Контрольная работа: Породы древесины. Технология теплоизоляционных материалов, пластмасс, железобетонных изделий
Контрольная работа: Породы древесины. Технология теплоизоляционных материалов, пластмасс, железобетонных изделий
Федеральное агентство по
образованию
Государственное
образовательное учреждение высшего
профессионального
образования
Кафедра технологии
строительного производства
Контрольная работа №1
По технологии
конструкционных материалов
Кемерово 2010
Задача:
Примерно насколько дуб
прочнее сосны на сжатие, если известно, что образец дуба тяжелее сосны в два
раза, а масса сосны при 12%-й влажности равна 420кг?
Решение
в зависимости от
средней плотности
R12 = d ρm12 – l,
где d, 1 -
коэффициенты, зависящие от вида древесины: для дуба d =
850, l = 67; для сосны
d = 920, l = 50; pm12 - средняя плотность
древесины при
стандартной влажности 12 %, г/см3.
Rд = 850х 690 – 67=58,6433МПа
Rс = 920х 500 – 50=45,9950МПа
Отсюда следует, что дуб
прочнее сосны на сжатие примерно в 1,2 раза.
Вопросы:
1.
Перечислить
основные ядровые, заболонные и спелодревесные породы древесины
Сделав только
поперечный срез, вы можете наиболее четко рассмотреть строение древесины.
Каждый брусок необтесанного дерева имеет кору – это кожа дерева, которая не
используется в работе, ее обязательно нужно снимать. Под корой располагается
зона роста дерева, которая практически не различима невооруженным глазом.
На свежем спиле с
растущего дерева этот слой камбия представлен очень хорошо. После того как вы
снимите кору, вам откроется тонкая прослойка влажной ткани зеленоватого цвета
это и будет камбий. За камбием расположена собственно древесина с годичными
кольцами. Ее еще называют заболонью. В центре каждого дерева есть ядро, которое
по цвету может сливаться с заболонью или иметь более темный цвет. В зависимости
от этого разделяют заболонные породы древесины, где ядро не имеет ярко
выраженной структуры и клетки расположены так же плотно, как и в заболони , и
ядровые, где, соответственно, ядро хорошо различимо . Иногда заболонные породы
дерева называют безъядровыми.
К ядровым древесным
породам относятся все хвойные (сосна, кедр, ель, тис, лиственница) и некоторые
лиственные породы, например дуб, ясень, тополь. Большинство лиственных пород
составляет ряд заболонных, или безъядровых: береза, граб, ольха, клен.
Спелодревесные породы
древесины — древесные породы с одинаковой окраской в поперечном сечении, у
которых центральная часть ствола отличается от заболони только меньшей
влажностью - ель, пихта, бук, липа и др.
2.
Какие
главные физико-химические процессы протекают при автоклавной обработке
известково-песчаных камней?
Автоклавными
силикатными изделиями называют изделия, изготовляемые из смеси извести и
мелкозернистых материалов (песка, золы-уноса, шлаков, лессовидных суглинков),
процесс твердения которых происходит в автоклавах под давлением пара 8-12 ат.
Изготовление цемента
сопровождается химическими реакциями на всех стадиях технологического процесса.
Огромный резерв увеличения выпуска, снижения стоимости и повышения качества
цемента связан с химизацией его производства. Так, при введении в сырьевую
смесь небольших доз разжижителей в виде сульфитно-дрожжевой бражки,
триполифосфата натрия, метасиликата натрия,продуктов обработки щелочью бурого
угля и других веществ значительно снижается влажность поступающего в печь
шлама, в результате чего повышается производительность печи и понижается расход
топлива на обжиг. Благодаря вводу в сырьевую шихту минерализаторов (плавиковый
шпат, фосфогипс, фосфоросодержащие шлаки, кремнефтористый натрий, гипс и др.)
