Курсовая работа: Анализ свариваемости сплавов на основе меди (М1)
Курсовая работа: Анализ свариваемости сплавов на основе меди (М1)
ФЕДЕРАЛЬНОЕ АГЕНТСТВО ПО
ОБРАЗОВАНИЮ
Государственное образовательное учреждение высшего
профессионального образования
«МАТИ» – Российский государственный технологический
университет
им. К.Э. Циолковского
|
Кафедра «Технология сварочного производства»
Курсовая работа
по дисциплине «Теория сварочных процессов»
на тему:
Анализ свариваемости сплавов на основе меди (М1) |
|
|
|
Студент группы
|
|
1СВ-4-41
|
/Бондарец Д.С./ |
Руководитель
|
|
|
/Резниченко Б.М./ |
Москва 2007 г.
Содержание
1.
Введение ………………………………………………………………………………… 3
2.
Структура и свойства меди …………………………………………………………….. 6
3.
Характеристика меди и ее сплавов …………………………………………………….17
4.
Пористость ……………………………………………………………………………… 17
5.
Особенности технологии сварки………………………………………………………. 19
5.1. Подготовка
под сварку…………………………………………………………….. 20
5.2. Газовая
сварка………………………………………………………………………. 21
5.3. Ручная
сварка……………………………………………………………………….. 22
5.4. Автоматическая
сварка под флюсом……………………………………………… 23
5.5. Электрошлаковая
сварка меди и ее сплавов……………………………………… 25
5.6. Дуговая
сварка в защитных газах………………………………………………….. 25
6.
Свариваемость меди…………………………………………………………………….. 27
7.
Вывод…………………………………………………………………………………….. 28
8.
Список литературы ……………………………………………………………………… 30
Введение
Медь (лат. Cuprum) - химический
элемент I группы периодической системы Менделеева (атомный номер 29, атомная
масса 63,546). В соединения медь обычно проявляет степени окисления +1 и +2,
известны также немногочисленные соединения трехвалентной меди. Важнейшие
соединения меди: оксиды Cu2O,
CuO, Cu2O3;
гидроксид Cu(OH)2, нитрат Cu(NO2)2*3H2O, сульфид CuS,
сульфат(медный купорос) CuSO4*5H2O, карбонат CuCO3*Cu(OH)2,
хлорид CuCl2*2H2O.
Медь - один из семи металлов,
известных с глубокой древности. Переходный период от каменного к бронзовому
веку (4 - 3-е тысячелетие до н.э.) назывался медным веком или халколитом ( от
греческого chalkos - медь и lithos - камень) или энеолитом (от латинского
aeneus - медный и греческого lithos - камень). В этот период появляются медные
орудия. Известно, что при возведении пирамиды Хеопса использовались медные
инструменты.
Чистая медь - ковкий и мягкий
металл красноватого, в изломе розового цвета, местами с бурой и пестрой
побежалостью, тяжелый (плотность 8,93 г/см3) , отличный проводник
тепла и электричества, уступая в этом отношении только серебру (температура
плавления 1083 °C). Медь легко
вытягивается в проволоку и прокатывается в тонкие листы, но сравнительно мало
активна. В сухом воздухе и кислороде при нормальных условиях медь не
окисляется. Но она достаточно легко вступает в реакции: уже при комнатной
температуре с галогенами, например с влажным хлором образует хлорид CuCl2,
при нагревании с серой образует сульфид Cu2S, с селеном. Но с водородом, углеродом и азотом медь не
взаимодействует даже при высоких температурах. Кислоты, не обладающие
окислительными свойствами, на медь не действуют, например, соляная и
разбавленная серная кислоты. Но в присутствии кислорода воздуха медь
растворяется в этих кислотах с образованием соответствующих солей:
2Cu + 4HCl + O2
= 2CuCl2 + 2H2O.
В атмосфере, содержащей CO2,
пары H2O и др.,
покрывается патиной - зеленоватой пленкой основного карбоната, ядовитого
вещества.
Медь входит более чем в 170
минералов, из которых для промышленности важны лишь 17, в том числе: борнит
(пестрая медная руда - Cu5FeS4), халькопирит (медный колчедан - CuFeS2),
халькозин (медный блеск - Cu2S), ковеллин (CuS), малахит (Cu 2 (OH)2CO3).
Встречается также самородная медь.
Производство меди
Медь добывают из оксидных и
сульфидных руд. Из сульфидных руд выплавляют 80% всей добываемой меди. Как
правило, медные руды содержат много пустой породы. Поэтому для получения меди
используется процесс обогащения. Медь получают методом ее выплавки из
сульфидных руд. Процесс состоит из ряда операций: обжига, плавки, конвертирования,
огневого и электролитического рафинирования. В процессе обжига большая часть
примесных сульфидов превращается в оксиды. Так, главная примесь большинства
медных руд пирит FeS2 превращается в Fe2O3. Газы, образующиеся при обжиге, содержат CO2,
который используется для получения серной кислоты. Получающиеся в процессе
обжига оксиды железа, цинка и других примесей отделяются в виде шлака при плавке.
Жидкий медный штейн (Cu2S
с примесью FeS) поступает в конвертор, где через него продувают воздух. В ходе
конвертирования выделяется диоксид серы и получается черновая или сырая медь.
Для извлечения ценных (Au, Ag, Te и т.д.) и для удаления вредных примесей
черновая медь подвергается сначала огневому, а затем электролитическому
рафинированию. В ходе огневого рафинирования жидкая медь насыщается кислородом.
При этом примеси железа, цинка и кобальта окисляются, переходят в шлак и
удаляются. А медь разливают в формы. Получающиеся отливки служат анодами при
электролитическом рафинировании.
Основным компонентом раствора при
электролитическом рафинировании служит сульфат меди - наиболее распространенная
и дешевая соль меди. Для увеличения низкой электропроводности сульфата меди в
электролит добавляют серную кислоту. А для получения компактного осадка меди в
раствор вводят небольшое количество добавок. Металлические примеси,
содержащиеся в неочищенной ("черновой") меди, можно разделить на две
группы:
1) Fe, Zn, Ni, Co. Эти металлы имеют значительно более
отрицательные электродные потенциалы, чем медь. Поэтому они анодно растворяются
вместе с медью, но не осаждаются на катоде, а накапливаются в электролите в
виде сульфатов. Поэтому электролит необходимо периодически заменять.
