|
Курсовая работа: Переработка вторичного сырья: инструментальных сталей, осколков и пыли на основе твердых сплавов карбида вольфрама
Курсовая работа: Переработка вторичного сырья: инструментальных сталей, осколков и пыли на основе твердых сплавов карбида вольфрама
Федеральное агентство по образованию Московская государственная
академия тонкой химической
технологии им. М.В. Ломоносова
Кафедра химии и технологии редких и рассеянных элементов
Курсовой проект
тема: "Переработка вторичного сырья: инструментальных сталей,
осколков и пыли на основе твердых сплавов карбида вольфрама"
Москва - 2006 г.
ОГЛАВЛЕНИЕ
1. Введение.. 5
2. Цель работы.. 7
3. Литературный обзор. 8
3.1. Основные проблемы
переработки вторичного редко металлического сырья 8
3.2. Источники образования
вторичного сырья. 9
3.3. Классификация вторичного
сырья. 11
3.3.1.
Основные группы.. 11
3.3.2.
Классификация по физическим признакам. 12
3.3.3.
Классификация по химическим признакам. 12
3.3.4.
Газообразные отходы.. 13
3.4.Способы утилизации и
переработки вторичного сырья. 14
3.5. Переработка сплавов редких
элементов. 15
3.5.1.Окислительные
методы.. 15
3.5.2.
Методы хлорирования. 16
3.5.3.Способы
электрохимического растворения отходов. 16
3.5.4.
Гидрометаллургические методы.. 17
4. Исходные данные. 18
4.1. Схема переработки карбида. 18
4.1.1.Аппаратурное
оформление. 19
4.1.2.
Рукавный фильтр. 19
4.1.2.Описание
схемы переработки карбида. 19
4.3. Краткая характеристика
элементов шихты.. 23
4.3.1. WC - Карбид вольфрама [12] 23
4.3.2. WO3 - Оксид вольфрама (VI) [12]. 24
4.3.3.TiC - Карбид титана [12] 24
4.3.4.
ТЮ2 - Оксид титана (IV) [12] 24
4.3.5.Со-Кобальт [12] 25
4.3.6.СоО
- Оксид кобальта (П) [12] 25
4.3.7.Со2О3
- Оксид кобальта (Ш) [12] 26
4.3.8. Zn - Цинк [12] 26
4.3.9.ZnO - Оксид цинка [12] 26
4.3.10.
Си - Медь [12] 27
4.3.11.
Си2О - Оксид меди (I) [12] 27
4.3.12.
СиО - Оксид меди (П) [12] 28
4.3.13. Fe-Железо [12] 28
4.3.14.
ГеО - Оксид железа (II) [12] 29
4.3.15. Fe2O3 -
Оксид железа (Ш) [12] 29
4.3.16.
Бентонит [13] 29
4.4. Термодинамические данные
компонентов сырья. 30
4.4.1.
Расчет термодинамических величин протекания реакций окисления 30
4.4.1.2.
Расчет термодинамических величин протекания реакций окисления [5] 31
5. Материальный баланс. 33
5.1. Блок 2. Грануляция и
окисление в печи кипящего слоя. 33
5.1.1.Запишем
уравнения используя исходные данные и принятые значения 34
5.1.3.
Расчет циклонной пыли. 35
5.1.4.
Количество связующих веществ в исходной шихте. 37
5.2. Окисление карбидов. 37
5.2.1.
Окисление WC: 37
5.2.2.
Окисление TiC: 38
5.2.3.
Окисление Со: 39
5.2.4.
Окисление Zn: 41
5.2.5.
Окисление Си: 42
5.2.6.
Окисление Ге: 43
5.2.7.
Теоретическое количество воздуха. 45
5.5. Блок 5. Прокалка и сушка. 49
6. Тепловой баланс. 50
6.1 Зона кипящего слоя. 50
6.1.1.
Приход тепла зоны кипящего слоя. 50
6.1.2.
Расход тепла. 54
6.1.3.
Определение требуемого избытка воздуха. 55
6.1.4.
Определение размеров сечения печи. 56
6.2. Надслоевая зона. 56
6.2.1.
Приход тепла. 56
6.2.2.
Расход тепла. 57
6.2.3.
Разность между приходом и расходом тепла при 900°С.. 58
7. Печь кипящего слоя. 59
8. Уточнение аппаратурного
оформления. 64
8.1. Щековая дробилка [14] 64
8.2. Дисковая мельница [14] 65
8.3. Гранулятор [14] 66
8.4. Печь кипящего слоя. 66
8.4.1.
Циклон [9] 66
7.4.2.
Рукавный фильтр [8] 67
7.5. Реактор для выщелачивания (с
распыляющимся с верху реагентом) 67
7.6. НУТЧ фильтр [7] 67
8.7.
Колонна осаждения. 68
8.9.Сушильные
аппараты с вращающимися барабанами [7] 68
8.10. Индукционная печь [10] 69
9. Вывод. 70
9. Список литературы... 72
1. Введение
Количество вторичных металлов в мире с каждым годом растет в
связи с непрерывным увеличением общего металлофонда черных и цветных металлов,
который превысил 8 млрд. т. Пропорционально увеличению металлофонда растет
количество амортизационного лома, отходов производства, таких, как пиритные
огарки, тонкие фракции пыли доменных печей, богатые по содержанию ценных
компонентов шлаки цветной металлургии, отходы химической промышленности и т.д.
На машиностроительных и обрабатывающих предприятиях образуются десятки тысяч
тонн стружки и другие отходы [2]. В настоящее время для производства режущих
инструментов широко используются твердые сплавы. Они состоят из карбидов
вольфрама, титана, тантала, сцементированных небольшим количеством кобальта.
Карбиды вольфрама, титана и тантала обладают высокой твердостью,
износостойкостью. Скорости резания инструментами, оснащенными твердыми
сплавами, в 3-4 раза превосходят скорости резания инструментами из быстрорежущей
стали. Недостатком твердых сплавов, по сравнению с быстрорежущей сталью,
является их повышенная хрупкость, которая возрастает с уменьшением содержания кобальта
в сплаве. И, следовательно, возникает вопрос утилизации таких сплавов. Переработка
лома и отходов позволяет вернуть металл в кругооборот [1].
В процессе производственной деятельности образуются отходы,
которые нарушают экологическое равновесие, загрязняя окружающую среду, и
снижают степень извлечения ценных компонентов, содержащихся в исходном сырье.
Их подразделяют на отходы производства и отходы потребления (лом). Под отходами
производства понимают остатки сырья, материалов, полуфабрикатов, образовавшиеся
при производстве продукции и утратившие полностью или частично исходные
потребительские свойства. Под отходами потребления понимают изделия и
материалы, потерявшие потребительские свойства из-за физического или морального
износа. Под вторичным сырьем мы будем подразумевать лишь ту часть отходов,
повторное использование которых технически возможно и экономически целесообразно.
Использование вторичного сырья позволяет решить ряд важнейших проблем:
сохранение невосполнимых природных ресурсов; улучшение экологической
обстановки; снижение капитальных и энергетических затрат; повышение производства
редких металлов; создание малоотходных технологий [2].
Цель данной работы состоит в разработке схемы переработки
вторичного сырья (в данном случае карбидов тугоплавких металлов режущих
инструментов их осколков, кусковые отходы), при заданных производительности и
качестве огарка, температуре обжига и способе подготовки сырья.
В настоящее время подсчеты показали, что удельные
капитальные затраты на сбор и переработку вторичного металла в 25 раз меньше,
чем на производство металла из руды. Производительность труда во вторичной
цветной металлургии примерно в два раза выше, чем в первичной. Сбор и переработка
вторичных металлов имеют не только экономический, но и социальный эффект.
При переработке вторичного сырья коэффициент комплексного
его использования должен быть достаточно высоким, так как задача вторичной
металлургии состоит в одних случаях в разделении металлов, а в других - в
подшихтовке к соответствующим ломам и отходам чистых металлов для получения в
конечном счете качественных сплавов.
Перед металлургической переработкой вторичное сырье нужно
рассортировать, спакетировать или (если это крупногабаритные детали) разрезать
на куски, удобные для шихтовки и дальнейшей переработки. В современной практике
далеко не всегда имеются эффективные способы осуществления этих операций.
При переработке отходов металлургического производства
желательно применение таких процессов, которые сочетались бы с основной
технологией без введения новых типов оборудования и без расхода дополнительных
реагентов. Во многих случаях извлечение металла из вторичного сырья проще, чем
из первичного, поскольку содержание его в отходах значительно выше.
Следовательно, затраты на производство вторичного металла могут быть уменьшены,
что приводит при значительной доле вторичного сырья к снижению себестоимости
продукции в целом и увеличению выпуска редких металлов.
При выборе способа переработки вторичного сырья следует
учитывать, что его состав в большинстве случаев существенно отличается от
первичного. Наличие в нем синтетических материалов, отсутствующих в природе,
загрязнение токсичными и взрывоопасными веществами в процессе эксплуатации
значительно изменяют состав вторичного сырья в количественном и качественном
отношении. Несмотря на существенную принципиальную разницу между первичной и
вторичной металлургией редких металлов, имеются и некоторые общие черты.
Основная из них - сложный состав сырья, поступающего в переработку:
полиметаллические сульфидные руды содержат 10-15 компонентов, имеющих
народнохозяйственное значение, вторичное сырье состоит, как правило, из
трех-четырех компонентов И.
Источниками вторичных сырьевых ресурсов, содержащих редкие и
благородные металлы, являются металлургическая, химическая, электротехническая,
радиотехническая, электронная промышленность, машиностроение и различные предприятия
военно-промышленного комплекса.
Стремительный прогресс во всех сферах материального
потребления требует увеличения производства металла. Развитие техники повлекло
за собой применение новых редких металлов, их сплавов и соединений. Обойтись
без них не могут атомная энергетика, реактивная и космическая авиация,
полупроводниковая техника, современная оптика и другие отрасли промышленности.
Для применения в технике зачастую необходимы металлы высокой степени чистоты.
Требования к чистоте металлов непрерывно повышаются, а следовательно,
совершенствуются и разрабатываются новые методы очистки. Использование бедного
сырья и высокие требования, предъявляемые к качеству конечного продукта -
металла, вызывают усложнение технологии, сочетающей различные пиро- и гидрометаллургические
способы концентрирования, выделения и глубокой очистки редкого металла. На
каждой ступени многостадийной технологической схемы получаются побочные
продукты, содержащие то или иное количество ценного компонента. Вследствие
этого прямой выход металла из первичного сырья мал (иногда не более 40-50%).
Отходы, получаемые на различных стадиях производства (растворы, шламы, кеки,
брак металла и пр), представляют собой материалы, в которых содержание металла
во много раз превышает его содержание в первичном сырье.
Объем отходов, содержащих редкие и цветные металлы и их
сплавы, из года в год возрастает и исчисляется величинами от десятков
килограммов до сотен тысяч тонн в год. Поэтому вопросы рационального и
комплексного использования вторичных сырьевых ресурсов приобретают все большее
значение в общем балансе производства металлов.
Таблица 1. Основные виды вторичного сырья редких металлов.
Источники образования вторичного
сырья
Металлургическая и химическая
промышленность
Электротехническа я, электронная и
радиотехническая промышленность
Машиностроение судостроение
авиационная и космическая промышленность
|
Виды втор.
отходы производства Шлаки, шламы,
пыли, кеки, илы, съемы, золы. Маточные и травильные растворы, отработанные
электролиты. Некондиционные металлы, сплавы, соли
Опилки, сколы, обрезь, высечка,
шлифпорошки. Некондиционные сплавы, соединения, изделия. Бракованные
микросхемы, модули, приборы
Стружки, опилки, шлаки, пыли, высечка,
режущий инструмент. Растворы. Бракованные узлы изделий
|
ганого сырья отходы потребления
Металлургическое оборудование и приборы, выработавшие срок эксплуатации:
печи, насосы, реакторы, контрольно-измерительные и регулирующие приборы
Технологическое оборудование и
приборы, вышедшие из строя в процессе эксплуатации и не подлежащие ремонту
Самолеты, машины, выработавшие
срок эксплуатации. Узлы и агрегаты, заменяемые при ремонте
|
На захоронение или используются в виде строительного
материала; отходы 1 - пыли, шламы, кеки и съемы, растворы, образующиеся в
процессе производства, бракованные металлы, сплавы и соли - в основном содержат
металл и компоненты, которые присутствуют в исходном сырье или введены с
реагентами в процессе его обогащения и переработки. Они могут быть переработаны
на предприятии, производящем данный металл. Более сложными по составу являются
отходы 2 - стружки, опилки, высечка, обрезь, проволока, шлифпорошки, травильные
растворы и особенно отходы 3 - стружка, опилки, бракованные узлы машин,
приборов и механизмов, поскольку в их состав могут входить искусственные
материалы - пластмасса, резина, бумага, отсутствующие в природе. Они содержат в
большом количестве Fe, Ni, Cr (конструкционные материалы), Pb, Sn, Zn (припои), Си и Al (провода). Поэтому переработка отходов 3 вызывает
наибольшие трудности и требует создания новых, специальных технологий для их
обогащения и извлечения ценных компонентов. Еще больше проблем возникает при
переработке вторичного сырья - приборов, машин и аппаратов, бывших в
эксплуатации. Поскольку в процессе эксплуатации может существенно изменяться
вещественный и фазовый состав вторичного сырья (испарение, взаимная диффузия
металлов и др.), возможно накопление токсичных и взрывоопасных соединений,
загрязнение продуктами смазки и окисления. Это требует дополнительных операций,
особенно на стадии обогащения.
