерального наповнювача знаходимо за формулою
,
де (В/Ц) / – водоцементне відношення із умови довговічності:
.
Загальний вміст в’яжучої речовини Ц+Д=230+39=269кг/м3.
Пустотність щебеню: Пщ=1–(rн.щ/rщ)=1–(1,45/2,6)=0,44.
В залежності від водоцементного відношення і витрати цементу за табл. 4.2
знаходимо коефіцієнт розсуву kp=1,34.Витрата щебеню і піску:
;
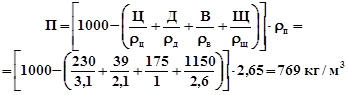
Для визначення складу бетону в частках за масою розділим витрату кожного
компонента на витрату цементу:
Ц/Ц:П/Ц:Щ/Ц:В/Ц:Д/Ц=230/230:769/230:1150/230:175/230:39/230=
=1:3,3:5:0,76:0,17.
Таблиця 4.2
Витрата цементу
|
В/Ц
|
0,4
|
0,5
|
0,6
|
0,7
|
0,8
|
250 |
— |
— |
1,26 |
1,32 |
1,38 |
300 |
— |
1,30 |
1,36 |
1,42 |
— |
350 |
1,32 |
1,38 |
1,44 |
— |
— |
400 |
1,40 |
1,46 |
— |
— |
— |
70.Визначити з допомогою номограм (рис. 4.3. – 4.5.) склад
без добавки і з добавкою СНВ бетону монолітного облицювання каналу. Рухливість
бетонної суміші ОК=4–6 см. Проектні марки бетону М300 і F200. Без добавки СНВ F200 забезпечується при марці бетону
М350.Вихідні матеріали: портландцемент середньоалюмінатний марки 400, НГ=27%, rц=3,1 г/см3; пісок
кварцовий Мк=2,8, rп=2,6 г/см3 щебінь
гранітний фракцією 5–20 мм, rщ=2,6 г/см3. Склад
бетону без застосування добавок ПАР за допомогою номографічного методу
знаходимо наступним чином. По номограмі (рис. 4.3.) для бетону М350 при осадці
конуса 4–5 см, марці цементу 400 з НГ=27% необхідно
Ц/В=2,3.Водопотреба бетонної суміші (рис. 4.4.) для щебеню з
максимальною крупністю 20 мм складає
205 кг/м3.
Витрата цементу Ц=В·Ц/В=205·2,3=472 кг/м3.
По номограмі (рис. 4.5.)
знаходимо оптимальну частку піску в суміші заповнювачів, для піску з Мк=2,8,
r =0,34.
Визначаємо витрату піску і
щебеню:
;
.
У випадку застосування добавки СНВ склад бетону знаходимо наступним
чином. За номограмою (рис. 4.6.) знаходимо (Ц/В)1=1,90. Водопотребу
знаходимо на рис. 4.4. і коректуємо з урахуванням оптимального об’єму
емульгованого повітря, встановлено емпірично.
Приймаємо
об’єм повітря vв=3%. Зниження водовмісту в бетонній суміші на
кожен процент повітря 3 л. Тоді В1=196 кг/м3.Витрата
цементу складає Ц1=В1·(Ц/В)1=196·1,9=372 кг/м3.
По номограмі (рис. 4.5.) визначаємо частку піску в суміші заповнювачів r1=0,35.
Витрати піску і щебеню:
;

71.Номінальний склад бетону 1:2,1:3,5 (за об’ємом), В/Ц=0,55, на 1 м3
бетону витрачається 310 кг цементу з насипною густиною rн.ц=1250 кг/м3.Для
виготовлення бетону застосували щебінь і пісок з вологістю w відповідно 2 і 4%
і насипною густиною rн.щ=1450 і
rн.п=1400 кг/м3
(в сухому стані).Визначити витрати матеріалів на v=200 м3
бетону за масою.
Визначаємо витрати матеріалів на 1 м3 бетону за об’ємом:
vц=Ц:rн.ц=310:1250=0,25 м3;
vп=vц·2,1=0,25·2,1=0,52 м3;
vщ=vц·3,5=0,25·3,5=0,87 м3;
.
За масою:
Ц=310 кг;
В=vв·rв=0,17·1000=170 кг;
П=vп·rп=0,52·1450=754 кг;
Щ=vщ·rщ=0,87·1400=1218 кг.
З урахуванням вологості
заповнювачів:
Цр=310 кг;
Пр=П+Пw/100=754+(754·0,04)=784 кг;
Щр=Щ+Щw/100=1218+(1218·0,02)=1242 кг;
Вр=В–Пw/100–Щw/100=170–(754·0.04)–(1218·0,02)=115 кг.
Робоча витрата матеріалів на 200 м3 бетону:
Цvр=310·200=62000 кг;
Пvр=784·200=156800 кг;
Щwр=1242·200=248400 кг;
Вvр=115·200=23000 кг.
72.Визначити коефіцієнт
виходу, середню і дійсну густину, а також пористість цементного бетону, якщо
для отримання 100 м3 бетонної суміші із В/Ц=0,7 використано mц=32
т, піску vп=45 м3 і щебеню vщ=78 м3.Насипна
густина цементу rн.ц=1300 кг/м3, піску rн.п=1500 кг/м3,
щебеню rн.щ=1450 кг/м3.Дійсна густина цементу rц=3,1 г/см3, суміші
заповнювачів rз=2,65 г/см3.Кількість хімічно зв’язної води
складає 20% від маси цементу.
Коефіцієнт виходу бетонної суміші
,
де vб.с, vц, vп, vщ –
відповідно об’єми бетонної суміші, цементу, піску, щебеню.