2) Au, Ag, Pb, Sn. Благородные металлы (Au, Ag) не претерпевают
анодного растворения, а в ходе процесса оседают у анода, образуя вместе с
другими примесями анодный шлам, который периодически извлекается. Олово же и
свинец растворяются вместе с медью, но в электролите образуют малорастворимые
соединения, выпадающие в осадок и также удаляемые.
Применение меди
Медь, ее соединения и
сплавы находят широкое применение в различных отраслях промышленности. В
электротехнике медь используется в чистом виде: в производстве кабельных
изделий, шин голого и контактного проводов, электрогенераторов, телефонного и
телеграфного оборудования и радиоаппаратуры. Из меди изготавливают
теплообменники, вакуум-аппараты, трубопроводы. Более 30% меди идет на сплавы.
Сплавы меди с другими металлами используют в машиностроении, в автомобильной и
тракторной промышленности (радиаторы, подшипники), для изготовления химической
аппаратуры. Высокая вязкость и пластичность металла позволяют применять медь
для изготовления разнообразных изделий с очень сложным узором. Проволока из
красной меди в отожженном состоянии становится настолько мягкой и пластичной,
что из нее без труда можно вить всевозможные шнуры и выгибать самые сложные
элементы орнамента. Кроме того, проволока из меди легко спаивается сканым
серебряным припоем, хорошо серебрится и золотится. Эти свойства меди делают ее
незаменимым материалом при производстве филигранных изделий. Коэффициент
линейного и объемного расширения меди при нагревании приблизительно такой же ,
как у горячих эмалей, в связи с чем при остывании эмаль хорошо держится на
медном изделии, не трескается , не отскакивает. Благодаря этому мастера для
производства эмалевых изделий предпочитают медь всем другим металлам. Как и
некоторые другие металлы, медь входит в число жизненно важных микроэлементов.
Она участвует в процессе фотосинтеза и усвоении растениями азота, способствует
синтезу сахара, белков, крахмала, витаминов. Чаще всего медь вносят в почву в
виде пятиводного сульфата - медного купороса CuSO4*2H2O. В большом
количестве он ядовит, как и многие другие соединения меди, особенно для низших
организмов. В малых же дозах медь необходима всему живому.
Структура
и свойства Меди
Среди технических
металлов Медь по своему значению и распространению занимает особое место.
Чистая медь обладает высокой теплопроводностью и электропроводимостью и
достаточно высокой коррозионной стойкостью.
Ниже приведены
физические константы меди:
Атомный вес |
63,54 |
Кристаллическая решетка |
Г.ц.к. |
Периоды решетки, А |
3,6080 |
Плотность, г/см3
|
8,94 |
Атомный объем, см3/г-атом
|
7,21 |
Температура плавления, °С |
1083 |
Температура кипения, °С |
2595 |
Удельная теплоемкость при 20°С, кал/см сек град |
0,0915 |
Теплопроводность при 20°С, кал/см сек град |
0,984 |
Удельный вес меди |
8,93 г/cм3 |
Удельная теплота плавления меди |
42 кал/г |
Коэффициент линейного расширения
меди
(при температуре около 20oC)
|
16,7 *106(1/град) |
Удельное сопротивление меди при
20oC |
0,0167 Ом*мм2/м |
Весьма ценным качеством меди
является также ее высокая пластичность в горячем и холодном состояниях. Это
позволяет изготавливать из меди различные деформируемые полуфабрикаты- листы,
ленты, полосы, прутки, трубы, проволоку и др. широко применяемые в различных
областях техники.
Промышленные
марки меди и области их применения указаны в Табл.1.
Табл.1.
Химический состав меди промышленных марок по ГОСТ 859-51.[1]
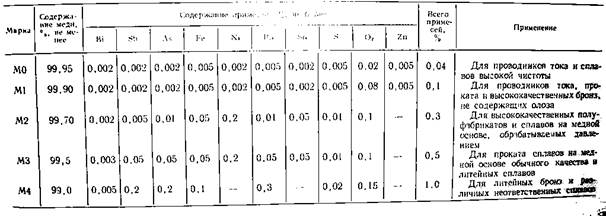
Как видно из этой таблицы,
указанные марки отличаются друг от руга различным содержанием примесей.
Содержание в меди
газовых и легкоплавких примесей может быть значительно снижено
электронно-лучевой плавкой.
Эффективность очистки меди при электронно-лучевой плавке
показана в Табл. 2.
Табл.2. Изменение содержания
примесей в меди при электронно-лучевой плавке.[1]
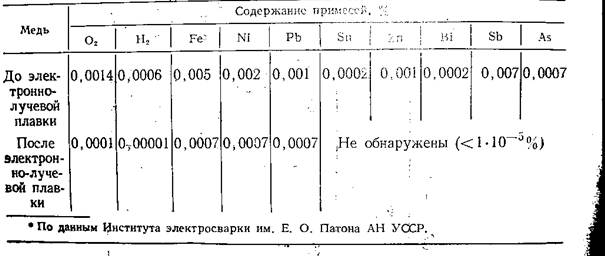
Медь, полученная
электронно-лучевой плавкой, характеризуется более высокой электропроводностью и
теплопроводностью. И обеспечивает большую стабильность и долговечность в работе
изделий электровакуумной и радиотехнической промышленности. Поэтому потребность
в такой меди возрастает с каждым годом.
Прочность и твердость
меди можно значительно повысить путем холодной деформации. Однако при этом
снижается пластичность и электропроводность меди.
Свойства наклепанной
меди можно восстановить путем отжига (рекристаллизации).
Механические свойства
меди, так же как и других металлов, существенно изменяются с повышением
температуры. Причем для меди имеется характерный провал пластичности в
интервале температур 200-800°С, причина
которого пока не выяснена.
Чистая медь устойчива
против атмосферной коррозии в следствии образования на поверхности тонкой
защитной пленки. Пресная вода и конденсат пара практически не действуют на
медь. Незначительна также скорость коррозии меди в морской воде. Медь плохо
сопротивляется действию аммиака, хлористого аммония, щелочных цианистых
соединений, окислительных минеральных кислот, сернистого газа и др.
Взаимодействие меди с
кислородом отмечается уже при комнатной температуре. При температурах до 100°С на поверхности меди образуется пленка
окиси меди черного цвета. При более высоких температурах скорость окисления
меди значительно возрастает и на поверхности образуется пленка закиси меди
красного цвета.
При деформировании меди
наблюдается раздробление и удлинение отдельных зерен и создается определенная
их ориентация. При больших степенях деформации материал приобретает волокнистую
структуру. При нагреве (отжиге) деформированной меди происходит
рекристаллизация, в результате чего создается качественно новая структура.