интенсифицируется процесс обжига клинкера. Добавка к сырьевой смеси частично
вместо части глинистого компонента фосфоросодержащих шлаков повышает
производительность вращающихся печей на 8-10%, повышает марку цемента.
Связующим в силикатных
бетонах является вяжущее, состоящее из гидросиликатов и гидроалюминатов
кальция, образующихся в результате физико-химического процесса, протекающего в
паровой среде автоклава.
В зависимости от
температуры пара, времени действия, удельной поверхности кремнеземистой
составляющей, насыщенности известью и других факторов образуются минералы -
гидросиликаты кальция (ксонотлит, тоберморит, гилебрандит и др.). Преобладание
той или иной формы гидросиликата кальция в изделии диктует свойства материала.
Управление процессом минералообразования путем правильного подбора смеси и
установления режима термообработки позволяет создать материалы с заданными
свойствами.
Первой операцией при
изготовлении силикатных изделий является измельчение извести в мельнице и
составление смеси в растворомешалке или бегунах.
Для активизации
процессов минералообразования в массу вводят молотый песок либо перемалывают
известь вместе с песком.
Для интенсификации
процесса образования гидросиликатов кальция иногда в массу добавляют сульфат
натрия (до 1%).
Одним из вариантов
технологии производства силикатных изделий является предварительное смешивание
и совместный помол в дезинтеграторе гашеной извести или молотой кипелки и
песка. Материал, попадая под удар быстро вращающихся стержней, смешивается и
частично измельчается. Недостатком этого способа является быстрое изнашивание
пальцев и корзин дезинтегратора.
Второй операцией
производства силикатных изделий является формование. Силикатный кирпич
прессуется на специальных прессах под давлением (150-250)*105 н/м2 и
укладывается автоматически на вагонетки. В процессе автоклавной обработки
известь вступает с кремнеземистым компонентом в химическую реакцию, в
результате которой образуются гидросиликаты кальция, скрепляющие зерна
заполнителя в прочный монолит.
Химические процессы,
происходящие на разных стадиях производства, можно представить в следующем
виде:
1. Выделение водорода
на стадии образования пористой структуры в сырце:
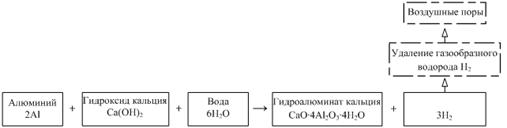
2. Образование
гидроксидов и гидросиликатов на стадии набора сырцом пластической
(транспортной) прочности:
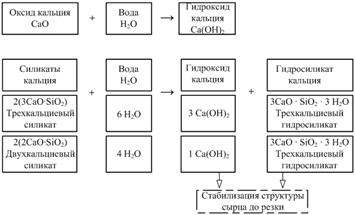
3. Образование новых
минералов (тоберморита) на стадии автоклавной обработки:
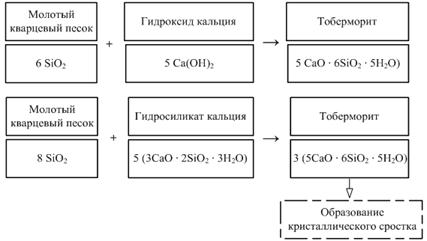
При производстве
крупногабаритных ячеистых изделий большой толщины необходимо принять меры к
уменьшению осадки массы. В этом случае до автоклавной обработки формы с залитой
ячеистой массой выдерживают в течение 3-4 ч; хорошие результаты дает ввод в
состав массы пористых добавок - шлака, керамзита и т. д.
Для сокращения срока
выдерживания изделий до автоклава в смесь вводят небольшое количество
хлористого кальция, растворимого стекла, гипса, сернокислого глинозема.
Одним из важнейших
вопросов в технологии производства ячеистых бетонов является выбор
порообразователя. Для изготовления пеносиликатных изделий хорошим
пенообразователем является гидролизованная кровь (ГК). Для газосиликатных
изделий применяют алюминиевую пудру.