Насипний об’єм цементу дорівнює відношенню маси цементу до його насипної
густини: vц=mц/rн.ц=32:1,3=24,6 м3;
.
Середня густина бетонної суміші
.
Витрати піску і щебеню за масою mп і mщ знайдені як
похідні відповідних їх витрат за об’ємом на значення насипних густин (mп=45·1,5=67,5 т,
mщ=78·1,45=113,1 т), а витрата води mв – як
похідну витрати цементу на В/Ц (mв=32·0,7=22,4 т).
Для того, щоб знайти середню густину бетону rоб при випаровуванні всієї надлишкової
води, треба врахувати її при визначенні маси бетону, а замість всієї витрати
води тільки кількість хімічно зв’язаної води mх.в=32·0,2=6,4 т;
.
Дійсну густину бетону знаходять за формулою
.
Абсолютні об’єми компонентів бетонної суміші:
vа.ц=32:3,1=10,32 м3;
vа.п+vа.щ=(67,5+113,1):2,65=67,1 м3;
vх.в=6,4:1=6,4 м3.
Пористість бетону
.
Пористість бетону орієнтовно можна визначити і за іншою формулою:
,
де wх – кількість хімічно зв’язаної води в частках від маси
цементу; В і Ц – витрата води і цементу на 1 м3 бетонної
суміші;
В=mв/vб.см=22400/100=224 кг/м3;
Ц=mц/vб.см=32000/100=320 кг/м3;
.
73.Бетон на матеріалах
рядової якості при В/Ц=0,5 через n=14 діб твердіння показав міцність на
стиск Rб=25 МПа. Визначити орієнтовно активність цементу.
Для орієнтовного визначення активності цементу можна скористатися
формулою Боломея–Скрамтаєва:
Rб=А·Rц·(Ц/В–0,5),
де А – коефіцієнт якості вихідних матеріалів (приймаємо 0,6); Rб
– міцність бетону в 28–добовому віці; Ц/В – цементно–водне відношення (Ц/В=1:0,5=2).
Орієнтовну міцність бетону у 28–добовому віці знаходимо за формулою
Б.Г.Скрамтаєва:
.
Визначаємо орієнтовно активність цементу: 32=0,6·Rц·(2–0,5),
звідки Rц=32/(0,6·1,5)=35 МПа.
74.Бетон М300 з ОК=9–12 см на цементі М400 після тепловологісної
обробки виробів повинен мати межу міцності при стиску 70% марочної. Досягнення
необхідної міцності бетону після теплової обробки потребувало завищення марки бетону
до М400.Для економії цементу було прийняте рішення ввести комплексну хімічну
добавку, яка містить пластифікатор і прискорювач твердіння. Яка може бути
досягнута економія цементу, якщо пластифікуюча добавка дозволяє на 8% зменшити
витрату води для досягнення потрібної рухливості бетонної суміші без зниження
міцності бетону, а прискорювач твердіння дозволяє забезпечити 70%–у міцність
бетону М350 після тепловологісної обробки? Найбільша крупність піску і щебеню
40 мм.
Знайдемо спочатку економію
цементу за рахунок прискорювача твердіння при переході бетону із М400 у М350.
Із формули Rб=АRц(Ц/В–0,5)
випливає Ц/В=(Rб+0,5Rц)/(А·Rц).
Витрата цементу Ц=(Ц/В)·В.
За рис. 4.2. можна зробити висновок, що необхідна витрата води повинна
бути 195 кг.
Для бетону М400 розрахункові значення Ц/В і Ц відповідно складають:
.
При зміні марочної міцності бетону
DЦ/В=DRб/(А·Rц,)
де DЦ/В – різниця
цементно–водних відношень, необхідних для відповідних марок бетону; DRб – різниця меж міцності бетону при стиску
для порівнюваних марок.
При переході бетону від М400 до М350
DЦ/В=(40–35)/(0,6·40)=0,21.
Економія цементу при введенні прискорювача твердіння DЦ1=(DЦ/В)·В=0,21·195=41 кг,
що складає 10% витрати цементу, необхідного для отримання бетону М400.
Додаткову економію цементу за рахунок введення пластифікуючої добавки
можна знайти за формулою
DЦ2=(Ц/В)·DВ,
де DВ – зменшення
водовмісту бетонної суміші.
Для бетону М350 Ц/В, вирахуване за приведеною вище формулою, складає
1,96; DВ=195·0,08=13,65 кг; DЦ2=1,96·13,6»27 кг.
Загальна економія цементу за рахунок комплексної пластифікатора і
прискорювача твердіння DЦ=DЦ1+DЦ2=41+27=68 кг.
Вона складає приблизно 17% від витрати цементу до введення добавки.
75.Встановити склад змішаного розчину М50 для кладки стін будівель із
порожнистої цегли. Рухливість розчину повинна складати 7 см. В’яжуче –
портландцемент активністю30 МПа і насипною густиною rоц=1200 кг/м3.
Неорганічна добавка – вапняне тісто із середньою густиною rов=1400 кг/м3, пісок –
дрібний кварцовий з насипною густиною rо.п=1350 кг/м3
і вологістю 6%.
Визначаємо витрати матеріалів на 1 м3 піску.
За табл. 4.3 витрата цементу
складає Ц=185 кг, а його об’єм vц=185:1,2=154 л.
Витрата вапняного тіста vВп=170(1–0,002·Ц)=170·0,630=107 л,
а його маса Вп=107·1,4»150 кг.
Складаємо пропорцію об’ємних частин розчину:
.