Для переработки многокомпонентного вторичного сырья,
разрабатывается, как правило, несколько альтернативных схем. Они подвергаются
опытно-промышленной проверке, а затем выбирается схема, оптимальная по
технико-экономическим, экологическим и другим показателям [2].
Для правильной организации сбора, хранения, обезвреживания,
обогащения и переработки вторичного сырья необходимо знать его состав,
количество и свойства, поэтому различные виды сырья необходимо
классифицировать. Все вторичное сырье делится на три основные группы: 1 -
твердое; 2 - жидкое; 3 - газообразное [2]. .
По физическим признакам отходы цветных металлов делятся на
четыре класса: А - лом и кусковые отходы; Б - стружка, проволока; В -
порошкообразные и пастообразные; Г - прочие отходы
Кроме основных четырех классов существуют специальные классы
для наиболее распространенных видов вторичного сырья: АЛ - лом и отходы
свинцовых аккумуляторов; АК - лом, отходы, покрытые оловом (луженые); 3 -
отходы, содержащие титан, высечка, обрезь; Ж - отходы кабельной промышленности;
Н - отходы катализаторов; Е - ртутьсодержащие отходы; К - отходы щелочных
аккумуляторов [2].
По химическому составу вторичное сырье делится на группы и
марки. Группы характеризуют состав вторичного сырья. Чем больше номер группы,
тем ниже содержание основного компонента и сложнее химический состав. Так, к
первой группе относится черновой вольфрам, содержащий 96-98% W,
ко второй группе - сплав вольфрама с рением (10% Re), а
к третьей группе - отходы твердых сплавов, содержащие до 40% W.
Марки указывают на состав данного вида сырья. Например,
Су-00 - металлическая сурьма; ВР-10 - сплав вольфрама с 10% рения; ВНЖ - сплав
вольфрам (90%), никель (6%), железо (4%); АГО-1 - арсенид галлия.
Кроме классов, групп и марок отходы делят на три сорта:
1-й сорт может быть подвергнут обработке непосредственно без
специальной подготовки и обогащения;
2-й сорт имеет более высокую засоренность неметаллическими
материалами и черным металлом (до 10%);
3-й сорт характеризуется наличием включений черных металлов
и имеет высокую засоренность. Такое сырье требует обязательной первичной
обработки.
На многие виды вторичного сырья, содержащего редкие металлы,
государственный стандарт не разработан, на них имеются отраслевые стандарты
(ОСТ) или технические условия (ТУ), которые служат критерием во взаиморасчетах
предприятий и при выборе технологической схемы обогащения и переработки.
Жидкие виды вторичного сырья также классифицируют, разделяя
на токсичные и нетоксичные; содержащие и не содержащие органические соединения;
кислые, щелочные или нейтральные. Кроме того, жидкие отходы можно
классифицировать по содержанию ценных компонентов: А - богатые травильные
растворы; Б - растворы отработанных электролитов; В - промывные и сточные воды;
Д - маточные растворы. В зависимости от вида жидкого сырья выбирается
соответствующая технологическая схема обезвреживания, обогащения и переработки
[2].
Промышленные газообразные отходы (ПГО) подразделяют на
токсичные и нетоксичные. Причем токсичные газообразные отходы подразделяют на
ПГОх - содержащие токсичные вещества в виде твердых частичек, пыли и ПГОг -
содержащие токсичные вещества в виде паров и газов. ПГОТ, соответственно,
делятся на отходы, содержащие твердые вещества неорганического происхождения -
ПГОТМ (асбест, соли минеральных кислот) и ПГОТО, содержащие пылевидные вещества
органического происхождения. Аналогично ПГОГ могут содержать газообразные
токсические вещества неорганического (ПГОГМ) и органического (ПГОГО)
происхождения. Кроме того, ПГОГОМ могут содержать органические соединения в
состав которых входят фосфор, сера, азот и галогены.
Такая классификация позволяет оценить экологические
особенности данного вида отходов и правильно выбрать способ их обезвреживания и
переработки [2].
Основные этапы переработки вторичного сырья определяются его
видом. Переработка твердых отходов включает:
• контроль радиоактивности, взрывоопасности и токсичности
сырья; •классификацию и выбор способов обогащения и обезвреживания отходов;
разработку экологически чистой, оптимальной схемы извлечения ценных
компонентов из вторичного сырья.
Переработка жидких отходов и промышленных стоков включает:
• входной контроль и обезвреживание токсичных веществ
(цианидов, хрома, ртути, органических веществ);
• нейтрализацию растворов (не обязательна);
• разработку оптимальной схемы обогащения и извлечения
ценных компонентов.
Выбор способа измельчения, обогащения и переработки зависит
от размера перерабатываемого сырья, его состава, требований к конечному
продукту, наличия необходимых реагентов, достаточного количества воды и
соответствующих энергоресурсов (природный газ, электроэнергия, уголь). Кроме
того, учитывается наличие необходимого оборудования, квалификация технического
персонала и рабочих предприятия, на котором планируется проводить обогащение и
переработку.
Особо следует учитывать экологические проблемы. Выбранная
схема должна характеризоваться минимальными объемами твердых отходов и сбросных
растворов, предусматривать улавливание и утилизацию газообразных продуктов; по
возможности не должны использоваться ядовитые вещества (ртуть, кадмий и др.)
[2].
Сплавы редких металлов перерабатывают окислением,
хлорированием, электролизом и гидрометаллургическим способом. Их переработка
осложнена более высоким содержанием других металлов и взаимным влиянием компонентов
сплавов на технологические процессы [2].
Их можно использовать и для переработки сплавов и кусковых
отходов твердых сплавов. Применяемые в настоящее время инструментальные твердые
сплавы базируются на карбидах вольфрама, титана и тантала или на смеси
указанных соединений с добавлением связующего металла - кобальта. К кусковым
отходам твердых сплавов относятся брак производства, неиспользованные части
пластинок инструмента, их осколки и др. В последние годы развивается выпуск
неперетачиваемого твердосплавного инструмента; в связи с этим масштабы
переработки кусковых отходов увеличиваются [2].
1) Распространенный способ переработки кусковых отходов
твердых сплавов - сплавление с NaNOs.
Недостатки способа - значительный расход реагентов, большое
количество циркулирующих растворов, разнообразной специальной аппаратуры,
выделение агрессивных газов (NO, N02) - ограничивают
его применение. Этот метод целесообразно применять на предприятиях, перерабатывающих
вольфрамовые концентраты.
2) Для переработки отходов твердосплавного инструмента на
основе карбидов тугоплавких металлов, содержащих Та, Nb,
W, V, предложено использовать
процесс самораспространяющегося высокотемпературного синтеза (СВС-процесс),
который значительно интенсифицирует вскрытие отходов [2].
3) Окислением кислородом при 900-1000 °С с последующим
выщелачиванием WO3 из продукта обжига растворами соды
или щелочи можно перерабатывать и кусковые отходы твердых сплавов, содержащих
вольфрам [1].
Метод может быть применен для переработки отходов W - Re сплавов, отходов радиоэлектронной
промышленности. При переработке отходов существуют две основные проблемы
экологического характера: полнота использования хлора и использование раствора
сопутствующих металлов.
При хороших технологических показателях следует отметить
громоздкость оборудования для хлорных схем, а также трудности, связанные с
агрессивностью и токсичностью хлора и хлоридов, необходимостью специальных
коррозионностойких материалов для аппаратуры и значительными затратами на
реагенты [2].
Электрохимическое растворение отходов сплавов используют на
отечественных и зарубежных предприятиях. Этот метод наиболее дешев и не требует
сложной аппаратуры. Электрохимическое растворение целесообразно вести в
щелочных растворах, так как образуются легко растворимые соли рения, вольфрама
и молибдена.
Для создания хорошего электроконтакта и компактности отходы
предварительно подготавливают к растворению: порошкообразные отходы и проволоку
брикетируют; проволочные отходы перед брикетированием режут механическими
ножницами и смешивают тонкую и толстую проволоки; отходы прутков и штабиков
рубят на куски, размеры которых не превышают 400 мм. При компоновке анода
брикеты из проволоки, порошкообразных материалов чередуют с отходами
компактного металла [2].
Их можно использовать для переработки ниобиевых сплавов,
содержащих 80-90% Nb, а также пылей от заточки
твердосплавного инструмента.
Технологические этапы переработки ниобиевых сплавов состоят
кислотной обработке, гидрировании, измельчении и сжигании.
Для переработки вольфрам-, молибденсодержащих ниобиевых
сплавов, имеющих состав, %: Nb 94,95; W
3,12; Mo 1,34; Zr 0,42 Та 0,17,
также можно использовать гидрометаллургический способ [2].
Схема. Технологическая схема переработки карбида
окислительным обжигом.
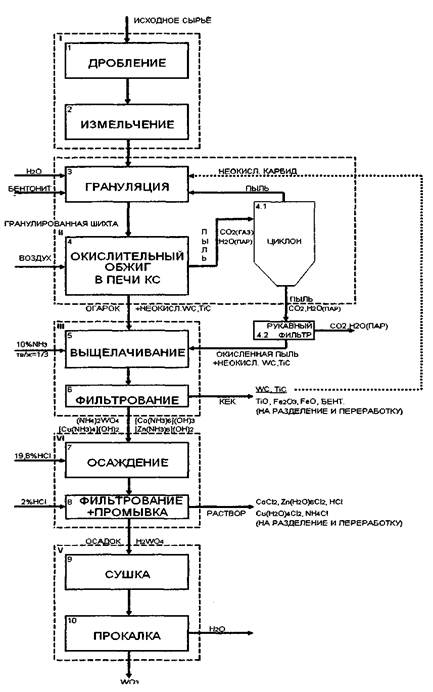
Щековая дробилка.
Дисковая мельница
Грану лятор
Печь кипящего слоя 4.1-Циклон.
Реактор для выщелачивания (с распыляющимся с верху
реагентом)
НУТЧ (вакуумный) фильтр
Колонна осаждения
НУТЧ (вакуумный) фильтр.
Сушильные аппараты с вращающимися барабанами
10-Индукционная печь
4.1.2.1.Дробление и измельчение.
Исходное сырье поступает в щековую дробилку, затем в
дисковую мельницу, где происходит измельчение сырья до нужного размера до 1,0
мм.
4.1.2.2. Грануляция.
После измельчения сырье направляется в чашевой гранулятор.
Грануляция позволяет существенно улучшить показатели обжига в кипящем слое, так
как, во-первых, обеспечивает возможность возврата на грануляцию и затем на
дообжиг в печь кипящего слоя неполно окисленной пыли циклона, во-вторых, при
работе на гранулах значительно возрастает производительность печей. Кроме того,
появляется возможность обжигать в кипящем слое наиболее тонкие концентраты,
которые без грануляции обжигать в печах кипящего слоя не удается из-за слишком
большого пылеуноса. В качестве связки используется бентонит, глина, обладающая
хорошими вяжущими свойствами. Шихта для грануляции содержит 5-6% бентонита,
12-16% воды, остальное концентрат, оборотная пыль и не окислившийся карбид. На
обжиг направляются гранулы крупностью до 2мм. без предварительной сушки [3].
4.1.2.3. Печь кипящего слоя.
Далее идет окислительный обжиг в печи кипящего слоя при
температуре 900°С. Печь кипящего слоя представляет собой шахту цилиндрического
или прямоугольного сечения, выполненную из жароупорного бетона или футерованную
шамотным кирпичом и заключенную в стальной кожух.
В нижней части шахты расположена подина, которая
обеспечивает равномерную подачу воздуха в поперечном сечении печи,
предотвращает просыпание твердой фазы в пространство под подиной. Поды имеют
сопла с колпачками в верхней части, для подвода воздуха и обеспечения
беспросыпности. Общее число сопел устанавливают с таким расчетом, чтобы площадь
живого сечения была 0,3-0,5% от площади пода.
Узел загрузки концентрата состоит га цилиндрического бункера
с установленными под ним тарельчатым питателем. При вращении; тарели лежащий на
ней материал сбрасывается неподвижным ножом в кольцевой желоб, а из последнего
скребками, закрепленными на тарели, - в выгрузочную тачку. Далее концентрат
через герметичный шлюзовой питатель, предотвращающий выброс газов из печи, и
загрузочную трубу непрерывно подается непосредственно в кипящий слой. Скорость
загрузки равна производительности тарельчатого питателя и определяется
расстоянием между нижним срезом бункера и тарелью (устанавливается о помощью
подвижной обечайки), а также скоростью вращения тарели. Воздух в печь кипящего
слоя подается воздуходувками.
Огарок из кипящего слоя непрерывно пересыпается через
разгрузочное отверстие, низший край которого (порог выгрузки) расположен на
уровне 1000-1500 мм над подиной, накапливается в бункере. Питатель периодически
выгружается в контейнеры. При обжиге гранулированного материала огарок
периодически выгружается через течку, расположенную непосредственно над
подиной.
Запыленные газы выходят из печи через отверстие,
расположенное под сводом. Основная часть пыли обычно улавливается циклонами.
Для глубокой очистки газов от тонких частиц пыли, могут использоваться рукавные
фильтры с рукавами из стеклоткани. Очищенные газы вентилятором выбрасываются в
атмосферу.