В качестве добавки для
регулирования скорости гашения извести применяют тонкомолотый гипс.
Формы перед заливкой
ячеистой массы смазывают петролату-мом или смесью солярового масла и автола или
выстилают полиэтиленовой пленкой.
Отформованные
силикатные изделия поступают в автоклавы на обработку паром под давлением 8-12
ат примерно по такому режиму: подъем давления 2-3 ч, выдержка при максимальном
давлении пара 2-12 ч, спуск давления 2 ч.
Автоклав представляет
собой горизонтальный цилиндр диаметром 2600-3600 мм и длиной 17-20 м. В нем
уложены рельсовые пути для вагонеток или платформ. После загрузки крышку
автоклава герметически закрывают, в котел впускают пар, постепенно доводят
давление до заданного.
Автоклавы применяют
двух типов: тупиковые и проходные.
Для ускорения процесса
запаривания иногда предварительна вакуумируют загруженный автоклав. При
пропаривании часть извести остается свободной и процесс твердения ее
заканчивается в дальнейшем за счет поглощения углекислоты из воздуха. При
запаривании крупногабаритных изделий в формах полезное заполнение автоклава
составляет не более 30%.
В последнее время
практикуют двухстадийный процесс запаривания: вначале изделия в формах
поступают в ямные камеры с температурой 60-80° С на 8-10 ч, где они приобретают
прочность, позволяющую направлять их в распалубленном состоянии в автоклавы для
дальнейшего твердения.
После термообработки
изделия остывают в течение 2 ч в теплом помещении, затем их транспортируют на
склад готовой продукции.
3.
Что
служит сырьем для изготовления теплоизоляционных материалов на основе
неорганических вяжущих веществ?
Минеральные изделия на
битумных вяжущих (неорганические). Неорганические теплоизоляционные материалы и
изделия получают из неорганического сырья путем его переработки. Изделия этой
группы характеризуются малой плотностью 35…500 кг/м3. Они не горят, не гниют,
сравнительно долговечны и поэтому широко применяются для теплоизоляции
строительных конструкций и промышленного оборудования. К этому типу относятся
минеральная вата, ячеистые и лёгкие бетоны, стекловолокно, пеностекло,
вспученный перлит и т.д.
Сырье: горные породы,
шлаки, стекло и асбест.
4.
Изложите
основу важнейших методов переработки пластмасс – экструзия, литье, под
давлением, горячее прессование.
Экструзия - это метод
изготовления изделий или полуфабрикатов (гранулированного, порошкообразного или
зернистого полимера) из полимерных материалов, заключающийся в выдавливании
материала через канал головки экструдера.
Экструзия двухручьевая
- это вид экструзии, осуществляемый на линиях, оснащенных двушнековыми
экструдерами.
По сравнению с обычной
двухручьевая экструзия имеет принципиальные отличия:
• по расположению
профиля в обоих потоках (в одну сторону или зеркально относительно средней
линии);
• по экструзии
одинаковых или разных профилей;
• по конструкции
экструзионной головки (одна общая или две одинаковых параллельных);
• по конструкции
калибраторов (в зависимости от формы профилей и их расположения в головке);
• по исполнению
экструдера;
• по схеме работы с
одним или двумя независимыми тянущими устройствами.
Экструзия одноручьевая
- это вид экструзии, который осуществляется на линиях, оснощенных одношнековыми
экструдерами, где перабатываются комплектующие профили к панелям типа вагонки
со скоростью в 1,5 раза выше чем при двуручьевой экструзии.
Экструзия многоручьевая
- это одновременное параллельное изготовление нескольких изделий сразу.
Многоручьевая экструзия
позволяет получить значительно больший выход продукции почти на той же площади,
что и при одноручьевой. Использование многоручьевой головки целесообразно
также, когда сечение экструдируемого профиля невелико и в обычной головке могут
развиться опасно высокие давления.