Витрата води В=0,50·(Ц+Вп)=0,50·(185+150)=167 кг.
Отриманий розрахунковий склад повинен бути відкоригований на пробних
замісах.
76. Визначити коефіцієнт виходу і витрату матеріалів на 1 м3
вапняного розчину складом вапно:пісок 1:3 (за об’ємом) при об’ємі порожнин в
піску П=40%.
Коефіцієнт виходу b=vр/(vВп+vп).
Об’єм розчину, отримуваного з 1 м3 вапняного тіста і
3 м3 піску, vр=1+3·(1–П/100)=1+3·(1–0,4)=2,8 м3.
Коефіцієнт виходу b=2,8/(1+3)=0,7.
Витрата вапна на 1 м3 розчину
.
Витрата піску vп=0,36·3=1,08 м3.
Таблиця 4.3
Марка
розчину
|
Рекомендована марка в’яжучого
|
Rв·mв
|
Витрата в'яжучого на 1 м3
|
піску
|
розчину
|
200
150
100
75
50
25
|
500
400
500
400
300
500
400
300
500
400
300
200
400
300
200
200
|
180
140
102
81
56
|
360
450
280
350
470
205
255
340
160
200
270
405
140
185
280
155
|
410
490
330
400
510
245
300
285
195
240
310
445
175
225
325
190
|
Примітка: Rб – активність в’яжучого, mв
– маса в’яжучого. Наведені витрати в’яжучих належать до цементно–вапняних та
цементно–глиняних розчинів і піску у рихло–сипучому стані при вологості 3–7%.
5. Штучні без випалювальні кам’яні матеріали
77. Визначити необхідну витрату вапна, води для гашення і піску для
отримання n=1000 шт. силікатної цегли густиною rс.ц=1800 кг/м3 при
вологості wц=6%. Активність вапна А=85%, вологість піску wп=6%.
Активність вапняно–піщаної маси (вміст СаО) Ам=8% за масою.
Прийняти, що при гасінні вапна добавка води Вф=120 % розрахункової.
Маса 1000 шт. силікатної цегли із вологістю 6% складає mк=b·h·l·n·rо.к=0,12·0,065·0,25·1000·1800=3510 кг,
де b=0,12, l=0.25 і h=0,065 – розмір цегли, м.
Маса 1000 шт. сухої цегли
.
Вміст СаО mСаО=mц.с·Ам/100=3300·0,08=264 кг.
При активності 85% вміст негашеного вапна у масі
.
Розрахункова витрата води на гасіння вапна можна знайти з реакції
СаО + Н2О = Са(ОН)2
56 18 74
56 — 18
264 — Вр
Вр=264·18/56=84,8 кг.
Витрата води Вф=(Вр·120)/100==(84,8·120)/100=102 кг.
Витрата сухого піску Пс=mц.с–mВп–Вф=3300–310–102=2888 кг.
Витрата вологого піску Пw=Пс+Пс·wп/100=2888+2888·0,06=
=3061 кг.
78. Порівняти теплопровідність звичайної керамічної цегли масою
3,41 кг, одинарної і потовщеної цегли масою відповідно 3,7 кг і
4,3 кг, а також пустотілого силікатного каменю масою 5,96 кг. Розміри
звичайної керамічної і одинарної силікатної цегли 0,25х0,12х0,065 м,
потовщеної силікатної цегли – 0,25х0,12х0,088м і пустотілого силікатного каменю – 0,25х0,12х0,138 м.
Знаходимо середню густину звичайної керамічної цегли:
rз.к.ц=3, 41/(0,25·0,12·0,065)=1748 кг/м3;
одинарної силікатної цегли: rо.с.ц=3,7/(0,25·0,12·0,065)=1897 кг/м3;
потовщеної силікатної цегли rп.с.ц=4,3/(0,25·0,12·0,088)=1628 кг/м3;
пустотілого силікатного каменю rп.с.ц=5,96/(0,25·0,12·0,138)=1440 кг/м3.
Орієнтовно можна підрахувати, що теплопровідність кам’яних матеріалів
пропорційна їх середній густині. Тоді, умовно прийнявши теплопровідність
звичайної керамічної цегли за 1, значення теплопровідності порівнюваних силікатних
виробів будуть відповідно 1,08, 0,93 і 0,82.
79. В каналізаційний колектор, помилково збудований із силікатної цегли,
попадають промислові стічні води, які містять соляну кислоту у кількості с=13 г
на 1 м3 води. Розрахувати, яка кількість вапна буде розчинена
із цегляних стін колектора за місяць його експлуатації, якщо за добу через
нього проходить v=100 м3 стічних кислих вод, а у реакцію
вступає m=40% кислоти. Через колектор в місяць проходить стічних вод
V=30·v=30·100=3000 м3.
В реакцію вступає кислота:
.
Руйнування цегли проходить в результаті реакції вапна із кислотою:
Са(ОН) + 2НСl = CaCl2 + H2O
Складаємо пропорцію:
73 кг НСl – 74 кг Са(ОН)2
15,6 кг НСl – x
кг. Са(ОН)2
x=15.6·74/73=15,7 кг.
80. Підібрати склад газосилікату при міцності Rr=5 МПа
середньою густиною в сухому сані ro.г=600 кг/м3.
Газоутворювач – алюмінієва пудра ПАК–3. Активність вапна АВп=70%.
В’яжуче змішане – вапно : пісок (1:1).
По графіку (рис. 5.1.) встановлюємо, що водотверде відношення
газосилікату (В/Т) при rо.г=600 кг/м3
складає 0,52, витрата алюмінієвої пудри – 0,175% маси матеріалів.