Размер зерна
рекристаллизованной меди оказывает заметное влияние на е механические свойства.
Чрезмерное повышение температуры отжига приводит к сильному росту зерна и
резкому падению прочности меди. Это явление в практике называется перегревом. При
температурах отжига, близких к температуре начала оплавления, кроме того,
возможно окисление границ зерен и частичное их оплавление (пережог). Перегрев
можно исправить повторной деформацией с последующим отжигом при более низких
температурах. Пережог является непоправимым браком.
Чистота меди оказывает
большое влияние как на ее свойства, так и на поведение при последующей
обработке. Многие примеси даже в ничтожных количествах (тысячные и сотые доли
процента) резко снижают электропроводность и теплопроводность меди, а также
ухудшают способность меди к обработке давлением.
В зависимости от
характера взаимодействия с медью все примеси можно условно разделить на три
группы:
1)
К первой группе относятся элементы, растворимые в твердой меди (Al, Fe, Ni, Sn, Zn, Au, Ag, Al, pt, Cd, Sb).
2)
Вторую группу составляют элементы, практически нерастворимые в
меди и образующие с ней легкоплавкие эвтектики (Pb, Bi, и др.)
3)
К третьей группе относятся элементы, образующие с медью хрупкие
химические соединения (S, O2,
P и др.)
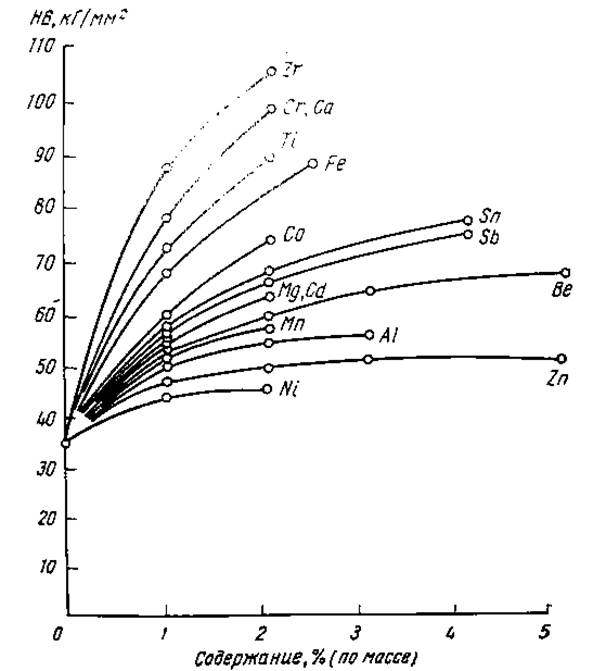
Рис.1
Влияние добавок на твердость меди.[1]
Растворимые элементы при малых
концентрациях не могут быть обнаружены под микроскопом, так как они входят в
твердый раствор. Эти примеси в допустимых пределах практически не уменьшают
способности меди к пластической деформации. В большинстве случае добавки этих
элементов повышают ее твердость и прочность, снижают электропроводность и
теплопроводность.
Нерастворимые
примеси – свинец и висмут – образуют с медью эвтектики, состоящие почти из
чистых металлов (содержание висмута в эвтектике 99,8 % , а свинца 99,94 %).
Вследствие почти полной нерастворимости свинца и висмута в твердой меди эти
эвтектики появляются в сплавах при любом их содержании и, кристаллизуясь
последними, залегают по границам зерен меди.
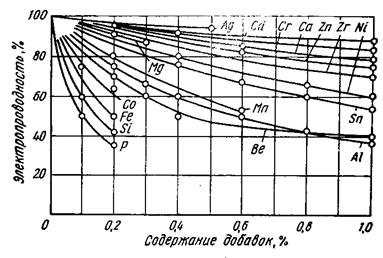
Рис.2
Влияние добавок на электропроводность меди.[1]
Висмут (точнее богатая
висмутом эвтектика) образует тончайшие прослойки между зернами меди, причем
толщина таких прослоек, по некоторым данным, по некоторым данным может
достигать нескольких атомных слоев. Поэтому обычно бывает достаточно уже
тысячных долей процента висмута, чтобы подобные прослойки образовались на значительной
части межзеренной поверхности.
Свинец при малых его
содержаниях, так же, как и висмут, образует по границам зерен меди тонкие
легкоплавкие прослойки, которые хорошо видны на нетравленом шлифе в виде темной
сетки. При больших содержаниях последний обнаруживается в виде темных точек по
границам зерен меди.
При микроскопическом
анализе литой меди на свинец необходимо иметь в виду, что, подобно свинцу,
могут выглядеть имеющиеся в отливках поры и мелкие раковины, которые тоже
располагаются преимущественно по границам зерен. Микропоры легко отличить от
включений свинца следующим простым приемом: поворотом микрометрического винта
микроскопа микрошлиф слегка выводят из фокуса и снова наводят на фокус, при
этом края микропор в отличие от включений свинца то сходятся, то расходятся.
Примеси третьей группы
сера и кислород – образуют с медью химические соединения Cu2S и Cu2O, которые также располагаются по границам зерен меди в виде
эвтектик Cu-Cu2O и a(Cu)-Cu2O.
Ввиду того, что
эвтектические точки на диаграммах состояния Cu-Cu2O и
Cu-Cu2S сильно сдвинуты в сторону чистой меди, то основой эвтектик
в этом случае является медь, в которой вкраплены включения сульфида или закиси
меди. При малом содержании кислорода эвтектика образует тонкую оторочку вокруг
зерен меди, намечая их контуры даже без травления. По мере увеличения
содержания кислорода количество эвтектики увеличивается и при содержании 0,39 %
O2 сплав имеет чисто эвтектическое строение.
Эвтектика a(Cu)-Cu2O
имеет точечное строение, где отдельные темные точки являются частичками закиси
меди (Cu2O) ; основу
эвтектики (светлое поле) составляет медь (точнее твердый раствор кислорода в
меди). Растворимость кислорода в меди при эвтектической температуре (1065°С) составляет 0,0035 %, при 600°С 0,0007 %. При переходе за эвтектическую
точку (0,39 % O2) выпадают первичные
кристаллы закиси меди, имеющие форму дендритов. Под микроскопом закись меди на
нетравленом шлифе выявляется в форме темно-голубых включений. В поляризованном
свете частички закиси меди принимают рубиново-красную окраску, что является
характерным ее признаком, так как другие включения – сульфиды, фосфиды – в этих
условиях не дают цветной реакции.
При травлении смесью 3
% -ого FeCl3 в 10 %-ной HCl закись меди принимает темную окраску в отличие от включений
сульфидов, фосфидов, которые не меняют свое окраски.