Число ручьев обычно не
превышает двух-четырех, так как при большем числе каналов возникают проблемы
обеспечения равномерности выхода расплава по сечению, поддержание стабильности
температуры в головке, равномерности отвода и охлаждения профилей. Обычно
каналы головки располагаются параллельно в горизонтальной плоскости. Каждый
ручей головки может иметь либо свое собственное комплектующее оборудование
(охлаждающую ванну, тянущее, отрезное и приемное устройства), либо общее. В
первом случае получение изделий упрощается, поскольку каждый ручей фактически
независим, и возможная неравномерность скоростей выдавливания расплава не имеет
существенного значения. Однако при такой компоновке возрастают производственные
площади под оборудование.
При отводе двух
профилей одним и тем же тянущим устройством приходится обеспечивать одинаковые
скорости выхода расплава из каждого канала. Это достигается применением
дросселирующих устройств в головке, если это возможно технически, или с помощью
изменения температуры по зонам головки каждого ручья, для чего головка должна
иметь независимые тепловые зоны регулирования.
В тех случаях, когда
изделие можно получать обычным путем или используя многоручьевую экструзию,
бывает трудно решить, что предпочтительнее.
Экструзия плунжерная -
это основной метод переработки высокомолекулярного полиэтилена в погонажные.
На долю плунжерной
экструзии приходится примерно 35% общего объема переработки ВМПЭ. С помощью
этого метода получают полуфабрикаты типа простых профилей, труб, стержней,
прутков. В плунжерных экструдерах полиэтиленовый порошок сжимается до
образования уплотненной массы, которая в последней обогреваемой зоне цилиндра
пластицируется под высоким давлением. Температура переработки составляет
180-200 "С.
Литье многослойное -
относится к специальным видам, иногда называемым соинжекционными.
Это
название отражает общую особенность этих методов — обязательное участие в
процессе двух, а в некоторых случаях и трех инжекционных узлов, в каждом из
которых пластицируется полимерный материал с индивидуальными свойствами. Таким
образом, появляется возможность получать многоцветные изделия, изделия,
состоящие из различных видов пластмасс (поверхность из ПЭВП, а основной объем
из вспененного полистирола), использовать вторичное полимерное сырье для
внутренних, неответственных частей деталей, производить изделия гибридной
конструкции и пр.
Литье ротационное - вид
многослойного литья, который позволяет получать изделия с четким разделением
цветов, однако требует использования съемной вставки. После оформления
центральной части изделия (узел I) вставка извлекается, а в образовавшийся
объем инжектируется расплав из узла П. В цикл производства изделия ротационным
литьем введена дополнительная операция размыкания формы и удаления (установки)
вставки, что не способствует высокой производительности метода.
Литье соинжекционное -
разновидность многослойного литья, которая требует применения сопла специальной
конструкции, называемого также разделительной головкой. Эта технология
позволяет получать изделия с числом слоев больше двух, с полным или частичным
разделением цветов.
Литье под давлением
Литье под давлением -
самый распространенный способ получения изделий из полимерных материалов.
Он
применяется как в производстве небольших деталей, например, шестеренок для
часов, так и для изготовления изделий большого размера (мусорные баки,
автомобильные бамперы). В большинстве случаев изготовленные по этой технологии
изделия не требуют дополнительной обработки.