За табл. 5.1 необхідна активність суміші, тобто вміст активного СаО, % до
маси сухої суміші, Асм=19%.
Витрата вапна

де k – коефіцієнт, враховуючий кількість гідратної води, k=0,85–0,95).
Вміст меленого піску у в’яжучому Пм=Вп=147 кг/м3.
Кількість кремнеземистого
компоненту в суміші:
Пк=k·rо.г–Вп–Пм=0,9·600–147–147=246 кг/м3.
Витрата
води В=(Вп+Пм+Пк)·В/Т=(147+147+246)·0,52=284 л.
Розрахунковий склад газосилікату повинен бути уточнений дослідними
замісами.
Таблиця 5.1
Вміст активного СаО, % до маси сухої суміші
|
Межа міцності при стиску, МПа,
при середній густині сухого газосилікату, кг/м3
|
300
|
400
|
500
|
600
|
700
|
800
|
900
|
1000
|
16 |
0,5 |
1,5 |
2,3 |
4,1 |
5,9 |
7,5 |
9,0 |
11,0 |
17 |
0,7 |
1,7 |
2,5 |
4,3 |
6,1 |
8,0 |
9,6 |
11,8 |
18 |
0,8 |
1,8 |
2,7 |
4,6 |
6,5 |
8,4 |
10,3 |
12,6 |
19 |
0,9 |
1,85 |
2,9 |
5,0 |
7,0 |
8,8 |
11,0 |
13,3 |
20 |
1,0 |
1,9 |
3,0 |
5,2 |
7,3 |
9,2 |
11,6 |
14,2 |
21 |
1,1 |
2,0 |
3,2 |
5,3 |
7,6 |
9,7 |
12,3 |
15,0 |
81. Розрахувати витрату матеріалів на заміс дрібнозернистого шлаколужного
бетону. Вологість суміші w=13%, маса одного замісу mз=350 кг
(прийнята із урахуванням коефіцієнта виходу із бетонозмішувача 0,6). Місткість
бетонозмішувача vб.м=250 л, середня густина бетону rо.б=2300 кг/м3. Склад
суміші, %: заповнювача – 75, шлаку – 25. Суміш замішується 15%–м розчином соди
(rс=1,15 кг/л).
Необхідна кількість води В=mз·w/(100+w)=350·13/110=40,26 кг.
Для визначення
кількості соди складаємо пропорцію:
0,085 кг води – 0,015 кг соди
40,26 кг води – x кг соди
x=40,26·0,015/0,085=7,1 кг.
Загальна кількість шлаку і заповнювача
Ш+З=mз–В–x=350–40,26–7,1=303 кг.
Кількість заповнювача З=303·75/100=227 кг.
Кількість шлаку Ш=303–227=76 кг.
Об’єм розчину соди vс=(В+х)/rс=(40,26+7,1)/1,15=41,18 л.
82. Розрахувати потребу гіпсу, шлаку і води для приготування S=300 м2
перегородочних гіпсошлакових плит. Визначити середню густину гіпсошлакової
суміші і висушеного гіпсошлакобетону. Співвідношення гіпсу і шлаку 1:2 (за
об’ємом); дійсна густина шлаку rш=2,5 г/см3,
насипна густина шлаку rн.ш=1250 кг/м3,
насипна густина гіпсу rн.г=800 кг/м3,
водогіпсове відношення В/Г=0,56, товщина плити b=8 см, кількість хімічно
зв’язної води в гіпсошлакобетоні – 20% маси гіпсу. Об’єм бетону, який
витрачається на 300 м2 плит,
v=S·b=300·0,08=24 м3.
Коефіцієнт виходу гіпсошлакобетону
,
де пористість ;
.
Витрата гіпсу на 24 м3 гіпсошлакобетону: за об’ємом:
;
за масою:
Г=vг·rн.г=12·800=9600 кг
Витрата шлаку за об’ємом: vш=12·2=24 м3;
за масою Ш=vш·rн.ш=24·1250=30000 кг.
Витрата води В=Г·В/Г=9600·0,56=5376 кг.
Середня густина гіпсошлакобетонної суміші
rг.б=(9600+30000+5376)/24=1874 кг/м3.
Середня густина сухого гіпсошлакобетону
rс.г.б=(9600+30000+9600·0,2)/24=1730 кг/м3.
6. Деревинні матеріали
83. Соснові дошки тривалий час зберігались на повітрі при t=20ºC і
відносній вологості wвідн=80%. Визначити вологість дощок і їх
середню густину, якщо при стандартній 12%–й вологості густина деревини сосни r12=500 кг/м3.
Рівноважну
вологість деревини визначаємо по діаграмі Н.Н.Чулицького (рис. 6.1.). При заданих
умовах зберігання w=18%.
Середню густину деревини при визначенні вологості легко знайти, знаючи
середню густину при стандартній вологості r12 і коефіцієнт об’ємної усушки (для
сосни k=0,44):
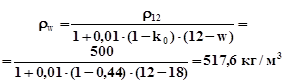
84. Сосновий брусок має розміри 25х30х400 мм (aхbхc) при вологості
w=21%. Як зміняться розміри бруска після повного висушування, а потім
зволоження до межі насичення? Коефіцієнт усушки сосни kу=0,44.
Величину усушки при висушуванні бруска знаходимо із умови
У=kу·w=0,44·21=9,24%.
Нехай розмір зразка при вологості 0 дорівнює a0, а при
вологості w – a, тоді
,
Звідки
a0=a·(100–У)/100=25·(100–9,24)/100=22,7 мм.