По количеству эвтектики
в доэвтектическом сплаве можно определить приблизительно содержание кислорода в
меди
[1]
где Fэвт
-площадь поля зрения микрошлифа, занимаемая эвтектикой, %
0,39 – содержание кислорода в
эвтектике.
При деформации
нарушается литая структура металла и частицы закиси меди располагаются по
границам сильно вытянутых зерен меди., образуя так называемую строчечную
структуру. При отжиге происходит перестройка структуры основного металла и
частиц закиси меди, несколько укрупняясь за счет их слияния, располагаются в
виде цепочек внутри рекристаллизационных зерен.
Структура меди с
примесями серы во многом подобна сплавам меди с кислородом, что объясняется
одинаковым характером взаимодействия этих примесей с медью. Однако в сплавах
меди с серой в сильной степени сказывается явление коалесценции, в результате
чего вместо раздробленных выделений сульфидов наблюдается образование крупных
скоплений в форме капель и эвтектика часто не имеет характерного точечного
строения.Рис.3.
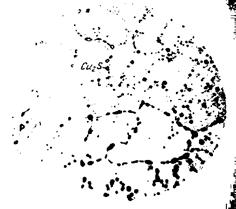
Рис.3
Микроструктура литой меди с примесью серы. ´250. По границам зерен меди (светлые) располагаются
включения сульфида меди (Cu2S) (темные).
Сульфид меди на
нетравленом шве по своей окраске ничем не отличается от закиси меди и только
применение идикаторного травителя (смеси 3%ого FeCl3
в 10%-ой HCl) и поляризованного света позволяет эти
соединения друг от друга.
Примеси, образующие с
медью легкоплавкие эвтектики и хрупкие химические соединения, ухудшают ее
механические свойства и сильно снижают способность к пластической деформации.
При небольших содержаниях кислород и сера не оказывают заметного отрицательного
влияния на горячую обработку меди.
Кислород является
причиной так называемой «водородной болезни» меди. Сущность этого явления
заключается в том, что при нагреве кислородосодержащей меди в восстановительной
атмосфере ( в среде, содержащей H2, CO, CH4 и т.п. газы)
водород и другие газы, проникая в твердую медь, взаимодействуют с содержащимся
в ней кислородом и образуют водяные пары (или CO2),
нерастворимые в меди и стремящиеся выделиться из нее под некоторым давлением. В
результате этого в местах их выхода образуются микротрещины, которые служат
причиной разрушения металла при последующей обработке давлением или в процессе
работы деталей, изготовленных из такой меди. По этой причине в отношении
содержания кислорода в стандартах на медь и медные изделия даются весьма
жесткие нормы.
Для раскисления меди
обычно применяют небольшие добавки фосфора. Весьма эффективным раскислителем
меди является также литий.
Влияние серы и
кислорода на механические свойства меди показано на Рис.4.
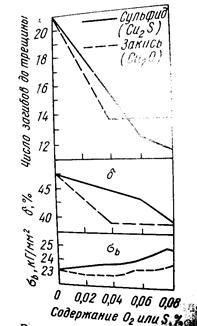
Рис.4
Влияние серы и кислорода на механические свойства меди.[1]
Наиболее
вредными примесями в меди и ее сплавах являются висмут и свинец. Эти примеси
уже при ничтожных содержаниях (тысячные и сотые доли процента) резко снижают
пластичность меди при повышенных температурах. Висмут вследствие его хрупкости
способствует также понижению пластичности и в холодном состоянии. Влияние свинца
на механические свойства меди показано на Рис.5.
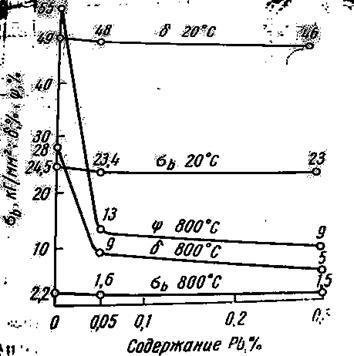
Рис.
5 Влияние свинца на механические свойства меди.[1]
Вредной примесью
считают также сурьму, отождествляя ее действие с поведением висмута и меди.
Однако это не вполне обосновано. Сурьма, согласно последним данным, до 2%
входит в твердый раствор с медью (см. Рис.6) и поэтому не должна
ухудшать ни горячей, ни холодной обработки меди. В сплавах на основе меди, где
растворимость сурьмы уменьшается в десятки раз, влияние на ее свойства
сказывается весьма существенно.
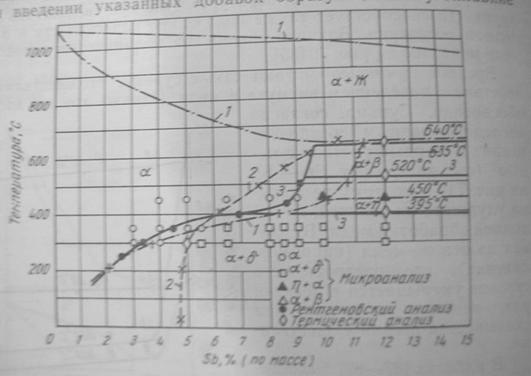
Рис.
6 Диаграмма состояния Cu-Sb [1]
1 – Марц и Матьюсон (1931г.);
2 – Шибота;
3 – по данным автора (1938 г.)
Вредное влияние
легкоплавких примесей можно устранить путем введения специальных присадок,
связывающих эти примеси в тугоплавкие химические соединения. Наиболее
эффективными являются такие добавки, которые образуют с примесью химические
соединения, кристаллизующиеся при температуре либо выше, чем сама медь, либо,
по крайней мере, при температуре выше горячей обработки сплава. Легкоплавкие
соединения могут способствовать горячеломкости. Зная формулы этих соединений,
при известном содержании примеси можно приблизительно подсчитать необходимое
количество нейтрализующей присадки.
Однако при выборе
присадок нельзя не учитывать и той среды, в которой происходит образование
соответствующих соединений. Во многих случаях вводимые добавки могут химически
взаимодействовать с другими компонентами сплава или образовывать с ними твердые
растворы. При образовании химических соединений или твердых растворов действие
таких добавок на примеси частично или полностью парализовываться.
Для связывания свинца и
висмута наиболее эффективными присадками оказались:
Для висмута- литий, кальций, церий,
цирконий, магний;
Для свинца- кальций, церий и
цирконий.