Литье
под давлением — метод формования изделий из полимерных материалов,
заключающийся в нагревании материала до вязкотекучего состояния и
передавливании его в закрытую литьевую форму, где материал приобретает
конфигурацию внутренней полости формы и затвердевает. Этим методом получают
изделия массой от нескольких граммов до нескольких килограммов с толщиной
стенок 1—20 мм (чаще 3—6 мм). Для осуществления литья под давлением применяют плунжерные
или шнековые литьевые машины (рис. 1), на которых устанавливаются литьевые
формы различной конструкции (рис. 2)
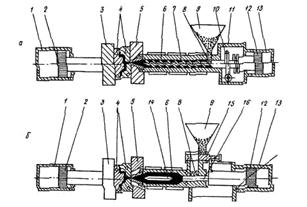
Рис. 1. Схема литьевой
машины со шнековой (а) и плунжерной (б) пластикацией расплава:
1 — гидроцилиндр
механизма смыкания; 2 — поршень гидроцилиндра механизма смыкания; 3 — подвижная
плита; 4 — полуформы; 5 — неподвижная плита; 6 — пластикационный цилиндр, 7
шнек литье пластмассы; 8 — загрузочное окно цилиндра пластикации; 9 — бункер;
10 — привод шнека; 11 — корпус гидроцилиндра механизма впрыска; 12 — поршень
гидроцилиндра впрыска; 13 — гидроцилиндр шнека; 14 — торпеда — рассекатель
потока расплава; 15 — дозатор; 16 — плунжер
Рис. 2. Литьевая форма:
1 — подвижная
полуформа; 2 — толкатель; 3 — выталкивающая плита, 4 — выталкиватели; 5
каналы системы термостатирования формы; 6 — литниковая втулка; 7 — центральный
литник; 8 — центрирующая втулка; 9 — центрирующая колонка; 10 — неподвижная
полуформа; 11 — сопло литьевой машины; 12 — разводящий литник; 13 — впускной
литник; 14 — формообразующая полость
Основными
технологическими параметрами процессов литья под давлением являются температура
расплава Тр, температура формы ТФ, давление литья Рл,
давление в форме Рф, время выдержки под давлением tвпд,
время охлаждения tохл или время отверждения в форме tотв
для термореактивных материалов. Литьем под давлением перерабатываются как
термопластичные, так и термореактивные материалы, но при этом тип материала
определяет специфику физико-химических процессов, сопровождающих нагревание и
перевод в твердое состояние этих видов пластмасс. Технологическая схема
процесса приведена на рис. 3. Анализ процесса литья под давлением может быть
проведен по следующим составляющим: перевод материала в вязкопластичное состояние
> подача его в зону дозирования —> накопление расплава —> течение
расплава в системе «сопло—форма» —> течение расплава в каналах формы и
формующей полости —> формирование структуры изделия.
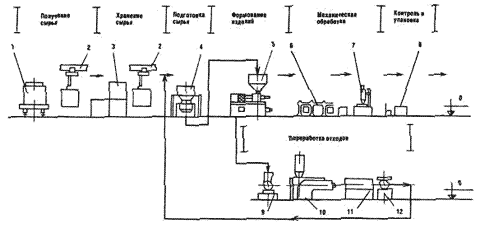
Рис. 3. Технологическая
схема литья под давлением:
1 — вагон (полувагон,
цистерна); 2 — подвесная кран-балка; 3 — склад материала; 4 — вакуумная
сушилка; 5 — литьевая машина; 6 — транспортер; 7 — станок механической
обработки; 8 — стол упаковки; 9 — дробилка; 10 — экструдер; 11 — охлаждающая
ванна; 12 — гранулятор
Горячее прессование
термореактивных пластмасс используется для производства элементов несложной
формы с урезанным числом арматуры либо в ее отсутствие.
Пластмассу (1) помещают
в загрузочную камеру (2). Там она разогревается от стенок загрузочной камеры,
переходит в вязко-текучее состояние и под действием старания пуансона (3) через
литниковую систему (4) поступает в оформляющую разъемную полость матрицы (5).
Сечение литниковых каналов слишком мало и материал поступает в плоскость с
маленькой скоростью в полужидком состоянии.