Аналогічно знайдемо інші розміри бруска. Вони становлять: b0=27,2 мм
і с0=363 мм. Таким чином, після висушування брусок буде мати
розміри: 22,7х27,2х363 мм.
При зволоженні сухого бруска його лінійні розміри збільшуються за рахунок
розбухання деревини, що відповідає межі насичення, wм.н=30%. При цій
вологості характерне максимальне розбухання деревини Pmax:
,
де kр – коефіцієнт розбухання.
Коефіцієнт розбухання kр пов’язаний із коефіцієнтом усушки
залежністю kр=100·kу·(100–30·kу).
Для сосни kр=100·0,044/(1000–30·0,44)=0,5.
.
Аналогічно знайдемо інші розміри бруска після зволоження до межі
насичення. Розміри соснового бруска 26,1х31,3х417,4 мм.
85. Середня густина дуба у абсолютно сухому стані rо.д=650 кг/м3, а граба rо.г=760 кг/м3. Знайти
пористість і максимальне водопоглинання деревини дуба і граба.
Дійсна густина деревини, чи так званий показник густини деревної речовини
rд.р, у середньому
для всіх порід становить 1,53 г/см3. Тоді пористість дуба і
граба:
;
.
Вологість, яка характеризує максимальне водопоглинання деревини,
знаходять за формулою
,
де wп.н – вологість межі насичення кліткових стінок (wп.н=30%);
rв – густина
води.
Для дуба .
Для граба .
86. Зразки деревини у вигляді прямокутних призм розрізом 20х20 мм і
висотою 30 мм при вологості w=20% зруйнувалися при випробуванні на стиск
вдовж волокон при максимальному навантаженні Fст=0,0147 МН.
Інші зразки із цієї ж породи деревини у вигляді прямокутних призм розрізом
20х20 мм і висотою 300 мм при w=20% зруйнувались при випробуванні на
статичний згин за одноточковою схемою при максимальному навантаженні Fзг=0,0014 МН.
Визначити породу деревини, з якої виготовлені зразки.
Межа міцності зразків при
стиску при w=20%:
Rст=Fсж/S=0,0147/(0,02·0,02)=36,75 МПа.
Межа міцності зразків при статичному згині при w=20% (l=0,24 м):
.
Перерахуємо отримані значення
межі міцності на стандартну вологість деревини:
Rст12=Rw·[1+0,04·(w–12)]=36,75·[1+0,04·(20–12)]=48,5 МПа;
Rзг12=Rw·[1+0,04·(w–12)]=63·[1+0.04·(20–12)]=83,16 МПа.
Можна зробити висновок, що випробуванні зразки виготовлені із деревини
сосни, для якої за довідковими даними Rст12=48,5 МПа, Rзг12=86 МПа.
87. Визначити орієнтовно межу міцності при стиску повздовж волокон і при
статичному згині зразків деревини сосни і дуба, якщо відомо, що кількість m
пізньої деревини у них становить відповідно 20 і 80%.
Кількість пізньої деревини, %, підраховується на торцевих зрізах деревини
вимірюванням пізньої зони річних шарів із точністю до 0,1 мм на відстані
15–20 мм.
Для розв’язку використовуємо емпіричні формули.
Для деревини сосни
Rст12=0,6·m+30=0,6·20+30=42 МПа;
Rзг12=1,4·m+56=1,4·20+56=84 МПа.
Для деревини дуба
Rст12=0,32·m+29,5=0,32·80+29,5=55,1 МПа;
Rзг12=0,43·m+47,5=0,43·80+47,5=81,9 МПа.
88. Порівняти для модрини і
липи при стандартній вологості межу міцності при стиску вздовж волокон і
поперек волокон у радіальному і тангенціальному напрямках.
Руйнівне навантаження при стиску вздовж волокон Fст виявилось
для модрини 0,026 МН, липи – 0,018 МН; поперек волокон Fст
у радіальному напрямку для модрини – 0,0027 МН, для липи – 0,0034 МН;
у тангенціальному напрямку – для модрини – 0,0037 МН, для липи –
0,0031 МН. Для випробування межі міцності деревини при стиску застосовують
зразки–призми з розмірами a=20 мм і h=30 мм. Межу міцності при стиску
вздовж волокон визначаємо за формулою Rст12=Fст/(a·b).
А при стиску поперек волокон R’сж12=F’ст/(a·h)
Для модрини
Rст12=0,026/(0,02·0,02)=65 МПа;
R'ст12=0,0027/(0,02·0,03)=4,5 МПа (в
радіальному напрямку);
R’’ст12=0,0037/(0,02·0,03)=6,17 МПа (в
тангенціальному напрямку).
Для липи
R ст12=0,018/(0,02·0,02)=45 МПа;
R’ст12=0,0034/(0,02·0,03)=5,67 МПа (в
радіальному напрямку);
R’’ст12=0,0031/(0,02·0,03)=5,17 МПа (в
тангенціальному напрямку).
Таким чином, міцність при
стиску вздовж волокон більше міцності при стиску поперек волокон для модрини в
10,5–14,4 рази, для липи – в 7,9–8,8 рази.
7. Метали
89. Розшифрувати марки вуглецевої сталі загального призначення:
Ст. 1кп, Ст. 3Гпс3, БСт. 2сп2, ВСт. 4пс6; Якісної
конструкційної вуглецевої сталі: 05кп, 10кп, 60Г, А12; легованої сталі: 09Г2СД,
12Х2Н4А, Г13, 30ГС.