Устойчивая работа печи обеспечивается с помощью систем
автоматического регулирования и контрольно-измерительных приборов. Наиболее
сложной и ответственной является система автоматического регулирования
температуры обжига путем изменения скорости загрузки в печь концентрата. Эта
система состоит из установленной в кипящем слое термопары,, пишущего
потенциометра о реостатным датчиком, нелинейного регулятора, исполнительного
механизма и двигателя постоянного тока с независимым возбуждением, являющегося
приводом тарельчатого питателя. При повышении температуры в печи исполнительный
механизм увеличивает силу тока в цепи возбуждения двигателя и одновременно
уменьшает напряжение, подаваемое на якорь, что приводит к снижению числа
оборотов тарели; при понижении температуры скорость вращения тарели увеличивается.
Отношение максимальной скорости загрузки к минимальной равно 5. Отклонения температуры
обжига от заданной не превышают ± 2,5°С. Автоматически поддерживаются
постоянными расход воздуха и разрежение под сводом печи [3].
4.1.2.4. Выщелачивание.
Огарок и пыль рукавного фильтра после окисления поступают в
реактор для выщелачивания. Сверху шахты емкости распыляется 10%МНз при
температуре 40°С с отношением тв/ж=1/3. При этом оксиды Ti,
Fe; карбиды W, Ti и бентонит будут в осадке, а W, Co, Zn, Си перейдут в раствор.
4.1.2.5.Фильтрация.
Раствор и осадок после выщелачивания отфильтровываются на
НУТЧ фильтре. Осадок идет на разделение и извлечение Ti,
Fe; карбиды возвращаются на грануляцию, а раствор
перекачивается из-за разности давлений в сборник и идет на следующую стадию.
4.1.2.6. Осаждение вольфрамовой кислоты.
Раствор содержащий целевые вещества в различных их
соединениях обрабатывается 19,8% НС1 кислотой при 40°С. При этом будет
образовываться осадок вольфрамовой кислоты, а все остальное будет находиться в
растворе.
4.1.2.7.Фильтрация.
Раствор и осадок после осаждения отфильтровываются на НУТЧ
фильтре, при этом идет дополнительное введение 2%НС1 для отмывки вольфрамовой
кислоты и кислота направляется на сушку и прокалку. Раствор, содержащий аква
комплексы Со, Zn, Си пойдет на дальнейшее разделение,
предположительно методом экстракции.
4.1.2.8.Сушку и прокалку.
Ведем процесс во вращающихся печах при температуру
750-800°С. Вода упаривается при сушке, а конечный получается после прокаливания
W03.
4.1.2.9. Аппаратурно-технологическая схема.
Схема 2. Аппаратурно-технологическая схема переработки
сплава карбидов окислительным обжигом в печи кипящего слоя.
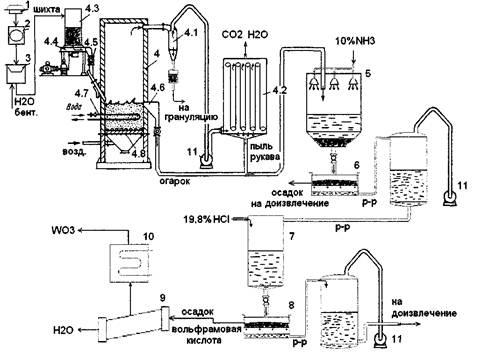
Щековая дробилка
Печь кипящего слоя
Чашевой гранулятор
Дисковая мельница 4.1-Циклон
Рукавный фильтр
Бункер
Тарельчатый питатель
Шлюзовый питатель
Порог выгрузки
Система водяного охлаждения
Подина
Реактор выщелачивания (с распыляющимся с верху реагентом)
ПУТЧ фильтр
Шахтная емкость осаждения (колонна осаждения)
НУТЧ фильтр.
Сушильные аппараты с вращающимися барабанами.
10-Индукционная печь 11-Насос
4.2. Состав исходного сырья
Таблица 2. Состав исходного сырья.
|
WC |
TiC |
Со |
Zn |
Си |
Fe |
всего |
кг/ч |
130,000 |
25,000 |
10,000 |
0,500 |
1,000 |
0,167 |
166,667 |
% |
78,000 |
15,000 |
6,000 |
0,300 |
0,600 |
0,100 |
100 |
4.3.1. WC - Карбид
вольфрама [12]
Молекулярная масса: 195,86
Получаются прокаливанием смеси W и С
при 1400-1500°С.
Физические и химические свойства, tnn WC свыше 3000°С; плотность WC 15,6 г/см3.
Нерастворимы без разложения ни в одном из известных
растворителей.
Применение: в производстве твердых сплавов.
Внешний вид: серые кристаллы
4.3.2. WO3 - Оксид
вольфрама (VI) [12].
Парамагнитные желтые (оранжевые при нагревании) ромбические
мелкие кристаллы (плотность равна 7,16-7,22 г/смЗ), которые плавятся при
1473°С, превращаясь в зеленую жидкость, кипящую при 1750°С. Они сублимируются,
начиная от 1357°С. Мало растворимы в воде и кислотах. Растворяется в расплавах
и растворах щелочей с образованием вольфраматов или поливольфраматов. Получают
нагреванием металлического вольфрама при 900°С на воздухе или в токе кислорода,
а также прокаливанием вольфрамовой кислоты H2WO4. Применяют в химической, стекольной и керамической
промышленности для получения металлического вольфрама и его сплавов.
4.3.3.TiC - Карбид
титана [12]
tun свыше 3000 °С. Карбид титана,
обладающий высокой твердостью и тугоплавкостью, является компонентом
жаропрочных и твердых инструментальных сплавов, абразивный материал, его
используют для нанесения износостойких покрытий, для изготовления различных
керамических изделий, в т. ч. тиглей и чехлов термопар, стойких к расплавленным
металлам, для футеровки вакуумных высокотемпературных печей.
Встречается в природе в виде минерала рутила, анатаза
(тетрагональные кристаллы) и брукита (ромбические кристаллы). Белый порошок. tra=1870°C, tKtni=30000C, плотность равна 3,6-3,95 г/см3 (анатаз), плотность равна
4,1-4,2 г/см3 [2] (брукит), плотность равна 4,2-4,3 г/см3 [2] (рутил).
Разлагается выше 2927°С. Мало растворим в воде, разбавленных кислотах или
растворах щелочей. Растворяется в концентрированной серной кислоте при
нагревании, в расплавах гидроксидов или карбонатов щелочных металлов. Получают
сжиганием металлического титана в избытке кислорода. Применяют в качестве
пигмента для пластических масс, масляных красок, при производстве молочного
стекла, тугоплавких стекол, фарфора, огнеупорного кирпича, в производстве
эмалей, глазурей. В реакциях органической химии служит в качестве катализатора.
Электронная формула KL3s23p63d74s2, еион (Ме<=>Ме++е) =7,86 эВ.
Степень окисления: (+1), +2, (+3, +4); валентность: (1), 2,
(3,4)
Физические свойства: серебристо-серый с розоватым оттенком
металл, tra=1494°C,
1кип=2960°С, плотность кобальта 8,90 г/см3
Распространенность в природе: содержание в земной коре
410"3%(масс)
Основной минерал: кобальтин CoAsS
(кобальтовый блеск).
Получение: из руд пиро - и гидрометаллургическими методами.
В частности на конечной стадии смесь оксидов кобальта восстанавливается
углеродом в электропечах.
Химические свойства: малоактивный металл. Устойчив к
действию сухого и влажного воздуха. Растворяется в разбавленных кислотах. При
нагревании реагирует с кислородом, галогенами, азотом, серой и другими
неметаллами.
Серовато-зеленый кристаллический порошок с решеткой типа NaCl.1ПЛ=1935°С, плотность равна 6,45 г/см. Устойчив до
2860°С. Мало растворим в воде и других растворителях. Проявляет основные
свойства. Восстанавливается до металлического кобальта водородом, углеродом, серой,
алюминием. Получают действием кислорода или паров воды на металлический кобальт
при температуре выше 940°С, разложением СозСч или СоаОз, прокаливанием
гидроксида, сульфата, нитрата кобальта (П). Применяют для изготовления
отрицательных электродов аккумуляторов, для получения окрашенных стекол,
фарфора и эмалей, в качестве катализатора.
Черные гексагональные мелкие кристаллы. Плотность равна 5,34
г/см3. Устойчив в виде моногидрата. Превращается в СозСч при 265°С, в СоО при
940°С с выделением кислорода. Окисляет хлороводородную кислоту с выделением
хлора. Восстанавливается водородом или метаном. Получают дегидратацией Со20з nt^O или прокаливанием нитрата
кобальта (П) при 180°С. Применяют как пигмент для эмалей и глазурей.
4.3.8. Zn - Цинк [12]
Электронная формула KLM4s2, Еион(Ме=>Ме++е) =9,39 эВ
Степень окисления: +2; валентность: 2
Физические свойства: серебристо-белый с голубоватым оттенком
мягкий металл,
U =1809°C, tjonr^OOCfC, плотность равна 7,13
г/см3
Распространенность в природе: содержание в земной коре
8,010"3%(масс)
Основные минералы: сфалерит (цинковая обманка) ZnS
Получение: из руды пирометаллургическим и
гидрометаллургическим способом
Химические свойства: малоактивный металл, проявляет
амфотерные свойства. Реагирует с неметаллами, водой, кислотами, щелочами.
4.3.9.ZnO - Оксид цинка
[12]
Встречается в природе в виде минерала цинкита. Диамагнитные
кристаллы со структурой вюртцита белого цвета. tnn=1969°C, плотность равна 5,70 г/см3. Мало растворим в воде.
Растворяется в кислотах и щелочах. Обладает люминесцентными и фотохимическими
свойствами. При нагревании восстанавливается углеродом, монооксидом углерода,
водородом. В лаборатории может быть получен сжиганием металлического цинка или
прокаливанием гидроксида, карбоната или нитрата цинка. Применяют для
приготовления масляных красок, для получения некоторых препаратов, используемых
в медицине и косметике, в резиновой и керамической промышленности, а также в
качестве катализатора при синтезе метанола.
Электронная формула KLM4S1, Еи0н(Ме<=>Ме++е) =7,72 эВ
Степень окисления: +1, +2, (+3); валентность: 1,2, (3)
Физические свойства: мягкий блестящий металл красноватого
цвета, 1Ш =1085°С,
1кип=2540°С, плотность меди 8,94 г/см3
Распространенность в природе: содержание в земной коре
4,710"3%(масс)
Основные минералы: халькопирит CuFeSi,
халькозин (медный блеск) CuiS, малахит Си2(ОН) 2СОз,
встречается также в свободном состоянии (самородная медь).
Получение: из руд пирометаллургическим и
гидрометаллургическим способом. В пирометаллургическом способе медь получается
при нагревании смеси оксида и сульфида меди(1). В гидрометаллургическом -
восстановлением железом (металлическим ломом) из раствора медного купороса.
Встречается в природе в виде минерала куприта. Диамагнитные
кубические кристаллы, цвет которых меняется от коричневого до
карминово-красного. tnn=1238°C.
Мало растворим в воде. Растворяется в аммиаке или галогеноводородах. При 1025°С
превращается в СиО, выше 1050°С - термически диссоциирует на элементы. Можно
получить обработкой солей меди (II) щелочами или
карбонатами щелочных металлов в присутствии восстановителя. Применяют в
керамической промышленности в качестве пигмента.
Встречается в природе и называется черной медью, мелаконитом
или теноритом. Парамагнитный черный порошок (или черные кубические кристаллы). tnn=1335°C, 1пл=1026°С, плотность
равна 6,45 г/см3. Мало растворим в воде. Растворяется в концентрированных
кислотах, при нагревании или в иодиде аммония. Растворяется в стекле, эмалях,
придавая им зеленовато-синюю окраску. Восстанавливается до меди водородом,
монооксидом углерода, металлами. Получают нагреванием меди выше 80°С, водной суспензии
гидроксида меди (П), прокаливанием нитрата или основного карбоната меди.
Применяется в производстве стекла и эмалей в качестве пигмента, в микроанализе
для определения углерода, водорода и азота в органических соединениях.
4.3.13. Fe-Железо [12]
Электронная формула KL3s23p63d64s2, ЕиОН(М<=>Ме++е) =7,90 эВ.
Степень окисления: +2, +3, (+4, +6, +8);
валентность: 2,3, (4,6, 8).
Физические свойства: серебристо-серый твердый металл, tim=1539°C, 1кип=3200°С, плотность
железа 7,87 г/см3.
Распространенность в природе: четвертый (после О, Si, A1) по распространенности в
земной коре элемент (4,65%(масс))
Основные минералы: магнетит РезО4, гематит Рб20з, лимонит
Рв2Оз хН2О
Получение: восстановлением железной руды коксом или оксидом
углерода (II).
Химические свойства: металл средней химической активности.
Окисляется при обычной температуре во влажном воздухе. Растворяется в
разбавленных кислотах. При нагревании реагирует с неметаллами.
Диамагнитный черный неустойчивый кристаллический порошок.
Решетка типа NaCl. tm=13680C. Превращается в при нагревании на воздухе. Мало растворим в
воде и щелочах. Растворяется в кислотах. Разлагает при нагревании воду.
Получают окислением металлического железа, восстановлением оксида железа (Ш) СО
или водородом, прокаливанием смеси Рб2Оз и порошка железа.
4.3.15. Fe2O3 - Оксид железа (Ш) [12]
Самое устойчивое природное кислородсодержащее соединение
железа, которое встречается в виде минералов гематита или красного железняка.
Существует три модификации: a-Fe2O3 (парамагнитна), у-Ре2Оз (ферромагнитна), 8-Ре2Оз
(ферромагнитна). а-Ре2Оз представляет собой красный порошок. tra=1562°C [1], плотность равна 5,24 г/см3. Мало растворим в воде.