При введении указанных добавок
образующиеся тугоплавкие соединения (см. Табл. 3) кристаллизуются не в
виде легкоплавких интеркристаллических прослоек, а в форме компактных
изолированных тугоплавких соединений.
Табл.
3 Химические соединения свинца и висмута и температуры их плавления.[1]
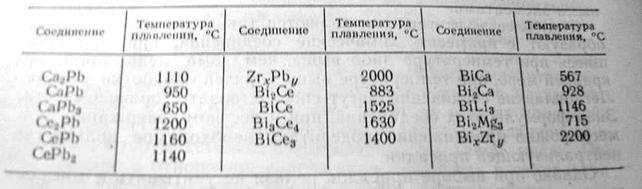
При этом происходит
заметное очищение границ зерен от примесей и значительная часть включений
располагается внутри зерен меди.
В результате такого
изменения (модифицирования) структуры достигаются существенные улучшения
механических свойств, особенно при высоких температурах. Одновременно с этим
устраняются горячеломкость и хладноломкость сплавов, типичные для меди,
содержащей легкоплавкие и хрупкие примеси.
Указанные методы
обезвреживания свинца и висмута в меди позволяют расширить возможности
использования низкосортных и вторичных металлов для производства медных
сплавов.
Как уже отмечалось,
чистая медь имеет невысокую прочность и поэтому ограниченно применяется как
конструкционный материал.
Для повышения прочности
и придания меди особых свойств (жаропрочности, коррозионной стойкости и т.д.)
ее легируют различными добавками.
Сплавы на основе меди
обладают высокими механическими и другими ценными свойствами и нашли широкое
применение в технике.
Характеристика
Меди и ее сплавов
Благодаря высокой
электропроводимости, теплопроводности и коррозионной стойкости медь заняла
прочное место в электропромышленности, приборной технике и химическом
машиностроении для изготовления разнообразной аппаратуры. Медь и многие другие
ее сплавы применяют при изготовлении криогенной техники.
Промышленность
выпускает медь марок М0,М1 и др. М1(99,9% Cu , примеси
не более 0,1%) Чистая медь хорошо обрабатывается давлением в холодном и горячих
состояниях, малочувствительна к изменениям низких температур.. При повышении
температуры прочностные свойства меди изменяются в довольно широких пределах.
В машиностроении
получили распространение сплавы на основе меди – латуни и бронзы, которые имеют
лучшие прочностные и технологические характеристики.
Медь и ее сплавы
свариваются многими способами сварки плавлением. При оценке свариваемости
необходимо учитывать, что медь и ее сплавы отличаются от большинства
конструкционных материалов более высокой теплопроводностью (в 6 раз выше, чем у
железа), коэффициентом линейного расширения (в 1,5 раза больше, чем у стали).
Медь и ее сплавы склонны к пористости и возникновению кристаллизационных
трещин, активно поглощают газы, особенно кислород и водород, которые оказывают
вредное влияние на прочностные и технические характеристики.
Кислород малорастворим
в твердой меди. При повышении температуры медь активно окисляется, образуя
оксид меди Cu2O, который при затвердевании
образует с медью эвтектику Cu-Cu2O. Располагаясь по границам зерен, эвтектика снижает коррозионную
стойкость и пластичность меди. При содержании в меди кислорода более 0,1%
затрудняются процессы горячей деформации, сварки, пайки и других видов горячей
обработки.
Водород хорошо
растворяется в жидкой меди. В затвердевшей меди растворимость водорода
незначительна. С повышением температуры растворимость водорода возрастает,
особенно при переходе в жидкое состояние.
Медь и ее сплавы в
жидком состоянии могут взаимодействовать также с оксидами углерода. Азот имеет
весьма малое сродство к меди и нерастворим в ней.
Пористость
Медь
и ее сплавы проявляют повышенную склонность к образованию пор в металле шва и
околошовной зоне. Причиной образования пор является водород, водяные пары или
образующийся углекислый газ при взаимодействии окиси углерода с закисью меди.
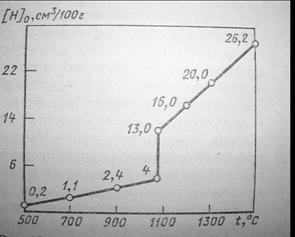
Рис.
4 Растворимость водорода в меди ( ). [4]
Высокие градиенты
температуры способствуют развитию термической диффузии водорода в зоне
термического влияния, что приводит к сегрегации водорода вблизи лини сплавления
и увеличивает вероятность возникновения дефектов: пор, трещин. Растворимость
водорода в меди зависит от содержания в ней кислорода и легирующих компонентов.
При сварке латуней
причиной пористости может стать испарение Zn,
температура кипения которого ниже температуры плавления Cu и составляет 907°С.
Испарение Zn уменьшает введение
Mn и Si.
При сварке бронз
выгорание легирующих примесей также может стать причиной появления пористости.
Возникновение пор и
микротрещин может быть также связано и с усадочными явлениями, протекающими в
процессе кристаллизации сварного шва. Низкая стойкость меди и ее сплавов против
возникновения пор в сварных швах в основном обусловлена активным
взаимодействием меди с водородом и протеканием при этом сопутствующих процессов
(образование водяных паров выделение водорода).
Медь и ее сплавы при
сварке подвержены образованию горячих трещин. Это обусловлено высоким значением
коэффициента теплового расширения, большой величиной усадки при затвердевании и
высокой теплопроводностью наряду наряду с наличием в меди и ее сплавах вредных
примесей (кислорода, сурьмы, висмута, мышьяка, серы, свинца), которые образуют
с медью легкоплавкие эвтектики. При затвердевании металла шва эвтектики
сосредотачиваются по границам кристаллов, снижая межкристаллитную прочность.
Для обеспечения высоких свойств металла концентрацию примесей в меди
ограничивают. Так, например, в меди допускается не более 0,005 сурьмы, 0,005
висмута, 0,004% серы.
При сварке меди и ее
сплавов в швах формируется крупнокристаллическая структура. Это связано с тем,
что высокая теплопроводность меди и ее сплавов при сварке способствует
интенсивному распространению теплового потока от центра сварного шва в основной
металл. При этом создаются благоприятные условия для направленной
кристаллизации от зоны сплавления в глубь сварочной ванны. Поскольку в этих
условиях не появляются новые центры кристаллизации, в сварном шве образуется
зона с кристаллитами с избирательной ориентацией; кристаллиты вытягиваются в
направлении теплового потока, образуя крупнозернистую столбчатую структуру
сварного шва.
Интенсивное
распространение теплоты в основной металл при сварке способствует росту зерна в
зоне термического влияния.