Вуглецеві сталі загального призначення:
Ст. 1кп – сталь групи А (постачається за механічними властивостями)
першої категорії з умовним номером 1, який залежить від хімічного складу і
механічних властивостей, кипляча; Ст. 3Гпс3 – сталь групи А третьої
категорії з умовним номером 3 із підвищеним вмістом марганцю (Г),
напівспокійна; БСт. 2сп2 – сталь групи Б (яка постачається за хімічним
складом) другої категорії з умовним номером 2, спокійна; ВСт. 4пс6 – сталь
групи В (яка постачається за механічними якостями і хімічному складу) шостої
категорії з умовним номером 4, напівспокійна.
Якісні конструкційні вуглецеві сталі: 05кп – сталь із середнім вмістом
вуглецю 0,05%, кипляча; 10 кп – сталь із середнім вмістом вуглецю 0,1%,
кипляча; 60Г – сталь із середнім вмістом вуглецю 0,6% і підвищеним вмістом
марганцю; А12 – автоматна сталь із середнім вмістом вуглецю 0,12%.
Леговані сталі:
09Г2СД – сталь із вмістом вуглецю 0,09%, марганцю до 2%,кремнію до 1%,,
міді до 1%; 12Х2Н4А – сталь із вмістом вуглецю 0,12%, хрому 2%, нікелю 4%,
високоякісна; Г13 – сталь із вмістом вуглецю 1% і більше, марганцю 13%; 30ГС –
сталь із вмістом вуглецю 0,3%,марганцю і кремнію до 1%.
90. Механічні властивості конструкційної сталі визначаємо на циліндричних
зразках з початковим діаметром d0=10 мм, площею поперечного
перерізу S0=78,5 мм2 і довжиною l0=100 мм.
Допустиме навантаження, пропорційне відносному видовженню зразка, Fп.п=34 кН.
Навантаження, при якому досягається кінцеве видовження, рівне 0,05% початкової
(розрахункової) довжини зразка, F0,05=37,36 кН. Навантаження,
при якому кінцеве видовження складає 0,02% початкової довжини, F0,2=41,5 кН.
Найбільше навантаження, яке передує руйнуванню, F=68 кН. Довжина робочої
частини зразка після розриву l1=110 мм. Діаметр шийки зразка
після розриву d1=8,4 мм.
Визначити межу пропорційності, умовну межу текучості, тимчасовий опір
сталі, відносне видовження і звуження.
Межа пропорційності σп.п=Fп.п/S0=0,034·106/78,5=433 МПа.
Межа пружності σ0,05=F0,05/S0=0,03736·106/78,5=475 МПа.
Умовна межа текучості σ0,2=F0,2/S0=0,0415·106/78,5=529 МПа.
Тимчасовий опір (межа міцності при розтягу)
σв=F/S0=0,068·106/78,5=866 МПа.
Відносне видовження
.
Відносне звуження
.
За довідковими даними можна знайти, що марка конструкційної сталі 70.
91. При визначенні модуля пружності сталі використали зразок з початковим
діаметром d=10 мм (початкова площа поперечного перерізу S0=78,5 мм2)
і розрахунковою довжиною l =100 мм. Вимірювачем деформації служить
тензометр з ціною поділки 0,002 мм. Навантаження проводили ступенями DF=5400 Н до навантаження F, яке відповідає 70%
очікуваної межі пропорційності (F=37800 Н). При даному навантаженні за
шкалою тензометра зафіксовано показник 105 поділок. Розрахувати модуль
пружності сталі.
Модуль пружності Е, МПа, вираховують за формулою
,
де Dlсер
– середня величина приросту видовження зразка, мм, на ступінь навантаження:
;
.
92. При випробовуванні твердості сталі по Брінеллю за допомогою кульки з
діаметром D=10 мм при навантаженні F=30 кН отриманий діаметр відтиску
d=5,05 мм. При випробовуванні твердості цієї ж сталі методом Роквела при
вимірюванні за шкалою В різниця h–h0 глибини занурення стальної
кульки під дією загального навантаження 981 Н і попереднього навантаження
98 Н складає 0,108 мм. Яку твердість має сталь і до якої марки її
можна віднести?
Твердість за Брінеллем
виражають числом твердості НВ і визначають за формулою
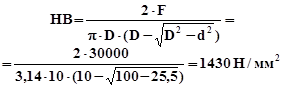
Для орієнтовного визначення тимчасового опору sв сталі використовуємо емпіричну формулу
sв»0,34·НВ»0,34·1430=486 МПа.
Твердість сталі при вимірюванні методом Роквела виражають в умовних
одиницях. При вимірюванні за шкалою В її визначають за формулою
HR=130–l
де l=(h–h0)/0,002; l=0,108/0,002=54.
HR=130–54=76.
За результатами визначення
твердості методами Брінелля і Роквела випробувану сталь можна віднести до марки
Ст.3.
93. Для випробування на ударну в’язкість сталі до і після термічної
обробки використовували стандартні квадратні зразки перерізом 1´1 см і довжиною 5,5 см з надрізом глибиною
0,2 см. Запас енергії маятника до удару складав А1=85 Дж.
Невикористана енергія маятника після злому зразка сталі до термообробки А2=15 Дж,
після термообробки А2=21 Дж. Знайти ударну в’язкість сталі.
Ударна в’язкість сталі Rуд характеризує роботу, яка
витрачається для ударного злому зразка металу з надрізом Ан,
віднесену до площі поперечного перерізу зразка S у місці надрізу: S=1·(1–0,2)=0,8 cм2.
Робота, затрачена на злом зразка сталі, до термообробки
Ан=А1–А2=85–15=70 Дж;
після термообробки
Ан=А1–А2=85–21=64 Дж.