Растворимость в кислотах зависит от температуры и продолжительности
прокаливания оксида перед растворением. Получают прокаливанием гидроксида или
нитрата железа (III), карбоната, сульфата железа (П)
или пирита на воздухе. Применяется как пигмент для изготовления красок.
Бентониты представляют собой монтмориллонитовую породу общей
формулы:
(Cao,5Na) oj(Al,Mg,Fe) 4(Si,Al) 802o(OH)
4nH2
и являются разновидностью белых или сукновальных глин.
Характеризуются рядом ценных свойств, таких, как высокая набухаемость в воде,
способность сохранять приданную форму, тонкая дисперсность, обладают моющей,
эмульгирующей, клеящей, загущающей способностями, что обусловливается
свойствами ведущего минерала этих глин - монтмориллонита; последний
подразделяют на щелочной - с высоким содержанием Na2O и щелочноземельный - содержащий преимущественно CaO, MgO.
Известно о применении бентонитовых глин в качестве
загустителей печатных красок при набивке шелковых тканей активными и кубовыми
красителями.
Таблица 3. Типовой химический состав бентонита.
Таблица 4. Термодинамические данные компонентов сырья [5].
Со203 |
159 |
- |
19,3 |
8Д |
-2,4 |
Си |
0 |
1085 |
5,41 |
1,5 |
_ |
СиО |
39,5 |
1026 |
9,27 |
4,8 |
- |
Си20 |
40,76 |
1238 |
14,9 |
5,7 |
- |
Zn |
0 |
1809 |
5,43 |
2,4 |
- |
ZnO |
83,4 |
1969 |
11,71 |
1,22 |
-2,18 |
Fe |
0 |
1539 |
9,0 |
- |
- |
FeO |
63 |
1368 |
12,38 |
1,62 |
-0,38 |
Fe203 |
197,51 |
1562 |
31 |
1,76 |
- |
C02 |
94,05 |
. |
10,55 |
2,16 |
-2,84 |
H20 |
57,795 |
- |
7,17 |
2,56 |
-2,84 |
02 |
0 |
- |
7,52 |
0,81 |
-0,9 |
N2 |
0 |
. |
6,66 |
1,02 |
_ |
|
|
|
|
|
|
4.4.1.1.Основные реакции протекающие при обжиге.
WC + 2,5О2 = WO3
+ СО2
TiC + 2О2 = ТЮ2 + СО2 3) Со +
0,5О2=СоО 4) Zn + 0,5O2= ZnO 5) 2Cu+0,5O2
= Cu2O 6) Ре+1,5О2 = Ре2Оз
0,5Cu2O +%О2
= CuO
2СоО + 0,5О2 = Со2О3
Fe + 0,5О2 = FeO
ДН7з=ЛН298+298Р173*ЛСр*с1Т
AHi173=AH298+
а*(1173-298) +1/2* Ь*10'3*(1173-298) 2 - с*105*1/Т
1) WC + 2,502 = W03
+ СО2
ДН298=-20146-94,05+9,67= - 285840 кал/моль
АСр=(17,58+10,55-2,5*7,52-12,27) +(6,79+2,16-2,5*0,81-2,06)
*10-3*Т+(0-2,04 + 0,9 *2,5+ 2,68) *105/Т2=-2,94+4,86*10"3*Т+2,89*107Т2
AHii73=-285840-2,94*875+4,86*10'3*1287125/2-2,89*105*(-0,0025)
= - 284553,8= - 1190,5кДж/моль
2) TiC + 2О2 = TiO2
+ СО2 ДН298=-225,8-94,05+43,9= - 245950 кал/моль
АСр=(17,97+10,55-2*7,52-13,296) +(0,28+2,16-2*0,81+1,944)
*10-3*Т+(-4,35+2,04+4,212+0,912) *105/Т2=0,184+2,764*10-3*Т+2,35*105/Т2
АНц7з=-245950+0,184*875+2,764*10-3*1287125/2-2,35*105*(-0,0025) = - 243423,0= -
1018,5кДж/моль
3) Со + 0,5О2=СоО
АН298==-57100 кал/моль
АСр= (11,54-3,3-7,52/2) +(2,04-5,86-0,81/2)
*10'3*Т+(0,4+0,9/2) *105/Т2= 4,48-4,22*
10-**Т+0,85*105/Т2
АНП7з= - 57100
+4,48*875-4,22*10'3*1287125/2-0,85*105*(-0,0025) =
-55683,3= - 232,9кДж/моль
4) Zn + 0,5O2
= ZnO
AH298=-83400 кал/моль
ДСр=(11,71-5,43-7,52/2) +(1,22-0,81/2-2,4)
*10-3*Т+(-2Д8+0,9/2) *105/Т2= 2,52-1,58*
1(Г*Т-1,73*105/Т2
ЛНц7з= - 83400 +2,52*875-1,58*10-3*1287125/2+1,73
*105*(-0,0025) =
-82644= - 345,8кДж/моль
5) 2Cu+0,502 = Cu20
ДН298=-40760 кал/моль
АСр(14,9-2*5,41-7,52/2) +(5,7-2,15-0,81/2) *10-3*Т+(0+0,9/2)
*105/Т2= 0,32+2,29*
1(И*Т+0,45*105/Т2
ДН„73= - 40760 +0,32*875+2,29*10-3*1287125/2-0,45*105*(-0,0025)
=
-38893,7= - 162,7кДж/моль
6) Ре+1,5О2 = Ре2Оз
АН298=-197510 кал/моль
АСр=(31/2-9-1,5/2*7,52) +(1,76/2-1,5/2*0,81)
*10'3*Т+(0+0,9*1,5/2) *105/Т2= 0,86+0,272*
10^*Т+0,675*105/Т2
АНц7з= - 197510 +0,86*875+0,272*10-3*1287125/2-0,675*105*(-0,0025)
=-821,787кДж/моль
7) 0,5Си20 + У4О2 = СиО АН298=-18620 кал/моль
ACp(9,27-14,9/2-7,54/4)
+(4,80-5,7/2-0,81/4) *10'3*T+(0+0,9/4) *105/T2=-0,06+1,75* 10-з*т+052о*ю5АГ2
АНц7з= - 18620 - 0,06*875+1,75*10-3*1287125/2-0,
20*105*(-0,0025) = - 17496,26= - 73,2кДж/моль
8) 2СоО + 0,5О2 = Со2О3 АН298=-22400 кал/моль
АСр (19,3/2-11,54-7,52/4) +(8,1/2-2,04-0,81/4)
*10'3*Т+(-2,4/2-0,4+0,9/2) *105/Т2= - 3,77+1,807*
10'% -1,15*105Я2
АНц7з=-22400-3,77*875+1,807*10"3*1287125/2+1,15*105*(-0,0025)
=
-24248,332= - 101,455кДж/моль
9) Fe + 0,5О2 = FeO
ДНаэв^-бЗООО кал/моль
ACp=(12,38-4,18-7,52/2) +(l,62-5,92-0,81/2) *10'3*T+(-0,38+0,9/2)
*105/T2= 4,44-4,7* 10'3*Т+0,07*105/Т2 AHii73=-63000+4,44*875-4,7*10'3*1287125/2-0,07*105*(-050025)
=
-62122= - 259,9кДж/моль
Схему переработки можно разбить на 5 блоков:
Дробление и измельчение.
Грануляция и окисление в печи кипящего слоя.
Выщелачивание и фильтрация.
Осаждение и фильтрация.
Прокалка и сушка.
Схема 3. Блок схема процесса переработки карбида.
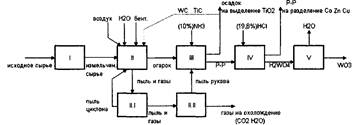
Производительность по поступающему сырью - 4т. в сутки,
т.е.166,667 кг. в час. В блок 1 поступает исходное сырье, где дробится и
измельчается.
В блок 2 поступает измельченное сырье не более 1 мм., где
смешивается с не прореагировавшими карбидами и гранулируется. Крупность гранул
- до 2мм.; распределение по крупности,% (масс) [3].:
(2-Й,5 мм) - 15(1,0+0,5 мм) - 35(1,5-1,0 мм) - 350,5 мм. -15
Продуктами обжига являются огарок 65%, циклонная пыль20%,
пыль рукавного фильтра 15%. В огарок переходит 65% карбида, в циклонную пыль20%
карбида, в пыль рукавного фильтра 15% карбида.
Степень окисления карбида в циклонной пыли 90%, в пыли
рукавного фильтра 99%, необходима степень окисления в огарке 98%. Металлы Со, Zn, Cu, Fe
окисляются нацело. Пыль рукавного фильтра и огарок поступают на выщелачивание,
а пыль циклона идет на грануляцию. Не прореагировавший карбид также
возвращается на грануляцию, т. к. при дальнейшем разделении присутствует как
балласт.
Для расчета материального баланса нам необходимо знать
состав исходной шихты для обжига.Т. к. после первого блока сырье гранулируется
и смешивается с возвратным карбидом и пылью циклона, его состав и количество
изменяются.
Таблица 5. Обозначение потоков.
Наименование потока |
Обозначение |
Значение кг/ч |
Первичное сырье |
ХО |
166,667 |
Шихта для обжига |
Х1 |
273,638 |
Возвратный карбид ог. |
Х21 |
2,082 |
Возвратный карбид рук. |
Х211 |
3, 202 |
Пыль циклона карбид |
Хк221 |
0,24 |
Пыль циклона оксид |
Хо221 |
30,992 |
Связующая вода |
ХН20 |
38,36 |
Связующий бентонит |
Хбент. |
13,152 |
Схема 4. Потоковая схема процесса окисления карбидов.
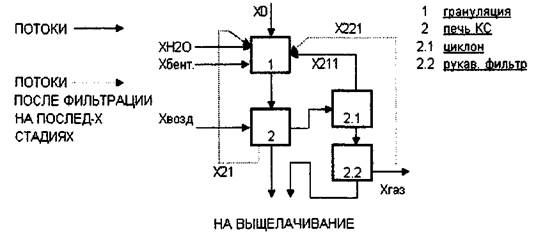
Xi=Xo+XK2i i+XO2l 1+X21+X221
Хо=166,67
Хк211=0,2*0,1 *(0,78+0,15) *Xi
X2i=0,65*0,02*(0,78+0,15) *X1
X22i=0,15*0,01*(0,78+0,15)
*Xi
0,1 - доля не окислившегося карбида в циклоне
0,02 - доля не окислившегося карбида в огарке
0,01 - доля не окислившегося карбида в рукаве
Получим:
Хк211=0,019*Xi
X2i=0,012*X!
Х221=0,001*Х!
Решение:
X1-0,019*Xi-0,012*X1-0,001*X1=166,67
0,968*Х1=166,67
Ху=172Л8 (без оксидов и связующих компонентов)
5.1.2Расчет потоков:
Поток Хк2ц равен:
Хи„=3, 202
Найдем количества веществ в этом потоке:
Xk2ii(WC): 0,2*0,78*0,1*172,18=2,686
ХииСТЮ): 0,2*0,15*0,1*172,18=0,516
Поток X2i
равен:
Х2] =2,082
Найдем количества веществ в этом потоке:
X2i(WC): 0,65*0,02*0,78*172,18=1,746
X2i(TiC): 0,65*0,02*0,15*172,18=0,336
Поток X22i
равен:
X22i(WC): 0,15*0,01*0,78*172,18=0, 201
X22i(TiC): 0,15*0,01*0,15*172,18=0,039
Количество карбида окисляемого в циклоне в виде металлов
(Со, Zn, Cu, Fe),
(кг/ч): 3, 202*(0,06+0,006+0,003+0,001) /(0,78+0,15) = 0,241
Количество оксидов в циклоне без учета оксидов поступающих
из шихты:
X'o22i = 0,2 *0,9*Xi=30,992
Количества оксидов, (кг/ч):
По реакции (1) WO3:
0,78*30,992*231,82/195,86=28,612
По реакции (2) ТЮ2: 0,15*30,992*79,88/59,84=6, 206
По реакции (3) СоО: (0,06*(30,992+0,241)) *74,93/58,93=2,383
По реакции (4) ZnO:
(0,06*(30,992+0,241)) *81,39/65,39=0,233
По реакции (5) Си2О: (0,06*(30,992+0,241))
*143,1/2*63,55=0,105
По реакции (6) Fe2O3:
(0,06*(30,992+0,241)) *231,55/2*55,85=0,065
Суммарное количество оксидов, (кг/ч): 37,604
Таблица 6. Количество оксидов в циклоне без учета оксидов
поступающих из шихты.
|
W03 |
ТЮ2 |
СоО |
ZnO |
Cu2O |
Fe203 |
всего |
кг/ч |
28,612 |
6, 206 |
2,383 |
0,233 |
0,105 |
0,065 |
37,604 |
% |
76,088 |
16,504 |
6,337 |
0,620 |
0,279 |
0,173 |
100 |
Итоговое количество оксида в шихте:
Хо2ц=37,604+0,2*Хо2ц
0,8*Х211=37,604
Xo2i
1=47,005 кг/ч
Количество оксида приходящее из шихты в циклон:
0,2*Xo2i
1=9,401 кг/ч
Состав и количество приходящих в циклон оксидов их шихты,
(кг/ч):
WO3: 9,401*0,761=7,154
ТЮ2: 9,401*0,165=1,551
СоО: 9,401*0,063=0,592
ZnO: 9,401*0,006=0,056
Cu20: 9,401*0,003=0,028
Fe2O3: 9,401*0,003=0,019
Итоговое суммарное состав и количество оксидов, (кг/ч):
WO3: 7,154 + 28,612=35,766
ТЮ2: 1,551+6, 206=7,757
СоО: 0,592+2,383=2,975
Си20: 0,028+0,105=0,133
ZnO: 0,056+0,233=0,289
Fe2O3: 0,019+0,065=0,084
Количество WC в шихте, (кг/ч):
166,67*0,76+1,746+2,686+0, 201=134,636 Количество ТЮ в шихте, (кг/ч):
166,67*0,15+0,516+0,336+0,039=25,531 Количество шихты без связующих веществ,
(кг/ч): 166,67+47,005+0,24+2,082,3, 202=219, 199
Количество связующих веществ 219, 199*(14%+6%) /80%:
Н2О: 219, 199*0,14/0,8=38,360 кг/ч Хшо=3 8,360 кг/ч
Бентонита: 219, 199*0,06/0,8=16,440кг/ч Распределение
бентонита, (кг/ч):
огарок: 16,440*0,65=10,686
пыль циклона: 16,440*0, 20=3,288
пыль рукавного фильтра: 16,440*0,15=2,466 Хбент. =16,440 -
3,288=13,152
Таблица 7. Состав шихты поступающей на обжиг.