Текучесть
пресс-материала - способность материала заполнять пресс-форму под давлением при
явной температуре: ориентируется в мг/с. Нежели менее текучесть
пресс-материала, тем более наверное давление прессования и напротив. Скорость
отвердевания - определяет продолжительность перехода пластика из пластического
состояния в твердое. Она выражается в секундах либо минутах на 1 мм толщины
образца (с/мм). Летучесть - (содержание летучих препаратов и влажности) -
ориентируется по разности в весе до и в последствии высушивания пресс-материала
в термостате при температуре (103-105)?С на протяжении 30мин; ориентируется в %
и колеблется в разных материалах 1,5-5%.
Затем болванки
извлекаются из пресс-формы и запекаются в термостате при температуре 150-170˚С
для полимеризации связующего препарата. При холодном прессовании существенно
повышается производительность труда, хотя качество продуктов хуже, плоскость -
матовая. Данный способ не используем для продуктов трудоемкое формы.
При повторном нагреве
они возвращаются в пластическое состояние (полистирол, полиэтилен, полиуретан и
т.д.) разгрузка пресс-форм имеет возможность производиться лишь в последствии
замараживания. По приему переработки пластика имеют все шансы быть разделены на
последующие группы:
Этим приемом производят
составные части из листовых термопластических материалов. Суть процесса состоит
в том, что подогретый лист материала покупает форму матрицы под поступком
лишнего давления либо под влиянием вакуума.
5.
Опишите
схему изготовления железобетонных изделий поточно-агрегатным способом, его
достоинства и недостатки.
В зависимости от
мощности предприятия и номенклатуры выпускаемых изделий на современных заводах
применяют технологические схемы изготовления сборных железобетонных изделий:
конвейерную, поточно-агрегатную или стендовую.
Поточно-агрегатная
схема является наиболее распространенной в производстве железобетонных изделий.
Конструкции и детали в данном случае изготавливаются в формах, которые в
процессе производства перемещаются от одного поста к другому. При этом каждый
пост оснащается стационарным оборудованием, а время нахождения изделия на
каждом посту может быть различным. Изделие с одного поста на другой
перемещается чаще всего мостовыми кранами.
При таком способе
производства изделия изготовляют в вертикальных формах-кассетах, представляющих
собой ряд отсеков, образованных стальными, прочно укрепленными стенками
перегородками. На кассетной установке осуществляется полностью весь цикл
производства тонкостенных изделий, т. е. укладка арматуры, укладка и уплотнение
бетонной смеси и твердение. Для этой цели кассетная установка имеет вибрирующие
устройства и устройства для парообогрева или электрообогрева изделий в процессе
твердения.
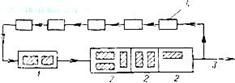
Поточно-агрегатная
схема производства сборных железобетонных изделий
1 — формовочные
агрегаты; 2 — камеры пропаривания; 3 — распалубка и выдача изделий на склад; 4
возврат пустых форм
Поточно-агрегатная
схема предусматривает достаточно высокий уровень механизации производства и
является наиболее приемлемой для смены номенклатуры выпускаемых изделий. Он
экономически целесообразен для заводов с широкой номенклатурой изделий и
средней годовой производительностью до 100 тыс. м3.
Основное преимущество
поточно-агрегатного способа производства заключается в универсальности
основного технологического оборудования. Так, например, при незначительной
затрате средств на изготовление новых форм можно быстро переходить на выпуск
другого вида изделий. Этот способ производства железобетона получил в нашей
стране наибольшее распространение. Однако, конвейерный способ производства
экономически целесообразен при выпуске однотипных изделий на заводах большой
мощности. А вот стендовый способ дает высокий экономический эффект при
изготовлении железобетонных изделий значительных размеров: плит перекрытий,
ферм и балок для промышленного и транспортного строительства.
Список литературы:
1. И.А. Рыбьев «Строительное
материаловедение»,
2. Г.И. Горчаков, Ю.М. Баженов
«Строительные материалы»,
3. В.Г. Микульский, В.Н. Куприянов и др.
«Строительные материалы»,
4. П.Ф. Шубенкин «Строительные материалы
и изделия. Примеры задач с решениями».
|