Ударна в’язкість сталі до термообробки Rуд=70/0,8=87,5 Дж/см2;
після термообробки R'уд=64/0,8=80 Дж/см2.
94. Визначити усереднену економію металу, %, і економію затрат, грн., на
1 т металу при заміні у виробництві залізобетонних виробів 1 т
арматурної сталі А–ІІІ на А–V.Коефіцієнти приведення для сталей А–ІІІ і А–V
відповідно 1,43 і 2,2. Гуртова вартість арматурних сталей А–І, А–ІІІ, А–V
відповідно 146; 163; 216 грн. за 1 т. Арматурна сталь різних класів і
видів може бути у відомих межах взаємозамінною. Із цього випливає, що кількість
сталі будь–якого класу Т може бути виражена в умовно еквівалентній за міцністю
приведеній кількості сталі класу А–І – Т–1:
Т=Т1/kпр,
де kпр – коефіцієнт приведення сталі даного класу до сталі
класу А–І (підраховується як відношення похідної розрахункового опору арматури
на коефіцієнти її конструктивного використання і використання металу для сталі
даного класу до значень цих характеристик для сталі класу А–І). Усереднена
економія металу визначається із виразу
Ем=(1–1/kпр)·100.
Економія витрат в вартісному виразі Эс від використання
1 т арматурної сталі даного класу визначається за формулою
Ес=kпр·Ц1–Ц2,
де Ц1 – вартість сталі класу А–І; Ц2 – вартість
сталі більш високого класу.
Економія металу при заміні арматури класу А–І на клас А–ІІІ:
Эм=(1–1/1,43)·100=30,1%;
А–V на А–І:
Э'м=(1–1/2,2)·100=54,7%.
Економія затрат при заміні
А–І на А–ІІІ:
Эс=1,43·146–163=45,78 грн. на 1 т;
А–І на А–V:
Э'с=2,2146–216=105,2 грн. на 1 т.
При заміні арматури класу А–ІІІ на А–V досягається, таким чином, економія
металу DЭм=Э'м–Эм=54,7–30,1=24,6%;
економія затрат DЭc=Э'с–Эс=105,2–45,78=59,42
грн. на 1 т.
8. Матеріали на основі
органічних в’яжучих
95. В якому
процентному відношенні потрібно змішати бітуми нафтові покрівельні
БНК 45/180 і БНК 90/30 при отриманні покрівельних гарячих мастик
МБК–Г–55 і МБК–Г–75?
У відповідності з
ДСТУ 4044–2001 температура розм’якшення бітумного в’яжучого t за методом
«кільця і кульки» повинна бути для мастик МБК–Г–55 – 41…50°С, МБК–Г–75 –
61…70°С.
Бітум
БНК 45/180 має середню температуру розм’якшення не нижче tм=45°С,
БНК 90/30 – tт=90°С, де tм і tт –
температура «м¢якого» і «твердого» бітумів. Кількість тугоплавкого бітуму Бт,
%, який вводиться в розплавлений бітум, можна знайти за формулою
.
Для мастики
МБК–Г–55 . 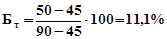
Для мастики
МБК–Г–75 .
Таким чином, у
склад бітумного в’яжучого мастики МБК–Г–55 повинно входити 11,1% бітуму
БНК 90/30 і 88,9% бітуму БНК 45/180, мастики МБК–Г–75 – 55,5%
БНК 90/30 і 44,5% БНК 45/180.
96. Розрахувати
склад дрібнозернистої гарячої асфальтобетонної суміші типу Б.
Зерновий склад вихідних
мінеральних матеріалів і результати розрахунку приведені в табл. 8.1.
Розрахунок складу
асфальтобетонних сумішей на першому етапі передбачає визначення складу
мінеральної частини, яка забезпечує максимальну густину мінерального остова.
Виходячи із
рекомендацій ГОСТ 9128–84 визначають часткову участь кожного компоненту.
Часткову участь щебеню Dо.щ назначаємо так, щоб отримати повний
залишок на ситі з розміром отворів 10 мм, який не перевищує 30% (Dо.щ=30:55=0,54).
У мінеральному
порошку міститься 20% зерен крупністю 0,071мм, звідси величина повного проходу
скрізь сито складатиме 100–20=80%. У відповідності із рекомендованими межами
повний прохід на ситі № 0071 повинен бути в межах 6–12% або в середньому 9%.
Частковий вміст мінерального порошку: Dо.м=9:80=0,11. Вміст піску 1–0,54–0,11=0,35.
Знайдені співвідношення між фракціями є об¢ємними. При використанні
матеріалів, які суттєво відрізняються за густиною, частковий вміст кожного
компонента множиться на поправочний коефіцієнт
kx=r2/r1,
де r1 – дійсна густина матеріалу,
кількість якого переважає в суміші; r2 – дійсна густина непереважаючого
матеріалу.