WC |
ТЮ |
Со |
Zn |
Си |
Fe |
W03 |
ТЮ2 |
СоО |
ZnO |
Си2О |
Fe2O3 |
Н2О |
бенг |
всего |
кг/ч 134,636% 49, 202 |
25,531 9,330 |
10,000 3,654 |
1,000 0,365 |
0,500 0,183 |
ОД 67 0,061 |
35,766 13,071 |
7,757 2,835 |
2,975 1,087 |
0,289 0,106 |
0,133 0,049 |
0,084 0,031 |
38,360 14,019 |
16,440 6,008 |
273,638 100,000 |
Распределение компонента, (кг/ч):
огарок: 134,636*0,65=87,513
пыль циклона: 134,636*0, 20=26,927
пыль рукавного фильтра: 134,636*0,15=20, 195
Основная реакция: WC + 2.5О? = WCb + ССЬ
М=195,86 М=16 М=231,82 М=44,01 (г/моль)
1) в огарке окислится: 26,927*0,9= 85,763 кг/ч Расходуется
кислорода, (кг/ч):
02: 85,763*2,5*2*16/195,86=17,515
Образуется веществ, (кг/ч):
С02: 85,763*44,01/195,86=19,272
WO3: 85,763*231,82/195,86=101,509
Оксида WO3 в исходной шихте, (кг/ч):
47,005*0,65*0,761=23,251
Суммарное количество WOs, (кг/ч):
124,76
2) в циклоне окислится: 26,927*0,9=24,234 кг/ч Расходуется
кислорода, (кг/ч):
О2: 24,334 * 2,5*2*1,6/195,86 = 4,949 Образуется веществ,
(кг/ч): СО2: 24,334*44,01/195,86=5,445
WO3: 28,612
Оксида WO3 в исходной шихте, (кг/ч):
47,005*0,2*0,761=7,154
Суммарное количество WO3, (кг/ч):
35,76
3) в рукаве окислится: 20, 195*0,99=19,993 кг/ч
Расходуется кислорода, (кг/ч):
О2: 19,993*2,5*2*16/195,86=4,083
Образуется веществ, (кг/ч):
СО2: 19,993*44,01/195,86=4,492
W03: 19,993*231,82/195,86=23,664
Оксида WO3 в исходной шихте, (кг/ч):
47,005*0,15*0,761=5,366
Суммарное количество WO3, (кг/ч):
29,03
Распределение компонента, (кг/ч):
огарок: 25,531*0,65=16,595
пыль циклона: 25,531*0, 20=5,106
пыль рукавного фильтра: 25,531*0,15=3,830
Основная реакция: TiC + 2OZ = TIP? + СО?
M=59,84 M=16
М=79,88 М=44,01 (г/моль)
1) в огарке окислится: 16,595* 0,98=10,787 кг/ч Расходуется
кислорода, (кг/ч):
02: 10,787*2*2* 16/59,84=5,768 кг/ч
Образуется веществ, (кг/ч):
ТЮ2: 10,787*79,88/59,84=14,399
СО2: 10,787*44,01/59,84=7,933
Оксида ТЮ2 в исходной шихте, (кг/ч): 47,005*0,65*0,165=5,042
Суммарное количество ТЮ2, (кг/ч): 12,975
2) в циклоне окислится: 5,106*0,9 =3,319 кг/ч Расходуется
кислорода, (кг/ч):
О2: 3,319*2*2*16/59,84=1,331
Образуется веществ, (кг/ч):
СО2: 3,319*44,01/59,84=2,441
ТЮ2: 6, 206
Оксида ТЮ2 в исходной шихте, (кг/ч): 47,005*0,
20*0,165=1,551
Суммарное количество ТЮ2, (кг/ч): 12,975
3) в рукаве окислится: 3,830*0,99=2,498 кг/ч Расходуется
кислорода, (кг/ч):
02: 2,489*2*2*16/59,84=1,331
Образуется веществ, (кг/ч):
ТЮ2: 2,489*79,88/59,84=3,322
С02: 2,489*44,01/59,84=1,831
Оксида ТЮ2 в исходной шихте, (кг/ч): 47,005*0,15*0,165=1,163
Суммарное количество ТЮ2, (кг/ч): 4,485
Распределение компонента, (кг/ч):
огарок: 10*0,65=6,5
пыль циклона: 10*0,2=2,0
пыль рукавного фильтра: 10*0,15=1,5
Реакции: а) Со + 0.5От= СоО
М=58,93 М=16 М=74,93 (г/моль)
б) 2СоО + 0.5О7 = CozCb М=74,93 М=16
М=165,86 (г/моль)
Весь СоО оседает в циклоне, а Со2Оз образуется в огарке и
пыли рукавного фильтра. СоО приходящий с исходной шихтой (оборотный) окисляется
до Со2Оз нацело.
1) в огарке окислится: 6,5кг/ч По реакции (а):
Расходуется кислорода, (кг/ч):
О2: 6,5* 16/58,93=1,765 Образуется веществ, (кг/ч):
Считаем, что СоО из шихты образуется 100% -98%=2%: 6,5*
2%=0,13
Из этого СоО по реакции (б) не будет доокисляться:
0,13*74,94/58,93=0,165
СоО: 6,5*74,93/58,93=8,265
По реакции (б):
Расходуется кислорода, (кг/ч):
О2: 8,965*16/165,86=0,865 Образуется веществ, (кг/ч):
СогО3: (8,265-0,165) * 165; 86/2*7,493=8; 965
Оксида СоО в исходной шихте, (кг/ч): 47,005*0,65*0,063=1,934
Со203: 1,934*165,86/2*7,493=2,140 Суммарное количество Со2Оз, (кг/ч): 11,105
2) в огарке окислится: 2,0 кг/ч
В циклоне окисление идет до СоО.
Расходуется кислорода, (кг/ч):
О2: 2,0*16/58,93=0,543
Образуется веществ, (кг/ч):
СоО: 2,383
Оксида СоО в исходной шихте, (кг/ч): 47,005*0,
20*0,0,063=0,592
Суммарное количество СоО, (кг/ч): 2,975
3) в рукаве окислится: 1,5 кг/ч По реакции (а):
Расходуется кислорода, (кг/ч):
О2: 1,5*16/58,93=0,407 Образуется веществ, (кг/ч):
Считаем, что СоО из шихты образуется 100% -99%=1%: 1,5*
1%=0,015
Из этого СоО по реакции (б) не будет доокисляться:
0,015*74,94/58,93=0,019
СоО: 1,5*74,93/58,93=1,907
По реакции (б):
Расходуется кислорода, (кг/ч):
О2: (1,907 - 0,019) * 16/165,86=0,182
Образуется веществ, (кг/ч):
Со2О3: (1,907-0,019) * 165,86/2*74,93=2,091
Оксида СоО в исходной шихте, (кг/ч): 47,005*0,15*0,063=0,444
Со203: 0,444*165,86/2*74,93=0,492
Суммарное количество Со2Оз, (кг/ч): 2,583
Распределение компонента, (кг/ч):
огарок: 1,0*0,65=0,65
пыль циклона: 1,0*0, 20=0, 20
пыль рукавного фильтра: 1,0*0,15=0,15
Основная реакция: Zn + 0,50? = ZnO
М=65,39 М=16 М=81,39 (г/моль)
1) в огарке окислится: 0,65 кг/ч Расходуется кислорода,
(кг/ч):
О2: 0,65*16/65,39=0,159 Образуется веществ, (кг/ч):
ZnO: 0,65*81,39/65,39=0,809
Оксида ZnO в исходной шихте, (кг/ч):
47,005*0,65*0,006=0,188 Суммарное количество ZnO,
(кг/ч): 0,997
2) в циклоне окислится: 0,2 кг/ч Расходуется кислорода,
(кг/ч):
02: 0,2*16/65,39=0,049 Образуется веществ, (кг/ч):
ZnO: 0,233
Оксида ZnO в исходной шихте, (кг/ч):
47,005*0, 20*0,006=0,056 Суммарное количество ZnO,
(кг/ч): 0,289
3) в рукаве окислится: 0,15кг/ч Расходуется кислорода, (кг/ч):
02: 0,15*16/65,39=0,037 Образуется веществ, (кг/ч):
ZnO: 0,15*81,39/65,39=0,187
Оксида ZnO в исходной шихте, (кг/ч):
47,005*0,15*0,006=0,043 Суммарное количество ZnO,
(кг/ч): 0,230
Распределение компонента, (кг/ч):
огарок: 0,5*0,65=0,325
пыль циклона: 0,5 *0, 20=0,1
пыль рукавного фильтра: 0,5*0,15=0,075
Реакции: а) 2Си + 0.5О2 = СшО
М=63,552 М=16 М=143,1 (г/моль)

По реакции (а): Расходуется кислорода, (кг/ч): О2:
0,325*16/63,552*2=0,041 Образуется веществ, (кг/ч): Си2О:
0,325*143,1/63,55*2=0,366
Оксида Си2О в исходной шихте, (кг/ч):
47,005*0,65*0,003=0,086
Из исходной шихты Си2О окисляется до СиО нацело. Из
окислившегося Си2О по реакциям не будет окисляться до СиО 100% -98%=2%:
0,366*2%=0,007кг/ч Отношение распределения образования оксидов: Cu20/CuO = 2/1 0,366*0,98=0,359 кг/ч
следовательно образуется: Си2О=0,244 кг/ч и 0,122 кг/ч идет на доокисление до
СиО Суммарное количество Си2О, (кг/ч): 0,007+0,244=0,251
По реакции (б):
Расходуется кислорода, (кг/ч):
О2: 0,232*1/4*32/79,56=0,023
Образуется веществ, (кг/ч):
СиО: (0,122+0,086) *79,55/143,1* 1/2=0,232
2) в циклоне окислится: 0,1 кг/ч
Будем считать, что реакция идет до образования Си2О.
Расходуется кислорода, (кг/ч):
02: 0,1*16/2*63,55=0,013
Образуется веществ, (кг/ч):
Си20: =0,105
Оксида Си2О в исходной шихте, (кг/ч): 47,005*0,
20*0,003=0,028
Суммарное количество Си2О, (кг/ч): 0,133
3) в рукаве окислится: 0,075кг/ч По реакции (а):
Расходуется кислорода, (кг/ч):
О2: 0,075*169/2*63,55=0,009 Образуется веществ, (кг/ч):
Си2О: 0,075*143,1/63,55*2=0,084
Оксида Си2О в исходной шихте, (кг/ч):
47,005*0,15*0,003=0,002
Из исходной шихты Си2О окисляется до СиО нацело. Из
окислившегося Си2О по реакциям
не будет окисляться до СиО 100% -99%=2%: 0,084*1%=0,001кг/ч
Отношение распределения образования оксидов: Cu20/CuO = 2/1
0,084*0,99=0,083 кг/ч следовательно образуется:
Си2О=0,056 кг/ч и 0,028 кг/ч идет на доокисление до СиО
Суммарное количество Си2О, (кг/ч): 0,001+0,056=0,057
По реакции (б):
Расходуется кислорода, (кг/ч):
О2: 0,053*1/4*32/79,55=0,005
Образуется веществ, (кг/ч):
СиО: (0,028+0,133*0,15) *79,55=0,005
Распределение компонента, (кг/ч):
огарок: 0,167*0,65=0,108
пыль циклона: 0,167*0,2=0,033
пыль рукавного фильтра: 0,167*0,15=0,025
Реакции: a) Fe + 0.50? = FeO
М=55,85 М=16 М=71,85 (г/моль)

1) в огарке окислится: 0,108 кг/ч
Отношение распределения образования оксидов: РеаОз/ FeO =3/1=0,081/0,027
По реакции (а):
Расходуется кислорода, (кг/ч):
О2: 0,027*16/55,85=0,008
Образуется веществ, (кг/ч):
FeO: 0,027*71,85/55,85=0,035
По реакции (б):
Расходуется кислорода, (кг/ч):
02: 0,081*1,5*32/55,85*2=0,04
Образуется веществ, (кг/ч):
FeiOs: 0,081*159,7/2*55,85=0,116
Оксида FeiOs в исходной шихте,
(кг/ч): 47,005*0,65*0,002=0,065
Суммарное количество Ре2Оз, (кг/ч): 0,181
2) в циклоне окислится: 0,033кг/ч
В циклоне окисление идет до РеаОз.