Особенности
технологии сварки
В связи с высокой
теплопроводностью меди и сплавов на ее основе для местного расплавления металла
необходимо применять источники теплоты с высокой тепловой мощностью и концентрацией
энергии в пятне нагрева. Из-за высокой теплопроводности и быстрого отвода
теплоты ухудшается формирование шва, возрастает склонность к появлению в
сварных швах дефектов (непроваров, подрезов, наплывов , трещин, пористости). В
связи с этим сварку металла большой толщины (свыше 10-15 мм) обычно выполняют с
предварительным и сопутствующим подогревом. Предварительный подогрев
обеспечивает более равномерное распределение теплоты в сварочной ванне,
улучшает условия кристаллизации сварного шва, снижает внутренние напряжения и
вероятность возникновения трещин. Изделия подогревают газовым пламенем,
рассредоточенной дугой и другими способами. Изделия из меди подогревают до
температуры 250-300°С.
Тонколистовые
конструкции с толщиной стенки 1,5-2 мм сваривают встык без разделки или с
отбортовкой кромок. Высота отбортовки 1,5-2s (s- толщина
свариваемых листов). Листы толщиной до 5 мм сваривают также без разделки
кромок, но с зазором до 2мм. Листы толщиной свыше 10мм сваривают с разделкой
кромок: под ручную дуговую сварку (РДС) с углом разделки 70° и притуплением кромок до 3мм.
Стыковое соединение
сваривают, как правило, на формирующих подкладках из меди, графита, керамики и
флюсовой подушке. Тавровые соединения больших толщин для удержания жидкой ванны
рекомендуется сваривать в «лодочку».
Применяют прессованные
прутки или проволоку диаметром 3-10мм. Химический состав присадочных стержней
(проволоки) выбирают в зависимости от требований к сварным швам и метода
сварки.
Конструкции из меди
сваривают с присадочной проволокой аналогичного состава или легированной
фосфором и кремнием до 0,2-0,3%. При введении в сварочную ванну указанных
раскислителей происходит восстановление Cu2O. Продукты реакции переходят в шлак, металл шва очищается от
кислорода. Для повышения прочностных свойств металла шва используют присадочные
стержни, легированные кремнием, фосфором, марганцем, оловом, железом и другими
элементами.
Дуговую сварку
покрытыми электродами выполняют на постоянном токе обратной полярности,
стремясь поддержать короткую дугу без колебания конца электрода. Силу тока
выбирают в зависимости от диаметра электрода. Физические и механические
свойства сварных швов обеспечивают соответствующим подбором химического состава
электродного стержня и покрытия.
Если при сварке
необходимо обеспечить высокие теплопроводность и электропроводимость металла
шва, используют электрода «Комсомолец-100» со стержнем из меди (М1).
Автоматическую сварку
меди и ее сплавов под флюсом выполняют на постоянном токе обратной полярности.
В сочетании с электродной проволокой М1 используют флюсы АН-348, ОСЦ-45, АН-20,
АН-26 и другие или керамические флюсы.
Дуговая сварка в среде
защитных газов (ручная или автоматическая) может быть выполнена в среде аргона,
гелия или их смесей вольфрамовым электродом или плавящейся электродной
проволокой.
При сварке в качестве
присадочного материала используют сварочную проволоку БрХ0,7, БрКМп3-1 или медь
марки М1 с добавкой фосфора и кремния до 0,1-0,2 %. Фосфор и кремний хорошо
раскисляют сварочную ванну, снижают пористость и обеспечивают высокие
физико-механические свойства сварных швов.
Подготовка под сварку.
Свариваемый металл и
электродная проволока перед сваркой тщательно очищаются от окислов механически
(шабером, наждаком и прочее)или химически (травлением в растворе, содержащем в
1л 75мл HNO3, 100мл H2SO4, 1мл HCl, остальное- дистиллированная вода, с
последующей промывкой в воде, затем обезжириваются).
Выбор технического
процесса сварки изделия в первую очередь определяется его назначением,
сложностью (наличие коротких или криволинейных швов в различных
пространственных положениях, труднодоступных мест) , а также числом
изготавливаемых изделий (серия) и требованиями, предъявляемыми к их качеству.
Газовая сварка.
При единичном
производстве и ремонтных работах рекомендуется использовать газовую сварку, в
процессе которой осуществляется подогрев и начальная термическая обработка
изделия. Невысокие температурные градиенты уменьшают воздействие сварочного термического
цикла на металл в зоне сварки (шов, зона термического влияния). Возможно Раскисление
и легирование металла через присадочную проволоку. Газовую сварку можно
применять как для чистой меди, так и для ее сплавов.
Газовая горелка-
тепловой источник малой сосредоточенности, поэтому для сварки меди желательно
использовать ацетиленокислородную сварку, обеспечивающую наибольшую температуру
ядра пламени. Для сварки толщин более 10мм рекомендуется применять две горелки,
из которых одна используется для подогрева, а вторая для образования сварочной
ванны.
Для сварки меди и бронз
используют нормальное пламя , а для сварки латуней (с целью уменьшения выгорания цинка).
Раскисление металла
сварочной ванны, несмотря на защиту от окружающей среды продуктами сгорания,
производится извлечение закиси меди флюсами или введением раскислителей через
присадочную проволоку.
Сварочные флюсы для
меди содержат соединения бора(борная кислота, борный ангидрид, бура), которые
растворяют закись меди, образуя легкоплавкую эвтектику, и выводят ее в шлак.
Кроме соединений бора, флюсы могут содержать фосфаты. (Табл.4)
Табл.4.
Состав Флюсов для сварки меди и ее сплавов % (по массе) [2]
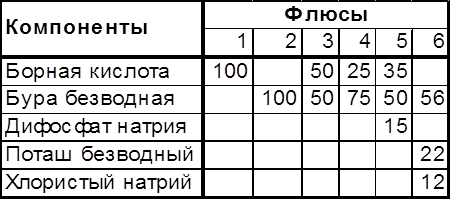
Флюсы наносят на
зачищенные и обезжиренные свариваемые кромки по 10-12 мм на сторону.
Дополнительно их можно вносить с помощью присадочного металла, на который
наносят покрытие из компонентов флюса и жидкого стекла с добавлением древесного
угля [10-20%(по массе)].При сварке алюминиевых бронз в состав флюса надо
вводить фториды и хлориды, растворяющие Al2O3, который получается при окислении
алюминия в составе бронзы.
При сварке Cu толщиной
до 3 мм разделку кромок не производят, в качестве присадочной проволоки
используют медь М1 или М2, так как медь не успевает существенно окислиться. При
больших толщинах применяют присадочную проволоку, легированную раскислителями.