Таблиця 8.1
Матеріал
|
Дольова частка
|
Вміст зерен, %,
крупніших (мм)
|
15
|
10
|
5
|
3
|
1,25
|
0,63
|
0,315
|
0,14
|
0,071
|
Щебінь гранітний |
— |
5 |
55 |
90 |
100 |
100 |
100 |
100 |
100 |
100 |
Пісок кварцовий |
— |
— |
— |
— |
— |
30 |
63 |
75 |
90 |
97 |
Порошок вапняковий |
— |
— |
— |
— |
— |
— |
3 |
5 |
10 |
20 |
Рекомендовані
ГОСТ 9128–84 межі сумарних залишків: |
— |
0–15 |
0–30 |
35–50 |
48–62 |
61–72 |
71–80 |
78–86 |
84–91 |
88–94 |
щебінь |
0,54 |
2,7 |
30 |
49 |
54 |
54 |
54 |
54 |
54 |
54 |
пісок |
0,35 |
— |
— |
— |
— |
10 |
22 |
26 |
31 |
34 |
порошок вапняковий |
0,11 |
— |
— |
— |
— |
— |
0,33 |
0,55 |
1,1 |
2,2 |
Сумарні залишки на
ситах |
|
2,7 |
30 |
49 |
54 |
64 |
78 |
81 |
86 |
90 |
Потрібна
кількість бітуму визначають за формулою
,
де Пм.ч
– порожнистість мінеральної частини випробуваних зразків, %; П0 –
задана остаточна пористість асфальтобетону, %; rб – дійсна густина бітуму при 20˚С,
г/см3;r0 – середня густина мінеральної частини асфальтобетону.
Наприклад, якщо
мінеральна частина зразків має середню густину r0=1750 кг/м3 і
порожнистість Пм.ц=18%, то при заданій остаточній пористості П0=3,5%
і rб=0,99;
.
Розрахунковий склад
асфальтобетонної суміші уточняють за експериментальними даними. Для виробництва
вибирається склад, який забезпечує необхідні властивості асфальтобетону при
мінімальній витраті бітуму.
97. Визначити
витрату матеріалів для виготовлення асфальтового бетону, який призначається для
влаштування покриття підвищеної шорсткості.
Вихідні
матеріали: дорожній бітум, вапняковий мінеральний порошок (наповнювач), пісок
із середньою густиною в ущільненому стані ρо.п=1650 кг/м3,
гранітний щебінь із середньою густиною в ущільненому стані ρо.щ=1600 кг/м3,
порожнистістю Пщ=40%. Необхідне експериментально установлене
співвідношення бітум : порошок(Б/Н) 0,96.
Для доріг із
підвищеною шорсткістю покриття необхідно, щоб міжщебеневий простір був
заповнений асфальтовим розчином без розсуву зерен щебеню. У відповідності з
цією умовою витрата щебеню повинна бути
,
де rр – густина асфальтового розчину,
орієнтовно рівна 2,3 г/см3;
.
Витрата піску
знайдемо із співвідношення
,
звідси 
Вміст
асфальтового в’яжучого (бітум + мінеральний порошок) Б+Н=100–63–26=11%.
Необхідну витрату
бітуму і мінерального порошку знайдемо із рівняння: (Б/Н)·Н+Н=11; 1,96·Н=11%;
Н=5,61%; Б=11–5,61=5,39%.
98. Визначити
склад полімерного розчину в процентах. Середня густина піску ρо.п=1440 кг/м3,
порожнистість піску Пп=40%, співвідношення полімерного в’яжучого і
наповнювача П/Н=0,4, дійсна густина наповнювача ρн=2,67 кг/м3.
Коефіцієнт зручновкладальності розчину kу=0,5.
Одна частина за
масою полімерної мастики може заповнити порожнини піску в наступній кількості:
.
Таким чином,
полімерна мастика і пісок у розчині повинні знаходитись в частках за масою – 1
: 1,24 або в % – 44,65 і 55,35. Враховуючи співвідношення полімеру і
наповнювача в складі мастики, склад розчину можна виразити наступним чином, %:
полімер – 12,75; наповнювач – 31,9; пісок – 55,35.
99. Визначити вид
білил, які використовуються для виготовлення масляної фарби, що містить 45%
оліфи (Ол), якщо на фарбування скляної пластинки площею S=200 см2
витрачено mк=4 г фарби. При визначенні олифомісткості білил на
mб=5 г сухого пігменту витрачено mм=0,7 г лляного
масла.
Відомо, що покривність,
тобто витрата пігменту, г на 1 м2 фарбованої поверхні, для
свинцевих білил – 160…200, літопонових – 110…140, титанових – 35…54, цинкових –
100…120. Олифомісткість свинцевих білил – 9…12, літопонових – 11…15, титанових
– 20…25, цинкових – 12…16 на 100 г пігменту.
Покривність, г/м2,
для фарб малярної консистенції Ук=mк/S; для сухих
пігментів: Уп=mк·(100–Ол)/(100·S).
Для використаних
сухих білил
Уп=4·(100–45)/(100·0,02)=110 г/м2.
Олифомісткість
сухих білил, г, на 100 г:
М=100·mм/mб=100·0,7/5=14.
Білила, які
використовуються для отримання фарби, являються цинковими білилами.
100. Визначити
кількість полімеру густиною 1,13 г/см3 для виготовлення плити
утеплювача розміром 100´50´5 см заливним способом і тиск, який створюється у формі,
якщо при вільному спіненні рідкого полімеру об’ємом vр.п=11 см3
утворюється vп=166 см3 пінопласту.
Визначаємо
кратність спінення К:К=vп/vр.п=166:11=15,1.
Необхідна
кількість полімеру
mп=1,2·vф·rп/К,
де 1,2 –
коефіцієнт запасу; vф – об’єм форми (vф=100´50´5=25000 см3);
mп=1,2·25000·1,13/15,1=2245 г,
або 2,24 кг.
Потрібний об’єм
рідкого полімеру для заповнення форми v¢р.п=2245:1,13=1987 см3.
Тиск, яке розвивається
в формі буде більше , ніж при вільному спіненні, у n раз:
n=К·vр.п/vф=15,1·1987/25000=1,2.
|