Расходуется кислорода, (кг/ч):
О2: 0,033*1,5*32/55,85*2=0,014
Образуется веществ, (кг/ч):
РегОз =0,065
Оксида Ре2Оз в исходной шихте, (кг/ч): 47,005*0,
20*0,002=0,019
Суммарное количество Ре2Оз, (кг/ч): 0,084
1) в огарке окислится: 0,025 кг/ч
Отношение распределения образования оксидов: РезОз/ FeO =3/1=0,019/0,006
По реакции (а):
Расходуется кислорода, (кг/ч):
О2: 0,006*16/55,85=0,002
Образуется веществ, (кг/ч):
FeO: 0,006*71,85/55,85=0,008
По реакции (б):
Расходуется кислорода, (кг/ч):
О2: 0,019*1,5*32/55,85*2=0,008
Образуется веществ, (кг/ч):
FeiOs: 0,019*159,7/2*55,85=0,027
Оксида Ре2Оз в исходной шихте, (кг/ч):
47,005*0,15*0,002=0,013
Суммарное количество Ре2Оз, (кг/ч): 0,04
Суммарное количество кислорода, (кг/ч): 35,03 + 9,939 +
11,563 + 3,55 + 2,662 + 1,765 + 0,865 + 0,543 + 0,407 + 0,182 + 0,159 + 0,049 +
0,037+0,023+0,013+0,009+0,005+0,003+ 0,008+ 0,014+0,002+0,008=75,043
Теоретический расход воздуха (из расчета. Оа - 23% по массе)
75,043*0,23=326,274 кг/ч
Количество азота: 326,274 - 75,043= 251,231 кг/ч
Количество влаги, вносимое с воздухом при Т=20°С и
относительной влажности 80%
(содержание влаги "0,012 кг. на 1кг. сухого воздуха):
326,274* 0,012 = 3,915 кг/ч
Теоретический расход влажного воздуха (кг/ч)
326,274 + 3,915 = 330,189 кг/ч.
Таблица 8. Состав огарка.
|
WC |
ТЮ |
Со |
Zn |
Си |
Fe |
WO3 |
ТЮ2 |
СоО |
ZnO |
Си2О |
Fe203 |
H20 |
Бент. всего |
кг/ч |
1,746 |
0,336 |
0 |
0 |
0 |
0 |
124,760 |
12,975 |
0,165 |
0,997 |
0,251 |
0,181 |
0 |
10,686 163,469 |
% |
1,068 |
0, 206 |
0 |
0 |
0 |
0 |
76,320 |
7,937 |
0,101 |
0,610 |
0,154 |
0,111 |
0 |
6,537 100,000 |
СиО FeO |
|
0,232 0,035 |
|
0,142 0,021 |
|
|
|
|
|
|
|
|
|
|
|
|
|
|
|
|
|
Таблица 9. Состав циклонной пыли.
|
WC |
TiC |
Со |
Zn |
Си |
Fe |
WO3 |
ТЮ2 |
СоО |
ZnO |
Си2О |
Fe2O3 |
Н2О |
Бент. |
всего |
кг/ч |
2,686 |
0,516 |
0 |
0 |
0 |
0 |
35,766 |
7,757 |
2,925 |
0,289 |
0,133 |
0,084 |
0 |
3,288 |
53,444 |
% |
5,026 |
0,965 |
0 |
0 |
0 |
0 |
66,922 |
14,514 |
5,473 |
0,541 |
0,249 |
0,157 |
0 |
6,152 |
100,000 |
Таблица 10. Состав пыли рукавного фильтра.
|
WC |
TiC |
Со |
Zn |
Си |
Fe |
WO3 |
ТЮ2 |
СоО |
ZnO |
Си2О |
Fe2O3 |
H2O |
Бент. |
всего |
кг/ч |
0, 201 |
0,039 |
0 |
0 |
0 |
0 |
29,030 |
4,485 |
0,019 |
0,230 |
0,057 |
0,040 |
0 |
2,466 |
39,211 |
% |
0,513 |
0,099 |
0 |
0 |
0 |
0 |
74,035 |
11,438 |
0,048 |
0,587 |
0,145 |
0,102 |
0 |
6,289 |
100,000 |
|
|
|
|
|
|
|
|
|
|
|
|
|
|
|
|
СиО |
FeO |
|
0,053 |
0,008 |
|
0,135 |
0,020 |
|
|
|
|
|
|
|
|
|
|
|
|
|
|
|
|
|
|
|
Таблица 11. Состав газов.
N2 кг/ч 251,231 |
Н2О 42,275 |
СО2
41,414
|
всего 334,920 |
% 75,012 |
12,622 |
12,365 |
100,000 |
Таблица 12. Материальный баланс обжига.
Г |
Приход |
|
Об |
разуется |
|
Вещество |
кг/ч |
% |
Вещество |
кг/ч |
% |
WC |
134,636 |
22,366 |
WC |
4,633 |
0,786 |
TiC |
25,531 |
4,241 |
TiC |
0,891 |
0,151 |
Со |
10,000 |
1,661 |
|
|
|
Zn |
1,000 |
0,166 |
WO3 |
189,556 |
32,172 |
Си |
0,500 |
0,083 |
ТЮ2 |
25,217 |
4,280 |
Fe |
0,167 |
0,028 |
СоО |
3,109 |
0,528 |
|
|
|
Со203 |
13,688 |
2,323 |
W03 |
35,766 |
5,941 |
ZnO |
1,516 |
0,257 |
ТЮ2 |
7,757 |
1,289 |
Си20 |
0,441 |
0,075 |
СоО |
2,975 |
0,494 |
СиО |
0,285 |
0,048 |
ZnO |
0,289 |
0,048 |
Fe203 |
0,305 |
0,052 |
Си2О |
0,133 |
0,022 |
FeO |
0,043 |
0,007 |
Fe203 |
0,084 |
0,014 |
|
|
|
|
|
|
бент |
16,440 |
2,790 |
бент |
16,440 |
2,731 |
|
|
|
H20 |
40,424 |
6,715 |
H20 |
40,424 |
6,861 |
|
|
|
N2 |
251,231 |
42,640 |
02 |
75,043 |
12,466 |
C02 |
41,414 |
7,029 |
N2 |
251,231 |
41,734 |
|
|
|
Всего |
601,976 |
100 |
Всего |
589, 193 |
100 |
|
|
Нее
пр
|
язка от ихода |
12,783 |
2,124 |
тшо: 3,036*МШо/201,38=0,270
тшо: 0,594*МШо/165,54=0,065
тшо: 0,178*МШо/165,54=0,019 Остаток воды:
547,236-21,251=525,985 кг.
Количество NH3 пошедшее на реакции,
(кг/ч):
тотв: 201,227*2*MNH3 (17)
7303,3=22,557
тшз: 0,520* 6*МШЗ /211,93=0,250
тшз: 34,980*12* Мню /211,93=33,670
ткш: 3,036* 6*МШЗ /201,38=1,537
тшз: 0,594*4* Мынз /165,54=0,240
6) тщз: ОД78* 4*МШЗ /165,54=0,078 Остаток NH3:
60,804-58,324=2,480 кг.
Таблица 13. Материальный баланс выщелачивания.
Приход |
Образуется |
Вещество WC |
кг/ч 1,947 |
% 0,236 |
Вещество (NH4) 2WO4 |
кг/ч 201,227 |
% 25,084 |
|
TiC |
0,375 |
0,046 |
[Co(NH3) 6] (OH) 3 |
35,500 |
4,425 |
|
WO3 |
153,790 |
18,662 |
[Zn (NH3) 6] (OH) 2 [Cu (NH3) 6j (OH) 2 |
3,036 0,774 |
0,378 0,096 |
|
|
|
|
|
|
|
|
|
Продолжение таблицы.
ТЮ2 |
17,460 |
2,119 |
|
|
|
СоО |
0,184 |
0,022 |
WC |
1,947 |
0,243 |
Со203 |
13,688 |
1,661 |
TiC |
0,375 |
0,047 |
ZnO |
1,227 |
0,149 |
|
|
|
Cu20 |
13,688 |
1,661 |
ТЮ2 |
17,460 |
2,177 |
CuO |
0,285 |
0,035 |
Fe203 |
0,221 |
0,028 |
Fe2O3 |
0,221 |
0,027 |
FeO |
0,043 |
0,005 |
FeO |
0,043 |
0,005 |
|
|
|
|
|
|
бент |
13,152 |
1,639 |
бент |
13,152 |
1,596 |
|
|
|
|
|
|
|
|
|
NH3 |
60,804 |
7,378 |
NH3 |
2,480 |
0,309 |
H20 |
547,236 |
66,404 |
H20 |
525,985 |
65,568 |
Всего |
824,100 |
100 |
Всего |
802,2 |
100 |
|
|
|
Невязка от прихода |
21,900 |
2,657 |
mCu(H20) 4ci2: (0,594+0,178) Mcu(mo) 4 012
206,44/165,54 = 0,963
mcocn: 7,756 M 7,756 Mc0ci2129,83/165,25=
6,093
Количество МНЦ С1, (кг/ч):
(165,765*2*53,5/249,85) +(7,756*6*53,5/165,28)
+(3,683*6*53,5/244,28) +(0,963* 4*53,5/
206,44) =91,891
Количество поглощаемой реакциями H2O, (кг/ч):
(3,683*4*18/244,28) +(0,963*2*18/206,44)
+(6,093*0,5*18/129,83) =1,676
Количество образующейся Н2О, (кг/ч):
7,756*3*18/165,765=2,527
Количество Н2О, приходящее с кислотой, (кг/ч):
Состав кислоты 19,8% НС1 80,2% Н2О
Количество требуемого НС1, (кг/ч):
(165,765*2*36,45/249,85) + (7,756 * 9 * 36,45 / 165,28) +
(3,683 * 8 * 36,45/244,28) +(0,963*6*36,45/206,44) =69,177
Приходящей с кислотой Н2О, (кг/ч):
69,177*0,802/0, 198= 280, 202
Суммарное количество приходящей Н2О, (кг/ч):
280, 202+525,985=806,187
Суммарное количество уходящей Н2О, (кг/ч):
806,187+2,527-1,676=807,03 8
Таблица 14. Материальный баланс осаждения.
Приход |
Образуется |
|
|
|
|
|
|
|
Вещество |
кг/ч |
% |
Вещество |
кг/ч |
% |
|
(NH4) 2 WO4 |
201,227 |
18,033 |
H2W04 |
165,765 |
15,414 |
|
[Co(NH3) 6] (OH) 3 |
35,500 |
3,181 |
Zn(H2O) 6Cl2 |
3,683 |
0,342 |
|
[Zn (NH3) 6] (OH) 2 |
3,036 |
0,272 |
Си(Н2О) 4С12 |
0,963 |
0,090 |
|
[Си (NH3) 6] (OH) 2 |
0,774 |
0,069 |
СоС12 |
6,093 |
0,567 |
|
|
|
|
NH4C1 |
91,891 |
8,545 |
|
НС1 |
69,177 |
6, 199 |
|
|
|
|
Н2О |
806,187 |
72,245 |
Н20 |
807,038 |
75,043 |
|
Всего |
1115,901 |
100 |
Всего |
1075,433 |
100 |
|
|
|
Невя: |
ка от прихода |
40,468 |
3,626 |
|
|
|
|
|
|
|
|
|
WOs получают термическим разложением
H2WC4 при 750-800 °С
При прокалке идет следующая реакция:
H2WO4^WO3+H2O
Количество продуктов, (кг/ч):
Масса WO3 =153,79 (кг/ч)
Масса Н2О = 165,765-153,76= 11,075 (кг/ч)
Вывод: полученная нарастающая с каждой стадией невязка до
3,626% вызвана погрешностью расчетов.
6.1.1.1. Физическое тепло при Т= 20°С.