При сварке медных сплавов состав присадочной проволоки должен совпадать с
составом основного металла. Медь больших толщин сваривают в вертикальном
положении. После сварки осуществляют проковку в подогретом состоянии (до
300-400 град.Цельсия) с последующим отжигом. При проковке получается мелкозернистая
структура шва и повышаются его пластические свойства.
При правильно
выполненной сварке и последующей проковке сварные швы имеют прочность и угол загиба 120-180°.
Ручная сварка.
Выполняется на
постоянном токе обратной полярности. Ориентировочные режимы приведены в Табл.5
Медь толщиной до 4 см
сваривают без разделки кромок, до 10 мм- с односторонней разделкой при угле
скоса кромок до 60-70 град. и притуплении 1,5-3 мм. При большей толщине
рекомендуется Х-образная разделка.
Теплопроводность и
электропроводность металла шва при сварке покрытыми электродами значительно
снижаются. В процессе плавления электрода с покрытием в металл шва переходит
часть легирующих компонентов и электропроводность шва составляет порядка 20% от
электропроводности меди М1. Механические свойства швов, выполненных дуговой
сваркой покрытыми электродами, вполне удовлетворительны:
, угол
загиба 180°.
Табл.5. Ориентировочные режимы
ручной однопроходной сварки меди покрытыми электродами [2]
Толщина, мм |
Диаметр электрода, мм |
Ток дуги, А |
Напряжение, В |
2 |
2-3 |
100-120 |
25-27 |
4 |
4-5 |
160-200 |
25-27 |
6 |
5-7 |
260-340 |
26-28 |
7-8 |
6-7 |
380-400 |
26-28 |
9-10 |
6-8 |
400-420 |
28-30 |
Автоматическая сварка под флюсом.
основным преимуществом
автоматической сварки Cu под флюсом является возможность получения стабильных
высоких механических свойств без предварительного подогрева. Поэтому при
изготовлении крупногабаритных сварных конструкций их Cu больших толщин
технологический процесс достаточно прост и почти не отличается от процесса
сварки сталей.
При сварке меди под
такими кислыми флюсами в металл шва переходят Si и Mn, в результате ухудшаются
тепло- и электрофизические свойства соединений по сравнению с основным
металлом. Применение бескислородных фторидных флюсов, например марки АН-М1,
позволяет получать швы, удельное сопротивление которых в 1,5 раза ниже, а
теплопроводность в 2 раза выше по сравнению со швами, выполненными под кислым
флюсом АН-348А.
Для электродуговой
сварки меди используются керамические флюсы: ЖМ-1 для сварки меди и К-13МВТУ
для сварки меди со сталью.
Режимы сварки меди под
флюсом К-13МВТУ приведены в Табл.6.
Табл.6.
Режимы сварки меди под флюсом К-13МВТУ.[2]
Толщина металла, мм |
Диаметр проволоки, мм |
Ток, А |
Напряжение, В |
1-2
5-6
|
1-2
2-3
|
160-180
400-500
|
26-27
28-30
|
Сварку ведут на
постоянном токе обратной полярности при жестком закреплениина подкладках из
охлаждающей меди(толщиной до 2,5 мм) или на графите(толщиной 5-6 мм). Состав
флюса К-13МВТУ,% (пол массе):
·
глинозем-20
·
плавиковый шпат-20
·
кварцевый песок-8-10
·
магнезит-15
·
мел-15
·
бура безводная-15-19
·
порошок алюминия-3-5
Применение керамического флюса
позволяет раскислить и легировать металл
шва, электро- и теплопроводность
металла шва получаются на уровне исходного металла.
С увеличением толщины
металла керамические флюсы становятся ограниченно пригодными, так как не
обеспечивают требуемой плотности и необходимой пластичности соединения. Снизить
пористость при сварке Cu позволила смесь, состоящая из 80% (по массе) флюса
АН-26С и 20% флюса АН-20С. Лучшие результаты по плотности швов обеспечивает
флюс сухой грануляции АН-М13 (ВТУ ИЭС 56Ф-72).
Автоматическую дуговую
сварку под флюсом применяют для соединения меди со сталью. Сварка производится
со смещением электрода на медь, практически без оплавления стали: расплавленная
медь смачивает стальную кромку и соединение образуется за счет диффузии меди в
сталь. Применяется специальная разделка кромок: скос только медной кромки под
углом 45 град. с притуплением, равным половине толщины. Стыковое или угловое
соединения собираются без зазора, расстояние оси электрода от края медной
кромки составляет 0,65-0,75 толщины меди. Режим сварки такой же, как и при
сварке медных соединений, но сварочный ток снижают до 15-20%. Сварные
соединения медь - низкоуглеродистая сталь
обладают хорошими механическими
свойствами.
Электрошлаковая сварка меди и ее сплавов.
Применяется для Cu
больших толщин 30-55мм. Легирование шва осуществляют, применяя пластинчатые
электроды соответствующего состава. Температура плавления флюса должна быть
ниже температуры плавления меди, применяются легкоплавкие флюсы системы
NaF-LiF-CaF2, которые обеспечивают устойчивый процесс, подогрев и плавление
кромок на требуемую глубину, хррошее формирование шва и легкое удаление
шлаковой корки. Особенностью режимов электрошлаковой сварки меди являются
повышенные сварочные токи: I=800-1000 A ; Uд =
40-50 В, скорость подачи пластинчатого электрода 12-15 м/ч. Механические
свойства металла шва мало отличаются от свойств основного металла.
Дуговая сварка в защитных газах.
Ручную, полуавтоматическую
и автоматическую сварку Cu и ее сплавов можно производить плавящимся и
неплавящимся электродом. Наиболее часто применяют сварку вольфрамовым
электродом с подачей присадочного металла в виде проволоки непосредственно в
зону дуги, узкой профилированной проставки, закладываемой в стык, или с
применением технологического бурта на одной из стыкуемых деталей. Реже
применяется сварка плавящимся электродом.
В качестве защитных
газов используют азот особой чистоты по МРТУ 6-02-375-66, аргон сорта высший по
ГОСТ 10157-79, гелий высшей категории качества марок А и Б по ТУ 51-940-80, а
также их смеси в соотношении по объему 50-75% аргона.
При сварке в среде
аргона плавящимся электродом процесс неустойчив, с трудом устанавливается
стабильный струйный перенос металла в сварочной дуге. При сварке в среде азота
эффективный и термический КПД дугового разряда выше, чем аргона и гелия.
Глубина проплавления получается выше, но устойчивость дугового разряда в азоте
ниже, чем в аргоне и гелии. Несмотря на высокую чистоту защитных газов, медь
при сварке подвергается окислению и может возникать пористость, что определяет
необходимость применения легированных присадочных и электродных проволок.
Сварку меди
неплавящимся электродом осуществляют на постоянном токе прямой полярности. При
сварке электрод располагают строго в плоскости стыка, наклон электрода 60-80°
"углом назад". При сварке Cu толщиной более 4-5 мм рекомендуется
подогрев до 300-400°.
Присадочные проволоки
из чистой меди М1, М0 при сварке обеспечивают получение металла шва, по составу
и физическим свойствам близкого к основному металлу, однако механические
свойства сварного соединения понижены, наличие пористости уменьшает плотность
металла шва. При введении в состав присадочных проволок раскислителей и
легирующих компонентов механические свойства возрастают, но, как правило,
тепло- и электропроводность металла шва, что в ряде случаев недопустимо. В
таких случаях рекомендуются присадочные проволоки, легированные сильными
раскислителями в микроколичествах, которые после сварки не остаются в составе
твердых растворов, а переходят в свои соединения и образуют высокодисперсные
шлаковые включения и поэтому не влияют на физические свойства металлов.
Составы присадочных
проволок приведены в Табл.7., позволяет получить металл шва с
физическими и механическими свойствами на уровне основного металла М1,
коррозионная стойкость сварных соединений такая же, как у основного металла.
Табл.7.
Марки присадочного металла для сварки меди и ее сплавов неплавящимся
электродом. [2]
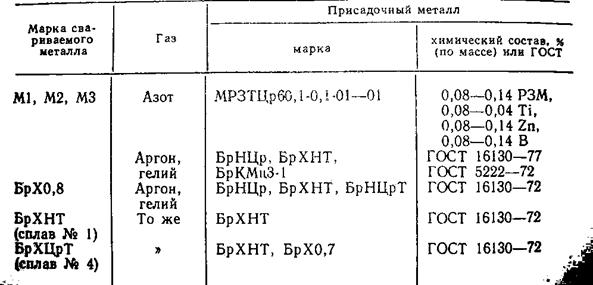
Свариваемость
меди
Общие вопросы
свариваемости определяются влиянием термического цикла сварки на физические
свойства металла: его прочность и пластичность. Для Cu эти свойства будут зависеть от степени ее чистоты. Так, Cu с повышенной концентрацией
водорода может иметь провал пластичности в интервале температур 350-450°С, который для чистой меди обычно не
регистрируется.
Сварка чистой Cu существенно отличается от сварки
сталей в силу особенностей теплофизических свойств этих металлов. Большие
тепло- и температуропроводности Cu создают
высокие градиенты температуры и скорости охлаждения, а также определяют малое
время существования сварочной ванны, что требует применения повышенной погонной
энергии или предварительного подогрева, а это является нежелательным
осложнением технологии сварки. Значительный коэффициент линейного расширения и
его зависимость от температуры вызывают необходимость сварки при жестком
закреплении кромок или по прихваткам. При большой толщине металла следует
регулировать величину зазора при сварке. Малое время существования сварочной
ванны в жидком состоянии ограничивает возможности ее металлургической
обработки. В частности, при раскислении меди требуются более активные
раскислители, чем при сварке сталей.
Особенностью сварки Cu и ее сплавов является склонность
швов к образованию горячих трещин. Кислород, сурьма, висмут, сера и свинец
образуют с медью легкоплавкие эвтектики, которые скапливаются по границам
кристаллитов. Это требует ограничения содержания примесей в меди:
- O2 – до
0,03 %
- Bi – до
0,003 %
- Sb – до
0,005 %
- Pb – до
0,03 %
Для ответственных конструкций
содержание этих примесей должно быть еще ниже. Для особо ответственных изделий
содержание O2 должно быть значительно ниже
менее 0,003% (по массе). Содержание S не должно превышать 0,1 % (по массе).
Вывод
Al, Fe, Ni, Sn, Zn, Ag повышают
прочность и твердость меди и используются для легированных сплавов на медной
основе. Нерастворимые элементы Pb и
Ni ухудшают механические
свойства меди и однофазных сплавов на ее основе. Образуя легкоплавкие
эвтектики, располагающиеся по границам зерен основной фазы, они вызывают
красноломкость. Висмут, будучи хрупким металлом, охрупчивает медь и ее сплавы.
Свинец, обладая низкой прочностью, снижает прочность медных сплавов, однако
вследствие хорошей пластичности не вызывает их охрупчивания. Кроме того, свинец
улучшает антифрикционные свойства и обрабатываемость резанием медных сплавов,
поэтому его применяют для легирования. Нерастворимые элементы O,S, Se, Te присутствуют в меди и ее сплавах в виде промежуточных фаз
(например, Cu2O, Cu2S), которые образуют с медью эвтектики с высокой температурой
плавления и не вызывают красноломкости. Кислород при отжиге меди в водороде
вызывает «водородную болезнь», которая может привести к разрушению металла при
обработке давлением или эксплуатации готовых деталей. Механические свойства
меди в большей степени зависят от ее состояния и в меньшей от содержания
примесей.
Медь обладает высокой
технологичностью. Она прокатывается в тонкие листы и ленту, из нее получают
тонкую проволоку, медь легко полируется, хорошо паяется и сваривается.
Список
литературы
- М.В.Мальцев «Металлография
промышленных цветных металлов и сплавов» (2 изд. Изд-во «Металлургия»,
1970, 364с.)
- Справочник «Сварка и свариваемые
материалы» (Том 1. Изд-во «Металлургия» 1991г.)
- Теория сварочных процессов /Под
ред. В.В. Фролова/. – М.:Высшая школа, 1988.-599 с.
- Технология и оборудование сварки
плавлением /Под ред. Г.Д. Никифорова/,-2-е изд. –М.: Машиностроение,
1986?/ - 320 c.
- Технологические основы сварки и
пайки в авиастроении. /Под ред. В.А. Фролова/. –М.:Интермет-инжиниринг,
2002. -456 с.
- http://www.sak.ru/
- «Материаловедение» учебник для
ВУЗов /Б.Н. Арзамасов, В.И. Макарова, Г.Г. Мухин и др. Под общ. Ред. Б.Н.
Арзамасова, Г.Г. Мухина. -3-е изд., переработ. И доп. – М.:Изд-во МГТУ им.
Н.э. Баумана, 2001. – 648 с., ил.
|