Теплоемкость шихты:
WC
Ср=12,27+2,06*10'3283 - 2,68 *105 * 1/283 =9,51 Дж/моль*град
С = 9,51 * 1000/195,86= 84,12 Дж/кг*град
WO3
Ср=17,58 + 6,79 * 10 - 3*283=19,5 Дж/моль * град
С =19,5 *1000/231,82= 84,12 Дж/(кг * град)
TiC
Ср = 13,29 - 1,94*10" 3*283-4,21*10 *1/2832 = 7,47
Дж/моль*град
С = 7,47 *1000/59,84 = 124,8 Дж/кг*град
TiO2
Ср=17,97+0,28*10"3 * 283 - 4,35 * 105 /2832 = 12,54
Дж/моль*град
С = 12,54* 1000/79,88 = 156,98 Дж/кг*град
Со
Ср=3,3+5,86 * 10"3 *283= 4,95 Дж/моль*град
С =4,96 * 1000/58,93=84,17 Дж/кг*град
СоО
Ср= 11,5 + 2,04* 10'3 * 283+0,4 * 105/2832 = 12,62
Дж/моль*град
С = 12,62 * 1000/74,93=168,42 Дж/кг*град
Со203
Ср= 19,3+8,1*10"3 *283-2,4*105/2832 =18,59 Дж/моль*град
0=18,59*1000/165,86=112,08 Дж/кг*град
Zn
Ср=5,43 + 2,4 * 10"3 *283=6,11 Дж/моль*град
С=6,11*1000/65,39=93,44 Дж/кг*град
ZnO
Ср= 11,71 + 1,22 * 10"3 *283-2,18 * 105/2832 =9,33
Дж/моль*град
0= 9,33 * 1000/81,39 = 114,63 Дж/кг*град
Си
Ср=5,41 + 1,5 10"3 *283 = 5,83 Дж/моль*град С=
5,83*1000/63,55=91,74 Дж/кг*град
Си2О
Ср= 14,9 + 5,7 *10"3 *283 = 16,51 Дж/моль*град
С = 16,51 * 1000/143,1 = 115,37 Дж/кг*град
CuO
Ср = 9,27 + 4,80* 10"3 *283= 10,628 Дж/моль*град
С = 10,628 * 1000/79,55 = 133,606 Дж/кг*град
Fe
Ср = 9,0 Дж/моль*град
С = 9,0* 1000/55,85=161,14 Дж/кг*град
FeO
Ср = 12,38 +1,62*10"3 *283-0,38*105*1/2832=12,364
Дж/моль*град
С =12,364*1000/71,85=172,081 Дж/кг*град
Fe203
Ср = 31+1,76*10"3 *283=31,5 Дж/моль*град
С = 31,5*1000/159,7=197,24 Дж/кг*град
Бентонит (Al2O3*4SiO2*2H2O)
Ср=(109,3+4*46,9+2*46,9) +(18,4+434,3+2*30,0) * 10"3
*283 - (30,4+17,9+27,3) * 105*1/2832 = 357,3 Дж/моль*град С = 945,5 Дж/кг*град
бентонит (A12O3*4SiO2*2H2O)
рассчитываем, как сумму теплоемкостей составляющих оксидов:
АСр(109,3+4*46,9+2+46,9) +(18,4+4*34,3+2*30)
*10'3*Т-(30,4+17,9+27,3) *105/Т2= 390,7*
10-**283-75,6*105/2832=357,3=945,5Дж/кг*град
Н2О
Теплоемкостыгринимаем равной 4184 Дж/кг*град
Средняя аддитивная теплоемкость шихты, (Дж/кг*град):
С=(48,55*0,49202+84,12*0,13071+124,8*0,09330+156,98*0,02835+84,17*0,03654+168,42*
0,01087+93,44*0,00365+114,63
*0,00106+91,74*0,00183+115,37*0,00049+161,14*0,00061+
197,24*0,00031+945,5*0,06008+4184*ОД4019):
100=700,04Дж/кг*град
Физическое тепло шихты при 20°С Ккал/ч:
700,04*273,638*20*10"3 =3831,15
6.1.1.2. Физическое тепло воздуха
Исходим из содержания в воздухе кислорода азота и паров
воды. Для 100°С
теплосодержания равны, (кДж/нм3): 131,7; 129,5 и 150,5 В
пересчете на 1 кг и Т=20°С,
кДж/кг.:
Кислород: 131,7*(20/100) *(22,4/32) =18,4
Азот: 129,5*(20/100) * (22,4/28) = 20,7
Пары воды: 150,5*(20/100) *(22,4/18>= 37,5 Физическое
тепло воздуха, кДж/ч:
18,4*75,043+20,7*251,231+37,5*3,915=6728,085 Теплосодержание
воздуха при 20°С ккал/кг: 6728,085/330,189=20,376
6.1.1.3. Тепло реакции окисления:
реакция 1: Окисление WC
ЛН1173=-1190,5 кДж/моль
Теплота окисления 1 кг WC
Q wc= 1190,5 *134,636*1000/195,86=818360,860 кДж/кг
реакция2: Окисление TiC
ДНц7з=-1018,5 кДж/моль
Теплота окисления 1 кг TiC
Q Tlc = 1018,5*25,531*1000/59,84=434547,526 кДж/кг
реакция 8: Окисление Со
ДН117з=-248,55 кДж/моль
Теплота окисления 1 кг Со
Q со = 248,55
*10,0*1000/58,93=42177,16 кДж/кг
реакция 4: Окисление Zn
ДН1Ш=-345,782 кДж/моль
Теплота окисления 1 кг Zn
Q zn = 345,782 * 1,0* 1000/65,39=5287,995 кДж/кг
реакция 11: Окисление Си
АНц7з=-162,7 кДж/моль
Теплота окисления 1 кг Си
Q Си= 162,7 *0,5*
1000/63,55=1280,094 кДж/кг
реакция 14: Окисление Fe
АНП73=-821,787 кДж/моль
Теплота окисления 1 кг Fe
QFe= 821,787 *0,167* 1000/55,85=2457,268
кДж/кг
реакция 12: Доокисление Си2О до СиО
ДН1173=-73,2 кДж/моль
Q сио= 73,2*1000*0,133/79,55=122,383
кДж/кг
реакция 9: Доокисление СоО до Со20з
ДНП73=-101,455 кДж/моль
Qco2o3=
101,455*1000*0,2,975/165,86=1819,779 кДж/кг
6.1.1.4Суммарный приход тепла.
Q =
3831,15+6728,085+818360,860+434547,526+42177,16+5287,995+1280,094+2457,268+
122,383+1819,779= 1316612,300 кДж/ч
6.1.2.1. Тепло уносимое огарком.
Средняя теплоемкость огарка, (Дж/кг*град):
О
(48,55*0,01068+124,8*0,00206+84,12*0,7632+156,98*0,07937+168,42*0,00101+112,08*
0,06793+114,63*0,0061+115,37*0,00154+133,606*0,00142+197,24*0,00111+172,081*0,00021+
945,5*0,06537) /1=148,348
Тепло уносимое огарком при 900°С, (кДж/ч):
148,348*10-3*900*163,469=21825,269
6.1.2.2. Тепло уносимое пылью.
Средняя теплоемкость пыли, (Дж/кг*град):
C=((48,55*0,05026+84,12*0,66922+124,8*0,00965+156,98*0,14514)
/l) +((48,55*0,00513+
84,12*0,74035+124,8*0,00099+156,98*0,11438+168,42*0,00048+18,59*0,06587+114,63*
0,00587+115,37*0,00145+133,606*0,00135+197,24*0,00102+172,081*0,0002+945,5*0,06289)
/!) =239,954
Тепло уносимое огарком при 900°С, (кДж/ч): 239,954*10'3
*900*92,655=20009,644
6.1.2.3. Тепло уносимое газами.
Теплосодержания компонентов газов при600°С равны, (кДж/нм3):
азот - 803,6 углекислый газ - 1228,8 вода - 968,0
Теплосодержания компонентов газов в пересчете на 900°С
равны, (кДж/кг):
азот: 803,6*900*22,4/600*28=964,32
углекислый газ: 1228,8*900*22,4/600*44,01=938,143
вода: 968,0900*22,4/600*18= 1806,93
Тепло уносимое газами при 900°С, (кДж/ч):
964,32*251,231+938,143*41,414+1806,93*42,275=357507,298
6.1.2.4. Затраты тепла на испарение воды в шихте.
Для нагрева воды от 20°С до 100°С затрачивается 2591,6 кДж.
Теплосодержания водяного пара при 100°С равно 150,5 кДж/нм3
150,5*22,4/18=187,2 кДж/ч
Тогда дополнительные затраты тепла на испарение воды
составляют, (кДж/кг):
2591,6-187,2=2404,4
Дополнительные затраты тепла на испарение воды составляют,
(кДж/ч):
2404,4*38,36=92232,784
6.1.2.5. Потери тепла через стены.
Условно принимаем, что потери тепла через стены составляет
3% от прихода тепла, (кДж/ч): 1316612,300*0,03=39498,369
6.1.2.6. Суммарные потери тепла.
Q =
21825,269+20009,644+357507,298+92232,784+39498,369=531073,364 кДж/ч
6.1.2.7Избыток тепла при теоретическом расходе воздуха
Q =
1316612,300-531073,364=785538,936 кДж/ч
6.1.3.1. Теплосодержание воздуха при 900°С.
Количество влаги 0,012кг. на 1кг. сухого воздуха (Oi-23%, N2-77%), следовательно 1кг. влажного воздуха будет
содержать: кислорода: 0,23*1/1,012=0,227 азота: 0,77*1/1,012=0,761 водяного
пара: 0,012*1/1,012=0,012
Теплосодержание кислорода при 600°С составляет 849,9
кДж/нм3, в пересчете на 900°С: 849,9*900*22,4/600*32=892,395 кДж/кг
Теплосодержание воздуха при 900°С, (кДж/кг):
0,027*892,395+0,761 *964,32+0,012* 1806,93=779,625
Количество тепла, расходуемого на нагревание 1кг. воздуха от
20°С до 900°С, кДж: 779,625-20,376=759,249
6.1.3.2. Необходимый избыток воздуха.
785538,936/759,249=1034,626 кг/ч
6.1.3.3. Суммарный расход воздуха.
330,189+1034,626=1364,815 кг/ч Коэффициент избытка воздуха:
1364,815/330,189=4,13
При обжиге в кипящем слое гранул крупностью до 2мм.,
оптимальный расход составляет 750 нм3/ч*м2 Оптимальный расход воздуха,
выраженный в кг/ ч*м2 определим, приняв среднюю молекулярную массу воздуха
равной 29 г/моль:
750*29/22,4=970,982
Площадь пода печи, м2: S=1364,815/970,982=1,4
примем 1,5
Для определения размеров сечения принимаем, что шахта имеет
вид окружности с радиусом:
S=rcR2,
отсюда R2=S/n
=1,5/3,14=0,477 следовательно R= V0,477=
0,69м. В соответствии с этим расстояние между точками загрузки и выгрузки
равна: В=2К=1,38м.
6.2.1.1. Физическое тепло пыли и газов.
20009,644+357507,298+785538,936=1163055,878 кДж/ч
6.2.1.2. Тепло окисления.
Первичной пыли в циклонной пыли 1/3 от всей, степень окисления
47% на выходе из кипящего слоя, отсюда доля не окисленных реагентов 53%. В
рукавном фильтре остается 1% компонентов пыли.
WC в первичной пыли, (кг/ч):
циклон: 24,234*0,53*1/3=4,281
рукав: 19,993*0,01=0, 199
Суммарное количество пыли окисляемое в надслоевой зоне,
(кг/ч): 4,48
TiC в первичной пыли, (кг/ч):
циклон: 3,319*0,53*1/3=0,586
рукав: 2,489*0,01=0,025
Суммарное количество пыли окисляемое в надслоевой зоне,
(кг/ч): 0,611
Тепло выделяемое при окислении в надслоевой зоне:
WC
АН! 173=-1190,5 кДж/моль
Q=l 190,5*
1000/195,86=6078,32 кДж/ч
TiC
ДНц7з=-1018,5 кДж/моль
д=1018,5*1000/59,84=17020,388кДж/ч
Суммарное количество тепла,(кДж/ч):
Q=27051,942+10399.457=37451,399
6.2.1.3. Приход тепла в надслоевой зоне.
1163055,878+37451,399=1200507,277 кДж/ч
Так как количества окисляющихся компонентов в надслоевой
зоне незначительны, примем, что количество тепла уносимое пылью и газами из
слоя и из печи одинаковы и равны И63055,878 кДж/ч.
6.2.2.1. Потери тепла через стены и свод.
Примем, что потери тепла через стены и свод равны 3% от
прихода тепла в надслоевую зону: 1200507,277*0,03=36015,218 кДж/ч
6.2.2.2. Суммарный расход тепла.
1163055,878+36015,218=1199071,096 кДж/ч
1200507,277-1199071,096=1436,181 кДж/ч
Вывод: Невязка - 0,12% от прихода тепла, следовательно
температура отходящих газов определена с достаточной точностью.
Как показали расчеты площадь пода равна 1,5м2. Для расчета
печи с такой площадью пода нужна спец литература. Целью данной работы не
является данный расчет, и рисунок 1., представленный ниже, является
приблизительной копией нужной печи кипящего слоя. Рисунок 1. Печь кипящего слоя
[4].
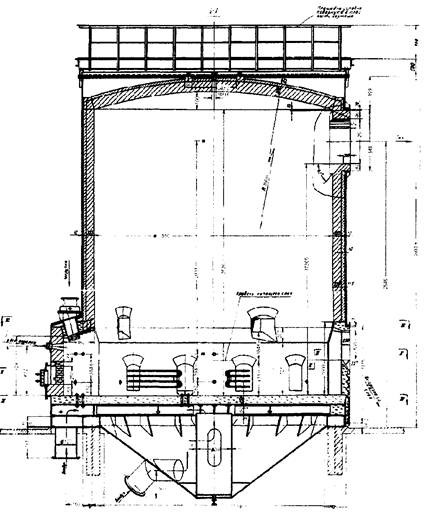
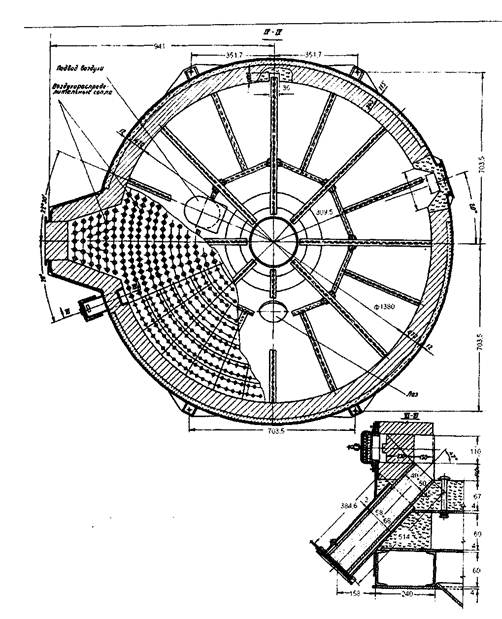
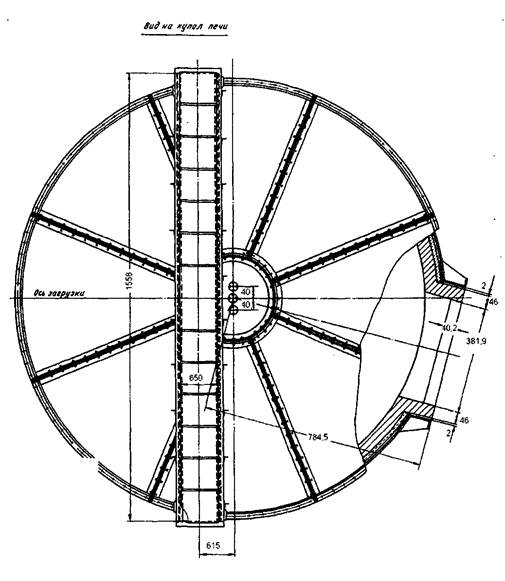
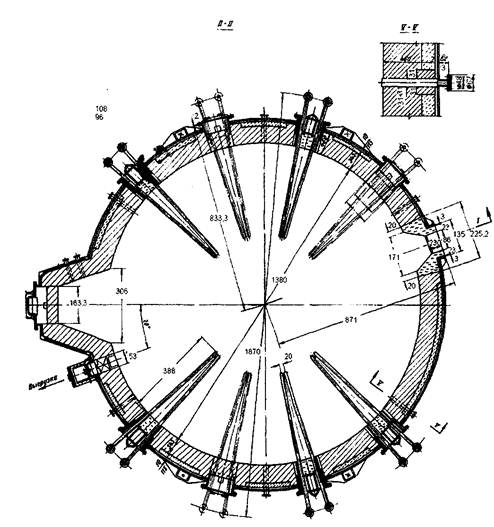
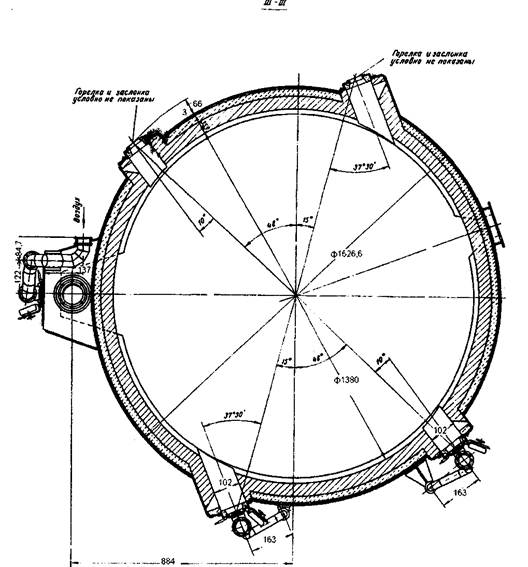
Основной проблемой схемы переработки является измельчение
сырья. Рисунок 2. Щековая дробилка
Достижимая конечная крупность зависит от выбранной ширины
щели и составляет: dso= 15 мм (наибольшая ширина щели) dso = 1 мм (наименьшая ширина щели).
Принцип действия:
Лабораторная проба измельчается в закрытом рабочем
пространстве воздействием большого давления между двумя дробящими плитами.
Между двумя боковыми опорными стенками находится неподвижная дробящая плита.
Второй дробящей плитой, которая приводится в движение эксцентриком, проба
втягивается и прижимается к неподвижной дробящей плите. Вследствие очень
большого давления между обеими плитами куски пробы раздрабливаются.
Раздробленный материал выступает внизу через регулируемую снаружи разгрузочную
щель. При непрерывной работе материал может, например, через желоб подводиться
для дальнейшего измельчения в лабораторной дисковой мельнице.
Принадлежности:
Дробящие плиты и опорные стенки - предлагаются в различных
материалах во избежание нежелательного загрязнения тюб при износе
измельчительных элементов.
Материал |
Плотность г/см3 |
Износостойкость |
Применение для следующих материалов |
Твёрдый сплав карбида вольфрама 91% WC +
9%Со |
14,8 |
очень хорошая |
твёрдая, абразивная проба |
Двуокись циркония 94,8%Zr02 |
5,7 |
чрезвычайно хорошая |
абразивная проба, проба средней твёрдости, безжелезное
измельчение |
Обычно дробящие плиты и опорные стенки изготавливаются из
одинакового материала, однако, если боковые стенки не подвергаются большой
нагрузке, то можно использовать стандартное исполнение их из закалённой
инструментальной стали. Тонкое измельчение в диапазоне от 95 мм до 0,1 мм -
монтажная станина с питающим желобом в комбинации с лабогатошой дисковой
мельницей.
Технические данные |
Модель П |
Размер отверстия воронки |
100 х 100 мм |
Крупность загружаемого материала |
ок.95 мм |
Производительность |
200 кг/час |
Ширина щели (тонкость) |
1-15 мм |
Мощность двигателя |
2,2 кВт |
Вес |
нетто 205 кг брутто 245 кг |
Стандартное исполнение |
Дробящие плиты и боковые стенки из закалённой хромистой стали |
Размеры (ширина х глубина х высота) |
41x83x72 см |
Область применения.
Прибор применяется для прерывного или непрерывного тонкого
измельчения хрупких и очень твёрдых проб. Максимальная крупность загружаемых
кусков составляет ок.20 мм длины ребра. Достижимая конечная тонкость (d50) находится в зависимости от установленной ширины щели в
диапазоне от ок.12 мм (наибольшая ширина щели):
·
до 0,1 мм (наименьшая ширина щели). Максимальная производительность
зависит от
·
выбранной ширины щели и твёрдости пробы и составляет ок.150
кг/час.
Принцип действия.
Материал измельчается между двумя встречнодействующими, с
внутренней стороны грубо.
Технические данные
Макс, крупность Загружаемого материала 20 мм Производительность
150 кг/час Конечная тонкость 0,1 - 12мм Питание 400 В/3~, 50 - 60 Гц, 1830Вт |
Скорость вращения измельчающего диска 439 об/мин Вес нетто 140
кг, брутто 170 кг Размеры (ширина х глубина х высота) 44 х 87 х 40 см
Упаковка картонный ящик! 08 х 60 х 70 см |
Гранулятор барабанный Модель ГБ-1600 обеспечивает получение
полуфабриката 0-20 мм. Он может быть использован для интенсивного перемешивания
влажных и сухих тонкодисперсных компонентов, производительность, м3/час - не
менее 10,0, диаметр барабана - 1600 мм, частота вращения барабана - 18 об/мин,
режим работы - непрерывный, электродвигатель 4А13288УЗ N=4 квт, п=750 об/мин
(привод барабана)
См. п. п.4.1.2.3; 7. Температура обжига 900°С Непрерывная
загрузка и отгрузка сырья
Модель: НО7215А
Коэффициент очистки: 0,99
Количество очищаемого воздуха: до6550 м2
Достигаемая эффективность очистки газов от взвешенных частиц
(пыли, золы и т. л) 20 мг/мЗ (до 99,9%) и в случае применения повторного цикла
можно достичь даже ниже 1 мг/мЗ. Регенерация фильтров производиться импульсом
сжатого воздуха либо низконапорной обратной продувкой воздухом.
По типу применяемых рукавов имеются фильтры рукавные,
карманные и др. В случае применения керамических рукавов можно эксплуатировать
фильтр до 850 °С
Марка: ФРИ-360
Площадь поверхности фильтрования: 360 м2
Диаметр рукава: 135 мм.
Выбран стандартный реакционный аппарат с перемешивающим
устройством. Объем 200л., материал корпуса - сталь.
Расчет количества оборудования производится по формуле
V= Q *T/(r*V*y)
Где Q - суточная производительность
на операции 18128 кг/сут
т - длительность цикла операции 20мин.
V - рабочая емкость аппарата 150л
г - число часов работы аппарата в сутки 22
у - коэффициент заполнения, обычно принимают 0,7-0,85
п=18128*20/(0,75*200*22*60) =1,8=2шт
Рисунок 4. НУТЧ фильтр.
Нутч-фильтр предназначен для обезвоживания осадка (шлама) из
отстойников и дифференциаторов под действием вакуума. Количество аппаратов
принимается в зависимости от количества шлама поступающего на обезвоживание.
Марка: НФ-1000-01.
Выпускаются производительностью 100 кг/ч по осадку
Допустимая температура стенки, С:
в кислой среде - от минус 20 до плюс 200
Выбран стандартный реакционный аппарат с перемешивающим
устройством. Объем 300л., материал корпуса - сталь.
V - Q *i/(r*V*y)
Где Q - суточная производительность
на операции 24530 кг/сут
т - длительность цикла операции 35 мин
V - рабочая емкость аппарата 100л
г - число часов работы аппарата в сутки 22
у - коэффициент заполнения, обычно принимают 0,7-0,85
п=24530*25/(0,75*300*22*60) =2шт.
7.8НУТЧ фильтр.
См. п. п.7.6
Сушилка представляет собой цилиндрический корпус,
установленный на роликовых опорах с наклоном в сторону выгрузки материала.
Выбираем не большую печь, с производительностью не менее
200кг/ч/ При температуре ~750°С.
Марка БНО,5-2,5НУ
Частота вращения барабана: 4,6 об/мин
Масса, кг, не более 2000кг.
Модель: камерные лабораторные печи производимые НПК
"ЛенТерм"
Тип печ: КЭСл-2,5Ь
Тмах, 900°С
Тип нагревателей: мет. спирали.
В процессе производственной деятельности образуются отходы,
которые нарушают экологическое равновесие, загрязняя окружающую среду, и
снижают степень извлечения ценных компонентов, содержащихся в исходном сырье.
Эти отходы необходимо перерабатывать.
В настоящее время подсчеты показали, что удельные
капитальные затраты на сбор и переработку вторичного металла в 25 раз меньше,
чем на производство металла из руды.
Производительность труда во вторичной цветной металлургии
примерно в два раза выше, чем в первичной. Сбор и переработка вторичных
металлов имеют не только экономический, но и социальный эффект.
Отходы подразделяют на отходы производства и отходы
потребления (лом).
В настоящее время для производства режущих инструментов
широко используются твердые сплавы. Они состоят из карбидов вольфрама, титана,
тантала, сцементированных небольшим количеством кобальта. Карбиды вольфрама,
титана и тантала обладают высокой твердостью, износостойкостью. Скорости
резания инструментами, оснащенными твердыми сплавами, в 3-4 раза превосходят
скорости резания инструментами из быстрорежущей стали.
Недостатком твердых сплавов, по сравнению с быстрорежущей
сталью, является их повышенная хрупкость, которая возрастает с уменьшением
содержания кобальта в сплаве. И, следовательно, возникает вопрос утилизации
таких сплавов. Переработка лома и отходов позволяет вернуть металл в
кругооборот.
5. Сплавы редких металлов перерабатывают окислением,
хлорированием, электролизом и гидрометаллургическим способом. Их переработка
осложнена более высоким содержанием других металлов и взаимным влиянием
компонентов сплавов на технологические процессы. - Окислительные методы.
Их можно использовать и для переработки сплавов и кусковых
отходов твердых сплавов. Применяемые в настоящее время инструментальные твердые
сплавы базируются на карбидах вольфрама, титана и тантала или на смеси
указанных соединений с добавлением связующего металла - кобальта. - Методы
хлорирования.
При хороших технологических показателях следует отметить громоздкость
оборудования для хлорных схем, а также трудности, связанные с агрессивностью и
токсичностью хлора и хлоридов, необходимостью специальных коррозионностойких
материалов для аппаратуры и значительными затратами на реагенты - Способы
электрохимического растворения отходов.
Электрохимическое растворение отходов сплавов используют на
отечественных и зарубежных предприятиях. Этот метод наиболее дешев и не требует
сложной аппаратуры. Электрохимическое растворение целесообразно вести в
щелочных растворах, так как образуются легко растворимые соли рения, вольфрама
и молибдена.
6. Как показали расчеты:
- невязка материального баланса обжига 2,124%, она связана с
погрешностью расчетов, - невязка теплового баланса 0,12% рассчитана с
удовлетворительной точностью, - площадь пода равна 1,5м2, для расчета печи с
такой площадью пода нужна спец литература, целью данной работы не является
данный расчет.
9. Список литературы
1.
Корвин С.С, Дробот Д.В., Федоров П.И. "Редкие и рассеянные
элементы. Химия и технология". В трех книгах. Книга 2. учебник для вузов -
М.: МИСИС, 1999. - 464с.
2.
Корвин С.С, Дробот Д.В., Федоров П.И. "Редкие и рассеянные
элементы. Химия и технология". В трех книгах. Книга 3. учебник для вузов -
М.: МИСИС, 1999. - 464с.
3.
Дробот Д.В., Резник А.М., Юрченко Л.Д. "Оборудование заводов
редкометалльной промышленности и основы проектирования": Учебное пособие.
- М МИХМ, 1985 - 72с.
4.
Морозов В.А., Миткалийный В.И., Егоров А.В., Сборщиков Г.С.
"Металлургические печи атлас". - М.: Металлургия. 1987. -384с.
5.
Краткий справочник физико-химических величин/ Под ред. Мищенко К.П.,
Равделя А.А.
6.
http: // www. mechanik. spb. ru
7.
http: // www. upmt. ru
8.
http: // www. fingo. ru/fri-360/
9.
http: // stankinprom. com.
ua/products/images/PDF/rci. pdf
10.
10. http: // wwwЛenterm.
n] /lenterm_laboratory_fumaces. html И. http: // www.
bank. referatoff. ru
11.
http: // www. chemport. ru
12.
http: // www. drillmat. ru
13.
http: // www. npftin. spb. ru
|